giriiş
Çelik borular, petrol ve gazda kritik öneme sahiptir ve aşırı koşullar altında eşsiz dayanıklılık ve güvenilirlik sunar. Keşif ve taşımacılık için olmazsa olmaz olan bu borular, yüksek basınçlara, aşındırıcı ortamlara ve sert sıcaklıklara dayanır. Bu sayfa, petrol ve gaz keşfinde çelik boruların kritik işlevlerini ele alarak, sondaj, altyapı ve güvenlikteki önemlerini ayrıntılı olarak açıklamaktadır. Uygun çelik boruların seçilmesinin, bu zorlu sektörde operasyonel verimliliği nasıl artırabileceğini ve maliyetleri nasıl azaltabileceğini keşfedin.
I. Petrol ve Gaz Endüstrisi için Çelik Boruların Temel Bilgileri
1. Terminoloji Açıklaması
API'si: Kısaltması Amerikan Petrol Enstitüsü.
OCTG: Kısaltması Petrol Ülkesi Borulu ÜrünlerYağ Muhafaza Borusu, Yağ Borusu, Sondaj Borusu, Matkap Yakası, Matkap Uçları, Sucker Rod, Pup eklemleri vb. dahil.
Yağ Borusu: Borulama, petrol kuyularında çıkarma, gaz çıkarma, su enjeksiyonu ve asit kırma amacıyla kullanılır.
Gövde: Duvar çökmesini önlemek amacıyla, sondaj kuyusuna yer yüzeyinden astar olarak indirilen borular.
Matkap Borusu: Sondaj kuyularının açılmasında kullanılan boru.
Hat borusu: Petrol veya gaz taşımak için kullanılan boru.
Kaplinler: İki dişli boruyu iç dişlilerle bağlamak için kullanılan silindirler.
Kaplin Malzemesi: Kaplin imalatında kullanılan boru.
API Konuları: API 5B standardı tarafından belirtilen boru dişleri, petrol borusu yuvarlak dişleri, muhafaza borusu kısa yuvarlak dişleri, muhafaza borusu uzun yuvarlak dişleri, muhafaza borusu kısmi trapez dişleri, hat borusu dişleri vb. dahil.
Premium Bağlantı: Benzersiz sızdırmazlık özellikleri, bağlantı özellikleri ve diğer özelliklere sahip API olmayan iş parçacıkları.
Başarısızlıklar: Belirli servis koşulları altında deformasyon, kırılma, yüzey hasarı ve orijinal fonksiyon kaybı.
Başarısızlığın Birincil Biçimleri: ezilme, kayma, kopma, sızıntı, korozyon, yapışma, aşınma vb.
2. Petrolle İlgili Standartlar
API Spec 5B, 17. Baskı – Muhafaza, Boru ve Hat Borusu Dişlerinin Diş Açma, Ölçme ve Diş Muayenesine İlişkin Şartname
API Spec 5L, 46. Baskı – Hat Borusu Şartnamesi
API Spec 5CT, 11. Baskı – Muhafaza ve Boru Şartnamesi
API Spec 5DP, 7. Baskı – Sondaj Borusu Şartnamesi
API Spec 7-1, 2. Baskı – Döner Matkap Kök Elemanlarının Özellikleri
API Spec 7-2, 2. Baskı – Döner Omuzlu Diş Bağlantılarının Diş Açılması ve Ölçülmesi Şartnamesi
API Spec 11B, 24. Baskı – Sucker Çubuklar, Cilalı Çubuklar ve Gömlekler, Kaplinler, Platin Çubuklar, Cilalı Çubuk Kelepçeleri, Salmastra Kutuları ve Pompa T Parçaları için Teknik Özellikler
ISO 3183:2019 – Petrol ve Doğal Gaz Endüstrileri — Boru Hattı Taşıma Sistemleri için Çelik Boru
ISO 11960:2020 – Petrol ve Doğal Gaz Endüstrileri – Kuyularda Muhafaza veya Boru Olarak Kullanılan Çelik Borular
NACE MR0175 / ISO 15156:2020 – Petrol ve Doğal Gaz Endüstrileri – Petrol ve Gaz Üretiminde H2S İçeren Ortamlarda Kullanıma Yönelik Malzemeler
II. Yağ Boruları
1. Yağ Borularının Sınıflandırılması
Yağ Boruları, Sıkıştırılmamış Yağ Boruları (NU), Harici Sıkıştırılmış Yağ Boruları (EU) ve Entegre Bağlantılı (IJ) Yağ Boruları olarak ayrılır. NU yağ boruları, borunun ucunun ortalama kalınlıkta olduğu, doğrudan dişleri döndürdüğü ve kaplinleri getirdiği anlamına gelir. Sıkıştırılmış borular, her iki borunun uçlarının harici olarak Sıkıştırıldığı, ardından diş açıldığı ve birleştirildiği anlamına gelir. Entegre Bağlantılı borular, borunun bir ucunun harici dişlerle Sıkıştırıldığı ve diğerinin kaplinler olmadan doğrudan bağlanmış dahili dişlerle Sıkıştırıldığı anlamına gelir.
