Przyczynę pęknięcia pierścieniowego na końcu rury bezszwowej rury stalowej SAE 4140 zbadano za pomocą badania składu chemicznego, testu twardości, obserwacji metalograficznej, skaningowego mikroskopu elektronowego i analizy widma energetycznego. Wyniki pokazują, że pęknięcie pierścieniowe rury stalowej bezszwowej SAE 4140 jest pęknięciem hartowniczym, występującym na ogół na końcu rury. Przyczyną pęknięcia hartowniczego są różne szybkości chłodzenia między ścianami wewnętrznymi i zewnętrznymi, a szybkość chłodzenia ściany zewnętrznej jest znacznie wyższa niż ściany wewnętrznej, co powoduje pęknięcie spowodowane koncentracją naprężeń w pobliżu położenia ściany wewnętrznej. Pęknięcie w kształcie pierścienia można wyeliminować, zwiększając szybkość chłodzenia ściany wewnętrznej rury stalowej podczas hartowania, poprawiając jednorodność szybkości chłodzenia między ścianą wewnętrzną i zewnętrzną oraz kontrolując temperaturę po hartowaniu w zakresie 150 ~ 200 ℃, aby zmniejszyć naprężenie hartownicze przez samoodpuszczanie.
SAE 4140 to stal konstrukcyjna niskostopowa CrMo, jest to gatunek amerykańskiej normy ASTM A519, w krajowej normie 42CrMo na podstawie wzrostu zawartości Mn; dlatego hartowność SAE 4140 została dodatkowo ulepszona. Rura stalowa bez szwu SAE 4140, zamiast litych odkuwek, walcowanie kęsów różnych typów wałów pustych, cylindrów, tulei i innych części może znacznie poprawić wydajność produkcji i zaoszczędzić stal; Rura stalowa SAE 4140 jest szeroko stosowana w narzędziach wiertniczych śrubowych do górnictwa ropy naftowej i gazu oraz innym sprzęcie wiertniczym. Obróbka cieplna rury stalowej bez szwu SAE 4140 może spełniać wymagania dotyczące różnych wytrzymałości stali i dopasowania wytrzymałości poprzez optymalizację procesu obróbki cieplnej. Mimo to często okazuje się, że wpływa to na wady dostawy produktu w procesie produkcyjnym. Niniejszy artykuł koncentruje się głównie na rurze stalowej SAE 4140 w procesie hartowania w środku grubości ścianki końca rury, przeprowadza analizę pęknięć pierścieniowych i przedstawia środki zaradcze.
1. Materiały i metody testowe
Firma opracowała specyfikacje dla rur stalowych bez szwu klasy SAE 4140 o wymiarach ∅ 139,7 × 31,75 mm, proces produkcyjny dla nagrzewania wlewków → przebijania → walcowania → kalibrowania → odpuszczania (850 ℃ czas namaczania 70 min hartowania + obrót rury poza chłodzeniem natryskowym wodą +735 ℃ czas namaczania 2 h odpuszczania) → wykrywanie wad i kontrola. Po obróbce odpuszczania, kontrola wykrywania wad wykazała, że w środku grubości ścianki na końcu rury znajdowało się pęknięcie pierścieniowe, jak pokazano na rys. 1; pęknięcie pierścieniowe pojawiło się w odległości około 21~24 mm od zewnątrz, okrążało obwód rury i było częściowo nieciągłe, podczas gdy w korpusie rury nie znaleziono takiego defektu.
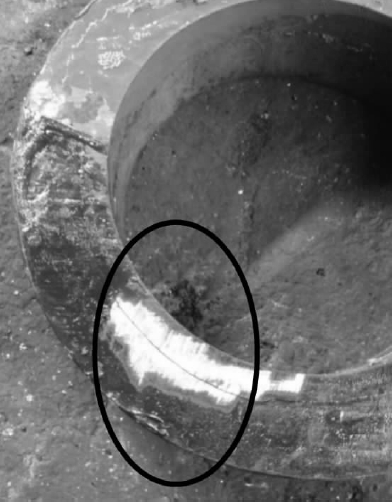
Rys.1 Pęknięcie pierścieniowe na końcu rury
Pobierz partię próbek hartowanych rur stalowych w celu analizy hartowania i obserwacji organizacji hartowania oraz analizy widmowej składu rury stalowej, a jednocześnie pobierz próbki o dużym powiększeniu w celu obserwacji mikromorfologii pęknięć, poziomu wielkości ziarna, a także w skaningowym mikroskopie elektronowym ze spektrometrem w celu analizy pęknięć w składzie wewnętrznym mikroobszaru.
