ท่อส่งและการวางท่อแบบบนบกเทียบกับแบบนอกชายฝั่ง
การแนะนำ
In the realm of energy transportation, the distinction between onshore and offshore pipelines and piping systems plays a crucial role in the efficiency, safety, and environmental impact of resource extraction and distribution. Onshore pipelines, typically situated on land, are designed to transport oil, gas, and other fluids over varying distances, benefiting from relatively more straightforward access for maintenance and monitoring. Conversely, offshore pipelines, laid on the seabed or suspended in water, present unique engineering challenges due to harsh marine conditions and logistical complexities. Understanding the Onshore vs Offshore Pipeline and Piping in design, construction, and operational considerations between these two types of pipelines is essential for optimizing infrastructure development and ensuring sustainable practices in the energy sector.
Definition: Onshore vs Offshore Pipeline and Piping
What is Pipeline?
Pipeline is a long series of pipes, usually of large diameter, running underground, aboveground and underwater, such as a submarine pipeline, and equipped with fittings, such as valves and pumps, to control the flow of large quantities of fluid over long distances. Pipelines have large diameters, making it easy to transport liquids or gases in bulk from one place to another, sometimes for thousands of miles.
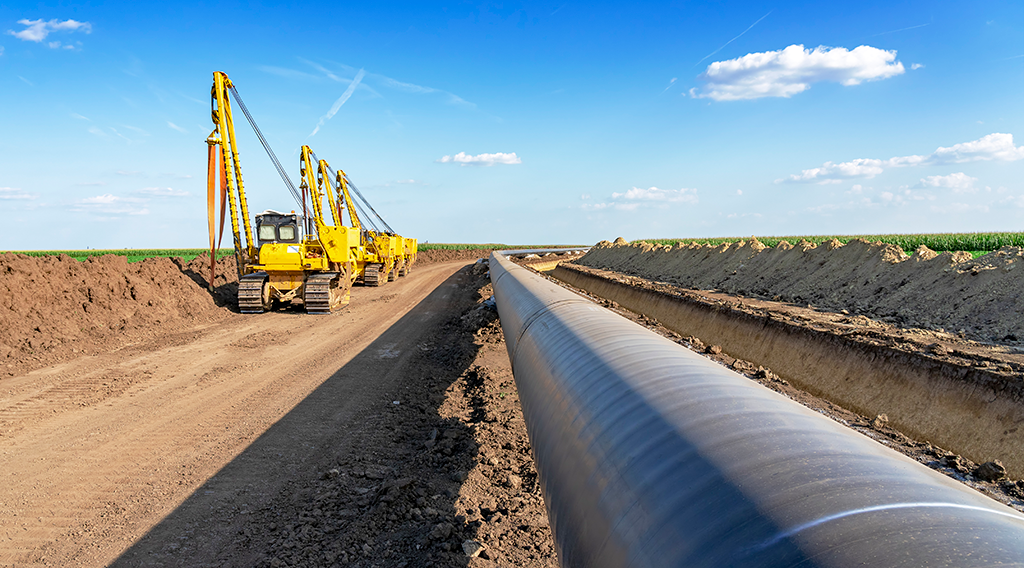
Pipeline
What is Piping?
งานท่อ is a system of pipes used to convey fluids (liquids and gases) from one location to another within the designated boundaries or spaces of petrochemical plants, power plants, refineries, etc. It is also equipped with valves and fittings to control the flow of fluids from one facility to another as needed, but only within the plant’s designated boundaries. Never skip these essential topics when taking an online course on piping engineering. Piping diameters range from 1/2 inch to 80 inches, depending on the facility’s design requirements for fluid transportation, usually from one facility to another within the facility’s boundaries.
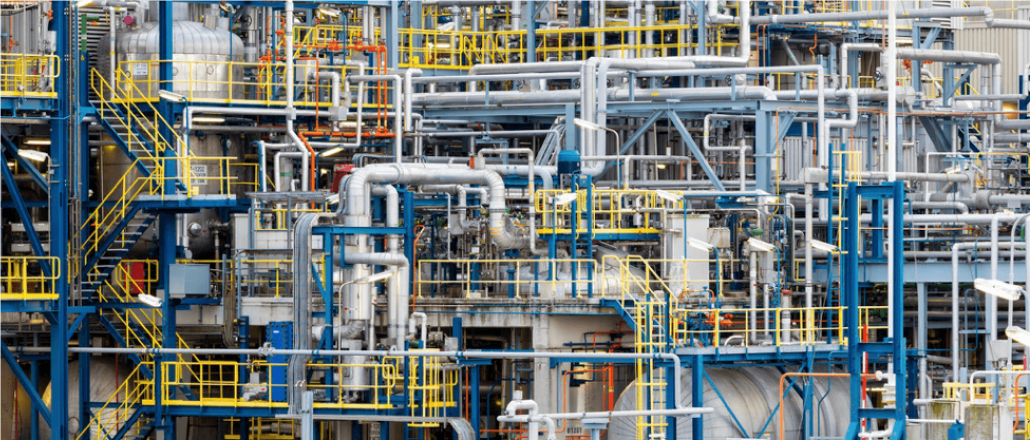
งานท่อ
What is Onshore Pipeline?
