giriiş
Elektrik üretimi, petrol ve gaz, petrokimyasallar ve rafineriler gibi endüstrilerde dikişsiz borular, özellikle aşırı sıcaklıklara, yüksek basınçlara ve sert, aşındırıcı ortamlara dayanması gereken ekipmanlarda temel bileşenlerdir. Kazanlar, ısı eşanjörleri, kondansatörler, aşırı ısıtıcılar, hava ön ısıtıcıları ve ekonomizerler bu boruları kullanır. Bu uygulamaların her biri, performans, güvenlik ve uzun ömür sağlamak için belirli malzeme özellikleri gerektirir. Kazan ve ısı eşanjörü için dikişsiz boruların seçimi, belirli sıcaklığa, basınca, korozyon direncine ve mekanik mukavemete bağlıdır.
Bu kılavuz, karbon çeliği, alaşımlı çelik, paslanmaz çelik, titanyum alaşımları, nikel bazlı alaşımlar, bakır alaşımları ve zirkonyum alaşımları dahil olmak üzere dikişsiz borular için kullanılan çeşitli malzemelere derinlemesine bir bakış sağlar. Ayrıca ilgili standartları ve dereceleri inceleyerek Kazan ve Isı Eşanjörü projeleriniz için daha bilinçli kararlar almanıza yardımcı olacağız.
CS, AS, SS, Nikel Alaşımları, Titanyum ve Zirkonyum Alaşımları, Bakır ve Bakır Alaşımlarına Genel Bakış
1. Korozyon Direnci Özellikleri
Dikişsiz borularda kullanılan her malzemenin, farklı ortamlara uygunluğunu belirleyen belirli korozyon direnci özellikleri vardır.
Karbon çelik: Sınırlı korozyon direnci, genellikle koruyucu kaplamalar veya astarlarla kullanılır. İşlenmediği takdirde su ve oksijen varlığında paslanmaya maruz kalır.
Alaşımlı çelik: Oksidasyon ve korozyona karşı orta düzeyde direnç. Krom ve molibden gibi alaşım ilaveleri yüksek sıcaklıklarda korozyon direncini artırır.
Paslanmaz çelik: Krom içeriği sayesinde genel korozyona, stres korozyon çatlamasına ve çukurlaşmaya karşı mükemmel direnç. 316L gibi daha yüksek sınıflar, klorür kaynaklı korozyona karşı geliştirilmiş dirence sahiptir.
Nikel Esaslı Alaşımlar: Asidik, alkali ve klorür açısından zengin ortamlar gibi agresif ortamlara karşı olağanüstü direnç. Son derece aşındırıcı uygulamalar Inconel 625, Hastelloy C276 ve Alloy 825 gibi alaşımları kullanır.
Titanyum ve Zirkonyum: Deniz suyu tuzlu sularına ve diğer yüksek aşındırıcı ortamlara karşı üstün direnç. Titanyum özellikle klorür ve asidik ortamlara karşı dirençlidir, zirkonyum alaşımları ise yüksek asidik koşullarda mükemmeldir.
Bakır ve Bakır Alaşımları: Tatlı su ve deniz suyunda mükemmel korozyon direncine sahip olup, bakır-nikel alaşımları deniz ortamlarında olağanüstü direnç göstermektedir.
2. Fiziksel ve Termal Özellikler
Karbon çelik:
Yoğunluk: 7,85 g/cm³
Erime Noktası: 1.425-1.500°C
Isıl İletkenlik: ~50 W/m·K
Alaşımlı çelik:
Yoğunluk: Alaşım elementlerine göre biraz değişir, tipik olarak 7,85 g/cm³ civarındadır
Erime Noktası: 1.450-1.530°C
Isıl İletkenlik: Alaşım elementleri nedeniyle karbon çeliklerinden daha düşüktür.
Paslanmaz çelik:
Yoğunluk: 7,75-8,0 g/cm³
Erime Noktası: ~1.400-1.530°C
Isıl İletkenlik: ~16 W/m·K (karbon çeliğinden daha düşük).
Nikel Esaslı Alaşımlar:
Yoğunluk: 8,4-8,9 g/cm³ (alaşıma bağlıdır)
Erime Noktası: 1.300-1.400°C
Isıl İletkenlik: Genellikle düşük, ~10-16 W/m·K.
Titanyum:
Yoğunluk: 4,51 g/cm³
Erime Noktası: 1.668°C
Isıl İletkenlik: ~22 W/m·K (nispeten düşük).
Bakır:
Yoğunluk: 8,94 g/cm³
Erime Noktası: 1.084°C
Isıl İletkenlik: ~390 W/m·K (mükemmel ısıl iletkenlik).
3. Kimyasal Bileşim
Karbon çelik: Başlıca 0.3%-1.2% karbonlu demir ve az miktarda manganez, silisyum ve kükürt.
Alaşımlı çelik: Mukavemet ve sıcaklık direncini artırmak için krom, molibden, vanadyum ve tungsten gibi elementler içerir.
Paslanmaz çelik: Genellikle 10.5%-30% kromun yanı sıra, dereceye bağlı olarak nikel, molibden ve diğer elementleri içerir.
Nikel Esaslı Alaşımlar: Korozyon direncini arttırmak için krom, molibden ve diğer alaşım elementleri ile ağırlıklı olarak nikel (40%-70%).
Titanyum: 1. ve 2. sınıflar ticari olarak saf titanyumdan oluşurken, 5. sınıf (Ti-6Al-4V) 6% alüminyum ve 4% vanadyumdan oluşmaktadır.
