Denizaltı Boru Hattı: Derinlemesine Bir Keşif
giriiş
Denizaltı boru hatları, petrol, gaz ve diğer sıvıları geniş su altı mesafelerinde taşır. Bu boru hatları, açık deniz petrol ve gaz platformlarını kara tesislerine bağlamak için olmazsa olmazdır ve kaynakların uzak yerlerden küresel pazara verimli ve güvenli bir şekilde aktarılmasını sağlar. Ancak, denizaltı boru hatlarının tasarlanması, inşa edilmesi ve bakımı, zorlu ve dinamik deniz ortamı nedeniyle benzersiz zorluklar sunar. Bu blog, uygulamaları, tasarım hususları, malzemeleri, kurulum yöntemleri ve bakım stratejileri dahil olmak üzere denizaltı boru hatlarına ilişkin kapsamlı bir genel bakış sunar.
1. Enerji Endüstrisinde Denizaltı Boru Hattının Rolü
1.1 Denizaltı Boru Hatlarının Önemi
Denizaltı boru hatları, açık deniz petrol ve gaz endüstrisinin can damarlarıdır. Hidrokarbonları açık deniz sahalarından karadaki rafinerilere ve işleme tesislerine taşımak için doğrudan ve güvenli bir rota sağlarlar. Bu boru hatları, özellikle petrol ve gaza olan talep arttıkça, küresel enerji tedarik zinciri için olmazsa olmazdır.
1.2 Temel Uygulamalar
Petrol ve Gaz Taşımacılığı: Denizaltı boru hatları, öncelikle ham petrol, doğal gaz ve kondensatların açık deniz üretim platformlarından işlenmek ve dağıtılmak üzere kara tesislerine taşınmasında kullanılır.
Su Enjeksiyon Hatları: Gelişmiş petrol çıkarma (EOR) operasyonlarında, basıncı korumak ve petrol çıkarma oranlarını iyileştirmek için denizaltı boru hatları rezervuara su enjekte eder.
Denizaltı Göbek Bağları: Bu özel boru hatları, deniz altı ekipmanları ile üstteki tesisler arasında kontrol sıvıları, elektrik gücü ve iletişim sinyalleri taşır.
2. Denizaltı Boru Hattı İçin Tasarım Hususları
2.1 Çevresel ve Jeoteknik Faktörler
Deniz Çevresi: Denizaltı boru hatları, deniz suyunun aşındırıcı etkilerine, güçlü akıntılara ve deniz araçlarından veya nesnelerden gelebilecek olası etkilere dayanacak şekilde tasarlanmalıdır. Deniz tabanındaki sıcaklık ve basınç koşulları da malzeme seçimini ve boru hattı tasarımını etkiler.
Deniz Tabanı Topografyası: Eğimler, vadiler ve hendekler dahil olmak üzere deniz tabanının topografyası, boru hattı güzergahını ve stabilitesini etkiler. Jeoteknik araştırmalar, deniz tabanı koşullarını değerlendirmek ve en iyi boru hattı güzergahını belirlemek için önemlidir.
Sismik Aktivite: Deprem riski taşıyan bölgelerde, denizaltı boru hatlarının deprem sırasında oluşacak yer hareketlerine uyum sağlayacak ve hasarı önleyecek şekilde tasarlanması gerekmektedir.
2.2 Boru Hattı Bütünlüğü ve Güvenliği
Malzeme seçimi: Denizaltı boru hatları genellikle yüksek mukavemetli karbon çelikten inşa edilir ve korozyona ve mekanik hasara karşı koruma sağlamak için füzyonla bağlanmış epoksi (FBE) veya üç katmanlı polietilen (3LPE) gibi korozyon önleyici malzemelerle kaplanır.
Boru Hattı Stabilitesi: Stabilite, özellikle güçlü akıntıların veya engebeli deniz tabanı arazisinin olduğu bölgelerde kritik bir endişe kaynağıdır. Kazma, gömme veya beton ağırlık kaplamaları ekleme gibi teknikler boru hattını stabilize eder.
Sızıntı Tespit Sistemleri: Denizaltı boru hatları, sızıntıları veya anormallikleri tespit etmek için basıncı, akış hızlarını ve diğer parametreleri gerçek zamanlı olarak izleyen gelişmiş sızıntı tespit sistemleriyle donatılmıştır.
