Giới thiệu
Ống thép đóng vai trò quan trọng trong dầu khí, mang lại độ bền và độ tin cậy vô song trong điều kiện khắc nghiệt. Thiết yếu cho hoạt động thăm dò và vận chuyển, những ống này chịu được áp suất cao, môi trường ăn mòn và nhiệt độ khắc nghiệt. Trang này khám phá các chức năng quan trọng của ống thép trong hoạt động thăm dò dầu khí, nêu chi tiết tầm quan trọng của chúng trong hoạt động khoan, cơ sở hạ tầng và an toàn. Khám phá cách lựa chọn ống thép phù hợp có thể nâng cao hiệu quả hoạt động và giảm chi phí trong ngành công nghiệp đòi hỏi khắt khe này.
I. Kiến thức cơ bản về ống thép cho ngành dầu khí
1. Giải thích thuật ngữ
API: Viết tắt của Viện Dầu khí Hoa Kỳ.
OCTG: Viết tắt của Hàng hóa dạng ống dầu Quốc gia, bao gồm Ống vỏ dầu, Ống dầu, Ống khoan, Cổ khoan, Mũi khoan, Thanh hút, khớp nối con chó con, v.v.
Ống dầu: Ống được sử dụng trong giếng dầu để khai thác, khai thác khí, bơm nước và nứt vỡ axit.
Vỏ: Ống được hạ xuống từ mặt đất vào lỗ khoan để làm lớp lót nhằm ngăn tường sụp đổ.
Ống khoan: Ống dùng để khoan lỗ khoan.
Đường ống: Ống dùng để vận chuyển dầu hoặc khí đốt.
Khớp nối: Xi lanh dùng để nối hai ống ren bằng ren trong.
Vật liệu ghép: Ống dùng để sản xuất khớp nối.
Chủ đề API: Ren ống được chỉ định theo tiêu chuẩn API 5B, bao gồm ren tròn ống dẫn dầu, ren tròn ngắn vỏ, ren tròn dài vỏ, ren hình thang một phần vỏ, ren ống dẫn, v.v.
Kết nối cao cấp: Luồng không phải API có các thuộc tính niêm phong, thuộc tính kết nối và các thuộc tính khác độc đáo.
Thất bại: biến dạng, gãy, hư hỏng bề mặt và mất chức năng ban đầu trong các điều kiện sử dụng cụ thể.
Các hình thức thất bại chính: nghiền nát, trượt, vỡ, rò rỉ, ăn mòn, liên kết, mài mòn, v.v.
2. Tiêu chuẩn liên quan đến dầu khí
API Spec 5B, Phiên bản thứ 17 – Đặc điểm kỹ thuật để tạo ren, đo và kiểm tra ren của ren vỏ, ống và ống dẫn
API Spec 5L, Phiên bản thứ 46 – Đặc điểm kỹ thuật cho đường ống
API Spec 5CT, Phiên bản thứ 11 – Đặc điểm kỹ thuật cho vỏ và ống
API Spec 5DP, Phiên bản thứ 7 – Đặc điểm kỹ thuật cho ống khoan
Thông số API 7-1, Phiên bản thứ 2 – Đặc điểm kỹ thuật cho các bộ phận thân máy khoan quay
Thông số API 7-2, Phiên bản thứ 2 – Đặc điểm kỹ thuật để tạo ren và đo các kết nối ren có vai quay
API Spec 11B, Phiên bản thứ 24 – Đặc điểm kỹ thuật cho Thanh mút, Thanh và lớp lót được đánh bóng, Khớp nối, Thanh chìm, Kẹp thanh được đánh bóng, Hộp nhồi và Ống bơm
ISO 3183:2019 – Công nghiệp dầu mỏ và khí đốt tự nhiên – Ống thép cho hệ thống vận chuyển đường ống
ISO 11960:2020 – Công nghiệp dầu mỏ và khí đốt tự nhiên – Ống thép dùng làm vỏ hoặc ống cho giếng
NACE MR0175 / ISO 15156:2020 – Công nghiệp dầu mỏ và khí đốt tự nhiên – Vật liệu sử dụng trong môi trường chứa H2S trong sản xuất dầu khí
II. ống dầu
1. Phân loại ống dầu
Ống dẫn dầu được chia thành Ống dẫn dầu không bị đảo ngược (NU), Ống dẫn dầu bị đảo ngược bên ngoài (EU) và Ống dẫn dầu khớp nối tích hợp (IJ). Ống dẫn dầu NU có nghĩa là đầu ống có độ dày trung bình, trực tiếp xoay ren và đưa các khớp nối vào. Ống bị đảo ngược ngụ ý rằng các đầu của cả hai ống đều được đảo ngược bên ngoài, sau đó được luồn ren và ghép nối. Ống nối tích hợp có nghĩa là một đầu của ống được đảo ngược với ren ngoài và đầu còn lại được đảo ngược với ren trong được kết nối trực tiếp mà không cần khớp nối.