2. Wyniki testów
2.1 Skład chemiczny
Tabela 1 przedstawia wyniki analizy widmowej składu chemicznego. Skład pierwiastków jest zgodny z wymaganiami normy ASTM A519.
Tabela 1 Wyniki analizy składu chemicznego (ułamek masowy, %)
Element |
C |
Si |
Mn |
P |
S |
Kr |
Pon |
Cu |
Ni |
Treść |
0.39 |
0.20 |
0.82 |
0.01 |
0.005 |
0.94 |
0.18 |
0.05 |
0.02 |
Wymagania ASTM A519 |
0.38-0.43 |
0.15-0.35 |
0.75-1.00 |
≤ 0,04 |
≤ 0,04 |
0.8-1.1 |
0.15-0.25 |
≤ 0,35 |
≤ 0,25 |
2.2 Badanie hartowności rur
Na hartowanych próbkach całkowitej grubości ścianki hartowanie twardości wyniki całkowitej grubości ścianki, jak pokazano na Rysunku 2, można zobaczyć na Rysunku 2, w 21 ~ 24 mm od zewnątrz hartowania twardość zaczęła znacząco spadać, a od zewnątrz 21 ~ 24 mm jest wysokotemperaturowe odpuszczanie rury znalezione w obszarze pęknięcia pierścieniowego, obszar poniżej i powyżej grubości ścianki twardości skrajnej różnicy między położeniem grubości ścianki obszaru osiągnął 5 (HRC) lub około. Różnica twardości między dolną i górną grubością ścianki tego obszaru wynosi około 5 (HRC). Organizacja metalograficzna w stanie hartowanym jest pokazana na Rysunku 3. Z organizacji metalograficznej na Rysunku 3; widać, że organizacja w zewnętrznym obszarze rury to niewielka ilość ferrytu + martenzytu, podczas gdy organizacja w pobliżu wewnętrznej powierzchni nie jest hartowana, z niewielką ilością ferrytu i bainitu, co prowadzi do niskiej twardości hartowniczej od zewnętrznej powierzchni rury do wewnętrznej powierzchni rury w odległości 21 mm. Wysoki stopień spójności pęknięć pierścieniowych w ściance rury i położenie skrajnej różnicy w