2. Yağ Borusunun İşlevi
① Petrol ve gazın çıkarılması: Petrol ve gaz kuyuları açıldıktan ve çimentolandıktan sonra, petrol ve gazı yere çıkarmak için borular petrol mahfazasına yerleştirilir.
② Su enjeksiyonu: kuyu içi basınç yetersiz olduğunda, boru aracılığıyla kuyuya su enjekte edin.
③ Buhar enjeksiyonu: Kalın yağ sıcak geri kazanımında, buhar, yalıtımlı yağ boruları ile kuyuya verilir.
④ Asitleştirme ve kırılma: Kuyu delme işleminin son aşamasında veya petrol ve gaz kuyularının üretimini iyileştirmek için, petrol ve gaz tabakasına asitleştirme ve kırılma ortamı veya kürleme malzemesi girmek gerekir ve ortam ve kürleme malzemesi petrol boruları aracılığıyla taşınır.
3. Yağ Borusunun Çelik Sınıfı
Yağ borularının çelik kaliteleri H40, J55, N80, L80, C90, T95, P110'dur.
N80, N80-1 ve N80Q olarak ikiye ayrılır, ikisi de aynı çekme özelliklerine sahiptir; iki fark ise teslimat durumu ve darbe performansı farklılıklarıdır, N80-1 normalize edilmiş halde veya son haddeleme sıcaklığı kritik sıcaklık Ar3'ten büyük olduğunda teslimat yapar ve hava soğutmasından sonra gerilim azaltımı yapar ve normalize edilmiş yerine sıcak haddeleme bulmak için kullanılabilir, darbe ve tahribatsız muayene gerekli değildir; N80Q temperlenmiş (söndürülmüş ve temperlenmiş) olmalıdır Isıl işlem, darbe fonksiyonu API 5CT hükümlerine uygun olmalı ve tahribatsız muayene yapılmalıdır.
L80, L80-1, L80-9Cr ve L80-13Cr olarak ayrılır. Mekanik özellikleri ve teslimat durumları aynıdır. Kullanım, üretim zorluğu ve fiyat farklılıkları: L80-1 genel tip içindir, L80-9Cr ve L80-13Cr yüksek korozyon dirençli borulardır, üretim zorluğu vardır ve pahalıdır ve genellikle ağır korozyon kuyularında kullanılır.
C90 ve T95, C90-1, C90-2 ve T95-1, T95-2 olmak üzere 1 ve 2 tipe ayrılır.
