Giới thiệu
Trong các ngành công nghiệp như sản xuất điện, dầu khí, hóa dầu và lọc dầu, ống liền mạch là thành phần thiết yếu, đặc biệt là trong các thiết bị phải chịu được nhiệt độ khắc nghiệt, áp suất cao và môi trường khắc nghiệt, ăn mòn. Các lò hơi, bộ trao đổi nhiệt, tụ điện, bộ siêu nhiệt, bộ gia nhiệt không khí và bộ tiết kiệm sử dụng các ống này. Mỗi ứng dụng này đòi hỏi các đặc tính vật liệu cụ thể để đảm bảo hiệu suất, độ an toàn và tuổi thọ. Việc lựa chọn ống liền mạch cho lò hơi và bộ trao đổi nhiệt phụ thuộc vào nhiệt độ, áp suất, khả năng chống ăn mòn và độ bền cơ học cụ thể.
Hướng dẫn này cung cấp cái nhìn sâu sắc về các vật liệu khác nhau được sử dụng cho ống liền mạch, bao gồm thép cacbon, thép hợp kim, thép không gỉ, hợp kim titan, hợp kim gốc niken, hợp kim đồng và hợp kim zirconium. Chúng tôi cũng sẽ khám phá các tiêu chuẩn và cấp độ có liên quan, do đó giúp bạn đưa ra quyết định sáng suốt hơn cho các dự án nồi hơi và bộ trao đổi nhiệt của mình.
Tổng quan về CS, AS, SS, Hợp kim Niken, Hợp kim Titan và Zirconi, Đồng và Hợp kim Đồng
1. Tính chất chống ăn mòn
Mỗi vật liệu dùng cho ống liền mạch đều có đặc tính chống ăn mòn riêng, quyết định tính phù hợp của vật liệu đó với các môi trường khác nhau.
Thép carbon: Khả năng chống ăn mòn hạn chế, thường được sử dụng với lớp phủ hoặc lớp lót bảo vệ. Có thể bị rỉ sét khi tiếp xúc với nước và oxy trừ khi được xử lý.
Thép hợp kim: Khả năng chống oxy hóa và ăn mòn ở mức trung bình. Các hợp kim bổ sung như crom và molypden cải thiện khả năng chống ăn mòn ở nhiệt độ cao.
Thép không gỉ: Khả năng chống ăn mòn chung, nứt do ăn mòn ứng suất và rỗ tuyệt vời do hàm lượng crom. Các loại cao cấp hơn, chẳng hạn như 316L, có khả năng chống ăn mòn do clorua tốt hơn.
Hợp kim gốc Niken: Khả năng chống chịu tuyệt vời với các môi trường khắc nghiệt như môi trường có tính axit, kiềm và giàu clorua. Các ứng dụng có tính ăn mòn cao sử dụng các hợp kim như Inconel 625, Hastelloy C276 và Alloy 825.
Titan và Zirconi: Khả năng chống chịu nước biển và các môi trường ăn mòn cao khác vượt trội. Titan đặc biệt chống chịu được clorua và môi trường axit, trong khi hợp kim zirconium vượt trội trong điều kiện axit cao.
Đồng và hợp kim đồng: Khả năng chống ăn mòn tuyệt vời trong nước ngọt và nước biển, hợp kim đồng-niken có khả năng chống chịu đặc biệt trong môi trường biển.
2. Tính chất vật lý và nhiệt
Thép carbon:
Mật độ: 7,85 g/cm³
Điểm nóng chảy: 1.425-1.500°C
Độ dẫn nhiệt: ~50 W/m·K
Thép hợp kim:
Mật độ: Thay đổi đôi chút tùy theo nguyên tố hợp kim, thường vào khoảng 7,85 g/cm³
Điểm nóng chảy: 1.450-1.530°C
Độ dẫn nhiệt: Thấp hơn thép cacbon do có chứa các nguyên tố hợp kim.
Thép không gỉ:
Mật độ: 7,75-8,0 g/cm³
Điểm nóng chảy: ~1.400-1.530°C
Độ dẫn nhiệt: ~16 W/m·K (thấp hơn thép cacbon).
Hợp kim gốc Niken:
Mật độ: 8,4-8,9 g/cm³ (tùy thuộc vào hợp kim)
Điểm nóng chảy: 1.300-1.400°C
Độ dẫn nhiệt: Thường thấp, ~10-16 W/m·K.
Titan:
Mật độ: 4,51 g/cm³
Điểm nóng chảy: 1.668°C
Độ dẫn nhiệt: ~22 W/m·K (tương đối thấp).
Đồng:
Mật độ: 8,94 g/cm³
Điểm nóng chảy: 1.084°C
Độ dẫn nhiệt: ~390 W/m·K (độ dẫn nhiệt tuyệt vời).
3. Thành phần hóa học
Thép carbon: Chủ yếu là sắt với 0,3%-1,2% cacbon và một lượng nhỏ mangan, silic và lưu huỳnh.
Thép hợp kim: Bao gồm các nguyên tố như crom, molypden, vanadi và vonfram để cải thiện độ bền và khả năng chịu nhiệt.
Thép không gỉ: Thông thường chứa 10,5%-30% crom, cùng với niken, molypden và các nguyên tố khác tùy thuộc vào cấp độ.
Hợp kim gốc Niken: Chủ yếu là niken (40%-70%) với crom, molypden và các nguyên tố hợp kim khác để tăng khả năng chống ăn mòn.
Titan: Loại 1 và loại 2 là titan nguyên chất thương mại, trong khi loại 5 (Ti-6Al-4V) bao gồm nhôm 6% và vanadi 4%.