Bakır alaşımları: Bakır alaşımları korozyon direnci için nikel (10%-30%) gibi çeşitli elementler içerir (örneğin, Cu-Ni 90/10).
4. Mekanik Özellikler
Karbon çelik: Çekme Dayanımı: 400-500 MPa, Akma Dayanımı: 250-350 MPa, Uzama: 15%-25%
Alaşımlı çelik: Çekme Dayanımı: 500-900 MPa, Akma Dayanımı: 300-700 MPa, Uzama: 10%-25%
Paslanmaz çelik: Çekme Dayanımı: 485-690 MPa (304/316), Akma Dayanımı: 170-300 MPa, Uzama: 35%-40%
Nikel Esaslı Alaşımlar: Çekme Dayanımı: 550-1.000 MPa (Inconel 625), Akma Dayanımı: 300-600 MPa, Uzama: 25%-50%
Titanyum: Çekme Dayanımı: 240-900 MPa (sınıfa göre değişir), Akma Dayanımı: 170-880 MPa, Uzama: 15%-30%
Bakır alaşımları: Çekme Dayanımı: 200-500 MPa (alaşıma bağlı), Akma Dayanımı: 100-300 MPa, Uzama: 20%-35%
5. Isıl İşlem (Teslimat Koşulu)
Karbon ve Alaşımlı Çelik: Tavlanmış veya normalize edilmiş durumda teslim edilir. Isıl işlemler, mukavemeti ve tokluğu artırmak için söndürme ve temperlemeyi içerir.
Paslanmaz çelik: İç gerilimleri gidermek ve sünekliği artırmak için tavlanmış halde teslim edilir.
Nikel Esaslı Alaşımlar: Mekanik özellikleri ve korozyon direncini optimize etmek için çözelti tavlanmıştır.
Titanyum ve Zirkonyum: Genellikle sünekliği ve tokluğu en üst düzeye çıkarmak için tavlanmış halde teslim edilir.
Bakır alaşımları: Özellikle şekillendirme uygulamaları için yumuşak tavlanmış halde teslim edilir.
6. Şekillendirme
Karbon ve Alaşımlı Çelik: Sıcak veya soğuk şekillendirilebilirler ancak alaşımlı çelikler daha yüksek mukavemetleri nedeniyle daha fazla emek gerektirirler.
Paslanmaz çelik: Soğuk şekillendirme yaygındır, ancak iş sertleştirme oranları karbon çeliğinden daha yüksektir.
Nikel Esaslı Alaşımlar: Yüksek mukavemet ve sertleşme oranları nedeniyle şekillendirilmesi daha zordur; sıklıkla sıcak işleme gerektirir.
Titanyum: Oda sıcaklığındaki yüksek mukavemeti nedeniyle şekillendirme işlemi yüksek sıcaklıklarda en iyi şekilde yapılır.
Bakır alaşımları: İyi sünekliğinden dolayı şekillendirilmesi kolaydır.
7. Kaynakçılık
Karbon ve Alaşımlı Çelik: Genellikle geleneksel tekniklerle kaynak yapmak kolaydır, ancak ön ısıtma ve kaynak sonrası ısıl işlem (PWHT) gerekebilir.
Paslanmaz çelik: Yaygın kaynak yöntemleri arasında TIG, MIG ve ark kaynağı bulunur. Hassasiyeti önlemek için ısı girişinin dikkatli bir şekilde kontrol edilmesi gerekir.
Nikel Esaslı Alaşımlar: Yüksek termal genleşme ve çatlama eğilimi nedeniyle kaynaklanması zordur.
Titanyum: Kirlenmeyi önlemek için korumalı bir ortamda (inert gaz) kaynaklanmıştır. Titanyumun yüksek sıcaklıklardaki reaktifliği nedeniyle önlemlere ihtiyaç vardır.
Bakır alaşımları: Özellikle bakır-nikel alaşımlarının kaynaklanması kolaydır, ancak çatlamaların önlenmesi için ön ısıtma gerekebilir.
8. Kaynakların Korozyonu
Paslanmaz çelik: Uygun şekilde kontrol edilmezse kaynak ısısından etkilenen bölgede lokal korozyon (örneğin çukurlaşma, çatlak korozyonu) meydana gelebilir.
Nikel Esaslı Alaşımlar: Yüksek sıcaklıklarda klorürlere maruz kaldığında stres korozyon çatlamasına karşı hassastır.
Titanyum: Kırılganlığı önlemek için kaynakların oksijenden uygun şekilde korunması gerekir.
9. Kireç çözme, Turşulama ve Temizleme
Karbon ve Alaşımlı Çelik: Turşulama, ısıl işlemden sonra yüzey oksitlerini giderir. Yaygın asitler arasında hidroklorik ve sülfürik asitler bulunur.
Paslanmaz Çelik ve Nikel Alaşımları: Nitrik/hidroflorik asitle asitleme, kaynak sonrası oluşan ısı izlerini gidermek ve korozyon direncini geri kazandırmak için kullanılır.
Titanyum: Metalin zarar görmesini engelleyerek yüzeyi temizlemek ve oksitleri uzaklaştırmak için hafif asitli asitleme solüsyonları kullanılır.
Bakır alaşımları: Asit temizliği, yüzeydeki kararmaları ve oksitleri gidermek için kullanılır.
10. Yüzey İşlemleri (AP, BA, MP, EP, vb.)
AP (Tavlanmış ve Turşulanmış): Tavlama ve asitleme işleminden sonra çoğu paslanmaz ve nikel alaşımı için standart yüzey işlemi.
