การแนะนำ
ในอุตสาหกรรมต่างๆ เช่น การผลิตไฟฟ้า น้ำมันและก๊าซ ปิโตรเคมี และโรงกลั่น ท่อไร้รอยต่อเป็นส่วนประกอบที่จำเป็น โดยเฉพาะอย่างยิ่งในอุปกรณ์ที่ต้องทนต่ออุณหภูมิที่รุนแรง แรงดันสูง และสภาพแวดล้อมที่กัดกร่อนรุนแรง หม้อไอน้ำ เครื่องแลกเปลี่ยนความร้อน คอนเดนเซอร์ ซูเปอร์ฮีตเตอร์ เครื่องอุ่นอากาศล่วงหน้า และเครื่องประหยัดพลังงานใช้ท่อเหล่านี้ การใช้งานแต่ละประเภทเหล่านี้ต้องการคุณสมบัติของวัสดุเฉพาะเพื่อให้มั่นใจถึงประสิทธิภาพ ความปลอดภัย และอายุการใช้งานที่ยาวนาน การเลือกท่อไร้รอยต่อสำหรับหม้อไอน้ำและเครื่องแลกเปลี่ยนความร้อนขึ้นอยู่กับอุณหภูมิ แรงดัน ความต้านทานการกัดกร่อน และความแข็งแรงเชิงกลที่เฉพาะเจาะจง
คู่มือนี้ให้ข้อมูลเชิงลึกเกี่ยวกับวัสดุต่างๆ ที่ใช้สำหรับท่อไร้รอยต่อ ได้แก่ เหล็กกล้าคาร์บอน เหล็กกล้าผสม เหล็กกล้าไร้สนิม โลหะผสมไททาเนียม โลหะผสมนิกเกิล โลหะผสมทองแดง และโลหะผสมเซอร์โคเนียม นอกจากนี้ เราจะสำรวจมาตรฐานและเกรดที่เกี่ยวข้องด้วย เพื่อช่วยให้คุณตัดสินใจได้ดีขึ้นสำหรับโครงการหม้อไอน้ำและเครื่องแลกเปลี่ยนความร้อนของคุณ
ภาพรวมของ CS, AS, SS, โลหะผสมนิกเกิล, โลหะผสมไททาเนียมและเซอร์โคเนียม, ทองแดงและโลหะผสมทองแดง
1. คุณสมบัติต้านทานการกัดกร่อน
วัสดุแต่ละชนิดที่ใช้ทำท่อไร้รอยต่อจะมีคุณสมบัติต้านทานการกัดกร่อนที่เฉพาะเจาะจง ซึ่งกำหนดความเหมาะสมกับสภาพแวดล้อมที่แตกต่างกัน
เหล็กกล้าคาร์บอน: ทนทานต่อการกัดกร่อนในระดับจำกัด โดยทั่วไปใช้ร่วมกับสารเคลือบหรือวัสดุบุผิวป้องกัน อาจเกิดสนิมได้หากมีน้ำและออกซิเจน เว้นแต่จะได้รับการบำบัด
โลหะผสมเหล็ก: ทนทานต่อการเกิดออกซิเดชันและการกัดกร่อนในระดับปานกลาง ส่วนผสมของโลหะผสม เช่น โครเมียมและโมลิบดีนัม ช่วยเพิ่มความทนทานต่อการกัดกร่อนที่อุณหภูมิสูง
สแตนเลส: ทนทานต่อการกัดกร่อนทั่วไป การแตกร้าวจากการกัดกร่อนจากความเค้น และการเกิดหลุมได้ดีเยี่ยม เนื่องจากมีโครเมียมเป็นส่วนผสม เกรดที่สูงกว่า เช่น 316L มีความทนทานต่อการกัดกร่อนที่เกิดจากคลอไรด์ดีขึ้น
โลหะผสมนิกเกิล: ทนทานต่อสภาพแวดล้อมที่รุนแรง เช่น สภาพแวดล้อมที่มีกรด ด่าง และคลอไรด์สูง การใช้งานที่มีฤทธิ์กัดกร่อนสูงจะใช้โลหะผสม เช่น Inconel 625, Hastelloy C276 และ Alloy 825
ไททาเนียมและเซอร์โคเนียม: ทนทานต่อเกลือทะเลและสารกัดกร่อนอื่นๆ ได้ดีเยี่ยม ไททาเนียมทนทานต่อคลอไรด์และสภาพแวดล้อมที่เป็นกรดเป็นพิเศษ ในขณะที่โลหะผสมเซอร์โคเนียมทนทานต่อสภาพแวดล้อมที่เป็นกรดสูงได้ดีเยี่ยม
ทองแดงและโลหะผสมทองแดง: ทนทานต่อการกัดกร่อนในน้ำจืดและน้ำทะเลได้ดีเยี่ยม โดยโลหะผสมทองแดง-นิกเกิลมีความทนทานเป็นพิเศษในสภาพแวดล้อมทางทะเล
2. สมบัติทางกายภาพและความร้อน
เหล็กกล้าคาร์บอน:
ความหนาแน่น: 7.85 g/cm³
จุดหลอมเหลว: 1,425-1,500°C
การนำความร้อน: ~50 W/m·K
โลหะผสมเหล็ก:
ความหนาแน่น: แตกต่างกันเล็กน้อยตามองค์ประกอบโลหะผสม โดยทั่วไปอยู่ที่ประมาณ 7.85 g/cm³
จุดหลอมเหลว: 1,450-1,530°C
ค่าการนำความร้อน: ต่ำกว่าเหล็กกล้าคาร์บอนเนื่องจากมีธาตุโลหะผสม
สแตนเลส:
ความหนาแน่น: 7.75-8.0 g/cm³
จุดหลอมเหลว: ~1,400-1,530°C
ค่าการนำความร้อน: ~16 W/m·K (ต่ำกว่าเหล็กกล้าคาร์บอน)
โลหะผสมนิกเกิล:
ความหนาแน่น: 8.4-8.9 g/cm³ (ขึ้นอยู่กับโลหะผสม)
จุดหลอมเหลว: 1,300-1,400°C
ค่าการนำความร้อน: โดยทั่วไปต่ำ ~10-16 W/m·K
ไทเทเนียม:
ความหนาแน่น: 4.51 g/cm³
จุดหลอมเหลว: 1,668°C
ค่าการนำความร้อน: ~22 W/m·K (ค่อนข้างต่ำ)
ทองแดง:
ความหนาแน่น: 8.94 g/cm³
จุดหลอมเหลว: 1,084°C
การนำความร้อน: ~390 W/m·K (การนำความร้อนได้ดีเยี่ยม)
3.องค์ประกอบทางเคมี
เหล็กกล้าคาร์บอน: ส่วนใหญ่เป็นเหล็กที่มีคาร์บอน 0.3%-1.2% และแมงกานีส ซิลิกอน และกำมะถันในปริมาณเล็กน้อย
โลหะผสมเหล็ก: ประกอบด้วยองค์ประกอบต่างๆ เช่น โครเมียม โมลิบดีนัม วาเนเดียม และทังสเตน เพื่อปรับปรุงความแข็งแกร่งและทนต่ออุณหภูมิ
สแตนเลส: โดยทั่วไปจะมีโครเมียม 10.5%-30% พร้อมด้วยนิกเกิล โมลิบดีนัม และธาตุอื่นๆ ขึ้นอยู่กับเกรด