2. Chức năng của ống dẫn dầu
① Khai thác dầu khí: sau khi các giếng dầu khí được khoan và trát xi măng, ống được đặt vào vỏ dầu để hút dầu khí xuống lòng đất.
② Phun nước: khi áp suất lỗ khoan không đủ, bơm nước vào giếng qua ống.
③ Phun hơi nước: Trong quá trình thu hồi dầu nóng đặc, hơi nước được đưa vào giếng bằng ống dẫn dầu cách nhiệt.
④ Axit hóa và nứt vỡ: Ở giai đoạn cuối của quá trình khoan giếng hoặc để cải thiện sản lượng giếng dầu khí, cần phải đưa môi trường axit hóa và nứt vỡ hoặc vật liệu bảo dưỡng vào lớp dầu khí, môi trường và vật liệu bảo dưỡng được vận chuyển qua ống dẫn dầu.
3. Lớp thép ống dầu
Các loại thép của ống dầu là H40, J55, N80, L80, C90, T95, P110.
N80 được chia thành N80-1 và N80Q, cả hai đều có cùng tính chất kéo; hai điểm khác biệt là trạng thái phân phối và sự khác biệt về hiệu suất va đập, phân phối N80-1 theo trạng thái chuẩn hóa hoặc khi nhiệt độ cán cuối cùng lớn hơn nhiệt độ tới hạn Ar3 và giảm độ căng sau khi làm mát bằng không khí và có thể được sử dụng để tìm cán nóng thay vì chuẩn hóa, không yêu cầu thử nghiệm va đập và không phá hủy; N80Q phải được ram (làm nguội và ram) Xử lý nhiệt, chức năng va đập phải phù hợp với các quy định của API 5CT và phải được thử nghiệm không phá hủy.
L80 được chia thành L80-1, L80-9Cr và L80-13Cr. Tính chất cơ học và tình trạng giao hàng của chúng là như nhau. Sự khác biệt về cách sử dụng, độ khó sản xuất và giá cả: L80-1 dành cho loại chung, L80-9Cr và L80-13Cr là ống có khả năng chống ăn mòn cao, độ khó sản xuất và đắt tiền, thường được sử dụng trong các giếng ăn mòn nặng.
C90 và T95 được chia thành 1 và 2 loại, cụ thể là C90-1, C90-2 và T95-1, T95-2.
4. Ống dầu Loại thép thường được sử dụng, Tên thép và Tình trạng giao hàng
J55 (37Mn5) Ống dầu NU: Cán nóng thay vì chuẩn hóa
J55 (37Mn5) Ống dầu EU: Chuẩn hóa toàn bộ chiều dài sau khi đảo lộn
Ống dầu NU N80-1 (36Mn2V): Cán nóng thay vì chuẩn hóa
Ống dầu EU N80-1 (36Mn2V): Chuẩn hóa toàn bộ chiều dài sau khi đảo lộn
Ống dầu N80-Q (30Mn5): 30Mn5, Nhiệt độ toàn bộ
Ống dầu L80-1 (30Mn5): 30Mn5, Nhiệt độ toàn bộ
Ống dầu P110 (25CrMnMo): 25CrMnMo, Nhiệt độ toàn bộ
Khớp nối J55 (37Mn5): Cán nóng trực tuyến Chuẩn hóa
Khớp nối N80 (28MnTiB): Nhiệt độ toàn thời gian
Khớp nối L80-1 (28MnTiB): Cường lực toàn phần
Khớp nối P110 (25CrMnMo): Nhiệt độ toàn thời gian
III. Ống vỏ
1. Phân loại và vai trò của vỏ bọc
Vỏ là ống thép đỡ thành giếng dầu khí. Một số lớp vỏ được sử dụng trong mỗi giếng tùy theo độ sâu khoan và điều kiện địa chất khác nhau. Xi măng được sử dụng để xi măng vỏ sau khi hạ xuống giếng, và không giống như ống dầu và ống khoan, nó không thể được tái sử dụng và thuộc về vật liệu tiêu hao dùng một lần. Vì vậy, việc tiêu thụ vỏ bọc chiếm hơn 70% tổng số ống dẫn dầu. Vỏ có thể được chia thành vỏ dây dẫn, vỏ trung gian, vỏ sản xuất và vỏ lót theo mục đích sử dụng và cấu trúc của chúng trong giếng dầu được thể hiện trong Hình 1.