twardości hartowniczej sugerują, że pęknięcia pierścieniowe prawdopodobnie powstaną w procesie hartowania. Wysoka spójność między położeniem pęknięć pierścieniowych a niższą twardością hartowniczą wskazuje, że pęknięcia pierścieniowe mogły powstać w procesie hartowania.
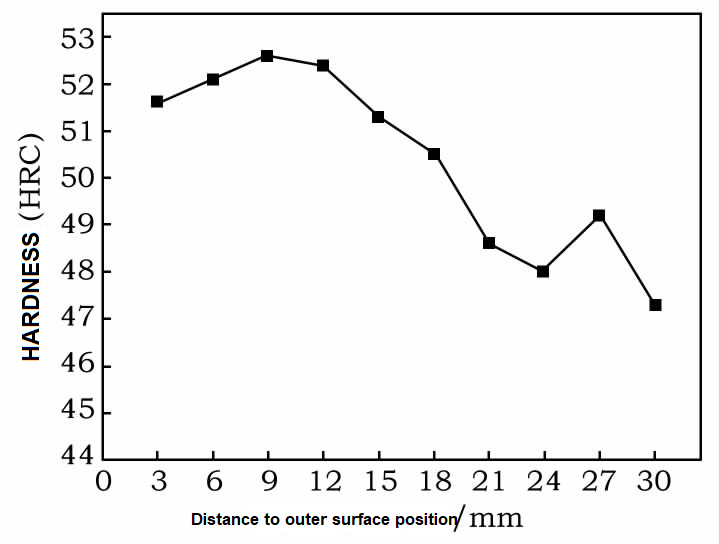
Rys.2 Wartość twardości hartowniczej przy pełnej grubości ścianki
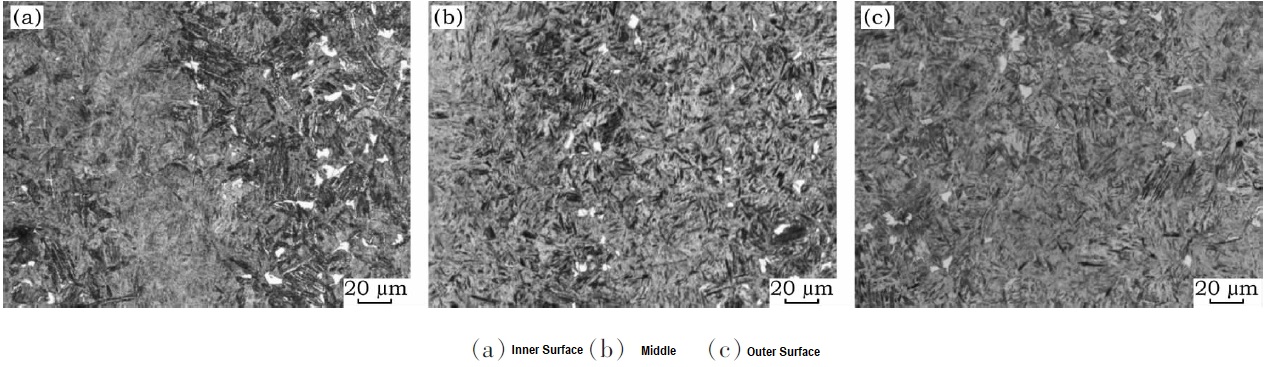
Rys.3 Struktura hartowania rury stalowej
2.3 Wyniki metalograficzne rury stalowej pokazano odpowiednio na rys. 4 i 5.
Organizacja matrycy rury stalowej to odpuszczony austenit + niewielka ilość ferrytu + niewielka ilość bainitu, o wielkości ziarna 8, co jest średnią odpuszczoną organizacją; pęknięcia rozciągają się wzdłuż kierunku podłużnego, który należy do pęknięć krystalicznych, a obie strony pęknięć mają typowe cechy angażowania się; występuje zjawisko odwęglenia po obu stronach, a na powierzchni pęknięć można zaobserwować warstwę szarego tlenku o wysokiej temperaturze. Po obu stronach występuje odwęglenie, a na powierzchni pęknięcia można zaobserwować warstwę szarego tlenku o wysokiej temperaturze, a w pobliżu pęknięcia nie można zobaczyć żadnych niemetalicznych wtrąceń.
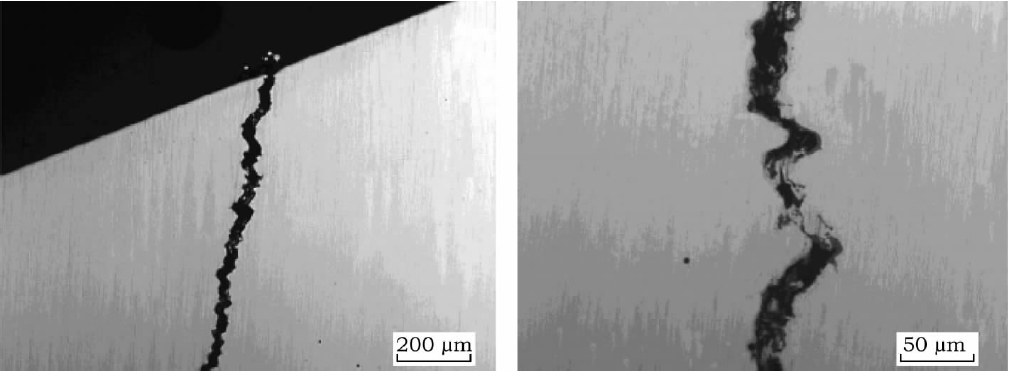
Rys.4 Obserwacje morfologii pęknięć
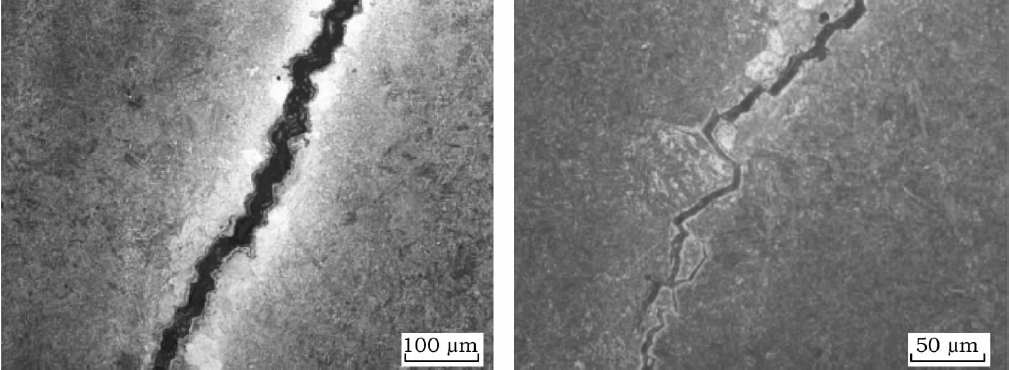
Rys.5 Mikrostruktura pęknięcia
2.4 Wyniki analizy morfologii pęknięć i widma energii
