Invoering
In industrieën zoals energieopwekking, olie en gas, petrochemie en raffinaderijen zijn naadloze buizen essentiële componenten, met name in apparatuur die bestand moet zijn tegen extreme temperaturen, hoge druk en agressieve, corrosieve omgevingen. Boilers, warmtewisselaars, condensors, oververhitters, luchtvoorverwarmers en economizers gebruiken deze buizen. Elk van deze toepassingen vereist specifieke materiaaleigenschappen om prestaties, veiligheid en levensduur te garanderen. De selectie van naadloze buizen voor de boiler en warmtewisselaar is afhankelijk van de specifieke temperatuur, druk, corrosiebestendigheid en mechanische sterkte.
Deze gids biedt een diepgaand inzicht in de verschillende materialen die worden gebruikt voor naadloze buizen, waaronder koolstofstaal, gelegeerd staal, roestvrij staal, titaniumlegeringen, nikkellegeringen, koperlegeringen en zirkoniumlegeringen. We zullen ook de relevante normen en klassen onderzoeken, waardoor u beter geïnformeerde beslissingen kunt nemen voor uw Boiler and Heat Exchanger-projecten.
Overzicht van CS, AS, SS, nikkellegeringen, titanium- en zirkoniumlegeringen, koper en koperlegeringen
1. Corrosiebestendige eigenschappen
Elk materiaal dat voor naadloze buizen wordt gebruikt, heeft specifieke corrosiebestendige eigenschappen die bepalen hoe geschikt het is voor verschillende omgevingen.
Koolstofstaal: Beperkte corrosiebestendigheid, doorgaans gebruikt met beschermende coatings of voeringen. Onderhevig aan roestvorming in aanwezigheid van water en zuurstof, tenzij behandeld.
Gelegeerd staal: Matige weerstand tegen oxidatie en corrosie. Legeringtoevoegingen zoals chroom en molybdeen verbeteren de corrosiebestendigheid bij hoge temperaturen.
Roestvrij staal: Uitstekende weerstand tegen algemene corrosie, spanningscorrosie en pitting vanwege het chroomgehalte. Hogere kwaliteiten, zoals 316L, hebben een verbeterde weerstand tegen chloride-geïnduceerde corrosie.
Nikkelgebaseerde legeringen: Uitstekende bestendigheid tegen agressieve omgevingen zoals zure, alkalische en chloriderijke omgevingen. Zeer corrosieve toepassingen gebruiken legeringen zoals Inconel 625, Hastelloy C276 en Alloy 825.
Titanium en zirkonium: Superieure bestendigheid tegen zeewaterpekels en andere zeer corrosieve media. Titanium is vooral bestand tegen chloride en zure omgevingen, terwijl zirkoniumlegeringen excelleren in zeer zure omstandigheden.
Koper en koperlegeringen: Uitstekende corrosiebestendigheid in zoet- en zeewater, waarbij koper-nikkellegeringen een uitzonderlijke bestendigheid in maritieme omgevingen vertonen.
2. Fysische en thermische eigenschappen
Koolstofstaal:
Dichtheid: 7,85 g/cm³
Smeltpunt: 1.425-1.500°C
Thermische geleidbaarheid: ~50 W/m·K
Gelegeerd staal:
Dichtheid: varieert lichtjes per legeringselement, meestal rond de 7,85 g/cm³
Smeltpunt: 1.450-1.530°C
Thermische geleidbaarheid: Lager dan koolstofstaal vanwege legeringselementen.
Roestvrij staal:
Dichtheid: 7,75-8,0 g/cm³
Smeltpunt: ~1.400-1.530°C
Thermische geleidbaarheid: ~16 W/m·K (lager dan koolstofstaal).
Nikkelgebaseerde legeringen:
Dichtheid: 8,4-8,9 g/cm³ (afhankelijk van legering)
Smeltpunt: 1.300-1.400°C
Thermische geleidbaarheid: Meestal laag, ~10-16 W/m·K.
Titanium:
Dichtheid: 4,51 g/cm³
Smeltpunt: 1.668°C
Thermische geleidbaarheid: ~22 W/m·K (relatief laag).
Koper:
Dichtheid: 8,94 g/cm³
Smeltpunt: 1.084°C
Thermische geleidbaarheid: ~390 W/m·K (uitstekende thermische geleidbaarheid).
3. Chemische samenstelling
Koolstofstaal: Voornamelijk ijzer met 0,3%-1,2% koolstof en kleine hoeveelheden mangaan, silicium en zwavel.
Gelegeerd staal: Bevat elementen zoals chroom, molybdeen, vanadium en wolfraam om de sterkte en temperatuurbestendigheid te verbeteren.
Roestvrij staal: Bevat doorgaans 10.5%-30% chroom, samen met nikkel, molybdeen en andere elementen, afhankelijk van de klasse.
Nikkelgebaseerde legeringen: Overwegend nikkel (40%-70%) met chroom, molybdeen en andere legeringselementen om de corrosiebestendigheid te verbeteren.