โลหะผสมนิกเกิล: ส่วนใหญ่เป็นนิกเกิล (40%-70%) พร้อมด้วยโครเมียม โมลิบดีนัม และธาตุโลหะผสมอื่นๆ เพื่อเพิ่มความทนทานต่อการกัดกร่อน
ไทเทเนียม: เกรด 1 และ 2 เป็นไททาเนียมบริสุทธิ์เชิงพาณิชย์ ในขณะที่เกรด 5 (Ti-6Al-4V) ประกอบด้วยอะลูมิเนียม 6% และวาเนเดียม 4%
โลหะผสมทองแดง: โลหะผสมทองแดงมีธาตุต่างๆ มากมาย เช่น นิกเกิล (10%-30%) ซึ่งมีคุณสมบัติทนทานต่อการกัดกร่อน (เช่น Cu-Ni 90/10)
4. คุณสมบัติทางกล
เหล็กกล้าคาร์บอน: ความแข็งแรงแรงดึง: 400-500 MPa, ความแข็งแรงผลผลิต: 250-350 MPa, การยืดตัว: 15%-25%
โลหะผสมเหล็ก: ความแข็งแรงแรงดึง: 500-900 MPa, ความแข็งแรงผลผลิต: 300-700 MPa, การยืดตัว: 10%-25%
สแตนเลส: ความแข็งแรงแรงดึง: 485-690 MPa (304/316), ความแข็งแรงการยืดหยุ่น: 170-300 MPa, การยืดตัว: 35%-40%
โลหะผสมนิกเกิล: ความแข็งแรงแรงดึง: 550-1,000 MPa (Inconel 625), ความแข็งแรงผลผลิต: 300-600 MPa, การยืดตัว: 25%-50%
ไทเทเนียม: ความแข็งแรงแรงดึง: 240-900 MPa (แตกต่างกันไปตามเกรด) ความแข็งแรงผลผลิต: 170-880 MPa การยืดตัว: 15%-30%
โลหะผสมทองแดง: ความแข็งแรงแรงดึง: 200-500 MPa (ขึ้นอยู่กับโลหะผสม) ความแข็งแรงการยืดตัว: 100-300 MPa การยืดตัว: 20%-35%
5. การอบชุบด้วยความร้อน (เงื่อนไขการส่งมอบ)
เหล็กกล้าคาร์บอนและโลหะผสม: จัดส่งในสภาพอบอ่อนหรือปกติ การอบด้วยความร้อนรวมถึงการชุบแข็งและอบอ่อนเพื่อเพิ่มความแข็งแรงและความเหนียว
สแตนเลส: ส่งมอบในสภาพอบอ่อนเพื่อขจัดความเครียดภายในและปรับปรุงความเหนียว
โลหะผสมนิกเกิล: สารละลายผ่านการอบเพื่อเพิ่มคุณสมบัติเชิงกลและทนต่อการกัดกร่อน
ไททาเนียมและเซอร์โคเนียม: โดยทั่วไปจะส่งมอบในสภาพอบอ่อนเพื่อเพิ่มความเหนียวและความเหนียวสูงสุด
โลหะผสมทองแดง: ส่งมอบในสภาพอบอ่อน โดยเฉพาะสำหรับการใช้งานขึ้นรูป
6. การก่อตัว
เหล็กกล้าคาร์บอนและโลหะผสม: เหล็กอัลลอยด์สามารถขึ้นรูปโดยร้อนหรือเย็นก็ได้ แต่ต้องใช้ความพยายามมากขึ้นเนื่องจากมีความแข็งแรงสูงกว่า
สแตนเลส: การขึ้นรูปเย็นเป็นเรื่องปกติ ถึงแม้ว่าอัตราการชุบแข็งจากการทำงานจะสูงกว่าเหล็กกล้าคาร์บอนก็ตาม
โลหะผสมนิกเกิล: มีความท้าทายในการขึ้นรูปเนื่องจากมีความแข็งแรงสูงและอัตราการแข็งตัวจากการทำงานหนัก มักต้องใช้การขึ้นรูปร้อน
ไทเทเนียม: การขึ้นรูปจะทำได้ดีที่สุดคือที่อุณหภูมิสูงเนื่องจากมีความแข็งแรงสูงที่อุณหภูมิห้อง
โลหะผสมทองแดง: ขึ้นรูปง่ายเนื่องจากมีความเหนียวที่ดี
7. การเชื่อม
เหล็กกล้าคาร์บอนและโลหะผสม: โดยทั่วไปการเชื่อมโดยใช้เทคนิคทั่วไปทำได้ง่าย แต่อาจต้องอุ่นเครื่องก่อนและอบด้วยความร้อนหลังการเชื่อม (PWHT)
สแตนเลส: วิธีการเชื่อมทั่วไป ได้แก่ TIG, MIG และการเชื่อมด้วยอาร์ก จำเป็นต้องควบคุมปริมาณความร้อนอย่างระมัดระวังเพื่อหลีกเลี่ยงการเกิดความไวต่อความร้อน
โลหะผสมนิกเกิล: มีความท้าทายในการเชื่อมเนื่องจากการขยายตัวเนื่องจากความร้อนสูงและเสี่ยงต่อการแตกร้าว
ไทเทเนียม: เชื่อมในสภาพแวดล้อมที่มีการป้องกัน (ก๊าซเฉื่อย) เพื่อหลีกเลี่ยงการปนเปื้อน ต้องใช้ความระมัดระวังเนื่องจากไททาเนียมมีปฏิกิริยาที่อุณหภูมิสูง
โลหะผสมทองแดง: เชื่อมได้ง่าย โดยเฉพาะโลหะผสมทองแดง-นิกเกิล แต่ต้องอุ่นเครื่องก่อนเพื่อป้องกันการแตกร้าว
8. การกัดกร่อนของรอยเชื่อม
สแตนเลส: อาจเกิดการกัดกร่อนเฉพาะที่ (เช่น การกัดกร่อนแบบหลุม การกัดกร่อนตามรอยแยก) บริเวณที่ได้รับผลกระทบจากความร้อนในการเชื่อม หากไม่ได้รับการควบคุมอย่างเหมาะสม
โลหะผสมนิกเกิล: ไวต่อการเกิดรอยแตกร้าวจากการกัดกร่อนหากสัมผัสกับคลอไรด์ที่อุณหภูมิสูง
ไทเทเนียม: รอยเชื่อมจะต้องได้รับการป้องกันจากออกซิเจนอย่างเหมาะสมเพื่อหลีกเลี่ยงการเปราะบาง
9. การขจัดตะกรัน การดอง และการทำความสะอาด
เหล็กกล้าคาร์บอนและโลหะผสม: การดองช่วยขจัดออกไซด์บนพื้นผิวหลังการอบด้วยความร้อน กรดทั่วไปได้แก่ กรดไฮโดรคลอริกและกรดซัลฟิวริก
สแตนเลสและโลหะผสมนิกเกิล: การดองด้วยกรดไนตริก/ไฮโดรฟลูออริกใช้เพื่อขจัดสีที่เกิดจากความร้อนและฟื้นฟูความทนทานต่อการกัดกร่อนหลังการเชื่อม
ไทเทเนียม: ใช้สารละลายกรดอ่อนในการดองเพื่อทำความสะอาดพื้นผิวและขจัดออกไซด์โดยไม่ทำลายโลหะ
