การแนะนำ
การเลือกวัสดุเป็นขั้นตอนสำคัญในการรับรองความน่าเชื่อถือ ความปลอดภัย และประสิทธิภาพของอุปกรณ์ในอุตสาหกรรมต่างๆ เช่น น้ำมันและก๊าซ การแปรรูปทางเคมี วิศวกรรมทางทะเล อวกาศ และอื่นๆ อีกมากมาย วัสดุที่เหมาะสมสามารถป้องกันการกัดกร่อน ทนต่ออุณหภูมิที่รุนแรง และรักษาความสมบูรณ์เชิงกลในสภาพแวดล้อมที่รุนแรงได้ เหล็กกล้าและโลหะผสม เช่น เหล็กกล้าคาร์บอน เหล็กกล้าผสม เหล็กกล้าไร้สนิม นิกเกิล ไททาเนียม และซูเปอร์อัลลอยด์ประสิทธิภาพสูงต่างๆ เช่น อินโคเนล โมเนล และฮาสเทลลอย นำเสนอข้อดีเฉพาะที่ทำให้เหมาะอย่างยิ่งสำหรับการใช้งานที่ต้องการความแม่นยำสูงเหล่านี้ บล็อกนี้จะให้ภาพรวมที่ครอบคลุมของ แนวทางการเลือกใช้วัสดุโดยเน้นที่วัสดุสำคัญและความเหมาะสมโดยพิจารณาจากความต้านทานการกัดกร่อน คุณสมบัติเชิงกล และความสามารถในการรับอุณหภูมิ โดยการทำความเข้าใจคุณสมบัติเหล่านี้ วิศวกรและผู้ตัดสินใจสามารถปรับการเลือกวัสดุให้เหมาะสมเพื่อให้มั่นใจถึงประสิทธิภาพและประสิทธิภาพการทำงานในระยะยาว
แนวทางการเลือกวัสดุ: ตารางที่ 1 – รายการคำย่อ
คำย่อ |
เอพีไอ |
สถาบันปิโตรเลียมอเมริกัน |
เอส ที เอส ที |
สมาคมการทดสอบและวัสดุแห่งอเมริกา |
ซีเอ |
ค่าเผื่อการกัดกร่อน |
การลงทุน |
รายจ่ายด้านทุน |
คาร์บอนไดออกไซด์ |
คาร์บอนไดออกไซด์ |
ซีเอ็มเอ็ม |
คู่มือการตรวจสอบการกัดกร่อน |
กรมสรรพากร |
โลหะผสมที่ทนต่อการกัดกร่อน |
ครส. |
การศึกษาการประเมินความเสี่ยงจากการกัดกร่อน |
เหล็กโครเมียม |
โครเมียมสแตนเลส |
22Cr |
สแตนเลสสตีลดูเพล็กซ์ ชนิด 2205 (เช่น UNS S31803/S32205) |
25Cr |
สแตนเลสสตีลดูเพล็กซ์ซุปเปอร์ 2507 (เช่น UNS S32750) |
ซีเอส |
เหล็กกล้าคาร์บอน |
ซีทีโอดี |
การเคลื่อนที่ของการเปิดปลายรอยแตก |
ดีเอสเอส |
สแตนเลสดูเพล็กซ์ |
อีเอ็นพี |
การชุบนิกเกิลแบบไม่ใช้ไฟฟ้า |
อีพีซี |
วิศวกรรม จัดซื้อจัดจ้าง และก่อสร้าง |
กลุ่ม GRP |
พลาสติกเสริมใยแก้ว |
แฮซ |
โซนที่ได้รับผลกระทบจากความร้อน |
เอชวี |
ความแข็งวิกเกอร์ส |
เอชไอซี |
การแตกร้าวที่เกิดจากไฮโดรเจน |
เอชทูเอส |
ไฮโดรเจนซัลไฟด์ |
ไอเอสโอ |
องค์กรมาตรฐานสากล |
แอลทีซีเอส |
เหล็กกล้าคาร์บอนอุณหภูมิต่ำ |
เอ็มซีเอ |
การตรวจสอบวัสดุและการกัดกร่อน |
ข้อมูล MSD |
แผนภาพการเลือกวัสดุ |
เอ็มเอสอาร์ |
รายงานการเลือกใช้วัสดุ |
นา |
ไม่สามารถใช้ได้ |
นาซ |
สมาคมวิศวกรป้องกันการกัดกร่อนแห่งชาติ |
ค่าใช้จ่ายในการดำเนินงาน |
รายจ่ายดำเนินงาน |
เสื้อชูชีพ |
ไดอะแกรมกระบวนการไหล |
พีเอช |
เลขไฮโดรเจน |
พีเอ็มไอ |
การระบุวัสดุเชิงบวก |
พรีน |
ค่าเทียบเท่าความต้านทานการกัดเซาะ = %Cr + 3.3 (%Mo+0.5 %W) + 16 %N |
(ซี-)พีวีซี |
โพลีไวนิลคลอไรด์ (คลอรีน) |
พีดับเบิลยูเอชที |
การรักษาความร้อนหลังการเชื่อม |
การรับประกันคุณภาพ |
การรับประกันคุณภาพ |
คิวซี |
การควบคุมคุณภาพ |
ธนาคารอาร์บีไอ |
การตรวจสอบตามความเสี่ยง |
เลื่อย |
เชื่อมด้วยอาร์คใต้น้ำ |
สสส. |
ซุปเปอร์ดูเพล็กซ์สแตนเลส |
ส.อ. |
คำชี้แจงความต้องการ |
หว่าน |
ขอบเขตการทำงาน |
เอสเอส |
สแตนเลส |
ดับเบิลยูพีคิวอาร์ |
บันทึกคุณสมบัติขั้นตอนการเชื่อม |
ยูเอฟดี |
แผนผังการไหลของสาธารณูปโภค |
แนวทางการเลือกวัสดุ: ตาราง 2 – การอ้างอิงเชิงบรรทัดฐาน
อ้างอิง |
เลขที่เอกสาร |
ชื่อ |
(1) |
เอ เอส ที เอ 262 |
แนวทางปฏิบัติมาตรฐานในการตรวจจับความอ่อนไหวต่อการโจมตีระหว่างเม็ด |
(2) |
ใบรับรอง NACE MR0175 / ISO15156 |
อุตสาหกรรมปิโตรเลียม ปิโตรเคมี และก๊าซธรรมชาติ – วัสดุสำหรับใช้ในสภาพแวดล้อมที่มี H2S ในการผลิตน้ำมันและก๊าซ |
(3) |
เอ็นเอซีเอสเอส0407 |
รูปแบบ เนื้อหา และแนวทางในการพัฒนาแผนภาพการเลือกใช้วัสดุ |
(4) |
ใบรับรองมาตรฐาน ISO 21457 |
อุตสาหกรรมปิโตรเลียม ปิโตรเคมี และก๊าซธรรมชาติ – การควบคุมการกัดกร่อนในการเลือกใช้วัสดุสำหรับระบบการผลิตน้ำมันและก๊าซ |
(5) |
กฎ NACE TM0177 |
การทดสอบโลหะในห้องปฏิบัติการเพื่อต้านทานการแตกร้าวจากความเค้นซัลไฟด์และการกัดกร่อนจากความเค้น |
(6) |
เอ็นเอซีทีเอ็ม0316 |
การทดสอบการดัดสี่จุดของวัสดุสำหรับการใช้งานน้ำมันและก๊าซ |
(7) |
เอ็นเอซีทีเอ็ม0284 |
วิธีทดสอบมาตรฐาน – การประเมินเหล็กท่อและภาชนะรับแรงดันเพื่อต้านทานการแตกร้าวที่เกิดจากไฮโดรเจน |
(8) |
API 6DSS |
ข้อมูลจำเพาะสำหรับวาล์วท่อใต้น้ำ |
(9) |
เอพีไอ พีอาร์ 945 |
หลีกเลี่ยงการแตกร้าวจากสิ่งแวดล้อมในหน่วยอะมีน |
(10) |
เอพีไอ อาร์พี 571 |
กลไกความเสียหายที่ส่งผลต่ออุปกรณ์คงที่ในอุตสาหกรรมการกลั่น |
(11) |
เอ เอส ที เอ 263 |
ข้อกำหนดมาตรฐานสำหรับแผ่นเหล็กเคลือบโครเมียมสแตนเลส |
(12) |
เอ เอส ที เอ 264 |
ข้อกำหนดมาตรฐานสำหรับแผ่นเหล็กเคลือบโครเมียม-นิกเกิลสแตนเลส |
(13) |
เอ เอส ที เอ 265 |
ข้อกำหนดมาตรฐานสำหรับแผ่นเหล็กหุ้มโลหะผสมนิกเกิลและฐานนิกเกิล |
(14) |
เอเอสทีเอ578 |
ข้อกำหนดมาตรฐานสำหรับการตรวจสอบแผ่นเหล็กรีดด้วยคลื่นอัลตราโซนิกแบบลำแสงตรงสำหรับการใช้งานพิเศษ |
(15) |
เอเอสทีเอ153 |
ข้อกำหนดมาตรฐานสำหรับการเคลือบสังกะสี (แบบจุ่มร้อน) บนฮาร์ดแวร์เหล็กและเหล็กกล้า |
(16) |
ใบรับรอง NACE MR0103/ISO17945 |
อุตสาหกรรมปิโตรเลียม ปิโตรเคมี และก๊าซธรรมชาติ – วัสดุโลหะที่ทนทานต่อการแตกร้าวจากซัลไฟด์ในสภาพแวดล้อมการกลั่นปิโตรเลียมที่กัดกร่อน |
(17) |
เอเอสทีเอ 672 |
ข้อกำหนดมาตรฐานสำหรับท่อเหล็กเชื่อมฟิวชั่นไฟฟ้าสำหรับการใช้งานแรงดันสูงที่อุณหภูมิปานกลาง |
(18) |
เอ็นเอซีเอส SP0742 |
วิธีการและการควบคุมเพื่อป้องกันการแตกร้าวจากสิ่งแวดล้อมในการใช้งานของรอยเชื่อมเหล็กกล้าคาร์บอนในสภาพแวดล้อมการกลั่นปิโตรเลียมที่กัดกร่อน |
(19) |
เอพีไอ 5 ลิตร |
ข้อมูลจำเพาะสำหรับท่อสายส่ง |
(20) |
เอ็นเอซีเอส SP0304 |
การออกแบบ ติดตั้ง และการใช้งานแผ่นบุเทอร์โมพลาสติกสำหรับท่อส่งน้ำมัน |
(21) |
DNV RP O501 |
การสึกหรอจากการกัดเซาะในระบบท่อ |
แนวทางการเลือกวัสดุ: ตารางที่ 5 – พารามิเตอร์ที่ใช้ในการประเมินการกัดกร่อน
พารามิเตอร์ |
หน่วย |
การออกแบบชีวิต |
ปี |
ช่วงอุณหภูมิในการทำงาน |
องศาเซลเซียส |
เส้นผ่านศูนย์กลางท่อ |
มม |
แรงกดดันในการออกแบบ |
MPa |
อุณหภูมิจุดน้ำค้าง |
องศาเซลเซียส |
อัตราส่วนก๊าซต่อน้ำมัน (GOR) |
สชเอฟ/สโบ |