Các hợp kim đồng: Hợp kim đồng chứa nhiều nguyên tố khác nhau như niken (10%-30%) để chống ăn mòn (ví dụ: Cu-Ni 90/10).
4. Tính chất cơ học
Thép carbon: Độ bền kéo: 400-500 MPa, Độ bền chảy: 250-350 MPa, Độ giãn dài: 15%-25%
Thép hợp kim: Độ bền kéo: 500-900 MPa, Độ bền chảy: 300-700 MPa, Độ giãn dài: 10%-25%
Thép không gỉ: Độ bền kéo: 485-690 MPa (304/316), Độ bền chảy: 170-300 MPa, Độ giãn dài: 35%-40%
Hợp kim gốc Niken: Độ bền kéo: 550-1.000 MPa (Inconel 625), Độ bền chảy: 300-600 MPa, Độ giãn dài: 25%-50%
Titan: Độ bền kéo: 240-900 MPa (thay đổi tùy theo cấp), Độ bền chảy: 170-880 MPa, Độ giãn dài: 15%-30%
Các hợp kim đồng: Độ bền kéo: 200-500 MPa (tùy thuộc vào hợp kim), Độ bền chảy: 100-300 MPa, Độ giãn dài: 20%-35%
5. Xử lý nhiệt (Điều kiện giao hàng)
Thép cacbon và thép hợp kim: Được giao trong điều kiện ủ hoặc chuẩn hóa. Xử lý nhiệt bao gồm làm nguội và ram để cải thiện độ bền và độ dẻo dai.
Thép không gỉ: Được cung cấp trong điều kiện ủ để loại bỏ ứng suất bên trong và cải thiện độ dẻo.
Hợp kim gốc Niken: Dung dịch ủ để tối ưu hóa các tính chất cơ học và khả năng chống ăn mòn.
Titan và Zirconi: Thông thường được cung cấp ở trạng thái ủ để tối đa hóa độ dẻo dai và độ bền.
Các hợp kim đồng: Được giao trong điều kiện ủ mềm, đặc biệt cho các ứng dụng tạo hình.
6. Hình thành
Thép cacbon và thép hợp kim: Có thể tạo hình nóng hoặc nguội, nhưng thép hợp kim đòi hỏi nhiều công sức hơn do có độ bền cao hơn.
Thép không gỉ: Ép nguội là phương pháp phổ biến, mặc dù tốc độ làm cứng cao hơn thép cacbon.
Hợp kim gốc Niken: Khó tạo hình hơn do độ bền và tốc độ làm cứng cao; thường đòi hỏi phải gia công nóng.
Titan: Quá trình tạo hình tốt nhất nên được thực hiện ở nhiệt độ cao vì nó có độ bền cao ở nhiệt độ phòng.
Các hợp kim đồng: Dễ tạo hình do có độ dẻo tốt.
7. Hàn
Thép cacbon và thép hợp kim: Nhìn chung dễ hàn bằng các kỹ thuật thông thường, nhưng có thể cần phải xử lý nhiệt trước và sau khi hàn (PWHT).
Thép không gỉ: Các phương pháp hàn phổ biến bao gồm hàn TIG, MIG và hàn hồ quang. Cần kiểm soát cẩn thận lượng nhiệt đầu vào để tránh nhạy cảm.
Hợp kim gốc Niken: Khó hàn do độ giãn nở nhiệt cao và dễ nứt.
Titan: Hàn trong môi trường được che chắn (khí trơ) để tránh nhiễm bẩn. Cần có biện pháp phòng ngừa do titan phản ứng ở nhiệt độ cao.
Các hợp kim đồng: Dễ hàn, đặc biệt là hợp kim đồng-niken, nhưng có thể cần phải gia nhiệt trước để tránh nứt.
8. Ăn mòn mối hàn
Thép không gỉ: Có thể bị ăn mòn cục bộ (ví dụ, rỗ, ăn mòn khe hở) tại vùng chịu ảnh hưởng của nhiệt mối hàn nếu không được kiểm soát đúng cách.
Hợp kim gốc Niken: Dễ bị nứt do ăn mòn ứng suất nếu tiếp xúc với clorua ở nhiệt độ cao.
Titan: Mối hàn phải được bảo vệ đúng cách khỏi oxy để tránh bị giòn.
9. Tẩy cặn, ngâm chua và vệ sinh
Thép cacbon và thép hợp kim: Quá trình ngâm chua loại bỏ oxit bề mặt sau khi xử lý nhiệt. Các axit phổ biến bao gồm axit clohydric và axit sunfuric.
Thép không gỉ và hợp kim niken: Tẩy bằng axit nitric/hydrofluoric được sử dụng để loại bỏ lớp màu do nhiệt và phục hồi khả năng chống ăn mòn sau khi hàn.
Titan: Dung dịch tẩy axit nhẹ được sử dụng để làm sạch bề mặt và loại bỏ oxit mà không làm hỏng kim loại.
Các hợp kim đồng: Làm sạch bằng axit được sử dụng để loại bỏ vết xỉn màu và oxit trên bề mặt.
10. Xử lý bề mặt (AP, BA, MP, EP, v.v.)
AP (Ủ và ngâm chua): Hoàn thiện tiêu chuẩn cho hầu hết các hợp kim thép không gỉ và niken sau khi ủ và ngâm chua.
BA (Ủ sáng): Đạt được bằng cách ủ trong môi trường được kiểm soát để tạo ra bề mặt phản chiếu mịn.
MP (Đánh bóng cơ học): Đánh bóng cơ học giúp cải thiện độ mịn bề mặt, giảm nguy cơ nhiễm bẩn và ăn mòn.