Po otwarciu pęknięcia obserwuje się mikromorfologię pęknięcia pod skaningowym mikroskopem elektronowym, jak pokazano na rys. 6, który pokazuje, że pęknięcie zostało poddane działaniu wysokich temperatur i na powierzchni nastąpiło utlenianie w wysokiej temperaturze. Pęknięcie występuje głównie wzdłuż pęknięcia kryształu, a wielkość ziarna waha się od 20 do 30 μm, i nie stwierdzono grubych ziaren ani nieprawidłowych defektów organizacyjnych; analiza widma energetycznego pokazuje, że powierzchnia pęknięcia składa się głównie z żelaza i jego tlenków i nie stwierdzono żadnych nieprawidłowych obcych pierwiastków. Analiza widmowa pokazuje, że powierzchnia pęknięcia składa się głównie z żelaza i jego tlenków, bez żadnych nieprawidłowych obcych pierwiastków.
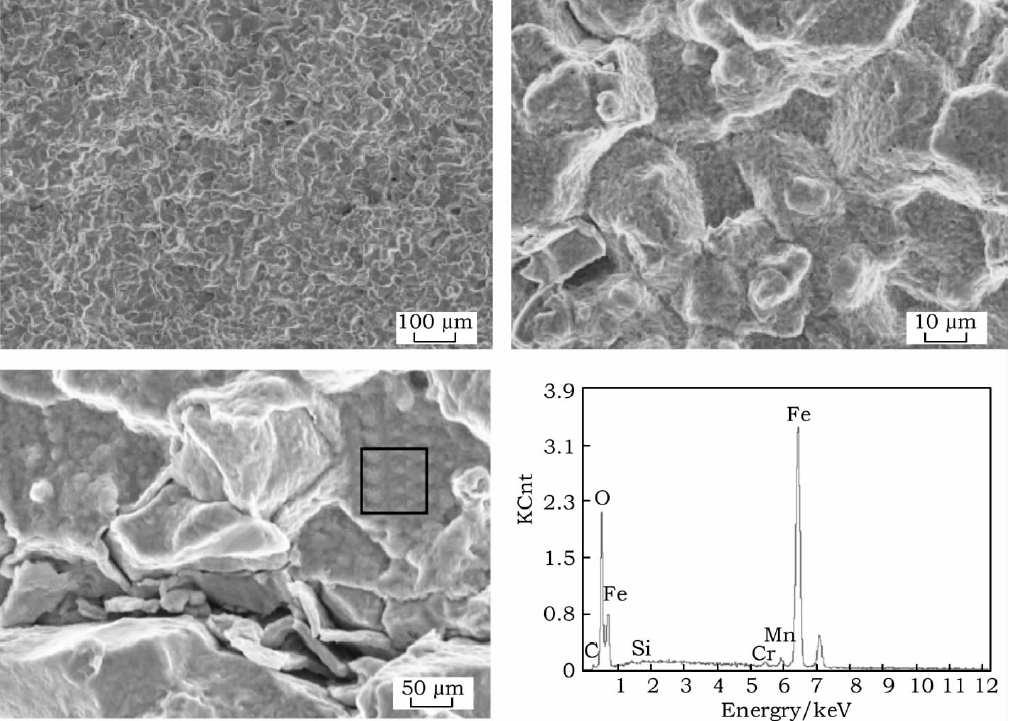
Rys.6 Morfologia pęknięcia
3 Analiza i dyskusja
3.1 Analiza uszkodzeń pęknięć
Z punktu widzenia mikromorfologii pęknięć, otwór pęknięcia jest prosty; ogon jest zakrzywiony i ostry; ścieżka rozszerzenia pęknięcia pokazuje cechy pękania wzdłuż kryształu, a dwie strony pęknięcia mają typowe cechy zazębienia, które są typowymi cechami pęknięć hartowniczych. Mimo to badanie metalograficzne wykazało, że po obu stronach pęknięcia występują zjawiska odwęglenia, co nie jest zgodne z cechami tradycyjnych pęknięć hartowniczych, biorąc pod uwagę fakt, że temperatura odpuszczania rury stalowej wynosi 735 ℃, a Ac1 wynosi 738 ℃ w SAE 4140, co nie jest zgodne z konwencjonalnymi cechami pęknięć hartowniczych. Biorąc pod uwagę, że temperatura odpuszczania zastosowana do rury wynosi 735 °C, a Ac1 normy SAE 4140 wynosi 738 °C, a więc wartości te są bardzo zbliżone, przyjmuje się, że odwęglenie po obu stronach pęknięcia jest związane z odpuszczaniem w wysokiej temperaturze podczas odpuszczania (735 °C) i nie jest pęknięciem, które istniało już przed obróbką cieplną rury.