โลหะผสมทองแดง: การทำความสะอาดด้วยกรดใช้เพื่อขจัดคราบหมองและออกไซด์บนพื้นผิว
10. กระบวนการพื้นผิว (AP, BA, MP, EP ฯลฯ)
AP (อบและดอง): การเคลือบผิวมาตรฐานสำหรับโลหะผสมสแตนเลสและนิเกิลส่วนใหญ่หลังการอบอ่อนและการดอง
BA (อบอ่อน) : ทำได้โดยการอบในบรรยากาศควบคุมเพื่อสร้างพื้นผิวเรียบและสะท้อนแสง
MP (ขัดเงาด้วยกลไก): การขัดด้วยเครื่องจักรช่วยปรับปรุงความเรียบของพื้นผิว ลดความเสี่ยงต่อการปนเปื้อนและการกัดกร่อน
EP (ขัดเงาด้วยไฟฟ้า): กระบวนการทางไฟฟ้าเคมีที่ขจัดวัสดุพื้นผิวเพื่อสร้างความเรียบเนียนเป็นพิเศษ ลดความหยาบของพื้นผิวและปรับปรุงความทนทานต่อการกัดกร่อน
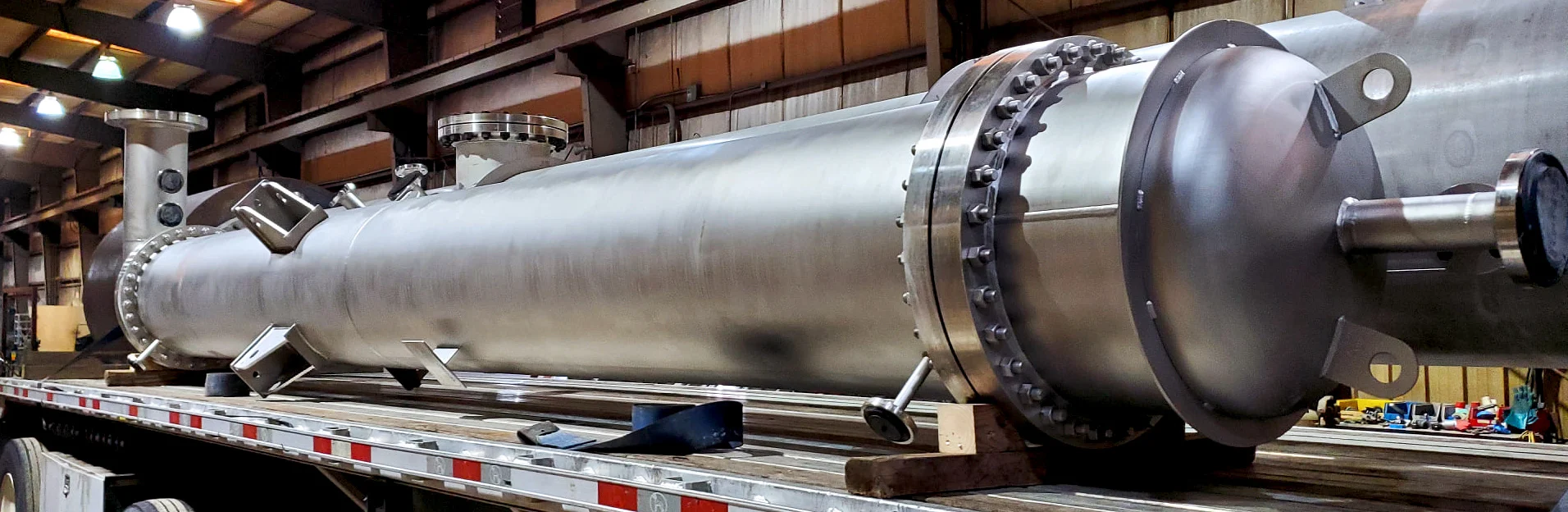
เครื่องแลกเปลี่ยนความร้อนสแตนเลส
I. ทำความเข้าใจท่อไร้รอยต่อ
ท่อไร้รอยต่อแตกต่างจากท่อเชื่อมตรงที่ท่อไร้รอยต่อไม่มีรอยต่อเชื่อม ซึ่งอาจเป็นจุดอ่อนในการใช้งานแรงดันสูงบางประเภท ท่อไร้รอยต่อขึ้นรูปจากแท่งเหล็กแข็งก่อน จากนั้นจึงให้ความร้อน จากนั้นจึงอัดขึ้นรูปหรือดึงผ่านแกนหมุนเพื่อสร้างรูปร่างท่อ การไม่มีรอยต่อทำให้ท่อมีความแข็งแรงและเชื่อถือได้เหนือกว่า จึงเหมาะอย่างยิ่งสำหรับสภาพแวดล้อมที่มีแรงดันสูงและอุณหภูมิสูง
การใช้งานทั่วไป:
หม้อไอน้ำ: ท่อไร้รอยต่อมีความจำเป็นในการสร้างหม้อไอน้ำแบบท่อน้ำและแบบท่อไฟที่มีอุณหภูมิและแรงดันสูง
เครื่องแลกเปลี่ยนความร้อน: ท่อไร้รอยต่อในเครื่องแลกเปลี่ยนความร้อนซึ่งใช้เพื่อถ่ายเทความร้อนระหว่างของไหลสองชนิด จะต้องทนทานต่อการกัดกร่อนและรักษาประสิทธิภาพความร้อนได้
คอนเดนเซอร์: ท่อไร้รอยต่อช่วยควบแน่นไอน้ำให้เป็นน้ำในระบบผลิตไฟฟ้าและระบบทำความเย็น
ซุปเปอร์ฮีตเตอร์: ท่อไร้รอยต่อใช้สำหรับเพิ่มความร้อนไอน้ำในหม้อไอน้ำ ช่วยเพิ่มประสิทธิภาพของกังหันในโรงไฟฟ้า
เครื่องอุ่นอากาศ: ท่อเหล่านี้ถ่ายเทความร้อนจากก๊าซไอเสียไปยังอากาศ ช่วยปรับปรุงประสิทธิภาพของหม้อไอน้ำ
นักเศรษฐศาสตร์: ท่อไร้รอยต่อในอีโคโนไมเซอร์จะอุ่นน้ำป้อนล่วงหน้าโดยใช้ความร้อนเหลือทิ้งจากไอเสียหม้อไอน้ำ ช่วยเพิ่มประสิทธิภาพเชิงความร้อน
หม้อไอน้ำ เครื่องแลกเปลี่ยนความร้อน คอนเดนเซอร์ เครื่องทำความร้อนสูง เครื่องอุ่นอากาศล่วงหน้า และเครื่องประหยัดพลังงานเป็นส่วนประกอบที่สำคัญในหลายอุตสาหกรรม โดยเฉพาะอุตสาหกรรมที่เกี่ยวข้องกับการถ่ายเทความร้อน การผลิตพลังงาน และการจัดการของไหล โดยเฉพาะอย่างยิ่ง ส่วนประกอบเหล่านี้มีการใช้งานหลักในอุตสาหกรรมต่อไปนี้:
1. อุตสาหกรรมการผลิตไฟฟ้า
หม้อไอน้ำ: ใช้ในโรงไฟฟ้าเพื่อแปลงพลังงานเคมีให้เป็นพลังงานความร้อน มักใช้เพื่อการผลิตไอน้ำ
เครื่องทำความร้อนสูง เครื่องประหยัดพลังงาน และเครื่องอุ่นอากาศล่วงหน้า ส่วนประกอบเหล่านี้ช่วยเพิ่มประสิทธิภาพด้วยการอุ่นอากาศที่เกิดจากการเผาไหม้ล่วงหน้า กู้คืนความร้อนจากก๊าซไอเสีย และให้ความร้อนไอน้ำเพิ่มเติม
เครื่องแลกเปลี่ยนความร้อนและคอนเดนเซอร์: ใช้ในการระบายความร้อนและการกู้คืนความร้อนในโรงไฟฟ้าพลังความร้อน โดยเฉพาะในกังหันไอน้ำและรอบการระบายความร้อน
2. อุตสาหกรรมน้ำมันและก๊าซ
เครื่องแลกเปลี่ยนความร้อน: มีความสำคัญในกระบวนการกลั่น ซึ่งความร้อนจะถูกถ่ายเทระหว่างของเหลว เช่น ในการกลั่นน้ำมันดิบหรือในแพลตฟอร์มนอกชายฝั่งสำหรับการแปรรูปก๊าซ
หม้อไอน้ำและเครื่องประหยัดพลังงาน: พบในโรงกลั่นและโรงงานปิโตรเคมีสำหรับการผลิตไอน้ำและการกู้คืนพลังงาน
คอนเดนเซอร์: ใช้ในการควบแน่นก๊าซให้เป็นของเหลวในระหว่างกระบวนการกลั่น
3. อุตสาหกรรมเคมี
เครื่องแลกเปลี่ยนความร้อน: ใช้กันอย่างแพร่หลายในการให้ความร้อนหรือความเย็นปฏิกิริยาทางเคมี และเพื่อกู้คืนความร้อนจากปฏิกิริยาคายความร้อน
หม้อไอน้ำและเครื่องทำความร้อนสูงพิเศษ: ใช้ในการผลิตไอน้ำที่จำเป็นสำหรับกระบวนการทางเคมีต่างๆ และเพื่อให้พลังงานสำหรับการกลั่นและขั้นตอนการเกิดปฏิกิริยา
เครื่องอุ่นอากาศล่วงหน้าและเครื่องประหยัดพลังงาน: ปรับปรุงประสิทธิภาพในกระบวนการเคมีที่ใช้พลังงานมากด้วยการกู้คืนความร้อนจากก๊าซไอเสียและลดการใช้เชื้อเพลิง
4. อุตสาหกรรมทางทะเล