EP (Đánh bóng điện hóa): Một quá trình điện hóa loại bỏ vật liệu bề mặt để tạo ra bề mặt siêu mịn, giảm độ nhám bề mặt và cải thiện khả năng chống ăn mòn.
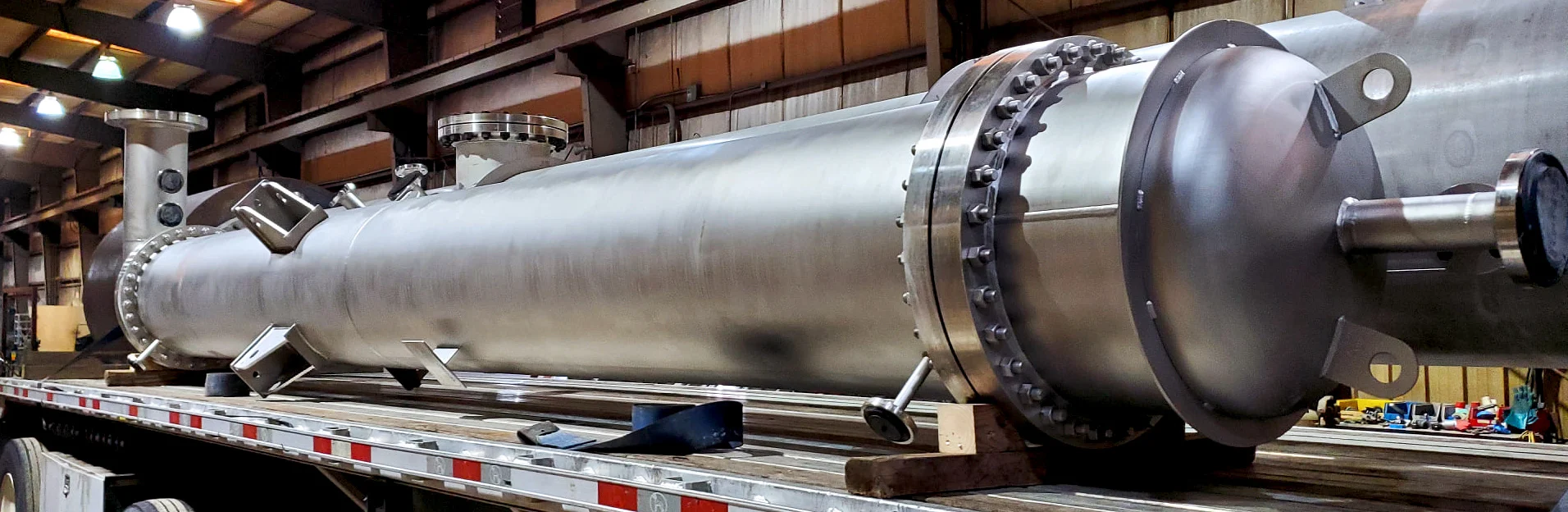
Bộ trao đổi nhiệt bằng thép không gỉ
I. Hiểu về ống liền mạch
Ống liền mạch khác với ống hàn ở chỗ chúng không có đường nối hàn, đây có thể là điểm yếu trong một số ứng dụng áp suất cao. Ống liền mạch ban đầu được tạo thành từ phôi rắn, sau đó được nung nóng, và sau đó, nó được đùn hoặc kéo qua một ống để tạo hình dạng ống. Việc không có đường nối mang lại cho chúng độ bền và độ tin cậy vượt trội, khiến chúng trở nên lý tưởng cho môi trường áp suất cao và nhiệt độ cao.
Ứng dụng phổ biến:
Nồi hơi: Ống liền mạch rất cần thiết trong việc chế tạo nồi hơi ống nước và ống lửa, nơi có nhiệt độ và áp suất cao.
Bộ trao đổi nhiệt: Được sử dụng để truyền nhiệt giữa hai chất lỏng, ống liền mạch trong bộ trao đổi nhiệt phải chống ăn mòn và duy trì hiệu suất nhiệt.
Thiết bị ngưng tụ: Ống liền mạch giúp ngưng tụ hơi nước thành nước trong hệ thống phát điện và làm lạnh.
Bộ quá nhiệt: Ống liền mạch được sử dụng để quá nhiệt hơi nước trong nồi hơi, nâng cao hiệu quả của tua-bin trong nhà máy điện.
Máy làm nóng không khí: Các ống này truyền nhiệt từ khí thải sang không khí, giúp cải thiện hiệu suất lò hơi.
Người tiết kiệm: Các ống liền mạch trong bộ tiết kiệm nhiệt làm nóng trước nước cấp bằng nhiệt thải từ lò hơi, giúp tăng hiệu suất nhiệt.
Lò hơi, bộ trao đổi nhiệt, tụ điện, bộ siêu nhiệt, bộ gia nhiệt không khí và bộ tiết kiệm là những thành phần không thể thiếu trong một số ngành công nghiệp, đặc biệt là những ngành liên quan đến truyền nhiệt, sản xuất năng lượng và quản lý chất lỏng. Cụ thể, các thành phần này được sử dụng chủ yếu trong các ngành công nghiệp sau:
1. Ngành sản xuất điện
Lò hơi: Được sử dụng trong các nhà máy điện để chuyển đổi năng lượng hóa học thành năng lượng nhiệt, thường để tạo ra hơi nước.
Bộ siêu nhiệt, bộ tiết kiệm nhiên liệu và bộ gia nhiệt không khí trước: Các bộ phận này cải thiện hiệu quả bằng cách làm nóng trước không khí đốt, thu hồi nhiệt từ khí thải và làm nóng hơi nước hơn nữa.