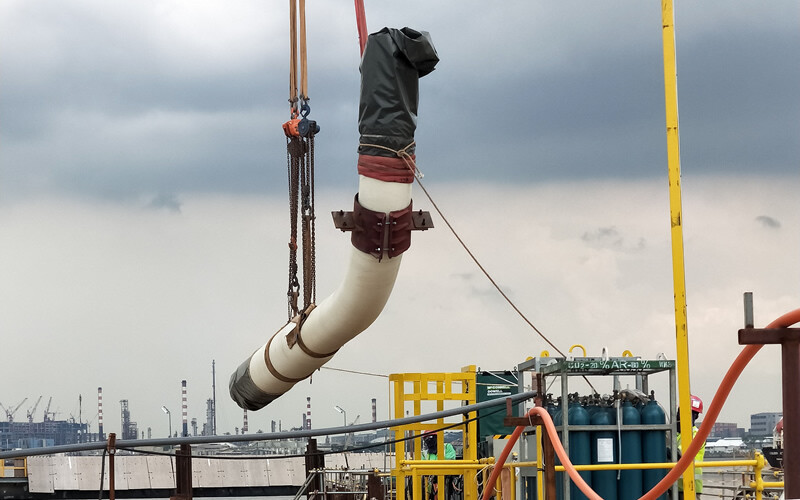
Denizaltı veya Denizaltı Boru Hattı
3. Denizaltı Boru Hattı Yapımında Kullanılan Malzemeler
3.1 Karbon Çelik
Karbon çeliği, mukavemeti, dayanıklılığı ve maliyet etkinliği nedeniyle denizaltı boru hatları için en yaygın malzemedir. Genellikle sert deniz ortamına karşı koruma sağlamak için korozyon önleyici katmanlarla kaplanır.
3.2 Korozyona Dayanıklı Alaşımlar (CRA'lar)
Boru hatlarının ekşi gaz veya deniz suyu gibi son derece aşındırıcı sıvılara maruz kaldığı alanlarda paslanmaz çelik, dubleks paslanmaz çelik veya Inconel gibi korozyona dayanıklı alaşımlar kullanılır. Bu malzemeler korozyona karşı mükemmel direnç ve yüksek mekanik mukavemet sunar.
3.3 Kaplama Sistemleri
Füzyonla Bağlı Epoksi (FBE): FBE kaplamalar mükemmel korozyon koruması sağlar ve genellikle deniz altı boru hatlarında kullanılır.
Üç Katmanlı Polietilen (3LPE): 3LPE kaplamalar, epoksi astar, polimer yapıştırıcı ve polietilen son kattan oluşur ve üstün mekanik koruma ve korozyon direnci sunar.
Beton Ağırlık Kaplaması: Beton ağırlık kaplamaları, özellikle güçlü akıntıların olduğu bölgelerde veya boru hattının deniz tabanına döşendiği yerlerde, boru hattının sağlamlığını sağlamak ve boru hattını dışarıdan gelebilecek hasarlardan korumak için sıklıkla uygulanır.
4. Kurulum Yöntemleri
4.1 S-Döşeme Yöntemi
S-döşeme yöntemi, denizaltı boru hatları döşemek için en yaygın tekniklerden biridir. Boru hattı bir döşeme mavnasına kaynaklanır ve S şeklinde bir eğriyle kademeli olarak deniz tabanına indirilir. Bu yöntem sığ ila orta su derinlikleri için uygundur.
4.2 J-Lay Yöntemi
J-döşeme yönteminde, boru hattı dikey olarak suya indirilir ve yatay olarak deniz tabanına döşenir. Bu teknik, döşeme işlemi sırasında boru hattındaki stresi azalttığı için derin su tesisatları için idealdir.
4.3 Makaralı Yatırma Yöntemi
Makaralı döşeme yöntemi, boru hattının büyük bir makaraya sarılmasını ve ardından kurulum sırasında açılmasını içerir. Bu hızlı ve etkili yöntem, onu kısa boru hatları veya uzak yerlerdeki kurulumlar için uygun hale getirir.