Titanium: Graad 1 en 2 zijn commercieel zuiver titanium, terwijl klasse 5 (Ti-6Al-4V) 6% aluminium en 4% vanadium bevat.
Koperlegeringen: Koperlegeringen bevatten verschillende elementen zoals nikkel (10%-30%) voor corrosiebestendigheid (bijv. Cu-Ni 90/10).
4. Mechanische eigenschappen
Koolstofstaal: Treksterkte: 400-500 MPa, Vloeigrens: 250-350 MPa, Rek: 15%-25%
Gelegeerd staal: Treksterkte: 500-900 MPa, Vloeigrens: 300-700 MPa, Rek: 10%-25%
Roestvrij staal: Treksterkte: 485-690 MPa (304/316), Vloeigrens: 170-300 MPa, Rek: 35%-40%
Nikkelgebaseerde legeringen: Treksterkte: 550-1.000 MPa (Inconel 625), Vloeigrens: 300-600 MPa, Rek: 25%-50%
Titanium: Treksterkte: 240-900 MPa (verschilt per klasse), Vloeigrens: 170-880 MPa, Rek: 15%-30%
Koperlegeringen: Treksterkte: 200-500 MPa (afhankelijk van de legering), Vloeigrens: 100-300 MPa, Rek: 20%-35%
5. Warmtebehandeling (leveringsconditie)
Koolstof- en gelegeerd staal: Geleverd in gegloeide of genormaliseerde toestand. Warmtebehandelingen omvatten blussen en temperen om de sterkte en taaiheid te verbeteren.
Roestvrij staal: Wordt geleverd in gegloeide toestand om interne spanningen te verwijderen en de ductiliteit te verbeteren.
Nikkelgebaseerde legeringen: Oplossingsgegloeid om de mechanische eigenschappen en corrosiebestendigheid te optimaliseren.
Titanium en zirkonium: Meestal geleverd in gegloeide toestand om de ductiliteit en taaiheid te maximaliseren.
Koperlegeringen: Wordt geleverd in zachtgegloeide toestand, speciaal voor vormtoepassingen.
6. Vormen
Koolstof- en gelegeerd staal: Kan warm of koud vervormd worden, maar gelegeerde staalsoorten vereisen meer inspanning vanwege hun hogere sterkte.
Roestvrij staal: Koudvervormen komt veel voor, maar de verhardingssnelheid is hoger dan bij koolstofstaal.
Nikkelgebaseerde legeringen: Moeilijker te vormen vanwege de hoge sterkte en de verhardingssnelheid; vereist vaak warmbewerking.
Titanium: Vormen gaat het beste bij hoge temperaturen, omdat het materiaal bij kamertemperatuur een hoge sterkte heeft.
Koperlegeringen: Gemakkelijk te vormen dankzij goede ductiliteit.
7. Lassen
Koolstof- en gelegeerd staal: Over het algemeen eenvoudig te lassen met conventionele technieken, maar voorverwarmen en warmtebehandeling na het lassen (PWHT) kan vereist zijn.
Roestvrij staal: Gangbare lasmethoden zijn onder andere TIG, MIG en booglassen. Zorgvuldige controle van warmte-inbreng is noodzakelijk om sensibilisatie te voorkomen.
Nikkelgebaseerde legeringen: Moeilijk te lassen vanwege de hoge thermische uitzetting en gevoeligheid voor scheuren.
Titanium: Gelast in een afgeschermde omgeving (inert gas) om verontreiniging te voorkomen. Voorzorgsmaatregelen zijn nodig vanwege de reactiviteit van titanium bij hoge temperaturen.
Koperlegeringen: Gemakkelijk te lassen, vooral koper-nikkellegeringen, maar voorverwarmen kan nodig zijn om scheuren te voorkomen.
8. Corrosie van lassen
Roestvrij staal: Kan plaatselijke corrosie (bijv. putcorrosie, spleetcorrosie) veroorzaken in de warmtebeïnvloede zone van de las als dit niet goed onder controle wordt gehouden.
Nikkelgebaseerde legeringen: Gevoelig voor spanningscorrosie bij blootstelling aan chloriden bij hoge temperaturen.
Titanium: Lassen moeten goed worden afgeschermd tegen zuurstof om brosheid te voorkomen.
9. Ontkalken, beitsen en reinigen
Koolstof- en gelegeerd staal: Beitsen verwijdert oppervlakteoxiden na warmtebehandeling. Veelvoorkomende zuren zijn zoutzuur en zwavelzuur.
Roestvrij staal en nikkellegeringen: Beitsen met salpeterzuur/waterstoffluoridezuur wordt gebruikt om lasverkleuring te verwijderen en de corrosiebestendigheid te herstellen na het lassen.
Titanium: Licht zure beitsoplossingen worden gebruikt om het oppervlak te reinigen en oxiden te verwijderen zonder het metaal te beschadigen.
Koperlegeringen: Zuurreiniging wordt gebruikt om oppervlakteaanslag en oxiden te verwijderen.