Bộ trao đổi nhiệt và tụ điện: Được sử dụng để làm mát và thu hồi nhiệt trong các nhà máy điện nhiệt, đặc biệt là trong các tua bin chạy bằng hơi nước và các chu trình làm mát.
2. Ngành Dầu khí
Bộ trao đổi nhiệt: Đóng vai trò quan trọng trong các quá trình lọc dầu, nơi nhiệt được truyền giữa các chất lỏng, chẳng hạn như trong quá trình chưng cất dầu thô hoặc trong các giàn khoan ngoài khơi để xử lý khí.
Lò hơi và bộ tiết kiệm nhiệt: Có trong các nhà máy lọc dầu và nhà máy hóa dầu để tạo ra hơi nước và thu hồi năng lượng.
Máy ngưng tụ: Được sử dụng để ngưng tụ khí thành chất lỏng trong quá trình chưng cất.
3. Công nghiệp hóa chất
Bộ trao đổi nhiệt: Được sử dụng rộng rãi để làm nóng hoặc làm mát các phản ứng hóa học và để thu hồi nhiệt từ các phản ứng tỏa nhiệt.
Lò hơi và thiết bị siêu nhiệt: Được sử dụng để tạo ra hơi nước cần thiết cho nhiều quá trình hóa học khác nhau và cung cấp năng lượng cho các bước chưng cất và phản ứng.
Bộ gia nhiệt và tiết kiệm không khí: Cải thiện hiệu quả trong các quy trình hóa học tiêu tốn nhiều năng lượng bằng cách thu hồi nhiệt từ khí thải và giảm mức tiêu thụ nhiên liệu.
4. Ngành hàng hải
Lò hơi và bộ trao đổi nhiệt: Thiết yếu trong tàu biển để tạo hơi nước, hệ thống sưởi ấm và làm mát. Bộ trao đổi nhiệt trên tàu biển thường được sử dụng để làm mát động cơ tàu và tạo ra điện.
Máy ngưng tụ: Được sử dụng để chuyển hơi nước thải trở lại thành nước để tái sử dụng trong hệ thống nồi hơi của tàu.
5. Ngành thực phẩm và đồ uống
Bộ trao đổi nhiệt: Thường được sử dụng cho quá trình thanh trùng, khử trùng và bay hơi.
Lò hơi và bộ tiết kiệm nhiên liệu: Được sử dụng để tạo ra hơi nước phục vụ cho hoạt động chế biến thực phẩm và thu hồi nhiệt từ khí thải để tiết kiệm nhiên liệu tiêu thụ.
6. HVAC (Hệ thống sưởi ấm, thông gió và điều hòa không khí)
Bộ trao đổi nhiệt và bộ gia nhiệt không khí: Được sử dụng trong hệ thống HVAC để truyền nhiệt hiệu quả giữa chất lỏng hoặc khí, cung cấp nhiệt hoặc làm mát cho các tòa nhà và cơ sở công nghiệp.
Máy ngưng tụ: Được sử dụng trong hệ thống điều hòa không khí để loại bỏ nhiệt từ chất làm lạnh.
7. Ngành công nghiệp giấy và bột giấy
Lò hơi, bộ trao đổi nhiệt và bộ tiết kiệm nhiệt: Cung cấp hơi nước và thu hồi nhiệt trong các quy trình như nghiền bột giấy, sấy giấy và thu hồi hóa chất.
Bộ siêu nhiệt và bộ gia nhiệt không khí: Nâng cao hiệu quả năng lượng trong các lò hơi thu hồi và cân bằng nhiệt tổng thể của các nhà máy giấy.
8. Ngành luyện kim và thép
Bộ trao đổi nhiệt: Được sử dụng để làm mát khí và chất lỏng nóng trong quá trình sản xuất thép và luyện kim.
Lò hơi và bộ tiết kiệm nhiệt: Cung cấp nhiệt cho nhiều quy trình khác nhau như vận hành lò cao, xử lý nhiệt và cán.
9. Ngành công nghiệp dược phẩm
Bộ trao đổi nhiệt: Được sử dụng để kiểm soát nhiệt độ trong quá trình sản xuất thuốc, quá trình lên men và môi trường vô trùng.
Lò hơi: Tạo ra hơi nước cần thiết cho việc khử trùng và làm nóng thiết bị dược phẩm.
10. Nhà máy chuyển đổi chất thải thành năng lượng
Lò hơi, máy ngưng tụ và máy tiết kiệm nhiệt: Được sử dụng để chuyển đổi chất thải thành năng lượng thông qua quá trình đốt cháy, đồng thời thu hồi nhiệt để cải thiện hiệu suất.
Bây giờ, chúng ta hãy tìm hiểu sâu hơn về các vật liệu làm nên ống liền mạch phù hợp cho những ứng dụng đòi hỏi khắt khe này.
II. Ống thép cacbon cho lò hơi và bộ trao đổi nhiệt
Thép cacbon là một trong những vật liệu được sử dụng rộng rãi nhất cho ống liền mạch trong các ứng dụng công nghiệp, chủ yếu là do độ bền tuyệt vời, cũng như giá cả phải chăng và tính sẵn có rộng rãi. Ống thép cacbon có khả năng chịu nhiệt độ và áp suất vừa phải, khiến chúng phù hợp với nhiều ứng dụng khác nhau.
Tính chất của thép cacbon:
Độ bền cao: Ống thép cacbon có thể chịu được áp suất và ứng suất đáng kể, lý tưởng để sử dụng trong nồi hơi và bộ trao đổi nhiệt.