หม้อไอน้ำและเครื่องแลกเปลี่ยนความร้อน: จำเป็นสำหรับเรือเดินทะเลสำหรับระบบผลิตไอน้ำ ระบบทำความร้อน และทำความเย็น เครื่องแลกเปลี่ยนความร้อนสำหรับเรือมักใช้เพื่อระบายความร้อนเครื่องยนต์ของเรือและสร้างพลังงาน
คอนเดนเซอร์: ใช้ในการแปลงไอน้ำเสียกลับเป็นน้ำเพื่อนำกลับมาใช้ใหม่ในระบบหม้อไอน้ำของเรือ
5. อุตสาหกรรมอาหารและเครื่องดื่ม
เครื่องแลกเปลี่ยนความร้อน: มักใช้สำหรับกระบวนการพาสเจอร์ไรเซชัน การฆ่าเชื้อ และกระบวนการระเหย
หม้อไอน้ำและเครื่องประหยัดพลังงาน: ใช้ในการผลิตไอน้ำสำหรับการดำเนินการแปรรูปอาหารและเพื่อกู้คืนความร้อนจากไอเสียเพื่อประหยัดการใช้เชื้อเพลิง
6. ระบบ HVAC (ระบบทำความร้อน ระบายอากาศ และปรับอากาศ)
เครื่องแลกเปลี่ยนความร้อนและเครื่องอุ่นอากาศล่วงหน้า: ใช้ในระบบ HVAC เพื่อการถ่ายเทความร้อนอย่างมีประสิทธิภาพระหว่างของเหลวหรือก๊าซ ให้ความร้อนหรือความเย็นแก่อาคารและโรงงานอุตสาหกรรม
คอนเดนเซอร์: ใช้ในระบบปรับอากาศเพื่อระบายความร้อนจากสารทำความเย็น
7. อุตสาหกรรมเยื่อและกระดาษ
หม้อไอน้ำ เครื่องแลกเปลี่ยนความร้อน และเครื่องประหยัดพลังงาน: ให้การกู้คืนไอน้ำและความร้อนในกระบวนการต่างๆ เช่น การผลิตเยื่อกระดาษ การอบแห้งกระดาษ และการกู้คืนสารเคมี
ซุปเปอร์ฮีตเตอร์และเครื่องอุ่นอากาศล่วงหน้า: เพิ่มประสิทธิภาพการใช้พลังงานในหม้อไอน้ำกู้คืนและสมดุลความร้อนโดยรวมของโรงงานกระดาษ
8. อุตสาหกรรมโลหะและเหล็กกล้า
เครื่องแลกเปลี่ยนความร้อน: ใช้ในการระบายความร้อนก๊าซและของเหลวร้อนในการผลิตเหล็กและกระบวนการทางโลหะวิทยา
หม้อไอน้ำและเครื่องประหยัดพลังงาน: ให้ความร้อนสำหรับกระบวนการต่างๆ เช่น การทำงานของเตาเผา การอบชุบด้วยความร้อน และการรีด
9. อุตสาหกรรมยา
เครื่องแลกเปลี่ยนความร้อน: ใช้ในการควบคุมอุณหภูมิในระหว่างการผลิตยา กระบวนการหมัก และสภาพแวดล้อมที่ปราศจากเชื้อ
หม้อไอน้ำ: สร้างไอน้ำที่จำเป็นสำหรับการฆ่าเชื้อและให้ความร้อนกับอุปกรณ์เภสัชกรรม
10. โรงงานแปรรูปขยะเป็นพลังงาน
หม้อไอน้ำ คอนเดนเซอร์ และเครื่องประหยัดพลังงาน ใช้ในการแปลงขยะให้เป็นพลังงานผ่านการเผาไหม้ พร้อมทั้งนำความร้อนกลับคืนมาเพื่อเพิ่มประสิทธิภาพ
ตอนนี้เรามาดูวัสดุต่างๆ ที่ใช้ทำท่อไร้รอยต่อที่เหมาะกับการใช้งานที่ต้องการความแม่นยำสูงเหล่านี้กัน
II. ท่อเหล็กกล้าคาร์บอนสำหรับหม้อไอน้ำและเครื่องแลกเปลี่ยนความร้อน
เหล็กกล้าคาร์บอนเป็นวัสดุที่ใช้กันอย่างแพร่หลายที่สุดชนิดหนึ่งสำหรับท่อไร้รอยต่อในงานอุตสาหกรรม เนื่องมาจากมีความแข็งแรงเป็นเลิศ รวมถึงราคาที่จับต้องได้และหาซื้อได้ง่าย ท่อเหล็กกล้าคาร์บอนมีความทนทานต่ออุณหภูมิและแรงดันปานกลาง จึงเหมาะสำหรับการใช้งานที่หลากหลาย
คุณสมบัติของเหล็กกล้าคาร์บอน:
ความแข็งแรงสูง: ท่อเหล็กกล้าคาร์บอนสามารถทนต่อแรงกดดันและความเครียดได้มาก จึงเหมาะอย่างยิ่งสำหรับการใช้งานในหม้อไอน้ำและเครื่องแลกเปลี่ยนความร้อน
คุ้มต้นทุน: เมื่อเทียบกับวัสดุอื่นๆ เหล็กกล้าคาร์บอนมีราคาค่อนข้างถูก ซึ่งทำให้เหล็กกล้าคาร์บอนเป็นตัวเลือกยอดนิยมในการใช้งานอุตสาหกรรมขนาดใหญ่
ความต้านทานการกัดกร่อนปานกลาง: แม้ว่าเหล็กกล้าคาร์บอนจะไม่ทนต่อการกัดกร่อนเท่ากับสแตนเลส แต่ก็สามารถเคลือบหรือบุผิวเพื่อเพิ่มอายุการใช้งานในสภาพแวดล้อมที่กัดกร่อนได้
มาตรฐานหลักและเกรด:
มาตรฐาน ASTM A179มาตรฐานนี้ครอบคลุมถึงท่อเหล็กกล้าคาร์บอนต่ำดึงเย็นแบบไร้รอยต่อที่ใช้สำหรับการแลกเปลี่ยนความร้อนและคอนเดนเซอร์ ท่อเหล่านี้มีคุณสมบัติในการถ่ายเทความร้อนได้ดีเยี่ยมและมักใช้ในงานที่มีอุณหภูมิและแรงดันต่ำถึงปานกลาง
มาตรฐาน ASTM A192:ท่อหม้อน้ำเหล็กกล้าคาร์บอนไร้รอยต่อที่ออกแบบมาสำหรับการใช้งานแรงดันสูง ท่อเหล่านี้ใช้ในการผลิตไอน้ำและสภาพแวดล้อมที่มีแรงดันสูงอื่นๆ
มาตรฐาน ASTM A210:มาตรฐานนี้ครอบคลุมถึงท่อเหล็กกล้าคาร์บอนปานกลางแบบไร้รอยต่อสำหรับหม้อไอน้ำและการใช้งานเครื่องทำความร้อนสูงพิเศษ เกรด A-1 และ C มีระดับความแข็งแรงและทนต่ออุณหภูมิที่แตกต่างกัน
เอเอสทีเอ334 (เกรด 1, 3, 6): ท่อเหล็กกล้าคาร์บอนไร้รอยต่อและเชื่อมที่ออกแบบมาสำหรับการใช้งานที่อุณหภูมิต่ำ เกรดเหล่านี้ใช้ในเครื่องแลกเปลี่ยนความร้อน คอนเดนเซอร์ และการใช้งานที่อุณหภูมิต่ำอื่นๆ