10. Oppervlakteproces (AP, BA, MP, EP, enz.)
AP (gegloeid en gebeitst): Standaardafwerking voor de meeste roestvaste en nikkellegeringen na gloeien en beitsen.
BA (Glanzend gegloeid): Wordt bereikt door gloeien in een gecontroleerde atmosfeer, waardoor een glad, reflecterend oppervlak ontstaat.
MP (Mechanisch gepolijst): Mechanisch polijsten verbetert de gladheid van het oppervlak, waardoor het risico op verontreiniging en corrosievorming afneemt.
EP (elektrogepolijst): Een elektrochemisch proces waarbij oppervlaktemateriaal wordt verwijderd om een ultragladde afwerking te creëren. Hierdoor wordt de oppervlakteruwheid verminderd en de corrosiebestendigheid verbeterd.
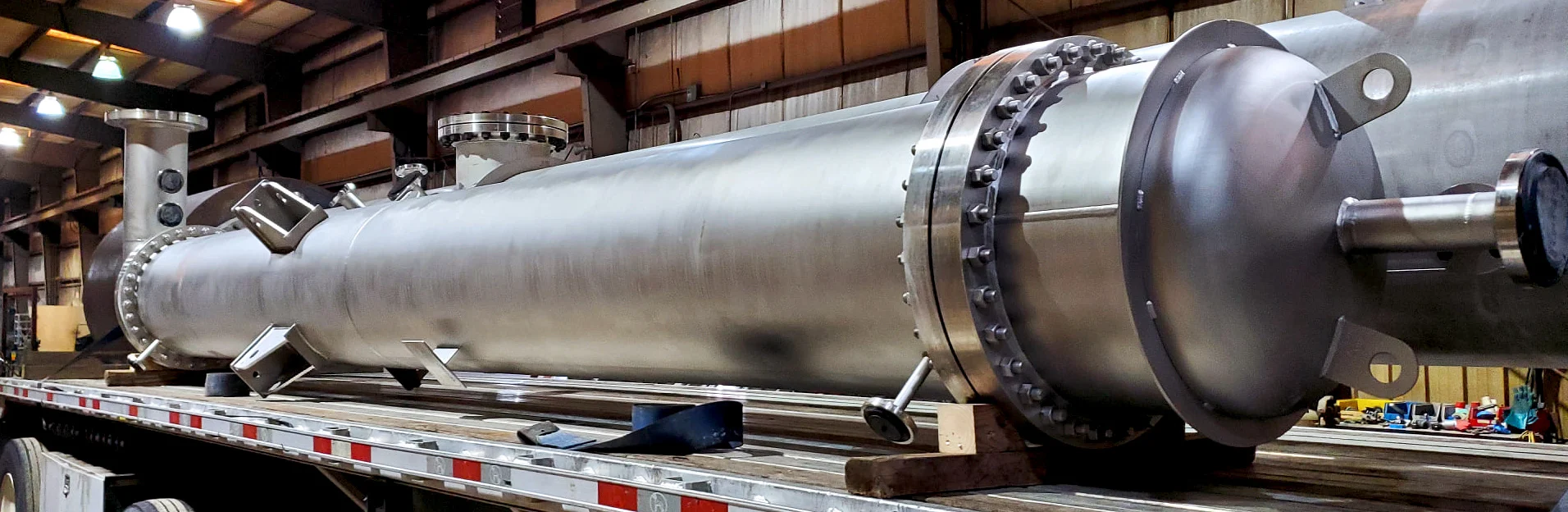
RVS warmtewisselaar
I. Naadloze buizen begrijpen
Naadloze buizen verschillen van gelaste buizen doordat ze geen gelaste naad hebben, wat een zwak punt kan zijn in sommige hogedruktoepassingen. Naadloze buizen worden in eerste instantie gevormd uit een massief blok, dat vervolgens wordt verhit en vervolgens wordt geëxtrudeerd of over een mandrel wordt getrokken om de buisvorm te creëren. De afwezigheid van naden geeft ze superieure sterkte en betrouwbaarheid, waardoor ze ideaal zijn voor omgevingen met hoge druk en hoge temperaturen.
Veel voorkomende toepassingen:
Ketels: Naadloze buizen zijn essentieel bij de constructie van waterpijp- en vlampijpketels, waar hoge temperaturen en druk heersen.
Warmtewisselaars: Naadloze buizen in warmtewisselaars worden gebruikt om warmte tussen twee vloeistoffen over te brengen. Ze moeten corrosiebestendig zijn en hun thermische efficiëntie behouden.
condensors: Naadloze buizen zorgen voor de condensatie van stoom tot water in energieopwekkings- en koelsystemen.
Oververhitters: Naadloze buizen worden gebruikt om stoom in boilers te oververhitten, waardoor de efficiëntie van turbines in energiecentrales wordt verbeterd.
Luchtvoorverwarmers: Deze buizen brengen de warmte van de rookgassen over naar de lucht, waardoor de efficiëntie van de ketel verbetert.