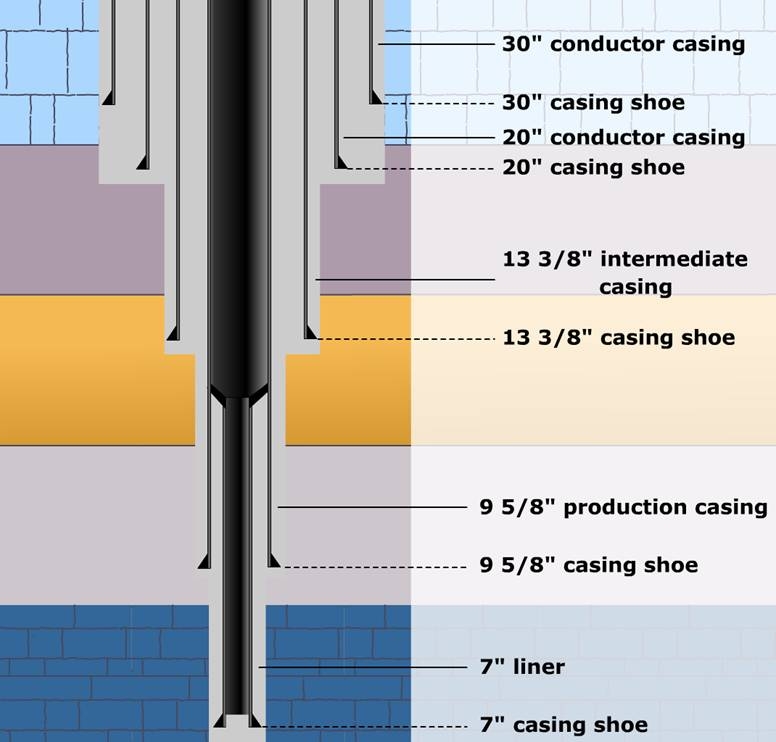
①Vỏ dây dẫn: Thông thường sử dụng các loại API K55, J55 hoặc H40, vỏ dây dẫn giúp ổn định đầu giếng và cách ly các tầng ngậm nước nông có đường kính thường khoảng 20 inch hoặc 16 inch.
②Vỏ trung gian: Vỏ trung gian, thường được làm từ các loại API K55, N80, L80 hoặc P110, được sử dụng để cách ly các thành tạo không ổn định và các vùng áp suất khác nhau, với đường kính điển hình là 13 3/8 inch, 11 3/4 inch hoặc 9 5/8 inch .
③Vỏ sản xuất: Được chế tạo từ thép cao cấp như các loại API J55, N80, L80, P110 hoặc Q125, vỏ sản xuất được thiết kế để chịu được áp lực sản xuất, thường có đường kính 9 5/8 inch, 7 inch hoặc 5 1/2 inch.
④Vỏ lót: Ống lót kéo dài giếng khoan vào bể chứa bằng các vật liệu như cấp API L80, N80 hoặc P110, với đường kính thông thường là 7 inch, 5 inch hoặc 4 1/2 inch.
⑤Ống: Ống vận chuyển hydrocarbon lên bề mặt, sử dụng các loại API J55, L80 hoặc P110 và có các đường kính 4 1/2 inch, 3 1/2 inch hoặc 2 7/8 inch.