เอ็น 10216-2 (P235GH, P265GH TC1/TC2): มาตรฐานยุโรปสำหรับท่อเหล็กไร้รอยต่อที่ใช้ในงานแรงดัน โดยเฉพาะในหม้อไอน้ำและบริการที่อุณหภูมิสูง
ท่อเหล็กกล้าคาร์บอนเป็นตัวเลือกที่ยอดเยี่ยมสำหรับการใช้งานในหม้อไอน้ำและเครื่องแลกเปลี่ยนความร้อนซึ่งต้องมีความแข็งแรงสูงและทนต่อการกัดกร่อนในระดับปานกลาง อย่างไรก็ตาม สำหรับการใช้งานที่เกี่ยวข้องกับอุณหภูมิที่สูงมากเท่านั้น แต่ยังรวมถึงสภาพแวดล้อมที่กัดกร่อนรุนแรงด้วย ท่อโลหะผสมหรือสแตนเลสมักได้รับความนิยมเนื่องจากมีความทนทานและความทนทานเหนือกว่า
III. ท่อเหล็กอัลลอยด์สำหรับหม้อไอน้ำและเครื่องแลกเปลี่ยนความร้อน
ท่อเหล็กอัลลอยด์ได้รับการออกแบบมาสำหรับการใช้งานในหม้อไอน้ำและตัวแลกเปลี่ยนความร้อนที่อุณหภูมิสูงและแรงดันสูง ท่อเหล่านี้ผสมโลหะผสมกับธาตุต่างๆ เช่น โครเมียม โมลิบดีนัม และวาเนเดียม เพื่อเพิ่มความแข็งแรง ความแข็ง และความต้านทานต่อการกัดกร่อนและความร้อน ท่อเหล็กอัลลอยด์ใช้กันอย่างแพร่หลายในแอปพลิเคชันที่สำคัญ เช่น เครื่องทำความร้อนสูงเกิน เครื่องประหยัดพลังงาน และตัวแลกเปลี่ยนความร้อนอุณหภูมิสูง เนื่องจากมีความแข็งแรงและทนต่อความร้อนและแรงดันได้ดีเยี่ยม
คุณสมบัติของเหล็กอัลลอยด์:
ทนความร้อนสูง: ธาตุโลหะผสม เช่น โครเมียมและโมลิบดีนัม ช่วยปรับปรุงประสิทธิภาพที่อุณหภูมิสูงของท่อเหล่านี้ ทำให้เหมาะสำหรับการใช้งานในอุณหภูมิที่รุนแรง
ความต้านทานการกัดกร่อนที่ได้รับการปรับปรุง: ท่อเหล็กกล้าโลหะผสมมีความทนทานต่อการเกิดออกซิเดชันและการกัดกร่อนได้ดีกว่าเมื่อเทียบกับเหล็กกล้าคาร์บอน โดยเฉพาะอย่างยิ่งในสภาพแวดล้อมที่มีอุณหภูมิสูง
ความแข็งแกร่งที่เพิ่มขึ้น: ธาตุโลหะผสมยังช่วยเพิ่มความแข็งแกร่งของท่อเหล่านี้ ทำให้สามารถทนต่อแรงดันสูงในหม้อไอน้ำและอุปกรณ์สำคัญอื่นๆ ได้
มาตรฐานหลักและเกรด:
เอ เอส ที เอ 213 (เกรด T5, T9, T11, T22, T91, T92): มาตรฐานนี้ครอบคลุมถึงท่อเหล็กอัลลอยด์เฟอร์ริติกและออสเทนนิติกแบบไร้รอยต่อสำหรับใช้ในหม้อไอน้ำ เครื่องทำความร้อนสูงพิเศษ และเครื่องแลกเปลี่ยนความร้อน เกรดต่างๆ แตกต่างกันในส่วนผสมของโลหะผสม และจะถูกเลือกตามข้อกำหนดด้านอุณหภูมิและแรงดันที่เฉพาะเจาะจง
T5 และ T9: เหมาะสำหรับการใช้งานที่อุณหภูมิปานกลางถึงสูง
T11 และ T22: มักใช้ในงานที่อุณหภูมิสูง ช่วยให้ทนความร้อนได้ดีขึ้น
T91 และ T92: โลหะผสมที่มีความแข็งแรงสูงขั้นสูงที่ออกแบบมาเพื่อการใช้งานที่อุณหภูมิสูงพิเศษในโรงไฟฟ้า
เอ็น 10216-2 (16Mo3, 13CrMo4-5, 10CrMo9-10, 15NiCuMoNb5-6-4, X20CrMoV11-1): มาตรฐานยุโรปสำหรับท่อเหล็กกล้าอัลลอยด์ไร้รอยต่อที่ใช้ในงานอุณหภูมิสูง ท่อเหล่านี้มักใช้ในหม้อไอน้ำ เครื่องทำความร้อนสูง และเครื่องประหยัดพลังงานในโรงไฟฟ้า
16Mo3: เหล็กกล้าอัลลอยด์ที่มีคุณสมบัติทนอุณหภูมิสูงได้ดี เหมาะสำหรับใช้ในหม้อไอน้ำและภาชนะรับแรงดัน
13CrMo4-5 และ 10CrMo9-10: โลหะผสมโครเมียม-โมลิบดีนัมที่ทนความร้อนและการกัดกร่อนได้ดีเยี่ยมสำหรับการใช้งานที่อุณหภูมิสูง
ท่อเหล็กกล้าอัลลอยด์เป็นตัวเลือกสำหรับสภาพแวดล้อมที่มีอุณหภูมิสูงและแรงดันสูง ซึ่งเหล็กกล้าคาร์บอนอาจไม่สามารถให้ประสิทธิภาพเพียงพอสำหรับหม้อไอน้ำและเครื่องแลกเปลี่ยนความร้อนได้
IV. ท่อสแตนเลสสำหรับหม้อไอน้ำและเครื่องแลกเปลี่ยนความร้อน
ท่อสแตนเลสมีความทนทานต่อการกัดกร่อนเป็นพิเศษ จึงเหมาะอย่างยิ่งสำหรับการใช้งานในหม้อไอน้ำและเครื่องแลกเปลี่ยนความร้อนที่เกี่ยวข้องกับของเหลวที่กัดกร่อน อุณหภูมิสูง และสภาพแวดล้อมที่รุนแรง ท่อสแตนเลสใช้กันอย่างแพร่หลายในเครื่องแลกเปลี่ยนความร้อน เครื่องทำความร้อนสูง และหม้อไอน้ำ ซึ่งนอกจากจะทนทานต่อการกัดกร่อนแล้ว ยังต้องมีความแข็งแรงที่อุณหภูมิสูงเพื่อประสิทธิภาพการทำงานที่เหมาะสมที่สุดอีกด้วย
คุณสมบัติของสแตนเลส:
ความต้านทานการกัดกร่อน: ความต้านทานการกัดกร่อนของสแตนเลสมาจากส่วนผสมของโครเมียมซึ่งสร้างชั้นออกไซด์ป้องกันบนพื้นผิว