Economen: Naadloze buizen in economizers verwarmen het voedingswater voor met behulp van restwarmte uit de keteluitlaat, waardoor de thermische efficiëntie wordt verhoogd.
Ketels, warmtewisselaars, condensors, oververhitters, luchtvoorverwarmers en economizers zijn integrale componenten in verschillende industrieën, met name die welke betrokken zijn bij warmteoverdracht, energieproductie en vloeistofbeheer. Deze componenten worden met name primair gebruikt in de volgende industrieën:
1. Energieopwekkingsindustrie
Ketels: Worden in energiecentrales gebruikt om chemische energie om te zetten in thermische energie, vaak voor stoomopwekking.
Oververhitters, economizers en luchtvoorverwarmers: Deze componenten verbeteren de efficiëntie door de verbrandingslucht voor te verwarmen, warmte uit uitlaatgassen terug te winnen en de stoom verder te verwarmen.
Warmtewisselaars en condensoren: worden gebruikt voor koeling en warmteterugwinning in thermische energiecentrales, met name in stoomturbines en koelcycli.
2. Olie- en gasindustrie
Warmtewisselaars: Onmisbaar in raffinageprocessen, waarbij warmte wordt overgedragen tussen vloeistoffen, zoals bij de destillatie van ruwe olie of op offshoreplatforms voor gasverwerking.
Ketels en economizers: worden gebruikt in raffinaderijen en petrochemische fabrieken voor stoomopwekking en energieterugwinning.
Condensatoren: worden gebruikt om gassen tijdens de destillatieprocessen te condenseren tot vloeistoffen.
3. Chemische industrie
Warmtewisselaars: Worden veel gebruikt om chemische reacties te verwarmen of te koelen en om warmte terug te winnen uit exotherme reacties.
Ketels en oververhitters: worden gebruikt om de stoom te produceren die nodig is voor verschillende chemische processen en om energie te leveren voor destillatie- en reactiestappen.
Luchtvoorverwarmers en economizers: Verbeter de efficiëntie van energie-intensieve chemische processen door warmte terug te winnen uit uitlaatgassen en het brandstofverbruik te verlagen.
4. Maritieme industrie
Boilers en warmtewisselaars: Essentieel in zeeschepen voor stoomopwekking, verwarmings- en koelsystemen. Marine warmtewisselaars worden vaak gebruikt om de motoren van het schip te koelen en stroom op te wekken.
Condensatoren: Worden gebruikt om uitlaatstoom om te zetten in water, dat opnieuw gebruikt kan worden in de ketelsystemen van het schip.
5. Voedings- en drankenindustrie
Warmtewisselaars: Worden veel gebruikt voor pasteurisatie-, sterilisatie- en verdampingsprocessen.
Ketels en economizers: worden gebruikt om stoom te produceren voor voedselverwerkingsprocessen en om warmte terug te winnen uit de uitlaatgassen om brandstofverbruik te besparen.
6. HVAC (Verwarming, Ventilatie en Airconditioning)
Warmtewisselaars en luchtvoorverwarmers: worden gebruikt in HVAC-systemen voor efficiënte warmteoverdracht tussen vloeistoffen of gassen, en zorgen voor verwarming of koeling van gebouwen en industriële faciliteiten.
Condensatoren: worden in airconditioningsystemen gebruikt om warmte van het koelmiddel af te voeren.
7. Pulp- en papierindustrie
Ketels, warmtewisselaars en economizers: zorgen voor stoom- en warmteterugwinning in processen zoals pulpproductie, papierdroging en chemische terugwinning.
Oververhitters en luchtvoorverwarmers: Verbeter de energie-efficiëntie in de terugwinningsketels en de algehele warmtebalans van papierfabrieken.
8. Metaal- en staalindustrie
Warmtewisselaars: worden gebruikt voor het koelen van hete gassen en vloeistoffen in de staalproductie en in metallurgische processen.
Ketels en economizers: Leveren warmte voor verschillende processen, zoals hoogovens, warmtebehandeling en walsen.
9. Farmaceutische industrie
Warmtewisselaars: worden gebruikt voor het regelen van de temperatuur tijdens de productie van medicijnen, fermentatieprocessen en steriele omgevingen.
Boilers: genereren de stoom die nodig is voor het steriliseren en verwarmen van farmaceutische apparatuur.
10. Afvalenergiecentrales
Ketels, condensors en economizers: worden gebruikt om afval om te zetten in energie door verbranding, terwijl warmte wordt teruggewonnen om de efficiëntie te verbeteren.
Laten we nu eens dieper ingaan op de materialen die naadloze buizen geschikt maken voor deze veeleisende toepassingen.
II. Koolstofstalen buizen voor ketel en warmtewisselaar
Koolstofstaal is een van de meest gebruikte materialen voor naadloze buizen in industriële toepassingen, voornamelijk vanwege de uitstekende sterkte, maar ook vanwege de betaalbaarheid en brede beschikbaarheid. Koolstofstalen buizen bieden een gemiddelde temperatuur- en drukbestendigheid, waardoor ze geschikt zijn voor een breed scala aan toepassingen.