อัตราการไหลของก๊าซ น้ำมัน และน้ำ |
ตัน/วัน |
ปริมาณ CO2 และความดันบางส่วน |
โมล % / ppm |
ปริมาณ H2S และความดันบางส่วน |
โมล % / ppm |
ปริมาณน้ำ |
% |
พีเอช |
นา |
ปริมาณคลอไรด์ |
หน่วยต่อนาที |
ออกซิเจน |
หน่วยต่อนาที/หน่วยพันล้านปอนด์ |
กำมะถัน |
wt% / ปอนด์ต่อนาที |
ปรอท |
wt% / ปอนด์ต่อนาที |
ความเข้มข้นของกรดอะซิติก |
มก./ล. |
ความเข้มข้นของไบคาร์บอเนต |
มก./ล. |
ความเข้มข้นของแคลเซียม |
มก./ล. |
ปริมาณทราย/อนุภาคของแข็ง (การกัดเซาะ) |
กก./ชม. |
ศักยภาพในการกัดกร่อนที่เกิดจากจุลินทรีย์ (MIC) |
นา |
นโยบายของบริษัทคือการใช้เหล็กกล้าคาร์บอน (CS) เมื่อใดก็ตามที่เป็นไปได้สำหรับการสร้างระบบการผลิต อุปกรณ์การแปรรูป และท่อส่ง โดยมีค่าเผื่อการกัดกร่อน (CA) ที่เพียงพอสำหรับสินทรัพย์ที่จะบรรลุอายุการใช้งานที่ต้องการเพื่อรองรับการกัดกร่อน (ส่วนที่ 11.2) และหากเป็นไปได้ จะมีการจัดเตรียมสารป้องกันการกัดกร่อน (ส่วนที่ 11.4) เพื่อลดความเสี่ยงของการเกิดหลุมและลดอัตราการกัดกร่อน
ในกรณีที่การใช้ CS ไม่ใช่ทางเลือกทางเทคนิคและเศรษฐกิจ และ/หรือในกรณีที่การกัดกร่อนที่ล้มเหลวก่อให้เกิดความเสี่ยงที่ยอมรับได้ต่อบุคลากร สิ่งแวดล้อม หรือทรัพย์สินของบริษัท อาจใช้โลหะผสมที่ทนต่อการกัดกร่อน (Corrosion Resistance Alloy หรือ CRA) หรืออีกทางหนึ่ง หากการกัดกร่อนของ CS ที่มีอายุการใช้งานเกิน 6 มม. ด้วยการบำบัดสารยับยั้ง จะเลือกใช้ CRA (CRA แบบแข็งหรือแบบหุ้ม) การเลือก CRA ควรให้แน่ใจว่าได้เลือกโลหะผสมที่เหมาะสมที่สุดโดยพิจารณาจากเกณฑ์ต้นทุนและประสิทธิภาพ แผนภาพขั้นตอนการเลือกวัสดุแสดงไว้ในรูปที่ 1 เพื่อสรุปกระบวนการที่การเลือกวัสดุอื่นแทน CS อาจเหมาะสม
รูปที่ 1 – แผนผังขั้นตอนการเลือกวัสดุ
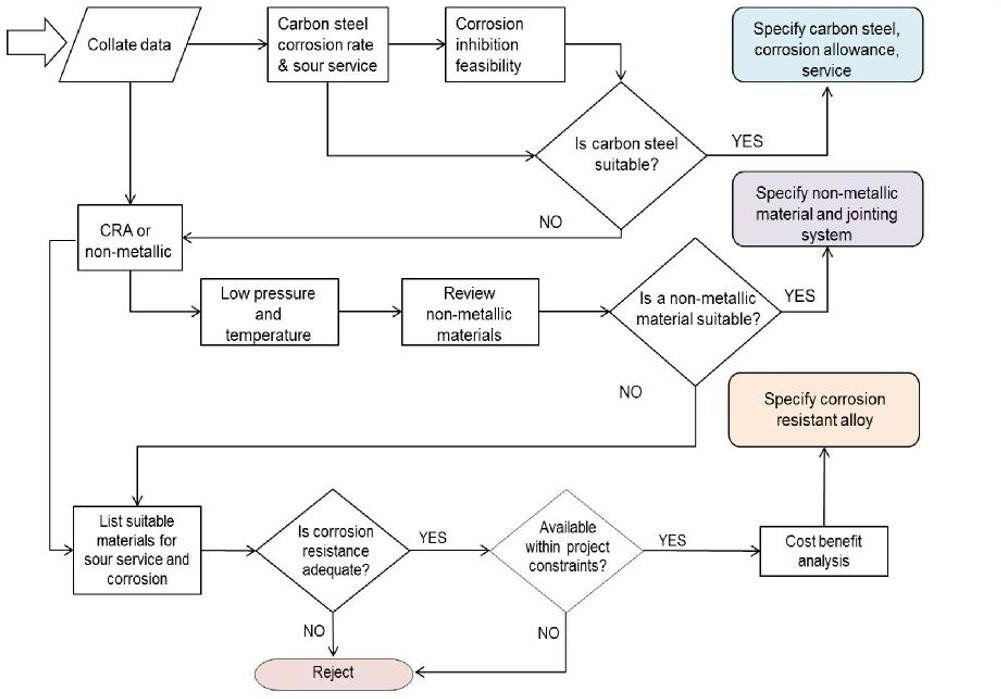
แนวทางการเลือกวัสดุ: ค่าเผื่อการกัดกร่อน
CA สำหรับ CS จะต้องระบุตามอัตราการกัดกร่อนที่คาดไว้หรืออัตราการเสื่อมสภาพของวัสดุภายใต้พารามิเตอร์กระบวนการที่รุนแรงที่สุด การระบุ CA ควรได้รับการออกแบบและอธิบายให้ถูกต้อง โดยสังเกตว่าเมื่อคาดว่าประสิทธิภาพของวัสดุในระยะสั้นหรือสภาวะชั่วคราวจะเพิ่มความเสี่ยงต่อการกัดกร่อนโดยทั่วไปหรือเฉพาะที่ ระยะเวลาการสึกกร่อนจะต้องประมาณตามอัตราการกัดกร่อนที่คำนวณตามสัดส่วน จากอัตราเหล่านี้ อาจต้องมีการเผื่อค่าการกัดกร่อนเพิ่มเติม ดังนั้น จำเป็นต้องดำเนินการ CRAS ในระยะเริ่มต้นของโครงการ
CA เองไม่ควรถือเป็นมาตรการควบคุมการกัดกร่อนที่รับรองได้ แต่ควรพิจารณาเป็นเพียงมาตรการที่ให้เวลาในการตรวจจับและประเมินอัตราการกัดกร่อนเท่านั้น
ขึ้นอยู่กับข้อกำหนดและเงื่อนไขของโครงการ ค่า CA ที่อนุญาตสามารถเพิ่มได้เกิน 6 มม. ในกรณีที่อัตราการกัดกร่อนที่ประมาณไว้เกิน 0.25 มม./ปี อย่างไรก็ตาม จะมีการหารือเรื่องนี้เป็นรายกรณี เมื่อค่าเผื่อการกัดกร่อนสูงเกินไป จะต้องพิจารณาและประเมินการอัปเกรดวัสดุ การเลือก CRA ควรให้แน่ใจว่าได้เลือกโลหะผสมที่เหมาะสมที่สุดตามเกณฑ์ประสิทธิภาพต้นทุน
ควรใช้หลักเกณฑ์ต่อไปนี้ในการระบุระดับ CA:
- CA คือผลคูณอัตราการกัดกร่อนโดยประมาณของวัสดุที่เลือกด้วยอายุการใช้งานที่ออกแบบไว้ (รวมถึงการขยายอายุการใช้งานที่เป็นไปได้) ปัดเศษเป็นค่าใกล้เคียงที่สุดเป็น 3.0, 4.5 หรือ 6.0 มม.
- สามารถประเมินการกัดกร่อนอันเกิดจาก CO2 ได้โดยใช้แบบจำลองการกัดกร่อนที่ได้รับการอนุมัติจากบริษัท เช่น ECE-4 และ 5, ทำนาย 6
- อัตราการกัดกร่อนที่ใช้ในการประมาณ CA จะต้องขึ้นอยู่กับประสบการณ์ของโรงงานในอดีตและข้อมูลที่เผยแพร่ที่มีอยู่สำหรับเงื่อนไขกระบวนการ ซึ่งควรประกอบด้วย:
- การกัดกร่อนของของเหลว เช่น การมีน้ำรวมกับไฮโดรเจนซัลไฟด์ (การกัดกร่อนแบบเปรี้ยว) CO2 (การกัดกร่อนแบบหวาน) ออกซิเจน กิจกรรมทางแบคทีเรีย อุณหภูมิและความดัน
- ความเร็วของของไหลที่กำหนดรูปแบบการไหลในระบบท่อ
- การสะสมของของแข็งที่อาจขัดขวางการป้องกันที่เหมาะสมโดยสารยับยั้งและสร้างเงื่อนไขสำหรับการเจริญเติบโตของแบคทีเรีย และ
- สภาวะที่อาจทำให้ผนังท่อ
- เหล็ก CS และโลหะผสมต่ำของชิ้นส่วนรับแรงดันต้องมีความหนาขั้นต่ำ 3.0 มม. ในกรณีพิเศษ อาจระบุความหนา 1.5 มม. ได้ด้วยการอนุมัติของบริษัท โดยพิจารณาจากอายุการใช้งานของรายการที่อยู่ระหว่างการพิจารณา ตัวอย่างของบริการที่ไม่กัดกร่อนหรือไม่กัดกร่อน ซึ่งอาจระบุความหนา 5 มม. ได้ ได้แก่ ไอ น้ำป้อนหม้อไอน้ำที่ผ่านการดีแอกทีฟ (< 10 ppb O2) น้ำหล่อเย็นที่ผ่านการบำบัด (ไม่กัดกร่อน ควบคุมด้วยคลอไรด์ ปราศจากแบคทีเรีย) อากาศอัดแห้ง ไฮโดรคาร์บอนที่ไม่มีน้ำ LPG, LNG, ก๊าซธรรมชาติแห้ง เป็นต้น หัวฉีดและคอท่อระบายน้ำจะต้องมีความหนา 5 มม. เท่ากับที่กำหนดไว้สำหรับอุปกรณ์ที่ควบคุมแรงดัน
- ค่า CA สูงสุดต้องอยู่ที่ 6.0 มม. ทั้งนี้ ขึ้นอยู่กับข้อกำหนดและเงื่อนไขของโครงการ ค่า CA ที่อนุญาตสามารถเพิ่มได้เกิน 6 มม. ในกรณีที่อัตราการกัดกร่อนที่ประมาณไว้เกิน 0.25 มม./ปี อย่างไรก็ตาม จะมีการหารือเรื่องนี้เป็นรายกรณี หากค่าเผื่อการกัดกร่อนสูงเกินไป จะต้องพิจารณาอัปเกรดวัสดุ และการเลือก CRA ควรให้แน่ใจว่าได้เลือกโลหะผสมที่เหมาะสมที่สุดตามเกณฑ์ประสิทธิภาพต้นทุน
- รูปแบบของการติดตั้งและผลกระทบต่ออัตราการไหล (รวมถึงขาตาย)
- ความน่าจะเป็นของความล้มเหลว รูปแบบของความล้มเหลว และผลที่ตามมาของความล้มเหลวต่อสุขภาพของมนุษย์ สิ่งแวดล้อม ความปลอดภัย และทรัพย์สินทางวัตถุ ล้วนถูกกำหนดโดยการดำเนินการประเมินความเสี่ยงไม่เพียงสำหรับวัสดุเท่านั้น แต่สำหรับสาขาอื่นๆ ด้วยเช่นกัน
- การเข้าถึงการบำรุงรักษาและ
สำหรับการเลือกวัสดุขั้นสุดท้าย จะต้องมีปัจจัยเพิ่มเติมต่อไปนี้ในการประเมิน:
- จะต้องให้ความสำคัญกับวัสดุที่มีความพร้อมจำหน่ายในตลาดดี และมีการบันทึกการผลิตและประสิทธิภาพการบริการ เช่น ความสามารถในการเชื่อม และความสามารถในการตรวจสอบ
- จะต้องลดจำนวนวัสดุที่แตกต่างกันให้เหลือน้อยที่สุดโดยคำนึงถึงสต็อก ต้นทุน ความสามารถในการใช้แทนกันได้ และความพร้อมใช้งานของชิ้นส่วนอะไหล่ที่เกี่ยวข้อง
- ความแข็งแรงต่อน้ำหนัก (สำหรับนอกชายฝั่ง) และ
- ความถี่ในการล้างท่อ/ทำความสะอาด ไม่จำเป็นต้องมี CA สำหรับ:
- วัสดุรองหลังของสิ่งของที่มีการหุ้มด้วยโลหะผสมหรือการเชื่อม
- บนปะเก็นที่หุ้มอยู่