3.2 Przyczyny pękania
Przyczyny pęknięć hartowniczych są na ogół związane z temperaturą nagrzewania hartowniczego, szybkością chłodzenia hartowniczego, wadami metalurgicznymi i naprężeniami hartowniczymi. Na podstawie wyników analizy składu chemicznego, skład chemiczny rury spełnia wymagania gatunku stali SAE 4140 w normie ASTM A519 i nie znaleziono żadnych przekraczających norm pierwiastków; nie znaleziono żadnych wtrąceń niemetalicznych w pobliżu pęknięć, a analiza widma energii przy pęknięciu pęknięcia wykazała, że szarymi produktami utleniania w pęknięciach były Fe i jego tlenki, i nie zaobserwowano żadnych nieprawidłowych obcych pierwiastków, więc można wykluczyć, że wady metalurgiczne spowodowały pęknięcia pierścieniowe; klasa wielkości ziarna rury wynosiła 8, a klasa wielkości ziarna wynosiła 7, a klasa wielkości ziarna wynosiła 8, a klasa wielkości ziarna wynosiła 8. Poziom wielkości ziarna rury wynosi 8; ziarno jest drobne, a nie grube, co wskazuje, że pęknięcie hartownicze nie ma nic wspólnego z temperaturą nagrzewania hartowniczego.
Powstawanie pęknięć hartowniczych jest ściśle związane z naprężeniami hartowniczymi, podzielonymi na naprężenia termiczne i organizacyjne. Naprężenie termiczne jest spowodowane procesem chłodzenia rury stalowej; warstwa powierzchniowa i serce rury stalowej szybkość chłodzenia nie są spójne, co powoduje nierównomierne kurczenie się materiału i naprężenia wewnętrzne; wynikiem jest warstwa powierzchniowa rury stalowej poddawana naprężeniom ściskającym, a serce naprężeniom rozciągającym; naprężenia tkankowe to hartowanie organizacji rury stalowej do przemiany martenzytycznej, wraz z rozszerzeniem objętości niespójności w generowaniu naprężeń wewnętrznych, organizacja naprężeń generowanych przez wynik jest warstwą powierzchniową naprężeń rozciągających, środkiem naprężeń rozciągających. Te dwa rodzaje naprężeń w rurze stalowej występują w tej samej części, ale rola kierunkowa jest odwrotna; połączony efekt wyniku jest taki, że jeden z dwóch dominujących czynników naprężeń, dominująca rola naprężenia termicznego jest wynikiem rozciągania serca przedmiotu obrabianego, ciśnienia powierzchniowego; dominującą rolę odgrywa naprężenie tkanki, będące wynikiem rozciągania powierzchniowego przedmiotu obrabianego.