Eigenschappen van koolstofstaal:
Hoge sterkte: Buizen van koolstofstaal kunnen grote druk en spanning weerstaan, waardoor ze ideaal zijn voor gebruik in boilers en warmtewisselaars.
Kosteneffectief: Vergeleken met andere materialen is koolstofstaal relatief goedkoop, waardoor het een populaire keuze is voor grootschalige industriële toepassingen.
Matige corrosiebestendigheid: koolstofstaal is niet zo corrosiebestendig als roestvrij staal, maar het kan worden behandeld met coatings of voeringen om de levensduur in corrosieve omgevingen te verlengen.
Belangrijkste normen en klassen:
ASTM A179: Deze norm omvat naadloze koudgetrokken koolstofarme stalen buizen die worden gebruikt voor warmtewisselaar- en condensortoepassingen. Deze buizen hebben uitstekende warmteoverdrachtseigenschappen en worden vaak gebruikt in toepassingen met lage tot matige temperaturen en druk.
ASTM A192: Naadloze koolstofstalen boilerbuizen ontworpen voor hogedrukservice. Deze buizen worden gebruikt in stoomgeneratie en andere hogedrukomgevingen.
ASTM A210: Deze norm omvat naadloze buizen van gemiddeld koolstofstaal voor ketel- en oververhittertoepassingen. De A-1 en C-klassen bieden verschillende niveaus van sterkte en temperatuurbestendigheid.
ASTM A334 (Klassen 1, 3, 6): Naadloze en gelaste koolstofstalen buizen ontworpen voor lagetemperatuurservice. Deze klassen worden gebruikt in warmtewisselaars, condensors en andere lagetemperatuurtoepassingen.
EN 10216-2 (P235GH, P265GH TC1/TC2): Europese norm voor naadloze stalen buizen die worden gebruikt in druktoepassingen, met name in boilers en bij hoge temperaturen.
Koolstofstalen buizen zijn een uitstekende keuze voor ketel- en warmtewisselaartoepassingen waar hoge sterkte en matige corrosiebestendigheid vereist zijn. Voor toepassingen waarbij niet alleen extreem hoge temperaturen maar ook agressieve corrosieve omgevingen een rol spelen, worden echter vaak buizen van gelegeerd of roestvrij staal verkozen vanwege hun superieure bestendigheid en duurzaamheid.
III. Gelegeerde stalen buizen voor ketel en warmtewisselaar
Gelegeerde stalen buizen zijn ontworpen voor hoge-temperatuur en hoge-druk ketel- en warmtewisselaartoepassingen. Deze buizen zijn gelegeerd met elementen zoals chroom, molybdeen en vanadium om hun sterkte, hardheid en weerstand tegen corrosie en hitte te verbeteren. Gelegeerde stalen buizen worden veel gebruikt in kritische toepassingen, zoals oververhitters, economizers en hoge-temperatuur warmtewisselaars, vanwege hun uitzonderlijke sterkte en weerstand tegen hitte en druk.
Eigenschappen van gelegeerd staal:
Hoge hittebestendigheid: Legeringselementen zoals chroom en molybdeen verbeteren de prestaties van deze buizen bij hoge temperaturen, waardoor ze geschikt zijn voor toepassingen met extreme temperaturen.
Verbeterde corrosiebestendigheid: buizen van gelegeerd staal bieden een betere weerstand tegen oxidatie en corrosie vergeleken met koolstofstaal, met name in omgevingen met hoge temperaturen.
Verbeterde sterkte: Legeringselementen vergroten bovendien de sterkte van deze buizen, waardoor ze bestand zijn tegen de hoge druk in boilers en andere belangrijke apparatuur.
Belangrijkste normen en klassen:
ASTM A213 (Klassen T5, T9, T11, T22, T91, T92): Deze norm omvat naadloze ferritische en austenitische gelegeerde stalen buizen voor gebruik in boilers, oververhitters en warmtewisselaars. De klassen verschillen in hun legeringssamenstelling en worden geselecteerd op basis van de specifieke temperatuur- en drukvereisten.
T5 en T9: Geschikt voor gebruik bij matige tot hoge temperaturen.
T11 en T22: Worden vaak gebruikt bij toepassingen met hoge temperaturen en bieden een betere hittebestendigheid.
T91 en T92: Geavanceerde, zeer sterke legeringen, ontworpen voor gebruik bij extreem hoge temperaturen in energiecentrales.
EN 10216-2 (16Mo3, 13CrMo4-5, 10CrMo9-10, 15NiCuMoNb5-6-4, X20CrMoV11-1): Europese normen voor naadloze gelegeerde stalen buizen die worden gebruikt in toepassingen met hoge temperaturen. Deze buizen worden vaak gebruikt in boilers, oververhitters en economizers in energiecentrales.
16Mo3: Een gelegeerd staal met goede eigenschappen bij hoge temperaturen, geschikt voor gebruik in boilers en drukvaten.