- สำหรับ CRA อย่างไรก็ตาม สำหรับ CRA ในงานกัดเซาะ จะต้องระบุ CA 1 มม. ซึ่งจะต้องได้รับการแก้ไขและรองรับด้วยการสร้างแบบจำลองการกัดเซาะผ่าน DNV RP O501 [อ้างอิง (e)(21)] (หรือแบบจำลองที่คล้ายคลึงกันเมื่อได้รับการอนุมัติให้ใช้งานโดยบริษัท)
หมายเหตุ: เมื่อคาดว่าสภาวะระยะสั้นหรือชั่วคราวจะเพิ่มความเสี่ยงต่อการกัดกร่อนโดยทั่วไปหรือเฉพาะที่ จะต้องประมาณระยะเวลาการสึกกร่อนโดยพิจารณาจากอัตราการกัดกร่อนตามสัดส่วน จากข้อมูลดังกล่าว อาจต้องเผื่อค่าการกัดกร่อนให้สูงขึ้น นอกจากนี้ ควรใช้ท่อ CRA หรือท่อหุ้ม/บุภายใน CRA สำหรับพื้นที่ที่มีความเร็วของของไหลสูงและคาดว่าจะเกิดการกัดกร่อนจากการกัดกร่อน
แนวทางการเลือกวัสดุ : วัสดุหุ้มโลหะ
เพื่อลดความเสี่ยงของการกัดกร่อนในกรณีที่อัตราการกัดกร่อนเกิน 6 มม. CA อาจเหมาะสมที่จะระบุวัสดุหลัก CS ที่มีชั้นของวัสดุหุ้ม CRA หรือวัสดุเคลือบเชื่อม หากมีข้อสงสัย ผู้ระบุวัสดุควรขอคำแนะนำจากบริษัท หากระบุวัสดุหุ้ม CRA ของภาชนะ หรือใช้วัสดุหุ้ม CRA โดยการยึดด้วยการเชื่อมระเบิด การยึดด้วยลูกกลิ้งโลหะ หรือการหุ้มด้วยการเชื่อม จำเป็นต้องใช้แผ่นฐานคุณภาพทนทานต่อ SSC แต่ไม่จำเป็นต้องมีแผ่นฐานทนทานต่อ HIC
หากเลือกใช้การเชื่อมแบบระเบิดหรือแบบม้วน จะต้องได้ความหนาขั้นต่ำ 3 มม. ทั่วทั้ง 100% ของวัสดุต้นทาง หากเลือกใช้การซ้อนทับ จะต้องผ่านอย่างน้อย 2 รอบ และต้องได้ความหนาขั้นต่ำ 3 มม. หากมีปัญหาเรื่องการเชื่อม ก็สามารถพิจารณาใช้การเชื่อมแบบระเบิดได้
วัสดุหุ้มทั่วไปได้แก่:
- 316SS (อาจระบุประเภท 317SS ได้ในกรณีที่มีความเสี่ยงการเกิดหลุมคลอไรด์สูง)
- โลหะผสม 904;
- โลหะผสม 825 (จำกัดเฉพาะการยึดด้วยม้วน เนื่องจากการเชื่อมอาจทำให้แผ่นหุ้มมีความต้านทานการกัดกร่อนที่ด้อยกว่า) และ
- โลหะผสม
ในกรณีที่ความหนาของภาชนะค่อนข้างบาง (ไม่เกิน 20 มม.) ควรใช้การวิเคราะห์ต้นทุนตลอดอายุการใช้งานเพื่อตัดสินใจว่าการเลือกใช้วัสดุ CRA แบบแข็งจะคุ้มค่าทางการค้ามากกว่าหรือไม่ โดยต้องพิจารณาเป็นรายกรณี
ท่อหุ้มหรือบุผิวอาจใช้สำหรับท่อส่งที่ขนส่งของเหลวที่มีฤทธิ์กัดกร่อนสูง ข้อกำหนดของ API 5LD มีผลบังคับใช้ ด้วยเหตุผลทางเศรษฐกิจ ท่อเหล่านี้จะมีเส้นผ่านศูนย์กลางเล็กและความยาวสั้น ท่อหุ้มจะขึ้นรูปจากแผ่นเหล็กที่มีชั้น CRA หนา 3 มม. ยึดติดกับพื้นผิวด้านใน ท่อหุ้ม CRA อาจยึดติดด้วยโลหะ การอัดรีดร่วม หรือการเชื่อมทับ หรือสำหรับการใช้งานใต้น้ำ อาจใช้การเชื่อมด้วยกระบวนการ/กลไกเมื่อความเสี่ยงในการคลายแรงดันต่ำ สำหรับท่อเชื่อม ท่อหุ้ม CRA จะถูกขึ้นรูปเข้ากับท่อและเชื่อมตะเข็บด้วยวัสดุสิ้นเปลืองของ CRA
ผู้รับเหมาจะต้องออกข้อกำหนดแยกกันตามข้อกำหนดเฉพาะของบริษัทที่มีอยู่แล้วสำหรับวัสดุหุ้มโลหะผสมหรือวัสดุหุ้มเชื่อมบน CS ซึ่งครอบคลุมข้อกำหนดสำหรับการออกแบบ การผลิต และการตรวจสอบวัสดุบุผิวและวัสดุหุ้มแบบรวมที่ใช้สำหรับภาชนะรับแรงดันและตัวแลกเปลี่ยนความร้อน อาจใช้ข้อกำหนด ASTM A263, A264, A265, A578 และ E164 และ NACE MR0175/ISO 15156 เป็นข้อมูลอ้างอิง
แนวทางการเลือกใช้วัสดุ: การใช้สารยับยั้งการกัดกร่อน
การเลือกและประเมินสารยับยั้งการกัดกร่อนจะต้องเป็นไปตามขั้นตอนของบริษัท สำหรับวัตถุประสงค์ในการออกแบบ ควรถือว่าประสิทธิภาพในการป้องกันการกัดกร่อนของ 95% ถือได้ว่าเป็นประสิทธิภาพสำหรับคอนเดนเสทก๊าซ และ 90% ถือได้ว่าเป็นประสิทธิภาพสำหรับน้ำมัน นอกจากนี้ ในระหว่างการออกแบบ ความพร้อมของสารยับยั้งจะต้องขึ้นอยู่กับความพร้อมของ 90% ในระหว่างขั้นตอนการดำเนินการ ความพร้อมของสารยับยั้งขั้นต่ำจะต้องมากกว่า 90% ความพร้อมของสารยับยั้งจะต้องระบุในขั้นตอน FEED ตามโครงการต่อโครงการ อย่างไรก็ตาม การใช้สารยับยั้งการกัดกร่อนจะต้องไม่ทดแทนข้อกำหนดการเลือกวัสดุสำหรับใช้งานที่มีรสเปรี้ยวตาม NACE MR0175/ISO 15156
เพื่อให้สามารถตรวจสอบประสิทธิภาพของระบบการยับยั้งระหว่างการใช้งาน จะต้องมีการรวมสิ่งต่อไปนี้ไว้ในการออกแบบ:
- ตำแหน่งที่มีโอกาสเกิดการกัดกร่อนสูงที่สุด
- การเข้าถึงตำแหน่งที่มีอัตราการกัดกร่อนสูงเพื่อการวัดความหนาของผนังในระหว่าง
- ความสามารถในการเก็บตัวอย่างของแข็ง/เศษซาก
- ควรใช้เครื่องมือวัดการกัดกร่อนเพื่อตรวจสอบประสิทธิภาพของการยับยั้ง
- ควรจะรวมสิ่งอำนวยความสะดวกสำหรับการตรวจนับเหล็กไว้ในการออกแบบเพื่อการตรวจสอบการยับยั้ง
จะต้องมีการจัดเตรียมในการออกแบบเพื่อให้สามารถวัดและติดตามตัวชี้วัดประสิทธิภาพหลัก (KPI) ต่อไปนี้สำหรับระบบที่ถูกยับยั้งได้:
- จำนวนชั่วโมงที่ระบบยับยั้งไม่
- ความเข้มข้นที่ฉีดจริงเทียบกับปริมาณการฉีดเป้าหมาย
- ความเข้มข้นของสารยับยั้งตกค้างเมื่อเทียบกับเป้าหมาย
- อัตราการกัดกร่อนเฉลี่ยเมื่อเทียบกับการกัดกร่อนยับยั้งเป้าหมาย
- การเปลี่ยนแปลงอัตราการกัดกร่อนหรือระดับเหล็กที่ละลายเป็นฟังก์ชันของ
- การไม่สามารถเข้าถึงการตรวจสอบการกัดกร่อนได้
แนวทางการเลือกใช้วัสดุ : วัสดุสำหรับบริการเปรี้ยว
การเลือกวัสดุสำหรับท่อและอุปกรณ์สำหรับใช้ในสภาพแวดล้อมที่มี H2S จะต้องเป็นไปตามข้อกำหนดล่าสุดของบริษัทสำหรับวัสดุในสภาพแวดล้อมที่มีกรด และต้องได้รับการตรวจยืนยันตามมาตรฐาน NACE MR0175/ISO15156 สำหรับกระบวนการต้นน้ำ และ NACE MR0103/ISO 17945 สำหรับกระบวนการปลายน้ำ
ควรพิจารณาใช้ 316L SS สำหรับบริการที่มีกรดเป็นส่วนประกอบส่วนใหญ่ ยกเว้นในกรณีที่มีอุณหภูมิสูงกว่า 60 °C ร่วมกับปริมาณ H2S และคลอไรด์ในของเหลวสูง อย่างไรก็ตาม จะพิจารณาเป็นรายกรณี สำหรับเงื่อนไขการทำงานนอกเหนือจากข้อจำกัดเหล่านี้ อาจพิจารณาใช้วัสดุโลหะผสมที่มีปริมาณสูงกว่าเพื่อให้เป็นไปตาม NACE MR0175/ISO15156 นอกจากนี้ ควรพิจารณาการแยกไอในกรณีที่ปริมาณคลอไรด์ที่ตกค้างจะลดลง
อาจพิจารณาใช้วัสดุหุ้ม SS 316L สำหรับเรือโดยปฏิบัติตามข้อจำกัดด้านสิ่งแวดล้อมและวัสดุจากตาราง A2 ใน ISO 15156 ส่วนที่ 3 เรือที่หุ้มด้วย 316L ต้องปล่อยให้เย็นลงต่ำกว่า 60 °C ก่อนเปิด เนื่องจากมีความเสี่ยงที่วัสดุหุ้มจะแตกร้าวจากความเค้นคลอไรด์เมื่อสัมผัสกับออกซิเจน สำหรับเงื่อนไขการทำงานนอกเหนือจากข้อจำกัดเหล่านี้ อาจพิจารณาใช้วัสดุโลหะผสมที่มีความแข็งแรงสูงกว่าเพื่อให้เป็นไปตาม NACE MR0175/ISO15156 จะต้องตรวจสอบวัสดุหุ้มเพื่อให้แน่ใจว่ามีความต่อเนื่องตลอด 100% ของพื้นผิวทั้งหมด รวมถึงหัวฉีดและสิ่งที่แนบมาอื่นๆ