BA (Parlak Tavlı): Kontrollü bir atmosferde tavlama yapılarak pürüzsüz, yansıtıcı bir yüzey elde edilir.
MP (Mekanik Cilalı): Mekanik parlatma, yüzey pürüzsüzlüğünü iyileştirerek kirlenme ve korozyon başlama riskini azaltır.
EP (Elektroparlatılmış): Yüzeydeki malzemeyi kaldırarak ultra pürüzsüz bir yüzey oluşturan, yüzey pürüzlülüğünü azaltan ve korozyon direncini artıran bir elektrokimyasal işlemdir.
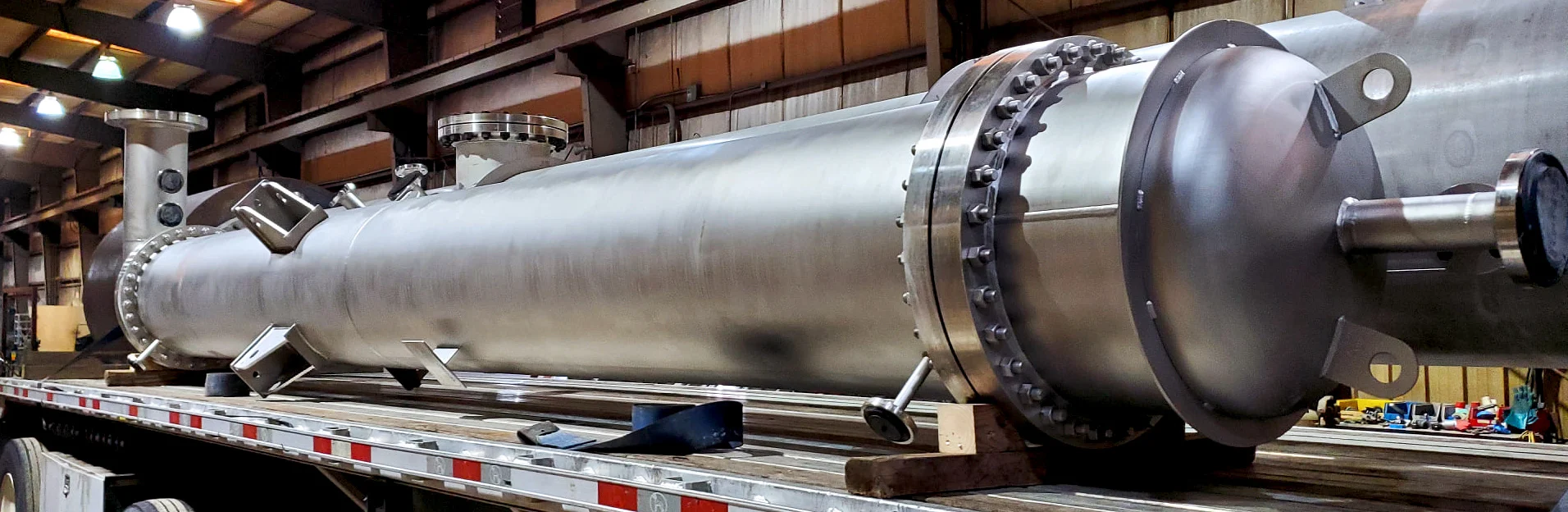
Paslanmaz Isı Eşanjörü
I. Dikişsiz Boruları Anlamak
Dikişsiz borular, kaynaklı borulardan, bazı yüksek basınç uygulamalarında zayıf bir nokta olabilen kaynaklı bir dikişe sahip olmamaları bakımından farklıdır. Dikişsiz borular, başlangıçta katı bir kütükten oluşturulur, daha sonra ısıtılır ve daha sonra boru şeklini oluşturmak için ekstrüde edilir veya bir mandrel üzerinden çekilir. Dikişlerin olmaması, onlara üstün bir güç ve güvenilirlik kazandırır ve bu da onları yüksek basınç ve yüksek sıcaklık ortamları için ideal hale getirir.
Yaygın Uygulamalar:
Kazanlar: Yüksek sıcaklık ve basıncın söz konusu olduğu su borulu ve alev borulu kazanların yapımında dikişsiz borular olmazsa olmazdır.
Isı Eşanjörleri: İki akışkan arasında ısı transferi sağlamak amacıyla kullanılan ısı değiştiricilerdeki dikişsiz borular korozyona dayanıklı olmalı ve termal verimi korumalıdır.
Kondansatörler: Dikişsiz borular, elektrik üretim ve soğutma sistemlerinde buharın suya yoğunlaştırılmasında kullanılır.
Kızdırıcılar: Dikişsiz borular, kazanlarda buharın aşırı ısıtılmasında kullanılarak, enerji santrallerindeki türbinlerin verimini artırmaktadır.
Hava Ön Isıtıcıları: Bu borular baca gazlarındaki ısıyı havaya aktararak kazan verimliliğini artırır.
Ekonomizerler: Ekonomizerlerdeki dikişsiz borular, kazan egzozundan çıkan atık ısıyı kullanarak besleme suyunu önceden ısıtarak termal verimliliği artırır.