Hartowanie rur stalowych SAE 4140 przy użyciu obrotowego zewnętrznego natrysku chłodzącego, szybkość chłodzenia powierzchni zewnętrznej jest znacznie większa niż powierzchni wewnętrznej, cały zewnętrzny metal rury stalowej jest hartowany, podczas gdy metal wewnętrzny nie jest całkowicie hartowany, aby wytworzyć część organizacji ferrytu i bainitu, metal wewnętrzny ze względu na metal wewnętrzny nie może być w pełni przekształcony w organizację martenzytyczną, metal wewnętrzny rury stalowej jest nieuchronnie poddawany naprężeniom rozciągającym generowanym przez rozszerzanie się ściany zewnętrznej martenzytu, a jednocześnie ze względu na różne rodzaje organizacji jego objętość właściwa jest różna między metalem wewnętrznym i zewnętrznym. Jednocześnie ze względu na różne rodzaje organizacji, objętość właściwa warstw wewnętrznej i zewnętrznej metalu jest różna, a szybkość skurczu nie jest taka sama podczas chłodzenia, naprężenie rozciągające będzie również generowane na styku dwóch typów organizacji, a rozkład naprężeń jest zdominowany przez naprężenia cieplne, a naprężenie rozciągające generowane na styku dwóch typów organizacji wewnątrz rury jest największy, powodując pęknięcia pierścieniowe występujące w obszarze grubości ścianki rury blisko powierzchni wewnętrznej (21~24 mm od powierzchni zewnętrznej); ponadto koniec rury stalowej jest wrażliwą na geometrię częścią całej rury, podatną na generowanie naprężeń. Ponadto koniec rury jest wrażliwą na geometrię częścią całej rury, która jest podatna na koncentrację naprężeń. To pęknięcie pierścieniowe zwykle występuje tylko na końcu rury, a takich pęknięć nie znaleziono w korpusie rury.
Podsumowując, pęknięcia pierścieniowe hartowanej rury stalowej o grubych ściankach SAE 4140 są spowodowane nierównomiernym chłodzeniem ścian wewnętrznych i zewnętrznych; szybkość chłodzenia ściany zewnętrznej jest znacznie wyższa niż ściany wewnętrznej; produkcja rury stalowej o grubych ściankach SAE 4140 w celu zmiany istniejącej metody chłodzenia, nie może być stosowana wyłącznie poza procesem chłodzenia, konieczność wzmocnienia chłodzenia ściany wewnętrznej rury stalowej, w celu poprawy jednorodności szybkości chłodzenia ścian wewnętrznych i zewnętrznych rury stalowej o grubych ściankach w celu zmniejszenia koncentracji naprężeń, eliminując pęknięcia pierścieniowe. Pęknięcia pierścieniowe.
3.3 Środki poprawy
Aby uniknąć pęknięć hartowniczych, w projekcie procesu hartowania wszystkie warunki, które przyczyniają się do rozwoju naprężeń rozciągających hartowniczych, są czynnikami powstawania pęknięć, w tym temperatura nagrzewania, proces chłodzenia i temperatura wylotu. Proponowane ulepszone środki procesowe obejmują: temperaturę hartowania 830-850 ℃; zastosowanie wewnętrznej dyszy dopasowanej do linii środkowej rury, kontrolę odpowiedniego wewnętrznego przepływu natrysku, poprawę szybkości chłodzenia otworu wewnętrznego w celu zapewnienia jednorodności szybkości chłodzenia wewnętrznych i zewnętrznych ścian grubościennej rury stalowej; kontrolę temperatury po hartowaniu 150-200 ℃, zastosowanie resztkowej temperatury rury stalowej samoodpuszczania, zmniejszenie naprężeń hartowniczych w rurze stalowej.
Zastosowanie ulepszonej technologii daje ∅158,75 × 34,93 mm, ∅139,7 × 31,75 mm, ∅254 × 38,1 mm, ∅224 × 26 mm itd., zgodnie z dziesiątkami specyfikacji rur stalowych. Po badaniu wad metodą ultradźwiękową produkty są kwalifikowane, bez pęknięć pierścieniowo-wytłaczających.
4. Wnioski
(1) Zgodnie z makroskopowymi i mikroskopowymi charakterystykami pęknięć rur, pęknięcia pierścieniowe na końcach rur stalowych SAE 4140 należą do pęknięć spowodowanych naprężeniem hartowniczym, które zwykle występuje na końcach rur.
(2) Hartowane pęknięcia pierścieniowe grubościennej rury stalowej SAE 4140 są spowodowane nierównomiernym chłodzeniem ścian wewnętrznych i zewnętrznych. Szybkość chłodzenia ściany zewnętrznej jest znacznie wyższa niż ściany wewnętrznej. Aby poprawić równomierność szybkości chłodzenia ścian wewnętrznych i zewnętrznych grubościennej rury stalowej, produkcja grubościennej rury stalowej SAE 4140 wymaga wzmocnienia chłodzenia ściany wewnętrznej.