เหล็กสำหรับท่อส่งน้ำที่มีกรดกัดกร่อนจะต้องทนทานต่อ HIC มีปริมาณกำมะถันน้อยกว่า 0.01% และต้องผ่านกระบวนการบำบัดขั้นที่สองด้วยแคลเซียมเพื่อควบคุมรูปร่างของการรวมตัว เหล็กสำหรับท่อเชื่อมตามยาวจะต้องมีปริมาณกำมะถันน้อยกว่า 0.003% และต้องผ่านกระบวนการบำบัดขั้นที่สองด้วยแคลเซียมเพื่อควบคุมรูปร่างของการรวมตัว
แนวทางเฉพาะสำหรับการใช้สลักเกลียวในสภาพแวดล้อมการบริการที่มีกรดกัดกร่อน สามารถพบได้ในส่วนการใช้สลักเกลียวของแนวทางปฏิบัตินี้ ส่วนที่ 12.8
เมื่อผู้ซื้อระบุข้อกำหนดบริการที่ไม่เหมาะสม จะต้องใช้สิ่งต่อไปนี้:
- วัสดุทั้งหมดจะต้องมีการทำเครื่องหมายเพื่อให้สามารถตรวจสอบย้อนกลับได้จนถึงการหลอมและการให้ความร้อน
- การอบชุบด้วยความร้อน สำหรับเงื่อนไขการอบชุบ จะต้องระบุอุณหภูมิการอบชุบ
- ต้องใช้คำต่อท้ายเพิ่มเติม "S" เพื่อระบุวัสดุที่ส่งมอบตาม MDS รวมถึงข้อกำหนดเพิ่มเติมสำหรับบริการที่มีรสเปรี้ยวไม่รวมการทดสอบ HIC และการตรวจ UT
- ต้องใช้คำต่อท้ายเพิ่มเติม 'SH' เพื่อระบุวัสดุที่ส่งมอบตาม MDS รวมถึงข้อกำหนดเพิ่มเติมสำหรับบริการที่มีรสเปรี้ยว รวมถึงการทดสอบ HIC และ UT
- ผู้ผลิตวัสดุจะต้องมีระบบคุณภาพที่ได้รับการรับรองตามมาตรฐาน ISO 9001 หรือมาตรฐานข้อกำหนดคุณภาพอื่นๆ ที่ผู้ซื้อยอมรับ
- เอกสารตรวจสอบจะต้องออกตามมาตรฐาน ISO 10474 /EN 10204 ประเภท 1 และต้องยืนยันว่าเป็นไปตามข้อกำหนดนี้
- วัสดุที่ถูกฆ่าจนหมดจะต้อง
- สำหรับท่อบริการที่มีกรด วัสดุจะต้องเป็นไปตามข้อกำหนดของ API 5L Annex H – PSL2 สำหรับท่อบริการที่มีกรดรุนแรง จะต้องระบุเกรดมาตรฐานที่มีความแข็งแรงต่ำ จำกัดไม่เกินเกรด X65
- จำเป็นต้องทำการทดสอบการใช้งานแบบ Sour Service กับทั้งวัสดุฐานและการเชื่อม และการทดสอบตามปกติสำหรับ SSC และ HIC จะต้องเป็นไปตาม NACE TM0177 และ NACE TM0284 การทดสอบ SOHIC และการแตกร้าวในโซนอ่อนอาจต้องทดสอบวงแหวนทั้งหมดด้วยการเชื่อมที่ผลิตขึ้นโดยใช้การเชื่อมการผลิตจริง การทดสอบการดัดสี่จุดจะต้องดำเนินการตาม NACE TM0316
- ความแข็งตามมาตรฐาน ISO 15156 สำหรับต้นน้ำ และ NACE MR0173/NACE SP0742 สำหรับ
แนวทางการเลือกวัสดุ: ข้อควรพิจารณาเฉพาะ
รายการต่อไปนี้ประกอบด้วยข้อควรพิจารณาในการเลือกวัสดุที่เฉพาะเจาะจงซึ่งไม่เฉพาะเจาะจงกับระบบใด ๆ และจะต้องใช้กับโครงการทั้งหมดของบริษัท:
- ผู้รับเหมาจะต้องรับผิดชอบอย่างเต็มที่ต่อการเลือกใช้วัสดุที่ผู้ให้สิทธิ์อนุญาต I เลือกใช้ในอุปกรณ์ที่บรรจุหีบห่อ ผู้รับเหมาจะต้องจัดเตรียมข้อมูลทั้งหมด รวมถึง MSD หลักการเลือกใช้วัสดุ CRAS RBI และ MCA ตามข้อกำหนดนี้เพื่อให้บริษัทอนุมัติ การเปลี่ยนแปลงวัสดุใดๆ ก็ตามจะรับประกันภายใต้ผู้รับเหมา
- จะต้องใส่ใจคุณสมบัติความเหนียวแตกหักของวัสดุท่อเพื่อป้องกันความเป็นไปได้ที่จะแตกหักแบบเปราะ
- ไม่ควรใช้อลูมิเนียมบรอนซ์ในชิ้นส่วนที่เชื่อม เนื่องจากอาจเชื่อมได้ไม่ดีและมีปัญหาในการบำรุงรักษา
- ห้ามใช้การชุบนิกเกิลแบบไม่ใช้ไฟฟ้า (ENP) เว้นแต่จะได้รับอนุมัติจาก
- วัสดุสำหรับระบบน้ำมันหล่อลื่นและซีลจะต้องเป็น SS316L หากมีความเหมาะสม
- ห้ามใช้แผ่นยางบุในกล่องน้ำของคอนเดนเซอร์พื้นผิวและตัวแลกเปลี่ยนอื่น ๆ เว้นแต่จะได้รับอนุมัติจากบริษัท
- อนุญาตให้ใช้วัสดุ GRE/HDPE สำหรับน้ำมันและก๊าซแรงดันต่ำ น้ำ น้ำมัน และน้ำฝน ท่อระบายน้ำที่อยู่ในพารามิเตอร์การบริการที่ยอมรับได้ และขีดจำกัดการโหลด (เมื่อฝังอยู่ใต้ดิน) โดยผู้ผลิต ได้รับอนุญาตโดยต้องได้รับการอนุมัติจากบริษัท
- การออกแบบเครื่องแลกเปลี่ยนความร้อนจะต้องขึ้นอยู่กับข้อกำหนดของกระบวนการ ดังนั้น การเลือกวัสดุจึงขึ้นอยู่กับเครื่องแลกเปลี่ยนความร้อนทุกเครื่อง และไม่ควรทำให้เป็นมาตรฐาน
- ไม่ควรใช้สแตนเลส 304, 304L เป็นวัสดุภายนอกในกรณีที่ไม่เหมาะกับบรรยากาศที่มีความชื้นของสหรัฐอาหรับเอมิเรตส์
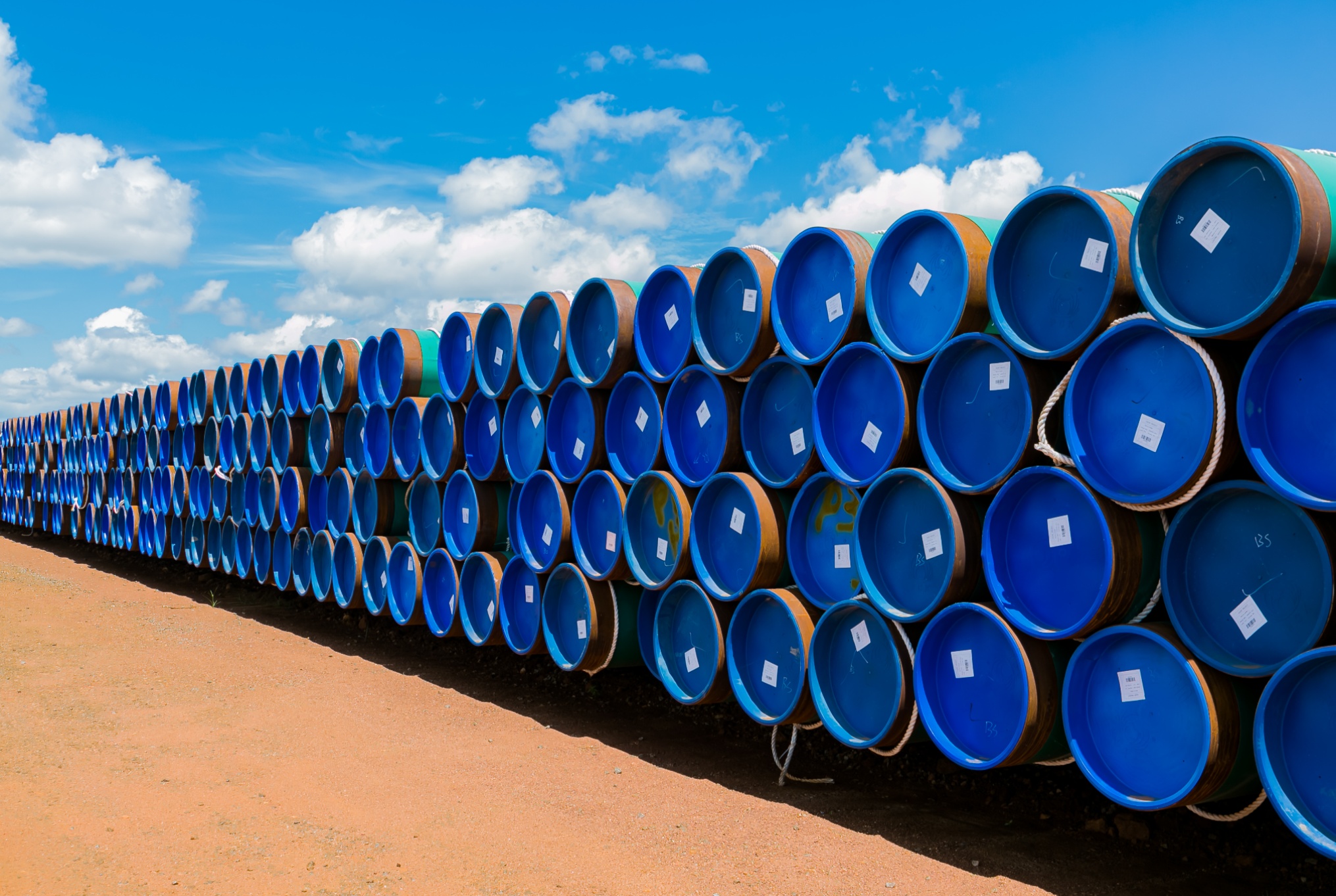
ท่อเคลือบ FBE
แนวทางการเลือกวัสดุ: การใช้งานและระบบเฉพาะ
ส่วนนี้ให้แนวทางที่สำคัญสำหรับระบบเฉพาะที่มีอยู่ในกลุ่มผลิตภัณฑ์ของบริษัท รวมถึงสินทรัพย์ต้นน้ำ (ทั้งบนบกและนอกชายฝั่ง) และปลายน้ำ (โรงกลั่น) ภาพรวม
จากหน่วยต่างๆ ที่พบในโรงงานเหล่านี้ ตัวเลือกวัสดุ กลไกความเสียหายที่อาจเกิดขึ้น และการบรรเทาผลกระทบจากกลไกดังกล่าวมีอยู่ในตารางต่อไปนี้ รายละเอียดเพิ่มเติมสำหรับแต่ละหน่วยจะระบุไว้ในส่วนที่เหลือของหัวข้อนี้ สำหรับรายละเอียดเพิ่มเติมเกี่ยวกับกลไกการกัดกร่อนที่ระบุไว้ โปรดดู API RP 571
หมายเหตุ: ตัวเลือกวัสดุที่ระบุไว้ในหัวข้อนี้ถือเป็นแนวทางเท่านั้น ผู้รับเหมาจะต้องรับผิดชอบในการเลือกวัสดุเฉพาะโครงการตลอดแต่ละขั้นตอนของโครงการโดยผ่านผลงานส่งมอบตามที่ระบุในหัวข้อที่ 10
แนวทางการเลือกใช้วัสดุ: ตาราง 6 – คำแนะนำด้านวัสดุสำหรับอุปกรณ์กระบวนการต้นน้ำและท่อ
บริการ |
ตัวเลือกวัสดุ |
กลไกการเสียหาย |
การบรรเทาผลกระทบ |
สปูลแข็งหัวบ่อน้ำมัน/จัมเปอร์และท่อร่วม |
CS+CRA แผ่นปิดผนัง, CRA, CS+CA |
การกัดกร่อนของ CO2 ความเสียหายจาก H2S เปียก การแตกร้าวจากการกัดกร่อนของคลอไรด์ (CSCC) |
การเลือกใช้วัสดุ
(เมื่อการยับยั้งการกัดกร่อนถือว่าไม่มีประสิทธิภาพที่ตำแหน่งดังกล่าว/บริการที่มีฤทธิ์กัดกร่อนสูง/แนะนำตัวเลือกหุ้ม CRA)
ออกแบบเพื่อการบริการที่เปรี้ยว
ตัวเลือกหุ้ม UNS N06625/UNS N08825
ข้อกำหนดการบริการที่มีรสเปรี้ยว NACE MR0175/ISO 15156 มีผลใช้กับการบริการที่มีรสเปรี้ยว |
ท่อส่งน้ำ/ท่อส่งน้ำ |
ซีเอส+ซีเอ |
การเปราะของไฮโดรเจน การกัดกร่อนของ CO2 ความเสียหายจาก H2S เปียก CSCC, MIC |
การป้องกันแบบแคโทดิกและการเคลือบเพื่อปกป้องส่วนโลหะที่ฝังอยู่
การใช้สารยับยั้งการกัดกร่อนของสารชีวฆ่า และเครื่องตัดหมู/เครื่องขูด
การตรวจสอบอินไลน์ตามระยะ (Intelligent Pigging) เพื่อวัดความหนาของผนังและการทำความสะอาดตามระยะโดยใช้อุปกรณ์ทำความสะอาดที่เหมาะสม |
ก๊าซไฮโดรคาร์บอนเปียก |
ซีเอส+ซีเอ
(+CA/CRA หุ้ม) 316SS, DSS, SDSS |
การกัดกร่อนของ CO2, ความเสียหายจาก H2S เปียก, CSCC, การเกิดหลุมคลอไรด์ |
การเลือกใช้วัสดุ
ออกแบบเพื่อการบริการที่เปรี้ยว
จะต้องประเมินการกัดกร่อนของ TOL และการบรรเทาผลกระทบจะต้องระบุการหุ้ม CRA เมื่อค่าเผื่อการกัดกร่อนเกิน 6 มม.