13CrMo4-5 en 10CrMo9-10: Chroom-molybdeenlegeringen die uitstekende hitte- en corrosiebestendigheid bieden voor toepassingen bij hoge temperaturen.
Buizen van gelegeerd staal zijn de beste optie voor omgevingen met hoge temperaturen en hoge druk, waarbij koolstofstaal mogelijk niet voldoende prestaties levert voor de ketel en warmtewisselaar.
IV. Roestvrijstalen buizen voor ketel en warmtewisselaar
Roestvrijstalen buizen bieden uitzonderlijke corrosiebestendigheid, waardoor ze ideaal zijn voor ketel- en warmtewisselaartoepassingen met corrosieve vloeistoffen, hoge temperaturen en zware omstandigheden. Ze worden veel gebruikt in warmtewisselaars, oververhitters en boilers, waar naast corrosiebestendigheid ook sterkte bij hoge temperaturen vereist is voor optimale prestaties.
Eigenschappen van roestvrij staal:
Corrosiebestendigheid: De corrosiebestendigheid van roestvrij staal komt voort uit het chroomgehalte, dat een beschermende oxidelaag op het oppervlak vormt.
Hoge sterkte bij hoge temperaturen: roestvast staal behoudt zijn mechanische eigenschappen, zelfs bij hoge temperaturen, waardoor het geschikt is voor oververhitters en andere hitte-intensieve toepassingen.
Duurzaamheid op lange termijn: De corrosie- en oxidatiebestendigheid van roestvrij staal zorgt voor een lange levensduur, zelfs in zware omstandigheden.
Belangrijkste normen en klassen:
ASTM A213 / ASTM A249: Deze normen omvatten naadloze en gelaste roestvrijstalen buizen voor gebruik in boilers, oververhitters en warmtewisselaars. Veelvoorkomende kwaliteiten zijn:
TP304 / TP304L (EN 1.4301 / 1.4307): Austenitische roestvaste staalsoorten worden veel gebruikt vanwege hun corrosiebestendigheid en sterkte.
TP310S / TP310MoLN (EN 1.4845 / 1.4466): Hittebestendige roestvaste staalsoorten met uitstekende oxidatiebestendigheid.
TP316 / TP316L (EN 1.4401 / 1.4404): Molybdeenhoudende kwaliteiten met een verbeterde corrosiebestendigheid, met name in chlorideomgevingen.
TP321 (EN 1.4541): Gestabiliseerde roestvaste staalsoort die in omgevingen met hoge temperaturen wordt gebruikt om interkristallijne corrosie te voorkomen.
TP347H / TP347HFG (EN 1.4550 / 1.4961): Gestabiliseerde typen met een hoog koolstofgehalte voor toepassingen bij hoge temperaturen, zoals oververhitters en boilers.
UNS N08904 (904L) (EN 1.4539): Superaustenitisch roestvast staal met uitstekende corrosiebestendigheid, vooral in zure omgevingen.
ASTM A269: Omvat naadloze en gelaste austenitische roestvrijstalen buizen voor algemene corrosiebestendige toepassingen.
ASTM A789: Standaard voor duplex roestvaststalen buizen, die een combinatie bieden van uitstekende corrosiebestendigheid en hoge sterkte.
UNS S31803, S32205, S32750, S32760: Duplex en super duplex roestvast staalsoorten die een superieure corrosiebestendigheid bieden, vooral in omgevingen met veel chloriden.
EN 10216-5: Europese norm voor naadloze buizen van roestvrij staal, waaronder de volgende kwaliteiten:
1.4301 / 1.4307 (TP304 / TP304L)
1.4401 / 1.4404 (TP316 / TP316L)
1.4845 (TP310S)
1,4466 (TP310MoLN)
1.4539 (UNS-N08904 / 904L)
Buizen van roestvast staal zijn zeer veelzijdig en worden gebruikt in een breed scala aan toepassingen, waaronder warmtewisselaars, boilers en oververhitters, waarbij zowel corrosiebestendigheid als sterkte bij hoge temperaturen niet alleen vereist zijn, maar ook essentieel zijn voor optimale prestaties.
V. Nikkelgebaseerde legeringen voor ketels en warmtewisselaars
Nikkelgebaseerde legeringen behoren tot de meest corrosiebestendige materialen die beschikbaar zijn en worden vaak gebruikt in boiler- en warmtewisselaartoepassingen met extreme temperaturen, corrosieve omgevingen en hoge drukomstandigheden. Nikkellegeringen bieden uitstekende weerstand tegen oxidatie, sulfidering en carburatie, waardoor ze ideaal zijn voor warmtewisselaars, boilers en oververhitters in zware omgevingen.
Eigenschappen van nikkelgebaseerde legeringen:
Uitzonderlijke corrosiebestendigheid: Nikkel-legeringen zijn bestand tegen corrosie in zure, alkalische en chloride-omgevingen.