IV. Ống khoan
1. Phân loại và chức năng của ống dùng cho dụng cụ khoan
Ống khoan vuông, ống khoan, ống khoan có trọng lượng và cổ khoan trong các dụng cụ khoan tạo thành ống khoan. Ống khoan là dụng cụ khoan lõi dẫn mũi khoan từ mặt đất xuống đáy giếng, và nó cũng là một kênh từ mặt đất xuống đáy giếng. Nó có ba vai trò chủ đạo:
① Để truyền mô-men xoắn để dẫn động mũi khoan;
② Dựa vào trọng lượng của mũi khoan để phá vỡ áp lực của đá đáy giếng;
③ Để vận chuyển dung dịch rửa, nghĩa là khoan bùn qua mặt đất thông qua máy bơm bùn áp suất cao, cột khoan vào lỗ khoan chảy vào đáy giếng để xả các mảnh vụn đá và làm mát mũi khoan, và mang các mảnh vụn đá xuyên qua mặt ngoài của cột và thành giếng giữa hình khuyên để quay trở lại mặt đất, nhằm đạt được mục đích khoan giếng.
Ống khoan được sử dụng trong quá trình khoan để chịu được nhiều loại tải trọng xen kẽ phức tạp, chẳng hạn như kéo, nén, xoắn, uốn và các ứng suất khác. Bề mặt bên trong cũng chịu sự xói mòn và ăn mòn bùn áp suất cao.
(1) Ống khoan vuông: Ống khoan vuông có hai loại: tứ giác và lục giác. Trong ống khoan dầu khí của Trung Quốc, mỗi bộ trụ khoan thường sử dụng ống khoan loại tứ giác. Thông số kỹ thuật của nó là 63,5mm (2-1/2 inch), 88,9mm (3-1/2 inch), 107,95mm (4-1/4 inch), 133,35mm (5-1/4 inch), 152,4mm (6 inch), v.v. Chiều dài sử dụng thường là 1214,5 m.
(2) Ống khoan: Ống khoan là công cụ chính để khoan giếng, được kết nối với đầu dưới của ống khoan vuông, và khi giếng khoan tiếp tục đào sâu, ống khoan sẽ tiếp tục kéo dài cột khoan lần lượt. Các thông số kỹ thuật của ống khoan là: 60,3mm (2-3/8 inch), 73,03mm (2-7/8 inch), 88,9mm (3-1/2 inch), 114,3mm (4-1/2 inch), 127mm (5 inch), 139,7mm (5-1/2 inch) v.v.
(3) Ống khoan hạng nặng: Ống khoan có trọng lượng là một công cụ chuyển tiếp nối ống khoan và vòng khoan, có thể cải thiện tình trạng lực của ống khoan và tăng áp lực lên mũi khoan. Thông số kỹ thuật chính của ống khoan có trọng lượng là 88,9mm (3-1/2 inch) và 127mm (5 inch).
(4) Cổ khoan: Cổ khoan được kết nối với phần dưới của ống khoan, là một ống đặc biệt có thành dày, độ cứng cao. Nó tạo áp lực lên mũi khoan để phá vỡ đá và đóng vai trò dẫn hướng khi khoan giếng thẳng. Các thông số kỹ thuật phổ biến của cổ khoan là 158,75mm (6-1/4 inch), 177,85mm (7 inch), 203,2mm (8 inch), 228,6mm (9 inch), v.v.
V. Đường ống
1. Phân loại đường ống
Ống dẫn được sử dụng trong ngành dầu khí để vận chuyển dầu, dầu tinh chế, khí đốt tự nhiên và đường ống nước với tên viết tắt là ống thép. Vận chuyển đường ống dầu khí được chia thành đường ống chính, đường ống nhánh và đường ống mạng lưới đường ống đô thị. Ba loại đường ống truyền dẫn chính có thông số kỹ thuật thông thường là ∅406 ~ 1219mm, độ dày thành 10 ~ 25mm, cấp thép X42 ~ X80; đường ống nhánh và đường ống mạng lưới đường ống đô thị thường có thông số kỹ thuật là ∅114 ~ 700mm, độ dày thành 6 ~ 20mm, cấp thép cho X42 ~ X80. Cấp thép là X42 ~ X80. Đường ống có sẵn ở dạng hàn và liền mạch. Đường ống hàn được sử dụng nhiều hơn Đường ống liền mạch.