ความแข็งแรงสูงที่อุณหภูมิสูง: สแตนเลสยังคงคุณสมบัติเชิงกลแม้ในอุณหภูมิสูง จึงเหมาะสำหรับเครื่องทำความร้อนสูงเกินและการใช้งานที่ต้องใช้ความร้อนสูงอื่นๆ
ความทนทานในระยะยาว: ความทนทานต่อการกัดกร่อนและออกซิเดชันของสแตนเลสช่วยให้มีอายุการใช้งานยาวนานแม้จะอยู่ในสภาพแวดล้อมที่รุนแรง
มาตรฐานหลักและเกรด:
เอ เอส ที เอ 213 / เอ เอส ที เอ็ม 249:มาตรฐานเหล่านี้ครอบคลุมถึงท่อเหล็กกล้าไร้สนิมแบบไร้รอยต่อและแบบเชื่อมสำหรับใช้ในหม้อไอน้ำ ซูเปอร์ฮีตเตอร์ และเครื่องแลกเปลี่ยนความร้อน เกรดทั่วไป ได้แก่:
TP304 / TP304L (EN 1.4301 / 1.4307): เกรดสแตนเลสออสเทนนิติกถูกนำมาใช้กันอย่างแพร่หลายเนื่องจากมีความทนทานต่อการกัดกร่อนและมีความแข็งแรง
TP310S / TP310MoLN (EN 1.4845 / 1.4466): เกรดสแตนเลสที่ทนทานต่ออุณหภูมิสูงพร้อมความทนทานต่อการเกิดออกซิเดชันที่ยอดเยี่ยม
TP316 / TP316L (EN 1.4401 / 1.4404): เกรดที่มีโมลิบดีนัมซึ่งมีความทนทานต่อการกัดกร่อนที่ดีขึ้น โดยเฉพาะในสภาพแวดล้อมที่มีคลอไรด์
TP321 (EN 1.4541): เกรดสแตนเลสที่มีเสถียรภาพซึ่งใช้ในสภาพแวดล้อมอุณหภูมิสูงเพื่อป้องกันการกัดกร่อนตามขอบเกรน
TP347H / TP347HFG (EN 1.4550 / 1.4961): เกรดคาร์บอนสูงที่เสถียรสำหรับการใช้งานที่อุณหภูมิสูง เช่น ซุปเปอร์ฮีตเตอร์และหม้อไอน้ำ
UNS N08904 (904L) (EN 1.4539): เหล็กกล้าไร้สนิมออสเทนนิติกระดับสูงที่มีความทนทานต่อการกัดกร่อนได้ดีเยี่ยม โดยเฉพาะในสภาพแวดล้อมที่มีกรด
เอ เอส ที เอ 269:ครอบคลุมท่อสแตนเลสออสเทนนิติกแบบเชื่อมและไร้รอยต่อสำหรับการใช้งานที่ทนต่อการกัดกร่อนทั่วไป
เอเอสทีเอ 789:มาตรฐานสำหรับท่อเหล็กกล้าไร้สนิมดูเพล็กซ์ ที่ให้ความทนทานต่อการกัดกร่อนที่ยอดเยี่ยมและความแข็งแรงสูง
UNS S31803, S32205, S32750, S32760: เกรดสแตนเลสดูเพล็กซ์และซูเปอร์ดูเพล็กซ์ ที่ให้ความทนทานต่อการกัดกร่อนที่เหนือกว่า โดยเฉพาะในสภาพแวดล้อมที่มีคลอไรด์
เอ็น 10216-5:มาตรฐานยุโรปครอบคลุมท่อสแตนเลสไร้รอยต่อ รวมถึงเกรดต่อไปนี้:
1.4301 / 1.4307 (ทีพี304 / ทีพี304แอล)
1.4401 / 1.4404 (ทีพี316 / ทีพี316แอล)
1.4845 (ทีพี310เอส)
1.4466 (ทีพี310โมลเอ็น)
1.4539 (หมายเลข UNN08904/904L)
ท่อสแตนเลสมีความอเนกประสงค์สูงและใช้ในแอปพลิเคชันต่างๆ มากมาย รวมถึงเครื่องแลกเปลี่ยนความร้อน หม้อไอน้ำ และเครื่องทำความร้อนสูงพิเศษ ซึ่งไม่เพียงแต่ต้องมีความทนทานต่อการกัดกร่อนและแข็งแรงต่ออุณหภูมิสูง แต่ยังจำเป็นต่อประสิทธิภาพการทำงานที่เหมาะสมที่สุดอีกด้วย
V. โลหะผสมนิกเกิลสำหรับหม้อไอน้ำและเครื่องแลกเปลี่ยนความร้อน
โลหะผสมนิกเกิลเป็นวัสดุที่ทนต่อการกัดกร่อนได้ดีที่สุดชนิดหนึ่ง และมักใช้ในหม้อไอน้ำและเครื่องแลกเปลี่ยนความร้อนที่ต้องเผชิญกับอุณหภูมิที่รุนแรง สภาพแวดล้อมที่กัดกร่อน และสภาวะแรงดันสูง โลหะผสมนิกเกิลมีความทนทานต่อการเกิดออกซิเดชัน ซัลไฟด์ และคาร์บูไรเซชันได้ดีเยี่ยม จึงเหมาะอย่างยิ่งสำหรับเครื่องแลกเปลี่ยนความร้อน หม้อไอน้ำ และเครื่องทำความร้อนสูงพิเศษในสภาพแวดล้อมที่รุนแรง
สมบัติของโลหะผสมนิกเกิล:
ความต้านทานการกัดกร่อนที่ยอดเยี่ยม: โลหะผสมนิกเกิลทนทานต่อการกัดกร่อนในสภาพแวดล้อมที่เป็นกรด ด่าง และคลอไรด์
เสถียรภาพในอุณหภูมิสูง: โลหะผสมนิกเกิลยังคงความแข็งแกร่งและทนต่อการกัดกร่อนแม้ในอุณหภูมิที่สูง ทำให้เหมาะสำหรับการใช้งานที่อุณหภูมิสูง
ความต้านทานต่อการเกิดออกซิเดชันและซัลไฟด์: โลหะผสมนิกเกิลมีความทนทานต่อการเกิดออกซิเดชันและซัลไฟด์ ซึ่งอาจเกิดขึ้นในสภาพแวดล้อมอุณหภูมิสูงที่เกี่ยวข้องกับสารประกอบที่มีกำมะถัน
มาตรฐานหลักและเกรด:
เอสทีเอ็ม บี 163 / แอสทาม B407 / แอสทาม B444:มาตรฐานเหล่านี้ครอบคลุมถึงโลหะผสมนิกเกิลสำหรับท่อไร้รอยต่อที่ใช้ในหม้อไอน้ำ เครื่องแลกเปลี่ยนความร้อน และเครื่องทำความร้อนสูงพิเศษ เกรดทั่วไป ได้แก่:
Inconel 600/601: ทนทานต่อการเกิดออกซิเดชันและการกัดกร่อนที่อุณหภูมิสูงได้ดีเยี่ยม ทำให้โลหะผสมเหล่านี้เหมาะอย่างยิ่งสำหรับเครื่องทำความร้อนสูงเกินและเครื่องแลกเปลี่ยนความร้อนอุณหภูมิสูง
Inconel 625: มีความทนทานต่อสภาวะกัดกร่อนต่างๆ ได้ดีเยี่ยม รวมถึงสภาวะที่เป็นกรดและมีคลอไรด์สูง