Kazanlar, ısı eşanjörleri, kondansatörler, süper ısıtıcılar, hava ön ısıtıcıları ve ekonomizerler, özellikle ısı transferi, enerji üretimi ve akışkan yönetimiyle ilgili olanlar olmak üzere birçok endüstride ayrılmaz bileşenlerdir. Özellikle, bu bileşenler aşağıdaki endüstrilerde birincil kullanım bulmaktadır:
1. Güç Üretim Endüstrisi
Kazanlar: Elektrik santrallerinde kimyasal enerjiyi ısı enerjisine dönüştürmek için kullanılır, çoğunlukla buhar üretimi için.
Süper Isıtıcılar, Ekonomizerler ve Hava Ön Isıtıcıları: Bu bileşenler, yanma havasını önceden ısıtarak, egzoz gazlarından ısıyı geri kazanarak ve buharı daha fazla ısıtarak verimliliği artırır.
Isı Değiştiriciler ve Kondenserler: Termik santrallerde, özellikle buharla çalışan türbinlerde ve soğutma çevrimlerinde soğutma ve ısı geri kazanımı amacıyla kullanılırlar.
2. Petrol ve Gaz Endüstrisi
Isı Eşanjörleri: Ham petrol damıtımı veya açık deniz gaz işleme platformları gibi akışkanlar arasında ısı transferi yapılan rafinasyon süreçlerinde hayati öneme sahiptir.
Kazanlar ve Ekonomizerler: Rafinerilerde ve petrokimya tesislerinde buhar üretimi ve enerji geri kazanımı amacıyla kullanılır.
Kondansatörler: Damıtma işlemleri sırasında gazları sıvıya yoğunlaştırmak için kullanılır.
3. Kimya Endüstrisi
Isı Değiştiriciler: Kimyasal reaksiyonları ısıtmak veya soğutmak ve ekzotermik reaksiyonlardan ısı geri kazanmak için yaygın olarak kullanılır.
Kazanlar ve Süper Isıtıcılar: Çeşitli kimyasal prosesler için gerekli buharı üretmek ve damıtma ve reaksiyon adımları için enerji sağlamak amacıyla kullanılırlar.
Hava Ön Isıtıcıları ve Ekonomizerler: Egzoz gazlarından ısıyı geri kazanarak ve yakıt tüketimini azaltarak enerji yoğun kimyasal proseslerde verimliliği artırın.
4. Denizcilik Endüstrisi
Kazanlar ve Isı Eşanjörleri: Deniz araçlarında buhar üretimi, ısıtma ve soğutma sistemleri için olmazsa olmazdır. Deniz ısı eşanjörleri genellikle geminin motorlarını soğutmak ve güç üretmek için kullanılır.
Kondenserler: Egzoz buharını gemi kazan sistemlerinde tekrar kullanılmak üzere suya dönüştürmek için kullanılır.
5. Gıda ve İçecek Endüstrisi
Isı Eşanjörleri: Genellikle pastörizasyon, sterilizasyon ve buharlaştırma işlemlerinde kullanılır.
Kazanlar ve Ekonomizerler: Gıda işleme operasyonlarında buhar üretmek ve egzozdan çıkan ısıyı geri kazanarak yakıt tüketiminden tasarruf etmek için kullanılır.
6. HVAC (Isıtma, Havalandırma ve Klima)
Isı Eşanjörleri ve Hava Ön Isıtıcıları: Binaların ve endüstriyel tesislerin ısıtma veya soğutmasını sağlamak amacıyla akışkanlar veya gazlar arasında verimli ısı transferi sağlamak amacıyla HVAC sistemlerinde kullanılır.
Kondenserler: Klima sistemlerinde soğutucu akışkanın ısısını atmak için kullanılır.
7. Kağıt Hamuru ve Kağıt Endüstrisi
Kazanlar, Isı Eşanjörleri ve Ekonomizerler: Kağıt hamuru hazırlama, kağıt kurutma ve kimyasal geri kazanımı gibi proseslerde buhar ve ısı geri kazanımı sağlarlar.
Süper Isıtıcılar ve Hava Ön Isıtıcıları: Kağıt fabrikalarındaki geri kazanım kazanlarında ve genel ısı dengesinde enerji verimliliğini artırır.
8. Metalurji ve Çelik Endüstrisi
Isı Eşanjörleri: Çelik üretimi ve metalurjik proseslerde sıcak gazların ve sıvıların soğutulmasında kullanılır.
Kazanlar ve Ekonomizerler: Yüksek fırın işletimi, ısıl işlem ve haddeleme gibi çeşitli prosesler için ısı sağlarlar.
9. İlaç Endüstrisi
Isı Değiştiriciler: İlaç üretimi, fermantasyon prosesleri ve steril ortamlarda sıcaklığı kontrol etmek için kullanılır.
Kazanlar: İlaç ekipmanlarının sterilizasyonu ve ısıtılması için gerekli buharı üretirler.
10. Atıktan Enerji Üretim Tesisleri
Kazanlar, Kondenserler ve Ekonomizerler: Atıkların yanma yoluyla enerjiye dönüştürülmesini, aynı zamanda ısının geri kazanılarak verimliliğin artırılmasını sağlayan cihazlardır.
Şimdi, bu zorlu uygulamalar için uygun dikişsiz boruları oluşturan malzemelere bir göz atalım.
II. Kazan ve Isı Eşanjörü için Karbon Çelik Borular
Karbon çeliği, endüstriyel uygulamalarda dikişsiz borular için en yaygın kullanılan malzemelerden biridir, bunun başlıca nedeni mükemmel mukavemeti ve uygun fiyatlı ve yaygın olarak bulunabilmesidir. Karbon çelik borular orta düzeyde sıcaklık ve basınç direnci sunarak onları çok çeşitli uygulamalar için uygun hale getirir.