4. Yaygın Olarak Kullanılan Yağ Boruları Çelik Sınıfı, Çelik Adı ve Teslimat Durumu
J55 (37Mn5) NU Yağ Borusu: Normalleştirilmiş yerine sıcak haddelenmiş
J55 (37Mn5) AB Yağ Borusu: Tam uzunlukta, üzüldükten sonra normalize edildi
N80-1 (36Mn2V) NU Yağ Borusu: Normalleştirilmiş yerine sıcak haddelenmiş
N80-1 (36Mn2V) AB Yağ Borusu: Tam uzunlukta, üzüldükten sonra normalize edildi
N80-Q (30Mn5) Yağ Borusu: 30Mn5, Tam Boy Temperleme
L80-1 (30Mn5) Yağ Borusu: 30Mn5, Tam Boy Temperleme
P110 (25CrMnMo) Yağ Borusu: 25CrMnMo, Tam Boy Temperleme
J55 (37Mn5) Kaplin: Sıcak haddelenmiş çevrimiçi Normalleştirilmiş
N80 (28MnTiB) Kaplin: Tam Boy Temperleme
L80-1 (28MnTiB) Kaplin: Tam Boy Temperli
P110 (25CrMnMo) Kaplin: Tam Boy Temperleme
III. Muhafaza Borusu
1. Muhafazanın Sınıflandırılması ve Rolü
Muhafaza, petrol ve gaz kuyularının duvarını destekleyen çelik borudur. Her kuyuda farklı sondaj derinlikleri ve jeolojik koşullara göre birkaç kat muhafaza kullanılmaktadır. Çimento, kuyuya indirildikten sonra mahfazayı çimentolamak için kullanılır ve petrol borusu ve sondaj borusundan farklı olarak tekrar kullanılamaz ve tek kullanımlık sarf malzemelerine aittir. Bu nedenle, muhafaza tüketimi tüm petrol kuyusu borularının yüzde 70'inden fazlasını oluşturmaktadır. Kasa, kullanım amacına göre iletken kasa, ara kasa, üretim kasası ve liner kasa olarak ayrılabilmekte olup, bunların petrol kuyularındaki yapıları Şekil 1'de gösterilmektedir.
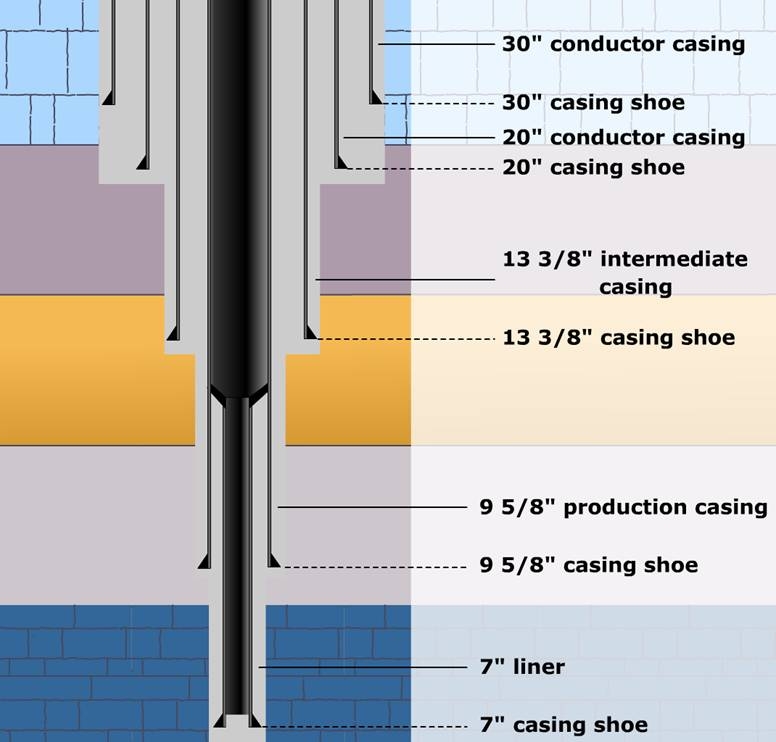
①İletken Muhafazası: Tipik olarak API sınıfları K55, J55 veya H40'ı kullanan iletken mahfaza, kuyu başını stabilize eder ve çapı genellikle 20 inç veya 16 inç civarında olan sığ akiferleri izole eder.
②Ara Gövde: Genellikle API sınıfları K55, N80, L80 veya P110'dan yapılan ara muhafaza, tipik çapları 13 3/8 inç, 11 3/4 inç veya 9 5/8 inç olan dengesiz oluşumları ve değişken basınç bölgelerini izole etmek için kullanılır .
③Üretim Muhafazası: API sınıfları J55, N80, L80, P110 veya Q125 gibi yüksek kaliteli çelikten üretilen üretim kasası, genellikle 9 5/8 inç, 7 inç veya 5 1/2 inç çaplarda üretim basınçlarına dayanacak şekilde tasarlanmıştır.
④Astar Muhafazası: Linerlar, tipik olarak 7 inç, 5 inç veya 4 1/2 inç çaplarında olan API L80, N80 veya P110 sınıflarındaki malzemeler kullanılarak kuyunun iç kısmını rezervuara doğru uzatır.
⑤Boru: Boru sistemi, J55, L80 veya P110 API sınıflarını kullanarak hidrokarbonları yüzeye taşır ve 4 1/2 inç, 3 1/2 inç veya 2 7/8 inç çaplarda mevcuttur.