Incoloy 800 / 800H / 800HT: ใช้ในงานที่อุณหภูมิสูงเนื่องจากมีความทนทานต่อการเกิดออกซิเดชันและคาร์บูไรเซชันได้ดีเยี่ยม
Hastelloy C276 / C22: โลหะผสมนิกเกิล-โมลิบดีนัม-โครเมียมเหล่านี้ขึ้นชื่อในเรื่องความทนทานต่อการกัดกร่อนที่โดดเด่นในสภาพแวดล้อมที่มีฤทธิ์กัดกร่อนสูง รวมถึงสื่อที่มีกรดและคลอไรด์
แอสทาม B423:ครอบคลุมท่อไร้รอยต่อที่ทำจากโลหะผสมนิกเกิล-เหล็ก-โครเมียม-โมลิบดีนัม เช่น โลหะผสม 825 ซึ่งมีคุณสมบัติทนทานต่อการแตกร้าวจากการกัดกร่อนภายใต้ความเค้น และการกัดกร่อนทั่วไปในสภาพแวดล้อมต่างๆ ได้ดีเยี่ยม
EN 10216-5: มาตรฐานยุโรปสำหรับโลหะผสมนิกเกิลที่ใช้ในท่อไร้รอยต่อสำหรับการใช้งานที่อุณหภูมิสูงและกัดกร่อน รวมถึงเกรดต่างๆ เช่น:
2.4816 (อินโคเนล 600)
2.4851 (อินโคเนล 601)
2.4856 (อินโคเนล 625)
2.4858 (โลหะผสม 825)
โลหะผสมนิกเกิลมักถูกเลือกใช้สำหรับการใช้งานที่สำคัญซึ่งต้องทนต่อการกัดกร่อนและทนต่ออุณหภูมิสูง เช่น ในโรงไฟฟ้า การแปรรูปทางเคมี โรงกลั่นน้ำมันและก๊าซ หม้อไอน้ำและเครื่องแลกเปลี่ยนความร้อน
VI. โลหะผสมไททาเนียมและเซอร์โคเนียมสำหรับหม้อไอน้ำและเครื่องแลกเปลี่ยนความร้อน
โลหะผสมไททาเนียมและเซอร์โคเนียมมีคุณสมบัติที่เป็นเอกลักษณ์เฉพาะตัวในด้านความแข็งแกร่ง ทนทานต่อการกัดกร่อน และน้ำหนักเบา จึงเหมาะอย่างยิ่งสำหรับการใช้งานเฉพาะในเครื่องแลกเปลี่ยนความร้อน คอนเดนเซอร์ และหม้อไอน้ำ
คุณสมบัติของโลหะผสมไททาเนียม:
อัตราส่วนความแข็งแรงต่อน้ำหนักสูง: ไททาเนียมมีความแข็งแกร่งเท่ากับเหล็กแต่เบากว่าอย่างเห็นได้ชัด จึงเหมาะสำหรับการใช้งานที่คำนึงถึงน้ำหนัก
ทนทานต่อการกัดกร่อนได้ดีเยี่ยม: โลหะผสมไททาเนียมทนทานต่อการกัดกร่อนในน้ำทะเล สภาพแวดล้อมที่มีกรด และสื่อที่มีคลอไรด์สูง
ทนความร้อนได้ดี: โลหะผสมไททาเนียมยังคงคุณสมบัติเชิงกลที่อุณหภูมิสูง ทำให้เหมาะสำหรับท่อแลกเปลี่ยนความร้อนในโรงไฟฟ้าและการแปรรูปทางเคมี
คุณสมบัติของโลหะผสมเซอร์โคเนียม:
ความต้านทานการกัดกร่อนที่โดดเด่น: โลหะผสมเซอร์โคเนียมมีความทนทานต่อการกัดกร่อนในสภาพแวดล้อมที่มีกรดสูง รวมถึงกรดซัลฟิวริก กรดไนตริก และกรดไฮโดรคลอริก
เสถียรภาพที่อุณหภูมิสูง: โลหะผสมเซอร์โคเนียมยังคงความแข็งแกร่งและทนต่อการกัดกร่อนที่อุณหภูมิสูง ทำให้เหมาะอย่างยิ่งสำหรับการใช้งานเครื่องแลกเปลี่ยนความร้อนอุณหภูมิสูง
มาตรฐานหลักและเกรด:
เอสทีเอ บี 338มาตรฐานนี้ครอบคลุมถึงท่อโลหะผสมไททาเนียมแบบไร้รอยต่อและแบบเชื่อมสำหรับใช้ในเครื่องแลกเปลี่ยนความร้อนและคอนเดนเซอร์ เกรดทั่วไป ได้แก่:
เกรด 1 / เกรด 2: เกรดไททาเนียมบริสุทธิ์เชิงพาณิชย์ที่มีความทนทานต่อการกัดกร่อนได้ดีเยี่ยม
เกรด 5 (Ti-6Al-4V): โลหะผสมไททาเนียมที่มีความแข็งแกร่งเพิ่มขึ้นและสมรรถนะที่อุณหภูมิสูง
แอสทาม B523:ครอบคลุมท่อโลหะผสมเซอร์โคเนียมแบบไร้รอยต่อและแบบเชื่อมสำหรับใช้ในเครื่องแลกเปลี่ยนความร้อนและคอนเดนเซอร์ เกรดทั่วไป ได้แก่:
เซอร์โคเนียม 702: โลหะผสมเซอร์โคเนียมบริสุทธิ์เชิงพาณิชย์ที่มีความทนทานต่อการกัดกร่อนได้ดีเยี่ยม
เซอร์โคเนียม 705: เกรดเซอร์โคเนียมอัลลอยด์ที่มีคุณสมบัติเชิงกลที่ได้รับการปรับปรุงและมีเสถียรภาพที่อุณหภูมิสูง
โลหะผสมไททาเนียมและเซอร์โคเนียมมักใช้ในสภาพแวดล้อมที่มีฤทธิ์กัดกร่อนสูง เช่น โรงงานการแยกเกลือจากน้ำทะเล อุตสาหกรรมแปรรูปเคมี โรงไฟฟ้านิวเคลียร์ หม้อไอน้ำและเครื่องแลกเปลี่ยนความร้อน เนื่องจากมีความทนทานต่อการกัดกร่อนที่เหนือกว่าและมีคุณสมบัติน้ำหนักเบา
VII. ทองแดงและโลหะผสมทองแดงสำหรับหม้อไอน้ำและเครื่องแลกเปลี่ยนความร้อน
ทองแดงและโลหะผสม เช่น ทองเหลือง ทองสัมฤทธิ์ และทองแดง-นิกเกิล ถูกใช้กันอย่างแพร่หลายในเครื่องแลกเปลี่ยนความร้อน คอนเดนเซอร์ และหม้อไอน้ำ เนื่องจากมีการนำความร้อนได้ดีเยี่ยมและทนต่อการกัดกร่อน
คุณสมบัติของโลหะผสมทองแดง:
การนำความร้อนที่ยอดเยี่ยม: โลหะผสมทองแดงเป็นที่รู้จักกันว่ามีคุณสมบัติการนำความร้อนสูง ทำให้เหมาะอย่างยิ่งสำหรับเครื่องแลกเปลี่ยนความร้อนและคอนเดนเซอร์