การใช้สารยับยั้งการกัดกร่อนตามข้อกำหนด NACE MR0175 /ISO 15156 สำหรับการบริการที่มีรสเปรี้ยวจะมีผลใช้กับการบริการที่มีรสเปรี้ยว
การเลือกที่ทางเข้าส่วนใหญ่ขึ้นอยู่กับข้อกำหนดการบริการที่เป็นกรด |
ก๊าซไฮโดรคาร์บอนแห้ง |
CS+CA (+CRA แผ่นหุ้ม) 316SS |
การกัดกร่อนของ CO2, ความเสียหายจาก H2S เปียก |
การเลือกใช้วัสดุ
ตรวจสอบให้แน่ใจว่าการดำเนินการอยู่ภายใต้เงื่อนไขที่กำหนด
การตรวจสอบการกัดกร่อนเป็นสิ่งสำคัญเพื่อให้แน่ใจว่าก๊าซยังคงแห้ง อาจต้องใช้ CA หากมีโอกาสเกิดความชื้นในช่วงระยะเวลาหนึ่ง |
คอนเดนเสทที่เสถียร |
ซีเอส+ซีเอ |
การกัดกร่อนของ CO2, ความเสียหายจาก H2S เปียก, MIC |
การเลือกใช้วัสดุ
การติดตามกิจกรรมของแบคทีเรีย |
น้ำที่ผลิต |
CS+CA, 316SS, DSS, SDSS. CS+CRA แผ่นซับ, CS+CRA (เชื่อมด้วยโลหะ) |
การกัดกร่อนของ CO2, ความเสียหายจาก H2S เปียก, CSCC, MIC, การกัดกร่อนของ O2 |
การเลือกใช้วัสดุ
ออกแบบเพื่อป้องกันการรั่วซึมของออกซิเจน
การใช้สารชีวฆ่า สารกำจัด O2 และสารยับยั้งการกัดกร่อน
เรืออาจเลือกซับใน CS + ภายในได้
ข้อมูลจำเพาะของวัสดุท่อขึ้นอยู่กับกระบวนการ/สภาวะของไหลเป็นอย่างมาก
ข้อกำหนดด้านบริการที่มีรสเปรี้ยว NACE MR0175 /ISO 15156 มีผลใช้กับบริการที่มีรสเปรี้ยว |
ส่งออกน้ำมัน/ก๊าซ ส่งออก/ก๊าซป้อน |
ซีเอส+ซีเอ |
การกัดกร่อนของ CO2, ความเสียหายจาก H2S เปียก, MIC |
การเลือกใช้วัสดุ
สำหรับการส่งออกก๊าซการตรวจสอบอุณหภูมิจุดน้ำค้าง
หากการส่งออกก๊าซถือเป็นแบบ 'เปียก' อาจจำเป็นต้องอัปเกรดเป็นวัสดุ CRA (หุ้ม/ของแข็ง) ตามผลการประเมินการกัดกร่อน |
ภาวะขาดน้ำจากก๊าซ (TEG) |
ซีเอส+ซีเอ, 316เอสเอส, ซีเอส+ซีอาร์เอ |
การกัดกร่อนจากกรดควบแน่นในคอลัมน์นิ่งเหนือศีรษะ |
การเลือกวัสดุนั้นขึ้นอยู่กับผู้อนุญาต แต่ความรับผิดชอบนั้นอยู่ที่ผู้รับเหมา |
สารเคมีฉีด (เช่น สารยับยั้งการกัดกร่อน) |
CS(+CA), 316SS, ซี-พีวีซี |
ความเข้ากันได้ทางเคมี การกัดกร่อน |
การเลือกวัสดุจะต้องมีการหารือกับผู้จำหน่าย/ซัพพลายเออร์ในแง่ความเข้ากันได้ทางเคมี |
การกำจัดสารปรอท |
ซีเอส+ซีเอ |
การกัดกร่อนของ CO2, ความเสียหายจาก H2S เปียก, CSCC, การเกิดหลุมคลอไรด์
*การเปราะของโลหะเหลว |
การเลือกใช้วัสดุ
*ไม่ควรใช้โลหะผสมไททาเนียมที่มีอะลูมิเนียมหรือทองแดงในกรณีที่มีความเสี่ยงต่อการปนเปื้อนปรอทเหลว |
อะมีน |
แผ่นหุ้ม CS+CA/CRA 316SS |
การกัดกร่อนของ CO2 ความเสียหายจาก H2S เปียก การแตกร้าวจากการกัดกร่อนของความเครียดของอะมีน (ASCC) การกัดกร่อนของอะมีน การกัดกร่อน (จากเกลือที่ทนความร้อน) |
ความเร็วการทำงานที่เหมาะสม อุณหภูมิสำหรับระบบที่ออกแบบ และการสุ่มตัวอย่างเป็นประจำเพื่อตรวจสอบเกลืออะมีน
อะมีนที่อุดมไปด้วยจะต้องเป็น 316SS
ภายในเรือต้องมีขนาด 316SS ขีดจำกัดความเร็ว
จะต้องระบุ PWHT สำหรับ CS เพื่อป้องกัน ASCC เมื่ออุณหภูมิการออกแบบอยู่ที่ > 53°C อุณหภูมิ PWHT ที่จะใช้จะต้องเป็นไปตาม API RP945 |
แฟลร์ |
ซีเอส+ซีเอ, 316เอสเอส
*310SS, 308SS, อัลลอย 800, อัลลอย 625 |
การแตกที่อุณหภูมิต่ำ การกัดกร่อนในบรรยากาศ การแตกจากการคืบคลาน (ความล้าจากความร้อน)
กสทช. |
CS + ซับในเป็นตัวเลือกสำหรับกลองแฟลร์
ออกแบบสำหรับอุณหภูมิการออกแบบทั้งต่ำสุดและสูงสุด
ปัญหาของการแตกเปราะที่อุณหภูมิต่ำที่ต้องได้รับการแก้ไข
กลไกการกัดกร่อนภายในมีแนวโน้มเกิดขึ้นมากขึ้นในสภาพแวดล้อมทางทะเล
* วัสดุสำหรับปลายบาน |
PLR (เครื่องรับ PIG Launcher) |
CS+Weld Overlay สำหรับปิดผนึกพื้นผิว |
การกัดกร่อนของ CO2, ความเสียหายจาก H2S เปียก, การกัดกร่อนจากการสะสมต่ำ, MIC,
การกัดกร่อนของขาตาย |
การตรวจสอบวัสดุตามระยะเวลา
การใช้สารชีวฆ่าและสารยับยั้งการกัดกร่อน |
ตาราง 7 – คำแนะนำด้านวัสดุสำหรับอุปกรณ์กระบวนการปลายน้ำและท่อ
บริการ |
ตัวเลือกวัสดุ |
กลไกการเสียหาย |
การบรรเทาผลกระทบ |
หน่วยธุรกิจน้ำมันดิบ |
CS, 5Cr-1/2 Mo, 9Cr-1Mo, 12Cr, 317L, 904L หรือโลหะผสมอื่นที่มี Mo สูงกว่า (เพื่อหลีกเลี่ยง NAC), CS+SS Clad |
การโจมตีของกำมะถัน การเกิดซัลไฟด์ การกัดกร่อนของกรดแนฟเทนิก (NAC) ความเสียหายจาก H2S เปียก การกัดกร่อนของ HCL |
การเลือกวัสดุการกำจัดเกลือ
ขีดจำกัดความเร็วการไหล
การใช้สารยับยั้งการกัดกร่อน |
การแตกร้าวจากตัวเร่งปฏิกิริยาของไหล |
เหล็ก CS + CA, 1Cr-1/2Mo, 2-1/4Cr-1Mo, 5Cr และ 9Cr, 12Cr SS, 300 ซีรีส์ SS, 405/410SS, โลหะผสม 625
การกัดเซาะภายใน/วัสดุบุผิวทนไฟที่เป็นฉนวน |
การกัดกร่อนตัวเร่งปฏิกิริยา
การเกิดซัลไฟด์ที่อุณหภูมิสูง การเกิดคาร์บอนที่อุณหภูมิสูง การคืบ ความเปราะบางจากการคืบ การแตกร้าวจากการกัดกร่อนของกรดพลอยไธโอนิก การเกิดกราไฟต์ที่อุณหภูมิสูง การเกิดออกซิเดชันที่อุณหภูมิสูง
ความเปราะบาง 885°F |
การเลือกใช้วัสดุ ซับในทนทานต่อการกัดกร่อน
ออกแบบความปั่นป่วนขั้นต่ำของตัวเร่งปฏิกิริยาและการส่งต่อตัวเร่งปฏิกิริยา |
การกู้คืนปลายแสง FCC |
CS + CA (+ 405/410SS Cladding), DSS, โลหะผสม C276, โลหะผสม 825 |
การกัดกร่อนที่เกิดจากการรวมกันของ H2S ในน้ำ แอมโมเนีย และไฮโดรเจนไซยาไนด์ (HCN)
ความเสียหายจาก H2S เปียก-SSC, SOHIC, HIC การแตกร้าวจากการกัดกร่อนจากความเครียดแอมโมเนียม, การแตกร้าวจากการกัดกร่อนจากความเครียดคาร์บอเนต |
การเลือกใช้วัสดุ
การฉีดโพลีซัลไฟด์เข้าไปในน้ำล้างเพื่อลดปริมาณ HCN
ขีดจำกัดความเร็ว
การฉีดสารยับยั้งการกัดกร่อน ป้องกันการรั่วซึมของออกซิเจน |
กรดซัลฟิวริก
การอัลคิเลชั่น |
CS + CA, เหล็กอัลลอยด์ต่ำ, อัลลอยด์ 20, 316SS, C-276 |
การกัดกร่อนของกรดซัลฟิวริก การเกิดร่องด้วยไฮโดรเจน การเจือจางของกรด การเกาะติด CUI |
การเลือกวัสดุ – อย่างไรก็ตามโลหะผสมที่มีระดับสูงนั้นไม่ค่อยพบเห็น
การควบคุมความเร็ว (CS- 0.6m/s – 0.9m/s, 316L จำกัดที่ 1.2m/sec)
ถังกรดตามมาตรฐาน NACE SP0294
การฉีดสารป้องกันการเกาะติด |
การไฮโดรโปรเซสซิ่ง |
CS, 1Cr-1/2Mo, 2-1/4Cr-1Mo, 18Cr-8Ni SS, 316SS, 321, 347SS, 405/410SS, โลหะผสม 20, โลหะผสม 800/825, โมเนล 400 |
การโจมตีด้วยไฮโดรเจนที่อุณหภูมิสูง (HTHA), การซัลไฟด์โดยส่วนผสมของไฮโดรเจน-H2S, ความเสียหายจาก H2S เปียก, CSCC, การกัดกร่อนของกรดแนฟเทนิก, การกัดกร่อนของแอมโมเนียมไบซัลไฟด์ |
เลือกใช้วัสดุตาม API 941-HTHA
การควบคุมความเร็ว (สูงเพียงพอที่จะรักษาการกระจายของเหลว)
PWHT ตามมาตรฐาน ASME VIII / B31.3 |
การปฏิรูปตัวเร่งปฏิกิริยา |
1-1/4Cr-0.5Mo, 2-1/4Cr-0.5Mo, |
การแตกร้าวจากการคืบคลาน, HTHA, SSC-แอมโมเนีย, SSC-คลอไรด์, การเปราะของไฮโดรเจน, การกัดกร่อนของแอมโมเนียมคลอไรด์, การแตกร้าวจากการคืบคลาน |
การเลือกวัสดุตาม API 941-HTHA การควบคุมความแข็ง PWHT |
โคเกอร์ที่ล่าช้า |
1-1/4Cr-.0.5Mo หุ้มด้วยเหล็ก 410S หรือ 405SS, 5Cr-Mo หรือ 9Cr-Mo, 316L, 317L |
การกัดกร่อนของกำมะถันที่อุณหภูมิสูง การกัดกร่อนของกรดแนฟเทนิก การเกิดออกซิเดชัน/คาร์บูไรเซชัน/ซัลไฟด์ที่อุณหภูมิสูง การกัดกร่อนจากการกัดเซาะ การกัดกร่อนในน้ำ (HIC, SOHIC, SSC, แอมโมเนียมคลอไรด์/ไบซัลไฟต์, CSCC), CUI, ความเหนื่อยล้าจากความร้อน (วัฏจักรความร้อน) |