IV. Sondaj borusu
1. Sondaj Aletleri İçin Borunun Sınıflandırılması ve İşlevi
Kare matkap borusu, matkap borusu, ağırlıklı matkap borusu ve delme aletlerindeki matkap yakası matkap borusunu oluşturur. Matkap borusu, matkap ucunu yerden kuyunun dibine süren çekirdek delme aletidir ve aynı zamanda yerden kuyunun dibine giden bir kanaldır. Üç ana rolü vardır:
① Matkap ucunu matkaba sürmek için torku iletmek;
② Kuyu dibindeki kayanın basıncını kırmak için ağırlığını matkap ucuna vermek;
③ Yıkama sıvısını taşımak, yani çamuru yüksek basınçlı çamur pompaları aracılığıyla zeminden delmek, kaya kalıntılarını temizlemek ve matkap ucunu soğutmak ve kaya kalıntılarını taşımak için sondaj sütununu kuyunun dibine doğru sondaj deliği akışına taşımak Kuyu delme amacına ulaşmak için kolonun dış yüzeyi ile halka arasındaki kuyunun duvarı boyunca zemine geri dönün.
Matkap borusu, çekme, sıkıştırma, burulma, bükülme ve diğer gerilimler gibi çeşitli karmaşık alternatif yüklere dayanmak için delme işleminde kullanılır. İç yüzey ayrıca yüksek basınçlı çamur aşınmasına ve korozyona maruz kalır.
(1) Kare Sondaj Borusu: Kare sondaj boruları iki türde gelir: dörtgen ve altıgen. Çin'in petrol sondaj borusunda, her sondaj kolonu seti genellikle dörtgen tipte bir sondaj borusu kullanır. Özellikleri 63,5 mm (2-1/2 inç), 88,9 mm (3-1/2 inç), 107,95 mm (4-1/4 inç), 133,35 mm (5-1/4 inç), 152,4 mm (6 inç) vb.'dir. Kullanılan uzunluk genellikle 1214,5 m'dir.
(2) Sondaj Borusu: Matkap borusu, kare matkap borusunun alt ucuna bağlanan kuyu delme için birincil araçtır ve sondaj kuyusu derinleşmeye devam ettikçe, matkap borusu matkap sütununu birbiri ardına uzatmaya devam eder. Matkap borusunun özellikleri şunlardır: 60,3 mm (2-3/8 inç), 73,03 mm (2-7/8 inç), 88,9 mm (3-1/2 inç), 114,3 mm (4-1/2 inç), 127 mm (5 inç), 139,7 mm (5-1/2 inç) vb.
(3) Ağır Hizmet Sondaj Borusu: Ağırlıklı sondaj borusu, sondaj borusunu ve sondaj bileziğini birbirine bağlayan, sondaj borusunun kuvvet durumunu iyileştirebilen ve matkap ucu üzerindeki basıncı artırabilen bir geçiş aracıdır. Ağırlıklı sondaj borusunun ana özellikleri 88,9 mm (3-1/2 inç) ve 127 mm'dir (5 inç).
(4) Matkap Yakası: Matkap yakası, yüksek sertliğe sahip özel kalın duvarlı bir boru olan matkap borusunun alt kısmına bağlanır. Kayayı kırmak için matkap ucuna baskı uygular ve düz bir kuyu delerken kılavuz rolü oynar. Matkap yakalarının genel özellikleri 158,75 mm (6-1/4 inç), 177,85 mm (7 inç), 203,2 mm (8 inç), 228,6 mm (9 inç) vb.'dir.
V. Hat borusu
1. Hat Borusunun Sınıflandırılması
Hat borusu, çelik boru kısaltmasıyla petrol ve gaz endüstrisinde petrol, rafine edilmiş petrol, doğal gaz ve su boru hatlarını iletmek için kullanılır. Petrol ve gaz iletim boru hatları ana hat, branşman ve kentsel boru hattı şebeke boru hatlarına ayrılır. Üç çeşit ana hat boru hattı iletimi, ∅406 ~ 1219 mm, 10 ~ 25 mm duvar kalınlığı, X42 ~ X80 çelik sınıfı özelliklerine sahiptir; branşman hat boru hattı ve kentsel boru hattı şebeke boru hatları genellikle ∅114 ~ 700 mm, 6 ~ 20 mm duvar kalınlığı, X42 ~ X80 çelik sınıfı özelliklerine sahiptir. Çelik sınıfı X42~X80'dir. Hat borusu kaynaklı ve dikişsiz tiplerde mevcuttur. Kaynaklı Hat Borusu Dikişsiz Hat Borusundan daha fazla kullanılır.