Karbon Çeliklerinin Özellikleri:
Yüksek Dayanıklılık: Karbon çelik borular önemli basınç ve strese dayanabilir, bu da onları kazanlarda ve ısı eşanjörlerinde kullanım için ideal hale getirir.
Maliyet Etkinliği: Diğer malzemelerle karşılaştırıldığında karbon çeliği nispeten ucuzdur, bu da onu büyük ölçekli endüstriyel uygulamalarda popüler bir seçim haline getirir.
Orta Derecede Korozyon Direnci: Karbon çeliği paslanmaz çelik kadar korozyona dayanıklı olmasa da, aşındırıcı ortamlarda ömrünü uzatmak için kaplamalar veya astarlarla işlenebilir.
Ana Standartlar ve Sınıflar:
ASTM A179: Bu standart, ısı eşanjörü ve kondenser uygulamaları için kullanılan dikişsiz soğuk çekilmiş düşük karbonlu çelik boruları kapsar. Bu borular mükemmel ısı transfer özelliklerine sahiptir ve genellikle düşük ila orta sıcaklık ve basınç uygulamalarında kullanılır.
ASTM A192: Yüksek basınçlı servis için tasarlanmış dikişsiz karbon çelik kazan boruları. Bu borular buhar üretimi ve diğer yüksek basınçlı ortamlarda kullanılır.
ASTM A210: Bu standart, kazan ve kızdırıcı uygulamaları için dikişsiz orta karbonlu çelik boruları kapsar. A-1 ve C sınıfları, çeşitli seviyelerde mukavemet ve sıcaklık direnci sunar.
ASTM A334 (Sınıf 1, 3, 6): Düşük sıcaklık hizmeti için tasarlanmış dikişsiz ve kaynaklı karbon çelik borular. Bu sınıflar ısı değiştiricilerde, kondansatörlerde ve diğer düşük sıcaklık uygulamalarında kullanılır.
EN 10216-2 (P235GH, P265GH TC1/TC2): Basınçlı uygulamalarda, özellikle kazanlarda ve yüksek sıcaklık servislerinde kullanılan dikişsiz çelik borular için Avrupa standardı.
Karbon çelik borular, yüksek mukavemet ve orta düzeyde korozyon direncinin gerekli olduğu Kazan ve Isı Eşanjörü uygulamaları için mükemmel bir seçimdir. Ancak, yalnızca aşırı yüksek sıcaklıkları değil aynı zamanda sert aşındırıcı ortamları da içeren uygulamalar için, üstün dirençleri ve dayanıklılıkları nedeniyle genellikle alaşımlı veya paslanmaz çelik borular tercih edilir.
III. Kazan ve Isı Eşanjörü için Alaşımlı Çelik Borular
Alaşımlı çelik borular, yüksek sıcaklık ve yüksek basınç Kazan ve Isı eşanjörü uygulamaları için tasarlanmıştır. Bu borular, mukavemetlerini, sertliklerini ve korozyon ve ısıya karşı dirençlerini artırmak için krom, molibden ve vanadyum gibi elementlerle alaşımlanmıştır. Alaşımlı çelik borular, olağanüstü mukavemetleri ve ısıya ve basınca karşı dirençleri nedeniyle süper ısıtıcılar, ekonomizerler ve yüksek sıcaklıklı ısı eşanjörleri gibi kritik uygulamalarda yaygın olarak kullanılır.
Alaşımlı Çeliklerin Özellikleri:
Yüksek Isı Direnci: Krom ve molibden gibi alaşım elementleri bu tüplerin yüksek sıcaklık performansını artırarak, aşırı sıcaklıkların olduğu uygulamalar için uygun hale getirir.
Gelişmiş Korozyon Direnci: Alaşımlı çelik borular, özellikle yüksek sıcaklık ortamlarında, karbon çeliğine kıyasla oksidasyona ve korozyona karşı daha iyi direnç sunar.
Arttırılmış Dayanıklılık: Alaşım elementleri ayrıca bu boruların dayanıklılığını artırarak, kazanlarda ve diğer kritik ekipmanlarda yüksek basınca dayanmalarını sağlar.
Ana Standartlar ve Sınıflar:
ASTM A213 (T5, T9, T11, T22, T91, T92 Sınıfları): Bu standart, kazanlarda, kızdırıcılarda ve ısı eşanjörlerinde kullanılan dikişsiz ferritik ve östenitik alaşımlı çelik boruları kapsar. Sınıflar alaşım bileşimlerinde farklılık gösterir ve belirli sıcaklık ve basınç gereksinimlerine göre seçilir.
T5 ve T9: Orta ve yüksek sıcaklıktaki servislere uygundur.
T11 ve T22: Genellikle yüksek sıcaklık uygulamalarında kullanılır, gelişmiş ısı direnci sunar.
T91 ve T92: Enerji santrallerinde ultra yüksek sıcaklıklarda kullanıma uygun, gelişmiş yüksek dayanımlı alaşımlar.
EN 10216-2 (16Mo3, 13CrMo4-5, 10CrMo9-10, 15NiCuMoNb5-6-4, X20CrMoV11-1): Yüksek sıcaklık uygulamalarında kullanılan dikişsiz alaşımlı çelik borular için Avrupa standartları. Bu borular genellikle enerji santrallerindeki kazanlarda, aşırı ısıtıcılarda ve ekonomizerlerde kullanılır.
16Mo3: Kazanlarda ve basınçlı kaplarda kullanıma uygun, yüksek sıcaklık özelliklerine sahip alaşımlı bir çeliktir.