Onshore pipelines refer to networks of pipelines and related equipment used to transport fluids such as oil, natural gas, water, and chemicals in a land environment. These pipelines are integral to long-distance oil and gas transportation from oil fields to refineries, from natural gas wells to gas stations, and from crude oil and refined oil tank farms, chemical tank farms, LNG tank farms, and aircraft refueling pipeline operations.
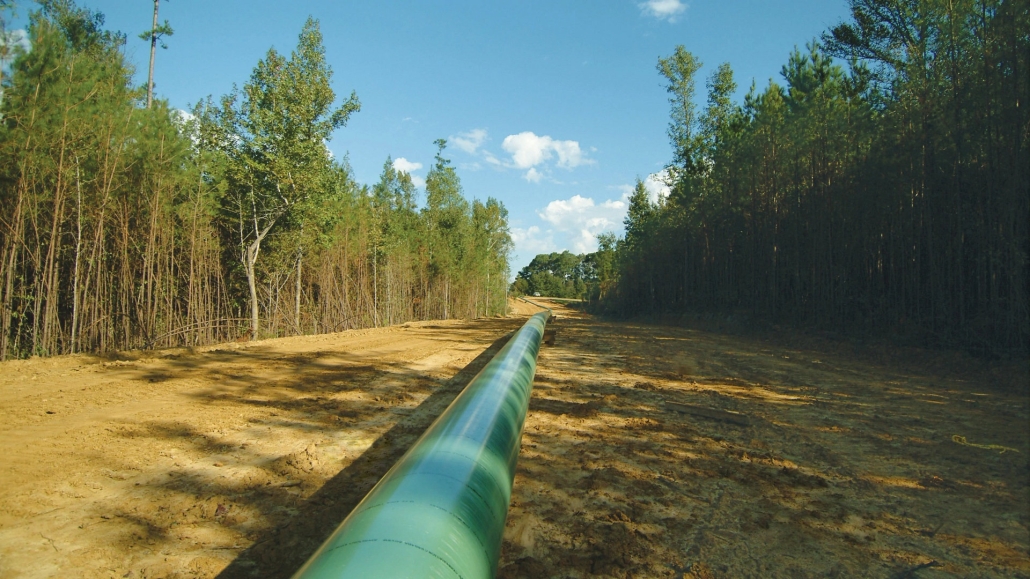
Onshore Pipeline
What is Offshore Pipeline?
Offshore pipelines refer to the network of pipes and related equipment used to transport fluids such as oil, gas, water, and chemicals in an offshore environment. These pipelines are integral to operating offshore oil rigs, platforms and floating production storage and offloading units (FPSOs). The unique conditions of the offshore environment, such as high salinity, extreme temperatures, and strong currents, present significant challenges to the design and maintenance of these systems.