Tiết kiệm chi phí: So với các vật liệu khác, thép cacbon tương đối rẻ, khiến nó trở thành lựa chọn phổ biến trong các ứng dụng công nghiệp quy mô lớn.
Khả năng chống ăn mòn trung bình: Mặc dù thép cacbon không có khả năng chống ăn mòn như thép không gỉ, nhưng có thể xử lý bằng lớp phủ hoặc lớp lót để cải thiện tuổi thọ trong môi trường ăn mòn.
Tiêu chuẩn và điểm chính:
ASTM A179: Tiêu chuẩn này bao gồm các ống thép cacbon thấp kéo nguội liền mạch được sử dụng cho các ứng dụng trao đổi nhiệt và ngưng tụ. Các ống này có đặc tính truyền nhiệt tuyệt vời và thường được sử dụng trong các ứng dụng nhiệt độ và áp suất thấp đến trung bình.
ASTM A192: Ống nồi hơi thép cacbon liền mạch được thiết kế cho dịch vụ áp suất cao. Các ống này được sử dụng trong quá trình tạo hơi nước và các môi trường áp suất cao khác.
ASTM A210: Tiêu chuẩn này bao gồm các ống thép cacbon trung bình liền mạch cho các ứng dụng nồi hơi và siêu nhiệt. Các loại A-1 và C cung cấp các mức độ khác nhau về độ bền và khả năng chịu nhiệt.
Tiêu chuẩn ASTMA334 (Cấp 1, 3, 6): Ống thép cacbon liền mạch và hàn được thiết kế để sử dụng ở nhiệt độ thấp. Các cấp này được sử dụng trong bộ trao đổi nhiệt, bình ngưng tụ và các ứng dụng nhiệt độ thấp khác.
EN 10216-2 (P235GH, P265GH TC1/TC2): Tiêu chuẩn Châu Âu cho ống thép liền mạch được sử dụng trong các ứng dụng chịu áp suất, đặc biệt là trong nồi hơi và dịch vụ nhiệt độ cao.
Ống thép cacbon là lựa chọn tuyệt vời cho các ứng dụng nồi hơi và bộ trao đổi nhiệt, nơi cần độ bền cao và khả năng chống ăn mòn vừa phải. Tuy nhiên, đối với các ứng dụng không chỉ liên quan đến nhiệt độ cực cao mà còn liên quan đến môi trường ăn mòn khắc nghiệt, ống hợp kim hoặc thép không gỉ thường được ưa chuộng do khả năng chống chịu và độ bền vượt trội của chúng.
III. Ống thép hợp kim cho lò hơi và bộ trao đổi nhiệt
Ống thép hợp kim được thiết kế cho các ứng dụng nồi hơi và bộ trao đổi nhiệt ở nhiệt độ cao và áp suất cao. Các ống này được hợp kim hóa với các nguyên tố như crom, molypden và vanadi để tăng cường độ bền, độ cứng và khả năng chống ăn mòn và nhiệt. Ống thép hợp kim được sử dụng rộng rãi trong các ứng dụng quan trọng, chẳng hạn như bộ siêu nhiệt, bộ tiết kiệm và bộ trao đổi nhiệt ở nhiệt độ cao, do độ bền và khả năng chống nhiệt và áp suất đặc biệt của chúng.
Tính chất của thép hợp kim:
Khả năng chịu nhiệt cao: Các nguyên tố hợp kim như crom và molypden cải thiện hiệu suất chịu nhiệt độ cao của các ống này, khiến chúng phù hợp cho các ứng dụng có nhiệt độ khắc nghiệt.
Khả năng chống ăn mòn được cải thiện: Ống thép hợp kim có khả năng chống oxy hóa và ăn mòn tốt hơn so với thép cacbon, đặc biệt là trong môi trường nhiệt độ cao.
Độ bền tăng cường: Các nguyên tố hợp kim cũng làm tăng độ bền của các ống này, cho phép chúng chịu được áp suất cao trong nồi hơi và các thiết bị quan trọng khác.
Tiêu chuẩn và điểm chính:
Tiêu chuẩn ASTMA213 (Cấp T5, T9, T11, T22, T91, T92): Tiêu chuẩn này bao gồm các ống thép hợp kim ferritic và austenitic liền mạch dùng trong nồi hơi, bộ siêu nhiệt và bộ trao đổi nhiệt. Các cấp khác nhau về thành phần hợp kim và được lựa chọn dựa trên các yêu cầu cụ thể về nhiệt độ và áp suất.
T5 và T9: Thích hợp cho hoạt động ở nhiệt độ trung bình đến cao.
T11 và T22: Thường được sử dụng trong các ứng dụng nhiệt độ cao, mang lại khả năng chịu nhiệt tốt hơn.
T91 và T92: Hợp kim cường độ cao tiên tiến được thiết kế để sử dụng ở nhiệt độ cực cao trong các nhà máy điện.
EN 10216-2 (16Mo3, 13CrMo4-5, 10CrMo9-10, 15NiCuMoNb5-6-4, X20CrMoV11-1): Tiêu chuẩn Châu Âu cho ống thép hợp kim liền mạch dùng trong ứng dụng nhiệt độ cao. Các ống này thường được dùng trong nồi hơi, bộ siêu nhiệt và bộ tiết kiệm trong nhà máy điện.
16Mo3: Một loại thép hợp kim có tính chất chịu nhiệt độ cao tốt, thích hợp sử dụng trong nồi hơi và bình chịu áp suất.
13CrMo4-5 và 10CrMo9-10: Hợp kim Crom-molypden có khả năng chịu nhiệt và chống ăn mòn tuyệt vời cho các ứng dụng nhiệt độ cao.