13CrMo4-5 ve 10CrMo9-10: Yüksek sıcaklık uygulamaları için mükemmel ısı ve korozyon direnci sağlayan krom-molibden alaşımları.
Alaşımlı çelik borular, karbon çeliğinin Kazan ve Isı Eşanjörü için yeterli performans sağlayamayacağı yüksek sıcaklık ve yüksek basınç ortamları için tercih edilen seçenektir.
IV. Kazan ve Isı Eşanjörü için Paslanmaz Çelik Borular
Paslanmaz çelik borular olağanüstü korozyon direnci sunar ve bu da onları aşındırıcı sıvılar, yüksek sıcaklıklar ve zorlu ortamlar içeren Kazan ve Isı Eşanjörü uygulamaları için ideal hale getirir. Korozyon direncine ek olarak optimum performans için yüksek sıcaklık mukavemetinin de gerekli olduğu ısı eşanjörlerinde, aşırı ısıtıcılarda ve kazanlarda yaygın olarak kullanılırlar.
Paslanmaz Çeliklerin Özellikleri:
Korozyon Direnci: Paslanmaz çeliğin korozyona karşı direnci, yüzeyde koruyucu bir oksit tabakası oluşturan krom içeriğinden kaynaklanır.
Yüksek Sıcaklıklarda Yüksek Dayanıklılık: Paslanmaz çelik, yüksek sıcaklıklarda bile mekanik özelliklerini koruyarak, aşırı ısıtıcılar ve diğer ısı yoğun uygulamalar için uygundur.
Uzun Vadeli Dayanıklılık: Paslanmaz çeliğin korozyona ve oksidasyona karşı direnci, zorlu ortamlarda bile uzun bir kullanım ömrü sağlar.
Ana Standartlar ve Sınıflar:
ASTM A213 / ASTM A249: Bu standartlar, kazanlarda, aşırı ısıtıcılarda ve ısı eşanjörlerinde kullanım için dikişsiz ve kaynaklı paslanmaz çelik boruları kapsar. Yaygın sınıflar şunları içerir:
TP304 / TP304L (EN 1.4301 / 1.4307): Ostenitik paslanmaz çelik sınıfları korozyon direnci ve mukavemeti nedeniyle yaygın olarak kullanılmaktadır.
TP310S / TP310MoLN (EN 1.4845 / 1.4466): Mükemmel oksidasyon direncine sahip yüksek sıcaklığa dayanıklı paslanmaz çelik kaliteleri.
TP316 / TP316L (EN 1.4401 / 1.4404): Özellikle klorür ortamlarında korozyon direnci artırılmış molibden içeren kaliteler.
TP321 (EN 1.4541): Yüksek sıcaklık ortamlarında taneler arası korozyonu önlemek için kullanılan stabilize paslanmaz çelik sınıfıdır.
TP347H / TP347HFG (EN 1.4550 / 1.4961): Süper ısıtıcılar ve kazanlar gibi yüksek sıcaklık uygulamaları için yüksek karbonlu, stabilize edilmiş kaliteler.
UNS N08904 (904L) (EN 1.4539): Özellikle asidik ortamlarda mükemmel korozyon direncine sahip süper östenitik paslanmaz çelik.
ASTM A269: Genel korozyona dayanıklı servis için dikişsiz ve kaynaklı östenitik paslanmaz çelik boruları kapsar.
ASTM A789: Mükemmel korozyon direnci ve yüksek mukavemeti bir arada sunan, dubleks paslanmaz çelik borular için standarttır.
UNS S31803, S32205, S32750, S32760: Özellikle klorür içeren ortamlarda üstün korozyon direnci sağlayan dubleks ve süper dubleks paslanmaz çelik sınıfları.
EN 10216-5: Paslanmaz çelik dikişsiz boruları kapsayan, aşağıdaki kaliteleri içeren Avrupa standardı:
1.4301 / 1.4307 (TP304 / TP304L)
1.4401 / 1.4404 (TP316 / TP316L)
1.4845 (TP310S)
1.4466 (TP310MoLN)
1.4539 (UNS N08904 / 904L)
Paslanmaz çelik borular son derece çok yönlüdür ve ısı eşanjörleri, kazanlar ve kızdırıcılar dahil olmak üzere çok çeşitli uygulamalarda kullanılır. Bu uygulamalarda hem korozyon direnci hem de yüksek sıcaklık dayanımı yalnızca gerekli değildir, aynı zamanda optimum performans için de gereklidir.
V. Kazan ve Isı Eşanjörü için Nikel Esaslı Alaşımlar
Nikel bazlı alaşımlar, mevcut en korozyona dayanıklı malzemeler arasındadır ve aşırı sıcaklıklar, aşındırıcı ortamlar ve yüksek basınç koşulları içeren Kazan ve Isı Eşanjörü uygulamalarında yaygın olarak kullanılır. Nikel alaşımları, oksidasyona, sülfürlenmeye ve karbürleşmeye karşı olağanüstü direnç sağlar ve bu da onları zorlu ortamlardaki ısı eşanjörleri, kazanlar ve aşırı ısıtıcılar için ideal hale getirir.
Nikel Esaslı Alaşımların Özellikleri:
Olağanüstü Korozyon Direnci: Nikel alaşımları asidik, alkali ve klorürlü ortamlarda korozyona karşı direnç gösterir.