Stabiliteit bij hoge temperaturen: Nikkellegeringen behouden hun sterkte en corrosiebestendigheid, zelfs bij hoge temperaturen. Hierdoor zijn ze geschikt voor toepassingen bij hoge temperaturen.
Oxidatie- en sulfidatiebestendigheid: Nikkellegeringen zijn bestand tegen oxidatie en sulfidatie, die kunnen optreden in omgevingen met hoge temperaturen en zwavelhoudende verbindingen.
Belangrijkste normen en klassen:
ASTM B163 / ASTM B407 / ASTM B444: Deze normen omvatten legeringen op nikkelbasis voor naadloze buizen die worden gebruikt in boilers, warmtewisselaars en oververhitters. Veelvoorkomende kwaliteiten zijn:
Inconel 600 / 601: Uitstekende weerstand tegen oxidatie en corrosie bij hoge temperaturen, waardoor deze legeringen ideaal zijn voor oververhitters en warmtewisselaars met hoge temperaturen.
Inconel 625: Biedt superieure weerstand tegen een breed scala aan corrosieve omgevingen, waaronder zure en chloriderijke omgevingen.
Incoloy 800 / 800H / 800HT: Wordt gebruikt bij toepassingen met hoge temperaturen vanwege de uitstekende weerstand tegen oxidatie en carburatie.
Hastelloy C276 / C22: Deze nikkel-molybdeen-chroomlegeringen staan bekend om hun uitstekende corrosiebestendigheid in zeer corrosieve omgevingen, waaronder zure en chloridehoudende media.
ASTM B423: Omvat naadloze buizen gemaakt van nikkel-ijzer-chroom-molybdeenlegeringen zoals legering 825, die een uitstekende weerstand biedt tegen spanningscorrosie en algemene corrosie in verschillende omgevingen.
EN 10216-5: Europese norm voor legeringen op nikkelbasis die worden gebruikt in naadloze buizen voor toepassingen bij hoge temperaturen en corrosie, waaronder kwaliteiten zoals:
2.4816 (Inconel 600)
2.4851 (Inconel 601)
2.4856 (Inconel 625)
2.4858 (Legering 825)
Nikkelgebaseerde legeringen worden vaak gekozen voor kritische toepassingen waarbij corrosiebestendigheid en prestaties bij hoge temperaturen essentieel zijn, zoals in energiecentrales, chemische verwerking en olie- en gasraffinaderijen (ketels en warmtewisselaars).
VI. Titanium- en zirkoniumlegeringen voor ketels en warmtewisselaars
Titanium- en zirkoniumlegeringen bieden een unieke combinatie van sterkte, corrosiebestendigheid en lichtgewicht eigenschappen, waardoor ze ideaal zijn voor specifieke toepassingen in warmtewisselaars, condensors en boilers.
Eigenschappen van titaniumlegeringen:
Hoge sterkte-gewichtsverhouding: Titanium is net zo sterk als staal, maar aanzienlijk lichter. Hierdoor is het geschikt voor toepassingen waarbij het gewicht belangrijk is.
Uitstekende corrosiebestendigheid: titaniumlegeringen zijn zeer goed bestand tegen corrosie in zeewater, zure omgevingen en chloridehoudende media.
Goede hittebestendigheid: Titaniumlegeringen behouden hun mechanische eigenschappen bij hoge temperaturen, waardoor ze geschikt zijn voor warmtewisselaarbuizen in energiecentrales en chemische verwerking.
Eigenschappen van zirkoniumlegeringen:
Uitstekende corrosiebestendigheid: Zirkoniumlegeringen zijn zeer goed bestand tegen corrosie in zure omgevingen, zoals zwavelzuur, salpeterzuur en zoutzuur.
Stabiliteit bij hoge temperaturen: Zirkoniumlegeringen behouden hun sterkte en corrosiebestendigheid bij hoge temperaturen, waardoor ze ideaal zijn voor toepassingen in warmtewisselaars met hoge temperaturen.
Belangrijkste normen en klassen:
ASTM B338: Deze norm omvat naadloze en gelaste titaniumlegeringbuizen voor gebruik in warmtewisselaars en condensors. Veelvoorkomende kwaliteiten zijn:
Graad 1 / Graad 2: Commerciële zuivere titaniumsoorten met uitstekende corrosiebestendigheid.
Graad 5 (Ti-6Al-4V): Een titaniumlegering met verbeterde sterkte en hoge temperatuurbestendigheid.
ASTM B523: Omvat naadloze en gelaste buizen van zirkoniumlegering voor gebruik in warmtewisselaars en condensors. Veelvoorkomende kwaliteiten zijn:
Zirkonium 702: Een commercieel zuivere zirkoniumlegering met uitstekende corrosiebestendigheid.
Zirkonium 705: Een gelegeerde zirkoniumsoort met verbeterde mechanische eigenschappen en hoge temperatuurstabiliteit.
Titanium- en zirkoniumlegeringen worden vaak gebruikt in zeer corrosieve omgevingen, zoals ontziltingsinstallaties voor zeewater, chemische verwerkingsindustrieën en kerncentrales (ketels en warmtewisselaars), vanwege hun superieure corrosiebestendigheid en lichte gewicht.