ลดความเครียดที่เกิดขึ้นให้เหลือน้อยที่สุด เหล็กกล้า Cr-Mo เนื้อละเอียด มีคุณสมบัติความเหนียวดี |
อะมีน |
ซีเอส+ซีเอ /
CS+ 316L แผ่นหุ้ม, 316SS |
การกัดกร่อนของ CO2 ความเสียหายจาก H2S เปียก การแตกร้าวจากการกัดกร่อนของความเครียดของอะมีน (ASCC) การกัดกร่อนของอะมีนในปริมาณมาก การกัดกร่อน (จากเกลือที่ทนความร้อนได้) |
ดูอะมีนในตารางที่ 6 |
การกู้คืนกำมะถัน
(หน่วยงานที่ได้รับใบอนุญาต) |
ซีเอส 310เอสเอส 321เอสเอส 347เอสเอส |
การเกิดซัลไฟด์ของเหล็กกล้าคาร์บอน ความเสียหาย/การแตกร้าวจาก H2S เปียก (SSC, HIC, SOHIC) การกัดกร่อนของกรดอ่อน |
การดำเนินงานท่อเหนืออุณหภูมิจุดน้ำค้างเพื่อหลีกเลี่ยงการกัดกร่อนรุนแรงของ CS
PWHT ของรอยเชื่อมเพื่อหลีกเลี่ยงการแตกร้าว การควบคุมความแข็ง
เหล็กทนทานต่อ HIC |
ไปป์ไลน์
วัสดุของท่อจะต้องเป็นไปตามข้อกำหนดวัสดุของท่อที่มีอยู่ของบริษัท วัสดุเริ่มต้นคือเหล็กกล้าคาร์บอน + ค่าเผื่อการกัดกร่อน ค่าเผื่อการกัดกร่อนจะต้องสูงที่สุดเท่าที่จะเป็นไปได้เพื่อพิจารณาการใช้งานที่เกินอายุการออกแบบ และจะพิจารณาเป็นรายกรณีในแต่ละโครงการ การเคลือบท่อจะระบุไว้ใน AGES-SP-07-002 ซึ่งเป็นข้อกำหนดการเคลือบท่อภายนอก
ขอแนะนำให้ใช้สารยับยั้งการกัดกร่อนในระบบท่อไฮโดรคาร์บอนที่มีน้ำควบแน่น และควรเป็นตัวเลือกเริ่มต้นสำหรับท่อใต้ทะเล เช่น CS + CA + สารยับยั้งการกัดกร่อน ควรพิจารณาเทคนิคการจัดการการกัดกร่อนเพิ่มเติม เช่น Pigging, CP เป็นต้น การเลือกและการประเมินสารยับยั้งการกัดกร่อนต้องเป็นไปตามขั้นตอนของบริษัท
การเลือกทางเลือก CRA สำหรับท่อต้องได้รับการประเมินอย่างละเอียดผ่านการวิเคราะห์ต้นทุนตลอดอายุการใช้งาน การพิจารณาต้นทุนสารเคมีและเทคนิคการจัดการการกัดกร่อน รวมถึงการขนส่งและจัดการสารเคมีจะต้องรวมอยู่ในการวิเคราะห์ รวมถึงข้อกำหนดการตรวจสอบด้วย
ท่อไฮโดรคาร์บอน
ผู้รับเหมาจะต้องเป็นผู้เลือกวัสดุสำหรับท่อตามข้อกำหนดในมาตรา 11 แนวทางการเลือกวัสดุสำหรับบริการต่างๆ ระบุไว้สำหรับทั้งสิ่งอำนวยความสะดวกต้นน้ำและปลายน้ำในตาราง 6 และ 7 ตามลำดับ การเชื่อมและเกณฑ์การยอมรับทั้งหมดจะต้องดำเนินการตามข้อกำหนดของ ASME B31.3 วัสดุสำหรับท่อจะต้องระบุโดยท่อตามข้อกำหนดวัสดุสำหรับท่อของ ADNOC AGES-SP-09-002
อาจจำเป็นต้องเลือกวัสดุเฉพาะและแยกกันสำหรับขาที่เสีย ในขณะที่อาจต้องใช้ CRA หรือ CRA cladding เพื่อควบคุมการกัดกร่อนในพื้นที่ที่มีการไหลนิ่ง อย่างไรก็ตาม การออกแบบท่อควรคำนึงถึงการหลีกเลี่ยงขาที่เสียเพื่อลดความน่าจะเป็นและความรุนแรงของการกัดกร่อน ในกรณีที่ไม่สามารถหลีกเลี่ยงขาที่เสียได้ ขอแนะนำให้เคลือบภายใน การกำหนดปริมาณสารยับยั้งและสารชีวฆ่า และการตรวจสอบการกัดกร่อนเป็นระยะๆ นอกจากนี้ยังใช้ได้กับอุปกรณ์แบบคงที่ด้วย
ในระหว่างการออกแบบ ควรระมัดระวังโดยเฉพาะอย่างยิ่งในด้านระเบียบวินัยของท่อ ไม่ให้สแตนเลสสัมผัสกับชิ้นส่วนที่เคลือบสังกะสี เพื่อหลีกเลี่ยงการเปราะบางจากสังกะสี ซึ่งเป็นปัญหาในอุณหภูมิที่สังกะสีสามารถแพร่กระจายได้ เช่น ในงานเชื่อม
ระบบสาธารณูปโภค
แนวทางการเลือกใช้วัสดุ: ตารางที่ 8 – แนวทางการเลือกใช้วัสดุสำหรับบริการสาธารณูปโภค
บริการ |
ตัวเลือกวัสดุ |
กลไกการเสียหาย |
การบรรเทาผลกระทบ |
เชื้อเพลิงก๊าซ |
ซีเอส 316เอสเอส |
หากก๊าซเชื้อเพลิงเปียก: การกัดกร่อนของ CO2 การเกิดหลุมคลอไรด์ CSCC ความเสียหายจาก H2S เปียก |
การเลือกใช้วัสดุ
ควบคุมเงื่อนไขการทำงานระหว่างการสตาร์ทเมื่ออาจใช้ก๊าซเชื้อเพลิงสำรองได้ |
ก๊าซเฉื่อย |
CS + ขั้นต่ำ CA |
สารปนเปื้อนทั่วไปจากผลิตภัณฑ์ก๊าซเชื้อเพลิง |
การเลือกใช้วัสดุ (ระดับการกัดกร่อนขึ้นอยู่กับก๊าซเฉื่อยที่ใช้ เช่น ก๊าซเชื้อเพลิงจากไอเสีย) |
น้ำมันดีเซล |
CS + CA, 316SS, CS + CA+ ซับใน
*เหล็กหล่อ |
ความเสี่ยงจากสารปนเปื้อน |
CS + Lining เหมาะกับถัง
*ปั๊มจะต้องเป็นเหล็กหล่อ |
เครื่องมือวัด/เครื่องตรวจวัดอากาศ |
CS ชุบสังกะสี 316 SS |
การกัดกร่อนในบรรยากาศ |
การกรองแบบควบคุม |
ไนโตรเจน |
CS ชุบสังกะสี 316SS |
ไม่มี การกัดกร่อนอาจมาจากการเข้ามาของ O2 ในระหว่างการดำเนินการคลุม |
อัพเกรดสเปกที่ทางเข้ามีโอกาสเข้าได้มากขึ้นหรือต้องการความสะอาด |
ไฮโปคลอไรต์ |
ซับใน CS + PTFE, C-PVC, C-276, Ti |
การกัดกร่อนตามรอยแยก, การเกิดออกซิเดชัน |
การเลือกใช้วัสดุ
การควบคุมอุณหภูมิ/การกำหนดปริมาณ |
น้ำเสีย |
316 SS, กองพัน |
การกัดกร่อนคลอไรด์, CSCC, การกัดกร่อน CO2, การกัดกร่อน O2, MIC |
การเลือกใช้วัสดุ |
น้ำจืด |
เคลือบอีพอกซี CS, CuNi, ทองแดง, ไม่ใช่โลหะ |
การกัดกร่อนของ O2, MIC |
การติดตามความสะอาด/การใช้สารชีวฆ่าหากไม่ได้ใช้กับน้ำดื่ม |
น้ำหล่อเย็น |
CS + CA, ไม่ใช่โลหะ |
การกัดกร่อนของน้ำหล่อเย็น |
การใช้สารกำจัด O2 และสารยับยั้งการกัดกร่อน
ระบบระบายความร้อนด้วยไกลคอลผสมน้ำที่สัมผัสกับส่วนประกอบ CS เป็นที่ทราบกันดีว่าทำให้เกิดการกัดกร่อน ควรผสมไกลคอลกับสารยับยั้งการกัดกร่อน |
น้ำทะเล |
CS + ซับใน, SDSS, โลหะผสม 625, Ti, CuNi, GRP |
การกัดกร่อนคลอไรด์, CSCC, การกัดกร่อนของ O2, การกัดกร่อนรอยแยก, MIC |
การเลือกใช้วัสดุ
การควบคุมอุณหภูมิ |
น้ำที่ผ่านการขจัดแร่ธาตุ |
เคลือบอีพ็อกซี CS, 316SS, ไม่ใช่โลหะ |
การกัดกร่อนของ O2 |
การเลือกใช้วัสดุ |
น้ำดื่ม |
วัสดุที่ไม่ใช่โลหะ (เช่น C-PVC/HDPE), Cu, CuNi, 316 SS |
ไมค์ |
ห้ามใช้ขั้วบวกเสียสละในระบบน้ำดื่ม |
สุรา |
CuNi, CS+3mmCA (ขั้นต่ำ) + การเคลือบภายใน, GRVE, GRE, HDPE |
การกัดกร่อนคลอไรด์, CSCC, การกัดกร่อนของ O2, การกัดกร่อนรอยแยก, MIC |
กลไกการกัดกร่อนขึ้นอยู่กับตัวกลางน้ำไฟ
ตัวเลือกที่ไม่ใช่โลหะต้องคำนึงถึงความเสี่ยงจากไฟไหม้ |
ท่อระบายน้ำเปิด |
ไม่ใช่โลหะ
CS + ซับในอีพอกซี |
การกัดกร่อนคลอไรด์, CSCC, การกัดกร่อนของ O2, การกัดกร่อนตามรอยแยก, MIC, การกัดกร่อนในบรรยากาศ |
ท่อจากภาชนะหุ้มจะต้องเป็น CRA |
ท่อระบายน้ำปิด |
CS + CA, 316SS, DSS, SDSS, CS +CRA หุ้ม |
การกัดกร่อนของ CO2 ความเสียหายจาก H2S เปียก CSCC การกัดกร่อนตามรอยแยก การกัดกร่อนของ O2 ASCC MIC |
การเลือกใช้วัสดุ |
ก๊าซเชื้อเพลิงจะถูกส่งมาในรูปแบบก๊าซแห้งจากปลายน้ำของคอลัมน์การคายน้ำ เช่น ก๊าซส่งออก หรือในรูปแบบก๊าซแรงดันต่ำที่แยกออกซึ่งยังไม่แห้งสนิท และอาจได้รับความร้อนเพื่อป้องกันการควบแน่นของน้ำในท่อส่ง
ก๊าซแห้งจะถูกขนส่งในท่อ CS ที่มี CA ที่กำหนดที่ 1 มม. และจะไม่ถูกยับยั้ง จะต้องวิเคราะห์อุณหภูมิการลดแรงดัน และหากต่ำกว่า -29 °C จะต้องระบุ CS ที่อุณหภูมิต่ำ ก๊าซเชื้อเพลิงที่ยังไม่แห้งควรได้รับการบำบัดในลักษณะเดียวกับก๊าซเปียกที่ผลิตได้ (อุณหภูมิต่ำกว่า 10 °C เหนือจุดน้ำค้าง) หากต้องการความสะอาด ควรระบุ 316 SS
ถือว่าไม่กัดกร่อน ดูตารางที่ 8
ถือว่าไม่กัดกร่อนและ CS เหมาะสม อย่างไรก็ตาม อาจมีสารปนเปื้อนอยู่บ้าง ขึ้นอยู่กับคุณภาพของน้ำมันดีเซล ในกรณีดังกล่าว ถังเก็บน้ำมันดีเซลที่ผลิตด้วย CS ที่มี CA 3 มม. จำเป็นต้องเคลือบภายในเพื่อป้องกันการกัดกร่อนและการตกตะกอนของผลิตภัณฑ์กัดกร่อนในน้ำมันดีเซล ซึ่งอาจรบกวนอุปกรณ์ได้ ควรเคลือบถังทั้งหมด เนื่องจากการควบแน่นบนพื้นผิวด้านบนอาจทำให้เกิดผลิตภัณฑ์กัดกร่อนได้เช่นกัน ทางเลือกอื่นคือใช้ถังที่ผลิตจากวัสดุที่ไม่ใช่โลหะ เช่น GRP