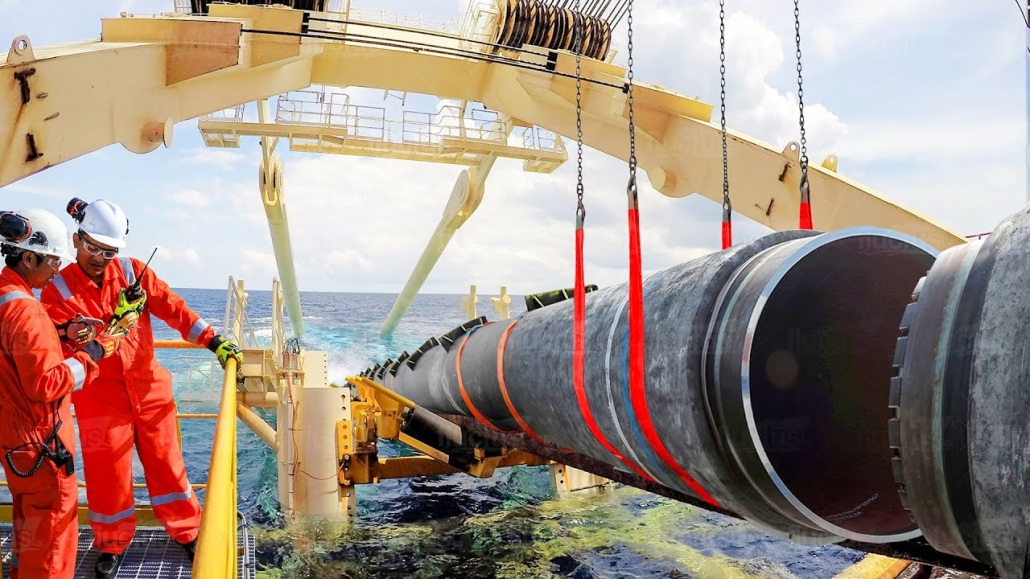
Offshore Pipeline
Main Differences: Onshore vs Offshore Pipeline and Piping
Comparison Table: Onshore vs Offshore Pipeline and Piping
ข้อมูลจำเพาะ | บนบก | นอกชายฝั่ง | ||
Pipeline | งานท่อ | Pipeline | งานท่อ | |
รหัสการออกแบบ | – ASME B31.4: Pipeline Transportation Systems for Liquids and Slurries – ASME B31.8: Gas Transmission and Distribution Piping Systems |
ASME B31.3: Process Piping | – DNVGL-ST-F101: Submarine pipeline systems – API RP 1111: Design, Construction, Operation, and Maintenance of Offshore Hydrocarbon Pipelines (Limit state design) |
ASME B31.3: Process Piping |
ขอบเขต | Outside plant boundary (Villages, fields, rivers, canals, railways, highways, cities, deserts, forests, hills, etc.) |
Within plant boundary | Outside plant boundary | Within plant boundary |
Type of pipe | API Spec 5L: Specification for Line pipes | – ASTM – BS – API 5L |
– API Spec 5L: Specification for Line pipes – DNVGล-ST-F101: Submarine Pipeline Systems |
มาตรฐาน ASTM |
วาล์ว | – API 6D: Specification for Pipeline and Piping Valves – Full Bore (FB) Ball Valves are used for pigs. |
– BS – API Standard – Full bore (FB) and Reduced bore (RB) |
– Full bore Valves: for smooth passage of intelligent pigs – API 6D SS: Specification on Subsea Pipeline Valves |
– RB valves – BS/API standards |
การเชื่อม | – API Std. 1104: Welding of Pipelines and Related Facilities – Type of welding: Automatic / Semi-Automatic/ Manual |
– ASME Sec. IX: Standard for Welding and Brazing Procedures, Welders, Brazers and Welding and Brazing Operators – Type of welding: Manual (mostly) |
– API Std. 1104: Welding of Pipelines and Related Facilities – Mostly automatic welding on pipelay barge. |
– ASME Sec. IX: Standard for Welding and Brazing Procedures, Welders, Brazers and Welding and Brazing Operators – Manual welding at the fabrication yard. |
Weld joint inspection (NDT requirements) | 100% by Automatic UT or RT (by using X-Ray) | 5% to 100% (mostly by using gamma rays) |
100% by Automatic UT | From 10% to 100% as required |
Analyses | – Wall Thickness Analysis – Elastic Bend Radius Analysis – Stability Analysis for Water Bodies/ Marshy Areas – Horizontal directional drilling design analysis – Railroad/ Highway Crossing Analysis – Casing Pipe Analysis for Crossings – Seismic Analysis |
– Piping wall thickness calculation – Piping Stress Analysis Static Analysis Dynamic Analysis Wind Analysis Flange Leakage Analysis Seismic Analysis |
– Wall thickness Analysis – On-bottom Stability – Span Analysis – Global Buckling – Lateral and Upheaval – Pipeline Expansion Analysis – Riser Design (Span, Stress & Flexibility Analysis) – Riser Clamp Design – Pipeline Crossing Design and Analysis |
– Deck piping stress analysis |
การติดตั้ง | Buried (mostly) | Above ground/On rack/slippers/T-postal etc. | Subsea (in water on the seabed or buried in the seabed) | Deck Platform Piping (similar to plant) |
Special Installations | – Across rivers – Horizontal Directional Drilling (HDD) method – Micro-tunnelling method – Across road/ rail/ highway – Auger boring/ jacking boring method – Shallow HDD – Ghats/ Hills |
– Modular installations – Finning – Studding – Jacketing – Spooling inside warehouse – U/G piping for cooling water |
– S-lay Method (for shallow water installation) – J-Lay Method (for deep water installation) – Shore pull/ barge pull near Land Fall Point (LFP) |
Along with the deck structure |
Special Equipment | – Sectionalizing Valves (Remote operated) – Insulating Joints – Scraper Launcher/ Receiver – Stem Extended Valves (for buried valves) – Flow Tee – Long Radius bends (R=6D) – Cold field bends (R = 30D or 40D) |