VII. Koper en koperlegeringen voor ketel en warmtewisselaar
Koper en koperlegeringen, zoals messing, brons en koper-nikkel, worden veel gebruikt in warmtewisselaars, condensors en boilers vanwege hun uitstekende thermische geleidbaarheid en corrosiebestendigheid.
Eigenschappen van koperlegeringen:
Uitstekende thermische geleidbaarheid: Koperlegeringen staan bekend om hun hoge thermische geleidbaarheid, waardoor ze ideaal zijn voor warmtewisselaars en condensatoren.
Corrosiebestendigheid: Koperlegeringen zijn bestand tegen corrosie in water, inclusief zeewater, waardoor ze geschikt zijn voor toepassingen in de zeevaart en bij ontzilting.
Antimicrobiële eigenschappen: Koperlegeringen hebben natuurlijke antimicrobiële eigenschappen, waardoor ze geschikt zijn voor toepassingen in de gezondheidszorg en waterzuivering.
Belangrijkste normen en klassen:
ASTM B111: Deze norm omvat naadloze koperen en koperlegeringsbuizen voor gebruik in warmtewisselaars, condensors en verdampers. Veelvoorkomende kwaliteiten zijn:
C44300 (Admiralty Brass): Een koper-zinklegering met een goede corrosiebestendigheid, vooral bij toepassingen in zeewater.
C70600 (koper-nikkel 90/10): Een koper-nikkellegering met uitstekende corrosiebestendigheid in zeewater en maritieme omgevingen.
C71500 (koper-nikkel 70/30): Een andere koper-nikkellegering met een hoger nikkelgehalte voor een betere corrosiebestendigheid.
Koper en koperlegeringen worden veel gebruikt in maritieme ketel- en warmtewisselaartoepassingen, energiecentrales en HVAC-systemen vanwege hun uitstekende thermische geleidbaarheid en weerstand tegen zeewatercorrosie.
Naast de ketel en warmtewisselaar zijn condensors, oververhitters, luchtvoorverwarmers en economizers ook essentiële componenten die de energie-efficiëntie aanzienlijk optimaliseren. De condensor koelt bijvoorbeeld de uitlaatgassen van zowel de ketel als de warmtewisselaar, terwijl de oververhitter daarentegen de stoomtemperatuur verhoogt voor betere prestaties. Ondertussen gebruikt de luchtvoorverwarmer uitlaatgassen om de inkomende lucht te verwarmen, waardoor de algehele efficiëntie van het ketel- en warmtewisselaarsysteem verder wordt verbeterd. Tot slot spelen economizers een cruciale rol door restwarmte uit rookgassen terug te winnen om water voor te verwarmen, wat uiteindelijk het energieverbruik vermindert en de efficiëntie van zowel de ketel als de warmtewisselaar verhoogt.
VIII. Conclusie: De juiste materialen kiezen voor de ketel en warmtewisselaar
Naadloze buizen zijn integraal voor de prestaties van boilers, warmtewisselaars, condensors, oververhitters, luchtvoorverwarmers en economizers in industrieën zoals energieopwekking, olie en gas en chemische verwerking. De keuze van het materiaal voor naadloze buizen hangt af van de specifieke toepassingsvereisten, waaronder temperatuur, druk, corrosiebestendigheid en mechanische sterkte.
Koolstofstaal biedt betaalbaarheid en sterkte voor toepassingen met gemiddelde temperaturen en druk.
Gelegeerd staal Biedt superieure prestaties bij hoge temperaturen en sterkte in boilers en oververhitters.
Roestvrij staal Biedt uitstekende corrosiebestendigheid en duurzaamheid in warmtewisselaars en oververhitters.
Nikkel-gebaseerde legeringen zijn de beste keuze voor extreem corrosieve omgevingen met hoge temperaturen.
Titanium- en zirkoniumlegeringen zijn ideaal voor lichte en zeer corrosieve toepassingen.
Koper en koperlegeringen worden vanwege hun thermische geleidbaarheid en corrosiebestendigheid geprefereerd in warmtewisselaars en condensoren.
Ketel- en warmtewisselaarsystemen spelen een cruciale rol in verschillende industrieën door warmte efficiënt van het ene medium naar het andere over te brengen. Een ketel en warmtewisselaar werken samen om warmte te genereren en over te brengen, en leveren essentiële warmte voor stoomproductie in energiecentrales en productieprocessen.
Door de eigenschappen en toepassingen van deze materialen te begrijpen, kunnen ingenieurs en ontwerpers weloverwogen beslissingen nemen en de veilige en efficiënte werking van hun apparatuur garanderen. Bij het selecteren van materialen voor de boiler en warmtewisselaar is het cruciaal om rekening te houden met de specifieke vereisten van uw toepassing. Daarnaast moet u de relevante normen raadplegen om compatibiliteit en optimale prestaties te garanderen.