Yüksek Sıcaklık Kararlılığı: Nikel alaşımları yüksek sıcaklıklarda bile mukavemetini ve korozyon direncini koruyarak yüksek sıcaklık uygulamaları için uygundur.
Oksidasyon ve Sülfürleşme Direnci: Nikel alaşımları, kükürt içeren bileşiklerin bulunduğu yüksek sıcaklık ortamlarında meydana gelebilen oksidasyon ve sülfürleşmeye karşı dirençlidir.
Ana Standartlar ve Sınıflar:
ASTM B163 / ASTM B407 / ASTM B444: Bu standartlar, kazanlarda, ısı eşanjörlerinde ve süper ısıtıcılarda kullanılan dikişsiz borular için nikel bazlı alaşımları kapsar. Yaygın sınıflar şunları içerir:
Inconel 600 / 601: Oksidasyona ve yüksek sıcaklık korozyonuna karşı mükemmel direnç, bu alaşımları süper ısıtıcılar ve yüksek sıcaklık ısı değiştiricileri için ideal hale getirir.
Inconel 625: Asidik ve klorür açısından zengin ortamlar da dahil olmak üzere çok çeşitli aşındırıcı ortamlara karşı üstün direnç sağlar.
Incoloy 800 / 800H / 800HT: Oksidasyon ve karbürlenmeye karşı mükemmel dirençleri nedeniyle yüksek sıcaklık uygulamalarında kullanılırlar.
Hastelloy C276 / C22: Bu nikel-molibden-krom alaşımları, asidik ve klorür içeren ortamlar da dahil olmak üzere son derece aşındırıcı ortamlardaki olağanüstü korozyon dirençleriyle bilinir.
ASTM B423: Çeşitli ortamlarda gerilim korozyon çatlamasına ve genel korozyona karşı mükemmel direnç sağlayan Alaşım 825 gibi nikel-demir-krom-molibden alaşımlarından yapılmış dikişsiz boruları kapsar.
EN 10216-5: Yüksek sıcaklık ve aşındırıcı uygulamalar için dikişsiz borularda kullanılan nikel bazlı alaşımlar için Avrupa standardı; aşağıdaki kaliteleri içerir:
2.4816 (İnkonel 600)
2.4851 (İnkonel 601)
2.4856 (İnconel625)
2.4858 (Alaşım 825)
Nikel esaslı alaşımlar genellikle korozyon direncinin ve yüksek sıcaklık performansının önemli olduğu enerji santralleri, kimyasal işleme ve petrol ve gaz rafinerileri gibi kritik uygulamalar için seçilir. Kazan ve Isı Eşanjörü.
VI. Kazan ve Isı Eşanjörü için Titanyum ve Zirkonyum Alaşımları
Titanyum ve zirkonyum alaşımları, mukavemet, korozyon direnci ve hafiflik özelliklerinin benzersiz bir kombinasyonunu sunarak, bunları ısı eşanjörleri, kondansatörler ve kazanlardaki özel uygulamalar için ideal hale getirir.
Titanyum Alaşımlarının Özellikleri:
Yüksek Mukavemet-Ağırlık Oranı: Titanyum, çelik kadar güçlüdür ancak önemli ölçüde daha hafiftir, bu da onu ağırlığa duyarlı uygulamalar için uygun hale getirir.
Mükemmel Korozyon Direnci: Titanyum alaşımları deniz suyunda, asidik ortamlarda ve klorür içeren ortamlarda korozyona karşı oldukça dirençlidir.
İyi Isı Direnci: Titanyum alaşımları yüksek sıcaklıklarda mekanik özelliklerini korurlar ve bu da onları enerji santrallerinde ve kimyasal işlemlerde ısı değiştirici boruları için uygun hale getirir.
Zirkonyum Alaşımlarının Özellikleri:
Üstün Korozyon Direnci: Zirkonyum alaşımları, sülfürik asit, nitrik asit ve hidroklorik asit gibi asidik ortamlarda korozyona karşı oldukça dirençlidir.
Yüksek Sıcaklık Kararlılığı: Zirkonyum alaşımları yüksek sıcaklıklarda mukavemetlerini ve korozyon dirençlerini koruyarak yüksek sıcaklıklı ısı değiştirici uygulamaları için idealdir.
Ana Standartlar ve Sınıflar:
ASTM B338: Bu standart, ısı değiştiriciler ve kondansatörlerde kullanılan dikişsiz ve kaynaklı titanyum alaşımlı boruları kapsar. Yaygın sınıflar şunları içerir:
Sınıf 1 / Sınıf 2: Mükemmel korozyon direncine sahip ticari olarak saf titanyum sınıfları.
5. Sınıf (Ti-6Al-4V): Geliştirilmiş mukavemet ve yüksek sıcaklık performansına sahip bir titanyum alaşımı.
ASTM B523: Isı değiştiriciler ve kondansatörlerde kullanım için dikişsiz ve kaynaklı zirkonyum alaşımlı boruları kapsar. Yaygın sınıflar şunları içerir:
Zirkonyum 702: Olağanüstü korozyon direncine sahip, ticari olarak saf bir zirkonyum alaşımıdır.
Zirkonyum 705: Geliştirilmiş mekanik özelliklere ve yüksek sıcaklık kararlılığına sahip alaşımlı bir zirkonyum sınıfıdır.
Titanyum ve zirkonyum alaşımları, üstün korozyon dirençleri ve hafif özellikleri nedeniyle deniz suyu arıtma tesisleri, kimyasal işleme endüstrileri ve nükleer santraller Kazan ve Isı Eşanjörü gibi yüksek korozif ortamlarda yaygın olarak kullanılmaktadır.