Ống thép hợp kim là lựa chọn phù hợp cho môi trường có nhiệt độ và áp suất cao, nơi thép cacbon có thể không cung cấp đủ hiệu suất cho lò hơi và bộ trao đổi nhiệt.
IV. Ống thép không gỉ cho lò hơi và bộ trao đổi nhiệt
Ống thép không gỉ có khả năng chống ăn mòn đặc biệt, khiến chúng trở nên lý tưởng cho các ứng dụng nồi hơi và bộ trao đổi nhiệt liên quan đến chất lỏng ăn mòn, nhiệt độ cao và môi trường khắc nghiệt. Chúng được sử dụng rộng rãi trong bộ trao đổi nhiệt, bộ siêu nhiệt và nồi hơi, nơi mà ngoài khả năng chống ăn mòn, độ bền nhiệt độ cao cũng được yêu cầu để có hiệu suất tối ưu.
Tính chất của thép không gỉ:
Khả năng chống ăn mòn: Khả năng chống ăn mòn của thép không gỉ bắt nguồn từ hàm lượng crom tạo thành lớp oxit bảo vệ trên bề mặt.
Độ bền cao ở nhiệt độ cao: Thép không gỉ vẫn giữ nguyên các đặc tính cơ học ngay cả ở nhiệt độ cao, do đó phù hợp với các thiết bị quá nhiệt và các ứng dụng nhiệt độ cao khác.
Độ bền lâu dài: Khả năng chống ăn mòn và oxy hóa của thép không gỉ đảm bảo tuổi thọ lâu dài, ngay cả trong môi trường khắc nghiệt.
Tiêu chuẩn và điểm chính:
Tiêu chuẩn ASTMA213 / Tiêu chuẩn ASTMA249: Các tiêu chuẩn này bao gồm các ống thép không gỉ hàn và liền mạch để sử dụng trong nồi hơi, bộ siêu nhiệt và bộ trao đổi nhiệt. Các loại phổ biến bao gồm:
TP304 / TP304L (EN 1.4301 / 1.4307): Các loại thép không gỉ Austenitic được sử dụng rộng rãi vì khả năng chống ăn mòn và độ bền của chúng.
TP310S / TP310MoLN (EN 1.4845 / 1.4466): Các loại thép không gỉ chịu nhiệt độ cao có khả năng chống oxy hóa tuyệt vời.
TP316 / TP316L (EN 1.4401 / 1.4404): Các loại thép chứa molypden có khả năng chống ăn mòn cao, đặc biệt là trong môi trường clorua.
TP321 (EN 1.4541): Loại thép không gỉ ổn định được sử dụng trong môi trường nhiệt độ cao để ngăn ngừa ăn mòn giữa các hạt.
TP347H / TP347HFG (EN 1.4550 / 1.4961): Cấp thép ổn định, hàm lượng carbon cao dùng cho các ứng dụng nhiệt độ cao như bộ quá nhiệt và nồi hơi.
UNS N08904 (904L) (EN 1.4539): Thép không gỉ siêu austenit có khả năng chống ăn mòn tuyệt vời, đặc biệt là trong môi trường có tính axit.
Tiêu chuẩn ASTMA269: Bao phủ các ống thép không gỉ austenitic hàn và liền mạch để phục vụ mục đích chống ăn mòn nói chung.
Tiêu chuẩn ASTM A789: Tiêu chuẩn cho ống thép không gỉ hai lớp, mang lại khả năng chống ăn mòn tuyệt vời và độ bền cao.
UNS S31803, S32205, S32750, S32760: Các loại thép không gỉ song công và siêu song công, có khả năng chống ăn mòn vượt trội, đặc biệt là trong môi trường có chứa clorua.
EN 10216-5:Tiêu chuẩn Châu Âu áp dụng cho ống thép không gỉ liền mạch, bao gồm các loại sau:
1.4301 / 1.4307 (TP304 / TP304L)
1.4401 / 1.4404 (TP316 / TP316L)
1.4845 (TP310S)
1.4466 (TP310MoLN)
1.4539 (UNS N08904 / 904L)
Ống thép không gỉ có tính linh hoạt cao và được sử dụng trong nhiều ứng dụng khác nhau, bao gồm bộ trao đổi nhiệt, nồi hơi và bộ siêu nhiệt, nơi không chỉ yêu cầu khả năng chống ăn mòn và độ bền nhiệt độ cao mà còn cần thiết để có hiệu suất tối ưu.
V. Hợp kim gốc niken cho nồi hơi và bộ trao đổi nhiệt
Hợp kim gốc niken là một trong những vật liệu chống ăn mòn tốt nhất hiện có và thường được sử dụng trong các ứng dụng nồi hơi và bộ trao đổi nhiệt liên quan đến nhiệt độ khắc nghiệt, môi trường ăn mòn và điều kiện áp suất cao. Hợp kim niken có khả năng chống oxy hóa, sunfua hóa và cacbon hóa vượt trội, khiến chúng trở nên lý tưởng cho bộ trao đổi nhiệt, nồi hơi và bộ siêu nhiệt trong môi trường khắc nghiệt.
Tính chất của hợp kim gốc niken:
Khả năng chống ăn mòn đặc biệt: Hợp kim niken có khả năng chống ăn mòn trong môi trường axit, kiềm và clorua.
Độ ổn định ở nhiệt độ cao: Hợp kim niken vẫn duy trì độ bền và khả năng chống ăn mòn ngay cả ở nhiệt độ cao, khiến chúng phù hợp cho các ứng dụng nhiệt độ cao.