2. Tiêu chuẩn đường ống
API Spec 5L – Đặc điểm kỹ thuật cho đường ống
ISO 3183 – Công nghiệp dầu mỏ và khí đốt tự nhiên – Ống thép cho hệ thống vận chuyển đường ống
3. PSL1 và PSL2
PSL là viết tắt của mức độ thông số kỹ thuật sản phẩm. Mức thông số kỹ thuật của sản phẩm ống thép được chia thành PSL 1 và PSL 2, và mức chất lượng được chia thành PSL 1 và PSL 2. PSL 2 cao hơn PSL 1; hai mức thông số kỹ thuật không chỉ có các yêu cầu thử nghiệm khác nhau mà thành phần hóa học và các yêu cầu về tính chất cơ học cũng khác nhau, vì vậy theo đơn đặt hàng API 5L, các điều khoản của hợp đồng, ngoài việc chỉ định các thông số kỹ thuật, cấp thép và các chỉ số chung khác, mà còn phải chỉ ra mức thông số kỹ thuật của sản phẩm, tức là PSL 1 hoặc PSL 2. PSL 2 trong thành phần hóa học, tính chất kéo, lực va đập, thử nghiệm không phá hủy và các chỉ số khác nghiêm ngặt hơn PSL 1.
4. Cấp thép ống, thành phần hóa học và tính chất cơ học
Các loại thép ống từ thấp đến cao được chia thành A25, A, B, X42, X46, X52, X60, X65, X70 và X80. Để biết thành phần hóa học và tính chất cơ học chi tiết, vui lòng tham khảo Sách API 5L Specification, ấn bản lần thứ 46.
5. Yêu cầu kiểm tra thủy tĩnh đường ống và kiểm tra không phá hủy
Đường ống phải được thử nghiệm thủy lực từng nhánh, tiêu chuẩn không cho phép tạo áp suất thủy lực không phá hủy, đây cũng là sự khác biệt lớn giữa tiêu chuẩn API và tiêu chuẩn của chúng tôi. PSL 1 không yêu cầu thử nghiệm không phá hủy; PSL 2 phải là thử nghiệm không phá hủy từng nhánh.
VI. Kết nối cao cấp
1. Giới thiệu Kết nối Cao cấp
Premium Connection là ren ống có cấu trúc độc đáo khác với ren API. Mặc dù vỏ dầu ren API hiện có được sử dụng rộng rãi trong khai thác giếng dầu, nhưng nhược điểm của nó được thể hiện rõ trong môi trường độc đáo của một số mỏ dầu: cột ống ren tròn API, mặc dù hiệu suất bịt kín của nó tốt hơn, nhưng lực kéo mà phần ren chịu chỉ tương đương với 60% đến 80% của sức mạnh thân ống, và do đó không thể sử dụng trong khai thác giếng sâu; cột ống ren hình thang lệch API, mặc dù hiệu suất kéo của nó cao hơn nhiều so với kết nối ren tròn API, nhưng hiệu suất bịt kín của nó không tốt lắm. Mặc dù hiệu suất kéo của cột cao hơn nhiều so với kết nối ren tròn API, nhưng hiệu suất bịt kín của nó không tốt lắm, vì vậy không thể sử dụng trong khai thác giếng khí áp suất cao; ngoài ra, mỡ ren chỉ có thể phát huy tác dụng của nó trong môi trường có nhiệt độ dưới 95℃, vì vậy không thể sử dụng trong khai thác giếng nhiệt độ cao.
So với kết nối ren tròn API và kết nối ren hình thang một phần, kết nối cao cấp đã có những tiến bộ đột phá về các khía cạnh sau:
(1) Độ kín tốt, thông qua thiết kế cấu trúc đệm đàn hồi và kim loại, làm cho khả năng bịt kín khí khớp có khả năng đạt đến giới hạn của thân ống trong áp suất chảy;
(2) Độ bền kết nối cao, kết nối với kết nối khóa đặc biệt của vỏ dầu, cường độ kết nối của nó đạt hoặc vượt quá độ bền của thân ống, để giải quyết vấn đề trượt một cách cơ bản;
(3) Bằng cách cải tiến quy trình lựa chọn Vật liệu và xử lý bề mặt, về cơ bản đã giải quyết được vấn đề khóa dính chỉ;
(4) Thông qua việc tối ưu hóa cấu trúc, để phân bố ứng suất chung hợp lý hơn và có lợi hơn cho khả năng chống ăn mòn ứng suất;
(5) Thông qua cấu trúc vai được thiết kế hợp lý, để thao tác khóa trên thao tác dễ tiếp cận hơn.