VII. Kazan ve Isı Eşanjörü için Bakır ve Bakır Alaşımları
Bakır ve pirinç, bronz ve bakır-nikel gibi alaşımları, mükemmel ısı iletkenliği ve korozyon direnci nedeniyle ısı eşanjörleri, kondansatörler ve kazanlarda yaygın olarak kullanılmaktadır.
Bakır Alaşımlarının Özellikleri:
Mükemmel Isı İletkenliği: Bakır alaşımları yüksek ısı iletkenlikleriyle bilinir ve bu da onları ısı eşanjörleri ve kondansatörler için ideal hale getirir.
Korozyon Direnci: Bakır alaşımları deniz suyu da dahil olmak üzere suda korozyona karşı direnç gösterir ve bu da onları denizcilik ve tuzdan arındırma uygulamaları için uygun hale getirir.
Antimikrobiyal Özellikler: Bakır alaşımları doğal antimikrobiyal özelliklere sahiptir ve bu da onları sağlık hizmetleri ve su arıtma uygulamaları için uygun hale getirir.
Ana Standartlar ve Sınıflar:
ASTM B111: Bu standart, ısı değiştiricilerde, kondansatörlerde ve buharlaştırıcılarda kullanılan dikişsiz bakır ve bakır alaşımlı boruları kapsar. Yaygın sınıflar şunları içerir:
C44300 (Admiralty Brass): Özellikle deniz suyu uygulamalarında iyi korozyon direncine sahip bir bakır-çinko alaşımıdır.
C70600 (Bakır-Nikel 90/10): Deniz suyu ve deniz ortamlarında mükemmel korozyon direncine sahip bir bakır-nikel alaşımıdır.
C71500 (Bakır-Nikel 70/30): Gelişmiş korozyon direnci için daha yüksek nikel içeriğine sahip başka bir bakır-nikel alaşımı.
Bakır ve bakır alaşımları, mükemmel ısı iletkenliği ve deniz suyu korozyonuna karşı direnci nedeniyle deniz kazanı ve ısı eşanjörü uygulamalarında, enerji santrallerinde ve HVAC sistemlerinde yaygın olarak kullanılmaktadır.
Kazan ve ısı değiştiriciye ek olarak, kondansatörler, süper ısıtıcılar, hava ön ısıtıcıları ve ekonomizerler de enerji verimliliğini önemli ölçüde optimize eden hayati bileşenlerdir. Örneğin, kondansatör hem kazandan hem de ısı değiştiriciden gelen egzoz gazlarını soğuturken, süper ısıtıcı ise performansı iyileştirmek için buhar sıcaklığını artırır. Bu arada, hava ön ısıtıcısı gelen havayı ısıtmak için egzoz gazlarını kullanır ve böylece kazan ve ısı değiştirici sisteminin genel verimliliğini daha da artırır. Son olarak, ekonomizerler baca gazlarından atık ısıyı geri kazanarak suyu ön ısıtmak suretiyle önemli bir rol oynar, bu da sonuçta enerji tüketimini azaltır ve hem kazan hem de ısı değiştiricinin verimliliğini artırır.
VIII. Sonuç: Kazan ve Isı Eşanjörü için Doğru Malzemelerin Seçimi
Dikişsiz borular, elektrik üretimi, petrol ve gaz ve kimyasal işleme gibi endüstrilerde kazanların, ısı eşanjörlerinin, kondansatörlerin, aşırı ısıtıcıların, hava ön ısıtıcılarının ve ekonomizerlerin performansının ayrılmaz bir parçasıdır. Dikişsiz borular için malzeme seçimi, sıcaklık, basınç, korozyon direnci ve mekanik mukavemet gibi belirli uygulama gereksinimlerine bağlıdır.
Karbon çeliği Orta sıcaklık ve basınç uygulamaları için uygun fiyat ve dayanıklılık sunar.
Alaşımlı çelik Kazan ve kızdırıcılarda üstün yüksek sıcaklık performansı ve mukavemeti sağlar.
Paslanmaz çelik Isı değiştiricilerde ve kızdırıcılarda mükemmel korozyon direnci ve dayanıklılık sağlar.
Nikel bazlı alaşımlar Aşırı aşındırıcı ve yüksek sıcaklık ortamları için en iyi seçimdir.
Titanyum ve zirkonyum alaşımları Hafif ve yüksek aşındırıcılığa sahip uygulamalar için idealdir.
Bakır ve bakır alaşımları Isı değiştiriciler ve kondenserlerde ısı iletkenliği ve korozyon direnci nedeniyle tercih edilirler.
Kazan ve ısı eşanjörü sistemleri, ısıyı bir ortamdan diğerine verimli bir şekilde aktararak çeşitli endüstrilerde önemli bir rol oynar. Bir kazan ve ısı eşanjörü, ısı üretmek ve aktarmak için birlikte çalışır ve enerji santrallerinde ve üretim süreçlerinde buhar üretimi için gerekli ısıyı sağlar.
Bu malzemelerin özelliklerini ve uygulamalarını anlayarak, mühendisler ve tasarımcılar bilinçli kararlar alabilir ve ekipmanlarının güvenli ve verimli çalışmasını sağlayabilirler. Kazan ve Isı Eşanjörü için malzeme seçerken, uygulamanızın özel gereksinimlerini göz önünde bulundurmak çok önemlidir. Ayrıca, uyumluluğu ve optimum performansı sağlamak için ilgili standartlara başvurmalısınız.