Khả năng chống oxy hóa và sunfua: Hợp kim niken có khả năng chống oxy hóa và sunfua, những hiện tượng có thể xảy ra trong môi trường nhiệt độ cao liên quan đến hợp chất chứa lưu huỳnh.
Tiêu chuẩn và điểm chính:
Tiêu chuẩn ASTMB163 / Tiêu chuẩn ASTMB407 / Tiêu chuẩn ASTM B444: Các tiêu chuẩn này bao gồm các hợp kim gốc niken dùng cho ống liền mạch được sử dụng trong nồi hơi, bộ trao đổi nhiệt và bộ siêu nhiệt. Các loại phổ biến bao gồm:
Inconel 600 / 601: Khả năng chống oxy hóa và ăn mòn ở nhiệt độ cao tuyệt vời, khiến các hợp kim này trở nên lý tưởng cho bộ quá nhiệt và bộ trao đổi nhiệt nhiệt độ cao.
Inconel 625: Có khả năng chống chịu vượt trội trong nhiều môi trường ăn mòn, bao gồm môi trường có tính axit và giàu clorua.
Incoloy 800 / 800H / 800HT: Được sử dụng trong các ứng dụng nhiệt độ cao do có khả năng chống oxy hóa và thấm cacbon tuyệt vời.
Hastelloy C276 / C22: Các hợp kim niken-molypden-crom này được biết đến với khả năng chống ăn mòn vượt trội trong môi trường có tính ăn mòn cao, bao gồm môi trường có tính axit và chứa clorua.
Tiêu chuẩn ASTM B423: Bao phủ các ống liền mạch được làm từ hợp kim niken-sắt-crom-molypden như Hợp kim 825, có khả năng chống nứt do ăn mòn ứng suất và ăn mòn nói chung tuyệt vời trong nhiều môi trường khác nhau.
EN 10216-5: Tiêu chuẩn Châu Âu đối với hợp kim gốc niken được sử dụng trong ống liền mạch cho các ứng dụng chịu nhiệt độ cao và ăn mòn, bao gồm các loại như:
2.4816 (Inconel 600)
2.4851 (Inconel 601)
2.4856 (Inconel 625)
2.4858 (Hợp kim 825)
Hợp kim gốc niken thường được lựa chọn cho các ứng dụng quan trọng đòi hỏi khả năng chống ăn mòn và hiệu suất nhiệt độ cao, chẳng hạn như trong nhà máy điện, chế biến hóa chất và nhà máy lọc dầu khí, lò hơi và bộ trao đổi nhiệt.
VI. Hợp kim Titan và Zirconium cho nồi hơi và bộ trao đổi nhiệt
Hợp kim titan và zirconi mang lại sự kết hợp độc đáo giữa độ bền, khả năng chống ăn mòn và tính chất nhẹ, khiến chúng trở nên lý tưởng cho các ứng dụng cụ thể trong bộ trao đổi nhiệt, bình ngưng và nồi hơi.
Tính chất của hợp kim Titan:
Tỷ lệ độ bền trên trọng lượng cao: Titan bền như thép nhưng nhẹ hơn đáng kể, phù hợp cho các ứng dụng nhạy cảm với trọng lượng.
Khả năng chống ăn mòn tuyệt vời: Hợp kim titan có khả năng chống ăn mòn cao trong nước biển, môi trường axit và môi trường có chứa clorua.
Khả năng chịu nhiệt tốt: Hợp kim titan vẫn duy trì được các tính chất cơ học ở nhiệt độ cao, do đó phù hợp để làm ống trao đổi nhiệt trong nhà máy điện và quá trình xử lý hóa chất.
Tính chất của hợp kim Zirconium:
Khả năng chống ăn mòn vượt trội: Hợp kim Zirconium có khả năng chống ăn mòn cao trong môi trường axit, bao gồm axit sunfuric, axit nitric và axit clohydric.
Độ ổn định ở nhiệt độ cao: Hợp kim Zirconium vẫn duy trì được độ bền và khả năng chống ăn mòn ở nhiệt độ cao, khiến chúng trở nên lý tưởng cho các ứng dụng trao đổi nhiệt ở nhiệt độ cao.
Tiêu chuẩn và điểm chính:
Tiêu chuẩn ASTMB338: Tiêu chuẩn này bao gồm các ống hợp kim titan hàn và liền mạch để sử dụng trong bộ trao đổi nhiệt và bình ngưng tụ. Các loại phổ biến bao gồm:
Cấp 1/Cấp 2: Cấp titan tinh khiết thương mại có khả năng chống ăn mòn tuyệt vời.
Cấp 5 (Ti-6Al-4V): Hợp kim titan có độ bền cao và khả năng chịu nhiệt độ cao.
Tiêu chuẩn ASTMB523: Bao phủ các ống hợp kim zirconium liền mạch và hàn để sử dụng trong bộ trao đổi nhiệt và bình ngưng tụ. Các loại phổ biến bao gồm:
Zirconium 702: Hợp kim zirconium tinh khiết thương mại có khả năng chống ăn mòn vượt trội.
Zirconium 705: Một loại zirconium hợp kim có tính chất cơ học được cải thiện và độ ổn định ở nhiệt độ cao.
Hợp kim titan và zirconi thường được sử dụng trong các môi trường có tính ăn mòn cao như nhà máy khử muối nước biển, ngành công nghiệp chế biến hóa chất và nhà máy điện hạt nhân Lò hơi và Bộ trao đổi nhiệt do khả năng chống ăn mòn vượt trội và đặc tính nhẹ.
VII. Đồng và hợp kim đồng cho nồi hơi và bộ trao đổi nhiệt
Đồng và các hợp kim của nó, bao gồm đồng thau, đồng đỏ và đồng-niken, được sử dụng rộng rãi trong bộ trao đổi nhiệt, bình ngưng và nồi hơi do có khả năng dẫn nhiệt và chống ăn mòn tuyệt vời.