- เครื่องมือ/โรงงาน อากาศและไนโตรเจน
CS ชุบสังกะสีมักใช้กับระบบอากาศและไนโตรเจนคุณภาพสูงสำหรับท่อที่มีเส้นผ่านศูนย์กลางใหญ่ และ 316 SS สำหรับท่อที่มีเส้นผ่านศูนย์กลางเล็กกว่า แม้ว่าจะกัดกร่อนไม่ได้ก็ตาม ในกรณีที่อาจมีความชื้นเข้ามา หรือต้องการความสะอาดบริเวณปลายน้ำของตัวกรอง ควรพิจารณาใช้ 316 SS ในทุกกรณี ควรใช้ข้อต่อและข้อต่อ DSS
หากได้รับการบำบัด (ตามที่กำหนดไว้ในมาตรา 11.2) จะอนุญาตให้ใช้ CS ที่มี CA ได้ หากไม่ได้รับการบำบัด ควรอัปเกรดระบบน้ำจืดเป็น CRA ที่เหมาะสมหรือ CS ที่มีแผ่นปิด CRA
น้ำดื่มควรเก็บไว้ในถัง CS ที่มีการเคลือบภายในด้วยสารเคลือบที่เป็นที่ยอมรับตามมาตรฐานด้านสุขภาพหรือในถังที่ผลิตจาก GRP เมื่อใช้ถัง GRP ถังจะต้องเคลือบภายนอกเพื่อป้องกันแสงเข้าในถังและการเจริญเติบโตของสาหร่ายในน้ำที่เก็บไว้ เพื่อป้องกันไม่ให้สารเคลือบภายนอกเสื่อมสภาพ จะต้องระบุเกรดที่ทนต่อรังสี UV ท่อควรใช้วัสดุที่ไม่ใช่โลหะและท่อทองแดงธรรมดาหากมีเส้นผ่านศูนย์กลางที่เหมาะสม หรืออาจระบุ 316 SS เพื่อความสะอาดก็ได้
การเลือกใช้วัสดุสำหรับระบบน้ำทะเลนั้นขึ้นอยู่กับอุณหภูมิเป็นอย่างมาก และควรเลือกโดยอ้างอิงจาก ISO 21457 วัสดุที่แนะนำมีอยู่ในตารางที่ 8 ควรเลือกใช้ CS ที่มีซับในสำหรับระบบน้ำทะเลที่ผ่านการกำจัดอากาศเท่านั้น ตาม API 15LE และ NACE SP0304
สำหรับระบบน้ำดับเพลิงที่ใช้น้ำทะเลเป็นตัวกลาง โปรดดูที่ส่วนที่ 12.3.8
น้ำที่ผ่านการขจัดแร่ธาตุจะกัดกร่อน CS ดังนั้นระบบเหล่านี้จึงควรใช้ SS 316 สามารถเลือกวัสดุที่ไม่ใช่โลหะได้โดยรับข้อมูลจากผู้ผลิตวัสดุและได้รับการอนุมัติจากบริษัท ถังอาจเป็น CS ที่มี CA และซับในที่เหมาะสม
สำหรับระบบดับเพลิงที่มีของเหลวอยู่ถาวรส่วนใหญ่ซึ่งมีน้ำทะเลเป็นตัวกลาง วัสดุที่แนะนำให้ใช้คือ CuNi หรือไททาเนียม 90/10 (ดูตารางยูทิลิตี้ 8 ใน ISO 21457)
ระบบดับเพลิงอาจบรรจุน้ำจืดที่มีอากาศถ่ายเทได้ ท่อน้ำหลักที่อยู่เหนือพื้นดินอาจสร้างจากทองแดง 90/10CuNi และท่อน้ำหลักใต้ดินอาจสร้างจาก GRVE (Glass Reinforced Vinyl Esther) ซึ่งไม่จำเป็นต้องเคลือบหรือป้องกันแคโทดิก วาล์วขนาดใหญ่ควรเป็น CS พร้อมหุ้ม CRA สำหรับพื้นผิวที่เปียกภายในและขอบ CRA วาล์วที่สำคัญจะต้องผลิตจากวัสดุ CRA ทั้งหมด เพื่อหลีกเลี่ยงปัญหาการกัดกร่อนแบบกัลวานิก จะต้องระบุสปูลแยกเมื่อใดก็ตามที่จำเป็นต้องมีการแยกไฟฟ้าระหว่างวัสดุที่ไม่เหมือนกัน
วาล์วบรอนซ์ NiAl เข้ากันได้กับท่อ 90/10CuNi อย่างไรก็ตาม บรอนซ์ NiAl และ CuNi ไม่เหมาะกับน้ำที่ปนเปื้อนซัลไฟด์
การเลือกใช้วัสดุจะขึ้นอยู่กับคุณภาพของน้ำและอุณหภูมิของน้ำ โดยต้องคำนึงถึงอุณหภูมิของวัตถุดำในการออกแบบด้วย
ท่อเหล็กกล้าคาร์บอนเคลือบอีพอกซีภายในสำหรับระบบดับเพลิงต้องได้รับการอนุมัติจากบริษัท
วัสดุที่เลือกใช้สำหรับอุปกรณ์ท่อระบายน้ำแบบเปิดควรเป็น CS พร้อมซับใน คำแนะนำสำหรับท่อคือท่อที่ไม่ใช่โลหะที่เหมาะสมโดยรอการอนุมัติจากบริษัท หรืออาจระบุ CS ที่มี CA 6 มม. เมื่อระบบมีวิกฤตการณ์ต่ำ ถังระบายน้ำแบบเปิดควรมีซับในด้วยระบบเคลือบสารอินทรีย์ที่มีคุณสมบัติเหมาะสมและเสริมด้วยระบบป้องกันแคโทดิก
การเลือกวัสดุสำหรับท่อระบายน้ำแบบปิดจะต้องพิจารณาถึงสภาพของไฮโดรคาร์บอนที่มีศักยภาพภายในระบบ ในกรณีที่ท่อระบายน้ำแบบปิดได้รับไฮโดรคาร์บอนที่เป็นกรด จะต้องปฏิบัติตามข้อกำหนดสำหรับบริการที่เป็นกรด (ตามมาตรา 11.5) การออกแบบระบบการคลุมสำหรับถังและถังเก็บน้ำทั้งหมดจะต้องพิจารณาถึงความเป็นไปได้ของออกซิเจนที่ตกค้าง และจึงควรพิจารณาเลือกวัสดุด้วย
วาล์ว
การเลือกวัสดุสำหรับวาล์วต้องเหมาะสมกับประเภทของท่อที่จัดอยู่ในและเป็นไปตามข้อกำหนดของ ASME B16.34 รายละเอียดเพิ่มเติมเกี่ยวกับวัสดุของวาล์วสามารถดูได้ใน AGES-SP-09-003 ซึ่งเป็นข้อกำหนดวาล์วท่อและท่อส่ง
วาล์วสำหรับการใช้งานใต้ทะเลจะต้องเลือกตามมาตรฐาน API 6DSS โดยจะต้องเลือกวาล์วให้สอดคล้องกับข้อกำหนด ADNOC AGES-SP-09-003
อุปกรณ์คงที่
แนวทางวัสดุสำหรับภาชนะรับแรงดันมีอยู่ในตาราง 6 และ 7 ข้างต้น โดยทั่วไปจะเป็น CS ที่มีซับในหรือหุ้มด้วย CRA แนวทางการเลือกใช้ CS ที่มีหุ้มหรือ CRA แบบแข็งมีอยู่ในหัวข้อ 11.3 แต่ควรพิจารณาเป็นรายกรณี ข้อกำหนดการเชื่อมและการยอมรับจะต้องเป็นไปตาม ASME IX
หากเลือกใช้วัสดุสำหรับเรือที่มีสภาพเป็นกรด โปรดดูส่วนที่ 11.5 หากอยู่นอกเหนือขีดจำกัดของ NACE MR0175 / ISO 15156-3 สำหรับ 316 SS เรือจะต้องหุ้มภายใน/เชื่อมทับด้วย Alloy 625
ตามที่ระบุไว้ในมาตรา 11.6 การออกแบบและการเลือกวัสดุของเครื่องแลกเปลี่ยนความร้อนจึงขึ้นอยู่กับข้อกำหนดในการให้บริการ อย่างไรก็ตาม ในทุกกรณี วัสดุจะต้องเป็นไปตามหลักเกณฑ์เหล่านี้:
- วัสดุที่ต้องเลือกให้ตรงตามข้อกำหนดอายุการใช้งานของการออกแบบ
- การเลือกใช้วัสดุจะต้องขับเคลื่อนด้วยการออกแบบ
- ไททาเนียม ASTM B265 เกรด 2 เป็นเกรดที่แนะนำสำหรับการใช้งานเครื่องแลกเปลี่ยนความร้อนที่มีน้ำทะเลและไกลคอลในปริมาณมาก ควรพิจารณาศักยภาพในการไฮไดรด์ไททาเนียมในการออกแบบเครื่องแลกเปลี่ยนความร้อนไททาเนียมทั้งหมด โดยต้องแน่ใจว่าเงื่อนไขต่างๆ ไม่เกิน 80 °C ค่า pH ต่ำกว่า 3 หรือสูงกว่า 12 (หรือสูงกว่า 7 หากมีปริมาณ H2S สูง) และไม่มีกลไกสำหรับการสร้างไฮโดรเจน เช่น การจับคู่ไฟฟ้า
- โดยทั่วไปไม่ควรมี CA สำหรับ CS ในเครื่องแลกเปลี่ยนความร้อน ดังนั้นอาจต้องอัปเกรดคุณลักษณะให้เป็น CRA ที่เหมาะสม
- หากใช้ CuNi สำหรับท่อในรูปแบบเปลือกและท่อ จะต้องปฏิบัติตามความเร็วต่ำสุดและสูงสุดในตารางที่ 9 อย่างไรก็ตาม ค่าเหล่านี้จะเปลี่ยนแปลงไปตามเส้นผ่านศูนย์กลางท่อ และจะต้องออกแบบตามกรณีเป็นรายกรณี
แนวทางการเลือกวัสดุ: ตาราง 9 – ความเร็วการไหลสูงสุดและต่ำสุดสำหรับท่อแลกเปลี่ยนความร้อน CuNi
วัสดุของท่อ |
ความเร็ว (ม./วินาที) |
สูงสุด |
ขั้นต่ำ |
คิวนิ 90/10 |
2.4 |
0.9 |
คิวนิ 70/30 |
3.0 |
1.5 |
รายละเอียดเพิ่มเติมเกี่ยวกับการออกแบบสามารถดูได้ใน AGES-SP-06-003 ซึ่งเป็นข้อมูลจำเพาะของเครื่องแลกเปลี่ยนความร้อนแบบเปลือกและท่อ อุปกรณ์/ปั๊มแบบหมุน
ผู้รับเหมาจะต้องเลือกประเภทของวัสดุปั๊มตามกรณีสำหรับโครงการของบริษัทที่ใช้ AGES-SP-05-001 ซึ่งเป็นข้อกำหนดของปั๊มหอยโข่ง (API 610) ตารางที่ 10 ด้านล่างแสดงแนวทางในการเลือกประเภทของวัสดุสำหรับปั๊มต่อระบบ รายละเอียดวัสดุเพิ่มเติม รวมถึงเมื่อจำเป็นต้องอัปเกรดเป็นข้อกำหนดสำหรับเงื่อนไขการทำงานเฉพาะ สามารถดูได้ใน AGES-SP-05-001
แนวทางการเลือกวัสดุ: ตาราง 10 – การจำแนกประเภทวัสดุสำหรับปั๊ม
บริการ |
ชั้นวัสดุ |
ไฮโดรคาร์บอนเปรี้ยว |
เอส-5, เอ-8 |
ไฮโดรคาร์บอนที่ไม่กัดกร่อน |
เอส-4 |
ไฮโดรคาร์บอนกัดกร่อน |
เอ-8 |
คอนเดนเสท ไม่มีการเติมอากาศ |
เอส-5 |
คอนเดนเสท, เติมอากาศ |
ซี-6, เอ-8 |
โพรเพน บิวเทน ก๊าซปิโตรเลียมเหลว แอมโมเนีย เอทิลีน บริการอุณหภูมิต่ำ |
เอส-1, เอ-8 |
น้ำมันดีเซล น้ำมันเบนซิน แนฟทา น้ำมันก๊าด น้ำมันก๊าซ น้ำมันหล่อลื่นเบา ปานกลาง และหนัก น้ำมันเชื้อเพลิง สารตกค้าง น้ำมันดิบ แอสฟัลต์ น้ำมันดิบสังเคราะห์ |