– Expansion Joints – Motor Operator Valves (MOV) – Cryogenic Valves – Springs |
– Subsea Isolation Valve (SSIV) – LR Bends – Flow tee – Pipeline End Manifold (PLEM) – Single Point Mooring (SPM) system – Submarine hoses – Floating hoses – Cables and umbilical installation – Piggy-back pipelines |
ไม่สามารถใช้ได้ |
Survey | – Topographical Survey (all along the pipeline route) – Geotechnical investigation (all along the pipeline route) – Soil resistivity survey (all along the pipeline route) – Hydrological Survey for water bodies (for scour depth calculation) – Cadastral Survey (for RoU acquisition) |
– Wind profile from meteorology – Seismic study of plot |
– Geophysical survey/ Bathymetric Survey by using side scan sonar, sub-bottom profiler, and echo-sounder – Met-Ocean data collection – Geotechnical data of the pipeline route |
ไม่สามารถใช้ได้ |
Corrosion Protection Coating | – Three Layer Polyethylene (3LPE) coating – Three Layer Polypropylene (3LPP) coating – Fusion bonded epoxy (FBE) coating – Coal tar enamel (CTE) Coating |
Painting | Coatings such as: – Coal Tar Enamel Coating (CTE) – Three-layer polyethylene coating (3LPE) – Three-layer polypropylene coating (3LPP) – Double-layer fusion bonded epoxy coating (2FBE) |
Painting |
Cathodic Protection System | – Impressed Current Cathodic Protection (ICCP) system – Sacrificial Anode (limited locations) |
Not applicable | Sacrificial Anodic Cathodic Protection (SACP) system | ไม่สามารถใช้ได้ |
Hydrostatic testing | – Gauge Plate run of 95% of the ID of the highest pipe thickness – Test Pressure Minimum: 1.25 times of Design Pressure (for liquid pipelines) 1.25 to 1.5 times of Design Pressure (for gas pipelines) Maximum: Pressure equivalent to Hoop stress of 95% of SMYS of pipe material – Hold period: 24 hours |
– No gauge plate run is done. Generally, cardboard blasting is done to clean the piping. – Test Pressure Minimum: 1.5 × Design Pressure × Temperature Factor Maximum: Based on line schedule – Hold period: 2 – 6 hours |
– Gauge Plate run of 95% of the ID of the highest pipeline thickness. – Test Pressure Minimum: 1.25 times x Design Pressure – Hold period: 24 hours |
– No gauging is done. – Test Pressure Maximum: As per line schedule – Hold period: 2 hours |
Preservation | – Preservation of pipeline with corrosion-inhibited water or by filling of inert gas (N2) | Not applicable | ||
Pigging | Intelligent Pigging | Not applicable | Compliant | Not applicable |
Machines/Equipment required for installation | – Trencher – Backhoe/ Excavator – Side Boom – Cold field bending machine – Holiday Detection Machines – Pneumatic/ Hydraulic Internal Clamps |
Crane/ Hydra | – Pipelay Barge – Derrick Barge – Diving support vessel – Dynamic Positioning (DP) barge (for deepwater) |
Pre-fabricated deck piping |
Conclusion: Onshore vs Offshore Pipeline and Piping
In summary, Onshore pipelines are usually buried or erected on land to transport oil, natural gas, drinking water, sewage, seawater, slurry, etc. Onshore piping is typically erected in petrochemical plants, power plants, refineries, fire protection systems, water treatment systems, etc., while Offshore pipelines are buried on the seabed. Offshore piping typically consists of transmission and structural support pipeline systems on offshore drilling platforms. Special offshore equipment includes underwater isolation valves, tees, and submarine hoses. Offshore surveys include geophysics, bathymetry, and ocean data collection, while onshore surveys focus on topographic and geotechnical engineering studies.