2. Hat Borusu Standardı
API Spec 5L – Hat Borusu Şartnamesi
ISO 3183 – Petrol ve Doğal Gaz Endüstrileri – Boru Hattı Taşıma Sistemleri için Çelik Boru
3. PSL1 ve PSL2
PSL kısaltmasıdır ürün spesifikasyon seviyesi. Boru hattı ürününün şartname seviyesi PSL 1 ve PSL 2 olarak ikiye ayrılır ve kalite seviyesi PSL 1 ve PSL 2 olarak ikiye ayrılır. PSL 2, PSL 1'den daha yüksektir; iki şartname seviyesinin sadece farklı test gereksinimleri değil, aynı zamanda kimyasal bileşim ve mekanik özellik gereksinimleri de farklıdır, bu nedenle API 5L siparişine göre, sözleşme şartları, şartnameleri, çelik sınıfını ve diğer ortak göstergeleri belirtmenin yanı sıra, ürün şartname seviyesini, yani PSL 1 veya PSL 2'yi de belirtmelidir. PSL 2'de kimyasal bileşim, çekme özellikleri, darbe gücü, tahribatsız muayene ve diğer göstergeler PSL 1'den daha katıdır.
4. Hat Borusu Çelik Sınıfı, Kimyasal Bileşimi ve Mekanik Özellikleri
Düşükten yükseğe doğru hat borusu çelik sınıfları A25, A, B, X42, X46, X52, X60, X65, X70 ve X80 olarak ayrılır. Ayrıntılı Kimyasal Bileşim ve Mekanik Özellikler için lütfen API 5L Spesifikasyonu, 46. Baskı Kitabına bakın.
5. Hat Borusu Hidrostatik Testi ve Tahribatsız Muayene Gereksinimleri
Hat borusunun her bir dalda hidrolik testi yapılmalıdır ve standart, hidrolik basıncın tahribatsız üretimine izin vermemektedir, bu da API standardı ile standartlarımız arasındaki büyük bir farktır. PSL 1 tahribatsız test gerektirmez; PSL 2 tahribatsız testin her bir dalda yapılması gerekir.
VI. Premium Bağlantılar
1. Premium Bağlantılara Giriş
Premium Bağlantı, API dişinden farklı, benzersiz bir yapıya sahip bir boru dişidir. Mevcut API dişli petrol muhafazası petrol kuyusu işletmeciliğinde yaygın olarak kullanılmasına rağmen, eksiklikleri bazı petrol sahalarının benzersiz ortamında açıkça görülmektedir: API yuvarlak dişli boru kolonu, sızdırmazlık performansı daha iyi olmasına rağmen, dişli parçanın taşıdığı çekme kuvveti boru gövdesinin mukavemetinin yalnızca 60% ila 80%'sine eşdeğerdir ve bu nedenle derin kuyuların işletilmesinde kullanılamaz; API önyargılı trapez dişli boru kolonu, çekme performansı API yuvarlak dişli bağlantıdan çok daha yüksek olmasına rağmen, sızdırmazlık performansı o kadar iyi değildir. Kolonun çekme performansı API yuvarlak dişli bağlantıdan çok daha yüksek olmasına rağmen, sızdırmazlık performansı çok iyi değildir, bu nedenle yüksek basınçlı gaz kuyularının işletilmesinde kullanılamaz; Ayrıca dişli gres sadece 95℃'nin altındaki sıcaklıklarda görevini yerine getirebildiğinden yüksek sıcaklıklı kuyuların işletilmesinde kullanılamaz.