4.4 Kazı ve Gömme
Yüksek çevresel riske sahip alanlarda veya deniz tabanı stabilitesinin endişe verici olduğu yerlerde, boru hattı dış kuvvetlere karşı ek koruma sağlamak için bir hendeğe gömülür. Hendek açma, pulluklar, püskürtme araçları veya mekanik hendek kazıcılar kullanılarak gerçekleştirilebilir.
5. Bakım ve Bütünlük Yönetimi
5.1 Muayene Teknikleri
Hat İçi Muayene (ILI): Genellikle "akıllı domuzlar" olarak bilinen ILI araçları, denizaltı boru hatlarının iç durumunu incelemek için kullanılır. Bu araçlar, boru hattı bütünlüğünü tehlikeye atabilecek korozyonu, çatlakları ve diğer anormallikleri tespit edebilir.
ROV ve AUV Muayeneleri: Uzaktan kumandalı araçlar (ROV'lar) ve otonom su altı araçları (AUV'lar), denizaltı boru hatlarının dış koşullarını denetler. Bu araçlar, boru hattının durumunu izlemek ve olası sorunları belirlemek için kameralara ve sensörlere sahiptir.
5.2 Korozyon İzleme
Katodik koruma: Katodik koruma sistemleri, denizaltı boru hatlarının dış yüzeyinde korozyonu önler. Bu sistemler, boru hattını aşındırıcı deniz suyundan korumak için kurban anotları veya uygulanan akımlar kullanır.
Korozyon Önleyiciler: Bazı durumlarda, iç yüzeyleri aşındırıcı sıvılardan korumak için boru hattına korozyon inhibitörleri enjekte edilir.
5.3 Sızıntı Tespiti ve Acil Durum Müdahalesi
Gerçek Zamanlı İzleme: Denizaltı boru hatlarında sızıntıları, basınç düşüşlerini ve diğer anormallikleri tespit eden gerçek zamanlı izleme sistemleri bulunur. Erken tespit, çevresel hasarı önlemek ve boru hattının güvenliğini sağlamak için kritik öneme sahiptir.
Acil Durum Müdahale Planları: Denizaltı boru hatlarındaki olası sızıntıları veya kopmaları ele almak için kapsamlı acil durum müdahale planları mevcuttur. Bu planlar, boru hattını kapatma, sızıntıyı sınırlama ve çevresel etkiyi azaltma prosedürlerini içerir.
6. Sonuç: Denizaltı Boru Hattının Geleceği
Enerji talebi artmaya devam ederken, küresel enerji tedarik zincirinde denizaltı boru hatlarının önemi abartılamaz. Malzemelerdeki, kurulum tekniklerindeki ve bütünlük yönetimindeki gelişmeler, bu kritik altyapıların güvenilirliğini ve emniyetini artırıyor. Ancak, korozyon, çevresel etki ve daha derin su kurulumları gibi devam eden zorluklar sürekli yenilik ve iyileştirme gerektiriyor.
Denizaltı boru hatlarının karmaşıklığını anlayarak ve tasarım, inşaat ve bakımda en iyi uygulamaları benimseyerek, sektör kaynakların açık deniz sahalarından dünya çapındaki pazarlara güvenli ve verimli bir şekilde taşınmasını sağlayabilir.
7. SSS
S1: Denizaltı boru hattı inşasında karşılaşılan başlıca zorluklar nelerdir?
Başlıca zorluklar arasında korozyon, güçlü akıntılar, deniz tabanının stabilitesi gibi çevresel faktörler ve malzeme seçimi, montaj yöntemleri ve zaman içinde boru hattı bütünlüğünün korunmasıyla ilgili teknik zorluklar yer alıyor.
S2: Denizaltı boru hatları korozyondan nasıl korunur?
Denizaltı boru hatları, FBE ve 3LPE gibi korozyon önleyici kaplamalar, katodik koruma sistemleri ve yüksek korozif ortamlarda korozyona dayanıklı malzemeler kullanılarak korozyondan korunmaktadır.
S3: Denizaltı boru hatlarında gerçek zamanlı izlemenin önemi nedir?
Gerçek zamanlı izleme, boru hattı bütünlüğünü tehlikeye atabilecek sızıntıları, basınç düşüşlerini ve diğer anormallikleri tespit etmek için çok önemlidir. Erken tespit, hızlı yanıt ve azaltma sağlayarak çevresel hasarı önler ve boru hattı güvenliğini sağlar.