Ngành công nghiệp dầu khí tự hào có hơn 100 kết nối cao cấp được cấp bằng sáng chế, đại diện cho những tiến bộ đáng kể trong công nghệ đường ống. Những thiết kế ren chuyên dụng này cung cấp khả năng bịt kín vượt trội, tăng cường độ bền kết nối và tăng khả năng chống chịu với các ứng suất môi trường. Bằng cách giải quyết các thách thức như áp suất cao, môi trường ăn mòn và nhiệt độ khắc nghiệt, những cải tiến này đảm bảo độ tin cậy và hiệu quả tuyệt vời trong các hoạt động khai thác dầu trên toàn thế giới. Nghiên cứu và phát triển liên tục trong các kết nối cao cấp nhấn mạnh vai trò quan trọng của chúng trong việc hỗ trợ các hoạt động khoan an toàn hơn và hiệu quả hơn, phản ánh cam kết liên tục về sự xuất sắc về công nghệ trong lĩnh vực năng lượng.
Kết nối VAM®: Được biết đến với hiệu suất mạnh mẽ trong môi trường đầy thách thức, kết nối VAM® có công nghệ hàn kín kim loại với kim loại tiên tiến và khả năng mô-men xoắn cao, đảm bảo hoạt động đáng tin cậy trong giếng sâu và bể chứa áp suất cao.
Dòng nêm TenarisHydril: Dòng sản phẩm này cung cấp một loạt các kết nối như Blue®, Dopeless® và Wedge 521®, được biết đến với khả năng bịt kín khí đặc biệt và khả năng chống lại lực nén và lực căng, nâng cao hiệu quả và an toàn khi vận hành.
TSH® Xanh: Được thiết kế bởi Tenaris, các kết nối TSH® Blue sử dụng thiết kế hai vai độc quyền và cấu hình ren hiệu suất cao, mang lại khả năng chống mỏi tuyệt vời và dễ dàng trang điểm trong các ứng dụng khoan quan trọng.
Kết nối Grant Prideco™ XT®: Được thiết kế bởi NOV, các kết nối XT® kết hợp lớp đệm kim loại-kim loại độc đáo và dạng ren chắc chắn, đảm bảo khả năng mô-men xoắn vượt trội và khả năng chống mài mòn, do đó kéo dài tuổi thọ hoạt động của kết nối.
Săn Seal-Lock® Kết nối: Với vòng đệm kim loại với kim loại và cấu hình ren độc đáo, kết nối Seal-Lock® của Hunting nổi tiếng với khả năng chịu áp lực vượt trội và độ tin cậy trong cả hoạt động khoan trên bờ và ngoài khơi.
Phần kết luận
Tóm lại, mạng lưới phức tạp của các ống thép đóng vai trò quan trọng đối với ngành dầu khí bao gồm một loạt các thiết bị chuyên dụng được thiết kế để chịu được môi trường khắc nghiệt và nhu cầu vận hành phức tạp. Từ các ống vỏ nền tảng hỗ trợ và bảo vệ các bức tường khỏe mạnh cho đến các ống đa năng được sử dụng trong các quy trình chiết xuất và phun, mỗi loại ống đều có mục đích riêng biệt trong việc thăm dò, sản xuất và vận chuyển hydrocarbon. Các tiêu chuẩn như thông số kỹ thuật API đảm bảo tính đồng nhất và chất lượng trên các ống này, trong khi các cải tiến như kết nối cao cấp giúp tăng cường hiệu suất trong các điều kiện đầy thách thức. Khi công nghệ phát triển, các thành phần quan trọng này sẽ tiến bộ, thúc đẩy hiệu quả và độ tin cậy trong các hoạt động năng lượng toàn cầu. Việc hiểu các ống này và các thông số kỹ thuật của chúng sẽ nhấn mạnh vai trò không thể thiếu của chúng trong cơ sở hạ tầng của ngành năng lượng hiện đại.