Tính chất của hợp kim đồng:
Độ dẫn nhiệt tuyệt vời: Hợp kim đồng được biết đến với độ dẫn nhiệt cao, rất lý tưởng cho bộ trao đổi nhiệt và bình ngưng tụ.
Khả năng chống ăn mòn: Hợp kim đồng có khả năng chống ăn mòn trong nước, bao gồm cả nước biển, nên phù hợp cho các ứng dụng hàng hải và khử muối.
Tính chất kháng khuẩn: Hợp kim đồng có tính chất kháng khuẩn tự nhiên, thích hợp cho các ứng dụng trong chăm sóc sức khỏe và xử lý nước.
Tiêu chuẩn và điểm chính:
Tiêu chuẩn ASTMB111: Tiêu chuẩn này bao gồm các ống đồng và hợp kim đồng liền mạch dùng trong bộ trao đổi nhiệt, bình ngưng tụ và máy bay hơi. Các loại phổ biến bao gồm:
C44300 (Đồng thau Admiralty): Hợp kim đồng-kẽm có khả năng chống ăn mòn tốt, đặc biệt là trong ứng dụng nước biển.
C70600 (Đồng-Niken 90/10): Hợp kim đồng-niken có khả năng chống ăn mòn tuyệt vời trong nước biển và môi trường biển.
C71500 (Đồng-Niken 70/30): Một hợp kim đồng-niken khác có hàm lượng niken cao hơn để tăng khả năng chống ăn mòn.
Đồng và hợp kim đồng được sử dụng rộng rãi trong các ứng dụng nồi hơi và bộ trao đổi nhiệt trên biển, nhà máy điện và hệ thống HVAC do có khả năng dẫn nhiệt tuyệt vời và khả năng chống ăn mòn của nước biển.
Ngoài nồi hơi và bộ trao đổi nhiệt, tụ điện, bộ siêu nhiệt, bộ gia nhiệt không khí trước và bộ tiết kiệm cũng là những thành phần quan trọng giúp tối ưu hóa đáng kể hiệu suất năng lượng. Ví dụ, tụ điện làm mát khí thải từ cả nồi hơi và bộ trao đổi nhiệt, trong khi bộ siêu nhiệt, mặt khác, làm tăng nhiệt độ hơi nước để cải thiện hiệu suất. Trong khi đó, bộ gia nhiệt không khí trước sử dụng khí thải để làm nóng không khí đi vào, do đó nâng cao hơn nữa hiệu suất tổng thể của hệ thống nồi hơi và bộ trao đổi nhiệt. Cuối cùng, bộ tiết kiệm đóng vai trò quan trọng bằng cách thu hồi nhiệt thải từ khí thải để làm nóng nước trước, giúp giảm mức tiêu thụ năng lượng và tăng hiệu suất của cả nồi hơi và bộ trao đổi nhiệt.
VIII. Kết luận: Lựa chọn vật liệu phù hợp cho nồi hơi và bộ trao đổi nhiệt
Ống liền mạch là một phần không thể thiếu trong hiệu suất của nồi hơi, bộ trao đổi nhiệt, bình ngưng, bộ siêu nhiệt, bộ gia nhiệt không khí và bộ tiết kiệm trong các ngành công nghiệp như phát điện, dầu khí và chế biến hóa chất. Việc lựa chọn vật liệu cho ống liền mạch phụ thuộc vào các yêu cầu ứng dụng cụ thể, bao gồm nhiệt độ, áp suất, khả năng chống ăn mòn và độ bền cơ học.
Thép cacbon có giá cả phải chăng và độ bền cao cho các ứng dụng ở nhiệt độ và áp suất vừa phải.
Thép hợp kim cung cấp hiệu suất và độ bền vượt trội ở nhiệt độ cao trong lò hơi và bộ quá nhiệt.
Thép không gỉ mang lại khả năng chống ăn mòn và độ bền tuyệt vời trong bộ trao đổi nhiệt và bộ quá nhiệt.
Hợp kim gốc niken là sự lựa chọn tốt nhất cho môi trường có tính ăn mòn cao và nhiệt độ cao.
Hợp kim titan và zirconi lý tưởng cho các ứng dụng nhẹ và có tính ăn mòn cao.
Đồng và hợp kim đồng được ưa chuộng vì tính dẫn nhiệt và khả năng chống ăn mòn trong bộ trao đổi nhiệt và tụ điện.
Hệ thống nồi hơi và bộ trao đổi nhiệt đóng vai trò quan trọng trong nhiều ngành công nghiệp khác nhau bằng cách truyền nhiệt hiệu quả từ môi trường này sang môi trường khác. Nồi hơi và bộ trao đổi nhiệt hoạt động cùng nhau để tạo ra và truyền nhiệt, cung cấp nhiệt cần thiết cho quá trình sản xuất hơi nước trong các nhà máy điện và quy trình sản xuất.
Bằng cách hiểu được các đặc tính và ứng dụng của các vật liệu này, các kỹ sư và nhà thiết kế có thể đưa ra quyết định sáng suốt, đảm bảo thiết bị của họ hoạt động an toàn và hiệu quả. Khi lựa chọn vật liệu cho Lò hơi và Bộ trao đổi nhiệt, điều quan trọng là phải xem xét các yêu cầu cụ thể của ứng dụng của bạn. Ngoài ra, bạn nên tham khảo các tiêu chuẩn có liên quan để đảm bảo khả năng tương thích và hiệu suất tối ưu.