API yuvarlak dişli ve kısmi trapez dişli bağlantıyla karşılaştırıldığında premium bağlantı aşağıdaki yönlerde çığır açıcı ilerleme kaydetmiştir:
(1) Esneklik ve metal sızdırmazlık yapısı tasarımı sayesinde iyi sızdırmazlık, bağlantı gazı sızdırmazlığını, akma basıncı dahilinde boru gövdesi sınırına ulaşmaya karşı dirençli hale getirir;
(2) Yağ muhafazasının özel tokalı bağlantısıyla bağlanan bağlantının yüksek mukavemeti, kayma problemini temel olarak çözmek için bağlantı mukavemeti boru gövdesinin mukavemetine ulaşır veya onu aşar;
(3) Malzeme seçimi ve yüzey işleme prosesinin iyileştirilmesiyle, temel olarak iplik yapışması tokası sorunu çözüldü;
(4) Yapının optimizasyonu yoluyla, eklem gerilimi dağılımının daha makul olması ve gerilim korozyonuna karşı dirence daha elverişli olması;
(5) Omuz yapısı makul bir tasarıma sahiptir, böylece tokanın çalışması daha erişilebilir hale gelir.
Petrol ve gaz endüstrisi, boru teknolojisinde önemli ilerlemeleri temsil eden 100'den fazla patentli birinci sınıf bağlantıya sahiptir. Bu özel dişli tasarımları, üstün sızdırmazlık yetenekleri, artırılmış bağlantı gücü ve çevresel streslere karşı gelişmiş direnç sunar. Yüksek basınçlar, aşındırıcı ortamlar ve aşırı sıcaklıklar gibi zorlukları ele alarak, bu yenilikler dünya çapında petrol açısından sağlıklı operasyonlarda mükemmel güvenilirlik ve verimlilik sağlar. Birinci sınıf bağlantılarda sürekli araştırma ve geliştirme, enerji sektöründe teknolojik mükemmelliğe olan sürekli bağlılığı yansıtan daha güvenli ve daha üretken sondaj uygulamalarını desteklemedeki temel rollerinin altını çizer.
VAM® Bağlantısı: Zorlu ortamlardaki sağlam performansıyla bilinen VAM® bağlantıları, gelişmiş metalden metale sızdırmazlık teknolojisine ve yüksek tork özelliklerine sahiptir ve derin kuyularda ve yüksek basınçlı rezervuarlarda güvenilir operasyon sağlar.
TenarisHydril Kama Serisi: Bu seri, olağanüstü gaz sızdırmazlığı ve sıkıştırma ve çekme kuvvetlerine karşı dayanıklılığıyla bilinen Blue®, Dopeless® ve Wedge 521® gibi bir dizi bağlantı sunar ve operasyonel güvenliği ve verimliliği artırır.
TSH® Mavi: Tenaris tarafından tasarlanan TSH® Blue bağlantıları, özel bir çift omuz tasarımı ve yüksek performanslı bir diş profili kullanarak, kritik delme uygulamalarında mükemmel yorulma direnci ve makyaj kolaylığı sağlar.
Prideco™ XT® Bağlantısını Verin: NOV tarafından tasarlanan XT® bağlantıları, benzersiz bir metal-metal conta ve sağlam bir diş formuna sahiptir, üstün tork kapasitesi ve aşınmaya karşı direnç sağlayarak bağlantının çalışma ömrünü uzatır.
Avcılık Seal-Lock® Bağlantısı: Metalden metale conta ve benzersiz diş profiline sahip Hunting'in Seal-Lock® bağlantısı, hem karada hem de denizde sondaj operasyonlarında üstün basınç direnci ve güvenilirliği ile ünlüdür.
Çözüm
Sonuç olarak, petrol ve gaz endüstrisi için hayati önem taşıyan karmaşık çelik boru ağı, zorlu ortamlara ve karmaşık operasyonel taleplere dayanacak şekilde tasarlanmış çok çeşitli özel ekipmanları kapsar. Sağlıklı duvarları destekleyen ve koruyan temel muhafaza borularından, çıkarma ve enjeksiyon süreçlerinde kullanılan çok yönlü borulara kadar her boru türü, hidrokarbonları keşfetme, üretme ve taşımada farklı bir amaca hizmet eder. API spesifikasyonları gibi standartlar, bu borularda tekdüzelik ve kaliteyi garanti ederken, birinci sınıf bağlantılar gibi yenilikler zorlu koşullarda performansı artırır. Teknoloji geliştikçe, bu kritik bileşenler ilerler ve küresel enerji operasyonlarında verimliliği ve güvenilirliği artırır. Bu boruları ve spesifikasyonlarını anlamak, modern enerji sektörünün altyapısındaki vazgeçilmez rollerinin altını çizer.