ความต้านทานการกัดกร่อน: โลหะผสมทองแดงต้านทานการกัดกร่อนในน้ำ รวมถึงน้ำทะเล ทำให้เหมาะสำหรับการใช้งานในทะเลและการแยกเกลือออกจากน้ำ
คุณสมบัติต้านจุลินทรีย์: โลหะผสมทองแดงมีคุณสมบัติต้านจุลินทรีย์ตามธรรมชาติ ทำให้เหมาะสำหรับการใช้งานในด้านการดูแลสุขภาพและการบำบัดน้ำ
มาตรฐานหลักและเกรด:
เอสทีเอ็ม บี 111มาตรฐานนี้ครอบคลุมถึงท่อทองแดงและท่อโลหะผสมทองแดงแบบไร้รอยต่อสำหรับใช้งานในเครื่องแลกเปลี่ยนความร้อน คอนเดนเซอร์ และเครื่องระเหย เกรดทั่วไป ได้แก่:
C44300 (Admiralty Brass): โลหะผสมทองแดง-สังกะสีที่มีความทนทานต่อการกัดกร่อนที่ดี โดยเฉพาะในการใช้งานกับน้ำทะเล
C70600 (ทองแดง-นิกเกิล 90/10): โลหะผสมทองแดง-นิกเกิลที่มีความทนทานต่อการกัดกร่อนในน้ำทะเลและสภาพแวดล้อมทางทะเลได้ดีเยี่ยม
C71500 (ทองแดง-นิกเกิล 70/30): โลหะผสมทองแดง-นิกเกิลอีกชนิดหนึ่งที่มีปริมาณนิกเกิลสูงเพื่อให้ทนทานต่อการกัดกร่อนได้ดีขึ้น
ทองแดงและโลหะผสมทองแดงถูกนำมาใช้กันอย่างแพร่หลายในหม้อไอน้ำทางทะเลและเครื่องแลกเปลี่ยนความร้อน โรงไฟฟ้า และระบบ HVAC เนื่องจากมีการนำความร้อนได้ดีเยี่ยมและทนทานต่อการกัดกร่อนของน้ำทะเล
นอกจากหม้อน้ำและเครื่องแลกเปลี่ยนความร้อนแล้ว คอนเดนเซอร์ ซูเปอร์ฮีตเตอร์ เครื่องอุ่นอากาศล่วงหน้า และเครื่องประหยัดพลังงานยังเป็นส่วนประกอบสำคัญที่ช่วยเพิ่มประสิทธิภาพการใช้พลังงานได้อย่างมาก ตัวอย่างเช่น คอนเดนเซอร์จะระบายความร้อนก๊าซไอเสียจากหม้อน้ำและเครื่องแลกเปลี่ยนความร้อน ในขณะที่ซูเปอร์ฮีตเตอร์จะเพิ่มอุณหภูมิของไอน้ำเพื่อเพิ่มประสิทธิภาพ ในขณะเดียวกัน เครื่องอุ่นอากาศล่วงหน้าจะใช้ก๊าซไอเสียเพื่อให้ความร้อนกับอากาศที่เข้ามา จึงช่วยเพิ่มประสิทธิภาพโดยรวมของระบบหม้อน้ำและเครื่องแลกเปลี่ยนความร้อนได้ดียิ่งขึ้น สุดท้าย เครื่องประหยัดพลังงานมีบทบาทสำคัญในการกู้คืนความร้อนเสียจากก๊าซไอเสียเพื่ออุ่นน้ำล่วงหน้า ซึ่งท้ายที่สุดจะช่วยลดการใช้พลังงานและเพิ่มประสิทธิภาพของหม้อน้ำและเครื่องแลกเปลี่ยนความร้อน
VIII. บทสรุป: การเลือกวัสดุที่เหมาะสมสำหรับหม้อไอน้ำและเครื่องแลกเปลี่ยนความร้อน
ท่อไร้รอยต่อเป็นส่วนสำคัญต่อประสิทธิภาพของหม้อไอน้ำ เครื่องแลกเปลี่ยนความร้อน คอนเดนเซอร์ เครื่องทำความร้อนสูง เครื่องอุ่นอากาศล่วงหน้า และเครื่องประหยัดพลังงานในอุตสาหกรรมต่างๆ เช่น การผลิตไฟฟ้า น้ำมันและก๊าซ และการแปรรูปทางเคมี การเลือกใช้วัสดุสำหรับท่อไร้รอยต่อขึ้นอยู่กับข้อกำหนดการใช้งานเฉพาะ เช่น อุณหภูมิ แรงดัน ความต้านทานการกัดกร่อน และความแข็งแรงเชิงกล
เหล็กกล้าคาร์บอน มีราคาที่เอื้อมถึงและมีความแข็งแรงสำหรับการใช้งานที่อุณหภูมิและแรงดันปานกลาง
เหล็กอัลลอยด์ มอบประสิทธิภาพการทำงานที่อุณหภูมิสูงและความแข็งแกร่งที่เหนือกว่าในหม้อไอน้ำและเครื่องทำความร้อนแบบซุปเปอร์ฮีตเตอร์
สแตนเลส มอบความต้านทานการกัดกร่อนและความทนทานที่ยอดเยี่ยมในเครื่องแลกเปลี่ยนความร้อนและซุปเปอร์ฮีตเตอร์
โลหะผสมนิกเกิล เป็นทางเลือกที่ดีที่สุดสำหรับสภาพแวดล้อมที่มีฤทธิ์กัดกร่อนสูงและอุณหภูมิสูงมาก
โลหะผสมไททาเนียมและเซอร์โคเนียม เหมาะอย่างยิ่งสำหรับการใช้งานน้ำหนักเบาและมีฤทธิ์กัดกร่อนสูง
ทองแดงและโลหะผสมทองแดง ได้รับความนิยมเนื่องจากมีคุณสมบัตินำความร้อนและทนต่อการกัดกร่อนในเครื่องแลกเปลี่ยนความร้อนและคอนเดนเซอร์
ระบบหม้อไอน้ำและเครื่องแลกเปลี่ยนความร้อนมีบทบาทสำคัญในอุตสาหกรรมต่างๆ โดยถ่ายเทความร้อนจากตัวกลางหนึ่งไปยังอีกตัวกลางหนึ่งอย่างมีประสิทธิภาพ หม้อไอน้ำและเครื่องแลกเปลี่ยนความร้อนทำงานร่วมกันเพื่อสร้างและถ่ายเทความร้อน ซึ่งให้ความร้อนที่จำเป็นสำหรับการผลิตไอน้ำในโรงไฟฟ้าและกระบวนการผลิต
จากการทำความเข้าใจคุณสมบัติและการใช้งานของวัสดุเหล่านี้ วิศวกรและนักออกแบบสามารถตัดสินใจอย่างรอบรู้ได้ ทำให้มั่นใจได้ว่าอุปกรณ์จะทำงานได้อย่างปลอดภัยและมีประสิทธิภาพ เมื่อเลือกวัสดุสำหรับหม้อไอน้ำและเครื่องแลกเปลี่ยนความร้อน สิ่งสำคัญคือต้องพิจารณาข้อกำหนดเฉพาะของการใช้งานของคุณ นอกจากนี้ คุณควรปรึกษาหารือกับมาตรฐานที่เกี่ยวข้องเพื่อให้แน่ใจว่าเข้ากันได้และมีประสิทธิภาพสูงสุด