เอส-1, เอส-6, ซี-6 |
ไซลีน, โทลูอีน, อะซิโตน, เบนซิน, เฟอร์ฟูรัล, เอ็มอีเค, คิวมีน |
เอส-1 |
ผลิตภัณฑ์น้ำมันที่มีสารประกอบกำมะถัน |
ซี-6, เอ-8 |
ผลิตภัณฑ์น้ำมันที่มีเฟสน้ำกัดกร่อน |
เอ-8 |
กำมะถันเหลว |
เอส-1 |
ซัลเฟอร์ไดออกไซด์เหลว แห้ง (สูงสุด 0.3% โดยน้ำหนัก H2O) มีหรือไม่มีไฮโดรคาร์บอน |
เอส-5 |
ซัลเฟอร์ไดออกไซด์ในน้ำ ทุกความเข้มข้น |
เอ-8 |
ซัลโฟเลน (ตัวทำละลายเคมีที่เป็นกรรมสิทธิ์ของเชลล์) |
เอส-5 |
สารตกค้างสั้นที่มีกรดแนฟเทนิก (ค่ากรดมากกว่า 0.5 มก. KOH/ก.) |
ซี-6, เอ-8 |
โซเดียมคาร์บอเนต |
ไอ-1 |
โซเดียมไฮดรอกไซด์ ความเข้มข้น < 20% |
เอส-1 |
ไกลคอล |
ระบุโดยผู้ให้ใบอนุญาต |
สารละลาย DEA, MEA, MDEA, TEA, ADIP หรือซัลฟินอลที่มี H2S หรือ CO2 มากกว่า 1% H2S |
เอส-5 |
DEA, MEA, MDEA, TEA, ADIP หรือสารละลายซัลฟินอล ไขมันที่มี CO2 น้อยกว่า 1% H2S หรือ ≥120 °C |
เอ-8 |
น้ำเดือดและน้ำแปรรูป |
ซี-6, เอส-5, เอส-6 |
น้ำป้อนหม้อไอน้ำ |
ซี-6, เอส-6 |
น้ำเสียและน้ำในถังไหลย้อน |
ซี-6, เอส-6 |
น้ำกร่อย |
เอ-8, ดี-2 |
น้ำทะเล |
กรณีต่อกรณี |
น้ำเปรี้ยว |
ดี-1 |
น้ำจืดมีอากาศ |
ซี-6 |
ระบายน้ำออกให้มีความเปรี้ยวเล็กน้อย ไม่เติมอากาศ |
เอ-8 |
ท่อและอุปกรณ์เครื่องมือ
โดยทั่วไปท่อขนาดเล็กที่มีเส้นผ่านศูนย์กลางน้อยกว่า 1' สำหรับงานเครื่องมือวัด ฉัน สารเคมี ฉัน ระบบน้ำมันหล่อลื่น/น้ำมันซีลจะต้องทำจากวัสดุ 904L หากไม่ได้ระบุไว้เป็นอย่างอื่น
ท่อ/อุปกรณ์ต่อท่อในบริการสาธารณูปโภคที่ไม่ต้องการการบำรุงรักษาที่เป็นพิษ (อากาศในเครื่องมือ น้ำมันไฮดรอลิก น้ำมันหล่อลื่น น้ำมันซีล ฯลฯ) สำหรับสิ่งอำนวยความสะดวกบนบก จะต้องเป็น 316L SS
สำหรับก๊าซตัวกลางกระบวนการที่มีบริการที่มีรสเปรี้ยว การใช้วัสดุ CRA (316L/ 6Mo / Inconel 825) สำหรับท่อเครื่องมือจะต้องเลือกให้เป็นไปตามขีดจำกัดวัสดุ NACE MR0175 / ISO 15156-3 โดยคำนึงถึงคลอไรด์ ความดันบางส่วนของ H2S ค่า pH และอุณหภูมิการออกแบบ หรือเป็นไปตาม NACE MR0103 / ISO 17495 สำหรับท่อเครื่องมือที่ใช้ในสภาพแวดล้อมการกลั่น
การเลือกวัสดุท่อเครื่องมือจะต้องพิจารณาถึงความเสี่ยงของการแตกร้าวจากการกัดกร่อนภายนอกที่เกิดจากคลอไรด์และความเสี่ยงของการกัดกร่อนเป็นหลุมและรอยแยกภายนอก โดยเฉพาะในสภาพแวดล้อมที่มีคลอไรด์ ดังนั้น ท่อเครื่องมือในโรงงานนอกชายฝั่ง (ไม่ว่าจะให้บริการแบบใดก็ตาม) ท่อ SS 316 เคลือบ PVC (หนา 2 มม.) ควรพิจารณาใช้ในสภาพแวดล้อมทางทะเลที่เปิดโล่งเป็นรายกรณี หรืออีกทางหนึ่ง ท่อ SS ออสเทนนิติก 6Mo ถือว่าเหมาะสมที่อุณหภูมิไม่เกิน 120 °C ในสภาพแวดล้อมทางทะเล โดยจะพิจารณาการใช้งานเป็นรายกรณี
การยึดน็อต
สลักเกลียวและน็อตทั้งหมดจะต้องมีใบรับรองตามมาตรฐาน EN 10204 ประเภท 3.1 ขึ้นไป และประเภท 3.2 สำหรับการใช้งานที่อุณหภูมิต่ำ
วัสดุที่ใช้ยึดสลักเกลียวต้องเป็นไปตามตารางยึดสลักเกลียวสำหรับโลหะเหล็ก ไม่ผสมโลหะผสม และมีโลหะผสม ซึ่งระบุไว้ในภาคผนวก 1– มาตรฐานวัสดุโลหะที่เลือก สามารถดูตาราง 11 ด้านล่างสำหรับยึดสลักเกลียวที่เหมาะสำหรับช่วงอุณหภูมิที่กำหนด
แนวทางการเลือกวัสดุ: ตาราง 11 – ข้อกำหนดวัสดุสำหรับช่วงอุณหภูมิการยึดสลักเกลียว
ช่วงอุณหภูมิ (องศาเซลเซียส) |
ข้อมูลจำเพาะของวัสดุ |
ข้อจำกัดด้านขนาด |
น็อต |
ถั่ว |
-100 ถึง +400 |
A320 เกรด L7 |
A194 เกรด 4/S3 หรือ เกรด 7/S3 |
≤ 65 |
A320 เกรด L43 |
A194 เกรด 7/S3 หรือ A194 เกรด 4/S3 |
< 100 |
-46 ถึง + 4004 |
A193 เกรด B7 |
A194 เกรด 2H |
ทั้งหมด |
-29 ถึง + 5404 |
A193 เกรด B161 |
A194 เกรด 7 |
ทั้งหมด |
-196/+ 540 |
A193 เกรด B8M2 |
A194 เกรด M/8MA3 |
ทั้งหมด |
หมายเหตุ:
- ไม่ควรใช้เกรดนี้กับอุปกรณ์ที่แช่น้ำตลอดเวลา เกรด B16 มีไว้สำหรับการใช้งานที่อุณหภูมิสูง นอกช่วงอุณหภูมิของเกรด B7
- ห้ามใช้สลักเกลียวและน็อตชนิด 316 ที่อุณหภูมิสูงกว่า 60°C หากสัมผัสกับน้ำเกลือเปียก
- ใช้ 8MA กับคลาส 1
- ขีดจำกัดอุณหภูมิที่ต่ำกว่านั้นขึ้นอยู่กับการตีความและจะต้องชี้แจงให้ชัดเจนสำหรับแต่ละ
วัสดุยึดแบบ CS และ/หรือโลหะผสมต่ำจะต้องชุบสังกะสีแบบจุ่มร้อนตามมาตรฐาน ASTM A153 หรือมีการป้องกันการกัดกร่อนที่เชื่อถือได้ในระดับเดียวกัน สำหรับบริการ LNG ต้องระมัดระวังอย่างยิ่งในกรณีที่ SS สัมผัสกับวัสดุชุบสังกะสี
สำหรับการใช้งานที่การละลายของชั้นสังกะสีหนาอาจทำให้สูญเสียแรงตึงของสลักเกลียว ควรใช้ฟอสเฟต สามารถใช้สลักเกลียวที่เคลือบด้วยโพลีเตตระฟลูออโรเอทิลีน (PTFE) เช่น Takecoat & Xylan หรือเทียบเท่าได้ แต่หากสลักเกลียวเหล่านี้ใช้การป้องกันแคโทดิก ควรใช้เฉพาะในกรณีที่มีการตรวจสอบความต่อเนื่องทางไฟฟ้าด้วยการวัดเท่านั้น ห้ามใช้สลักเกลียวที่ชุบแคดเมียม
หากสลักเกลียว น็อต และสเปเซอร์ภายนอกต้องได้รับการปกป้องด้วยสารเคลือบที่ไม่ใช่โลหะ จะต้องเคลือบด้วยสารเคลือบ PTFE ที่ผ่านการทดสอบการพ่นเกลือเป็นเวลา 6,000 ชั่วโมงในห้องปฏิบัติการของบุคคลที่สามที่ได้รับการรับรองมาตรฐาน ISO 17025 สำหรับการทดสอบเหล่านี้ ตัวอย่างจะต้องเก็บจากโรงงานผู้พ่นสี ไม่ใช่จากผู้ผลิตสี
การยึดด้วยสลักเกลียวสำหรับการเคลือบสารที่ไม่ใช่โลหะนั้นสามารถใช้ได้กับ:
- การเชื่อมต่อหน้าแปลนภายนอกทั้งหมด (ประกอบในโรงงานและในสนาม) รวมถึงการยึดหน้าแปลนแบบมีฉนวนที่อุณหภูมิใช้งานน้อยกว่า 200 °C
- การขันน็อตอุปกรณ์ที่ต้องถอดออกเพื่อการบำรุงรักษาและการตรวจสอบตามกำหนด การเคลือบที่ไม่ใช่โลหะบนการขันน็อตไม่สามารถทำได้กับ:
- งานยึดโครงสร้างทั้งหมด
- ตัวยึด/สลักเกลียวที่ใช้ในการประกอบส่วนประกอบต่างๆ ภายในแพ็คเกจของซัพพลายเออร์หรืออุปกรณ์มาตรฐานของผู้ผลิต ชุดมาตรฐานต่างๆ และเครื่องมือวัด ผู้รับเหมาจะต้องตรวจสอบการเคลือบมาตรฐานของซัพพลายเออร์/ผู้ผลิตว่าเหมาะสมตามกรณีเป็นรายกรณี
- ตัวยึดแบบโลหะผสม;
- โบลท์ฝาครอบและโบลท์ต่อมสำหรับวาล์ว;
- น็อตสำหรับต่อสายเป่าลมของตะแกรงกรอง
- สลักเกลียวสำหรับสินค้าเฉพาะทางท่อมาตรฐานของผู้ผลิต (กระจกมองเห็น เกจวัดระดับ และตัวเก็บเสียง)
วัสดุการยึดสลักเกลียวสำหรับการใช้งานที่มีกรดด่างจะต้องเป็นไปตามข้อกำหนดในตารางที่ 12
แนวทางการเลือกวัสดุ: ตาราง 12 – วัสดุยึดสลักเกลียวสำหรับงานที่มีกรด
เงื่อนไขการให้บริการ |
วัสดุ |
ข้อมูลจำเพาะของวัสดุ |
ความคิดเห็น |
น็อต |
ถั่ว |
อุณหภูมิปานกลางและสูง > -29 °C |
เหล็กอัลลอยด์ |
ASTM A193 เกรด B7M |
ASTM A194 เกรด 2, 2H, 2HM |
เนื่องจากอันตรายของการเปราะบางจากไฮโดรเจนที่เกิดจากการป้องกันแคโทดิก จึงจำเป็นต้องใช้สลักและน็อตที่มีความแข็งที่ควบคุมได้ ดังนั้นจึงระบุเกรด "M" ด้วย |
อุณหภูมิต่ำ (-100°C ถึง -29 °C) |
เหล็กอัลลอยด์ |
ASTM A320 เกรด L7M หรือ L43 |
ASTM A194 เกรด 4 หรือ 7 |
ระดับกลางและสูงถึง -50 °C |
DSS และ SDSS |
เอ เอส ที เอ 276; เอเอสทีเอ 479 |
เอ เอส ที เอ 194 |
|
ระดับกลางและสูงถึง -196 °C สำหรับการใช้งานแรงดันต่ำเท่านั้น |
ออสเทนนิติก SS (316) |
ASTM A193 B8M คลาส 1 (ผ่านการบำบัดด้วยสารละลายคาร์ไบด์และควบคุมความแข็งสูงสุด 22HRC) |
ASTM A194 เกรด 8M, 8MA (ควบคุมความแข็งได้สูงสุด 22HRC) |
|
ระดับกลางและสูงถึง -196 °C |
ซูเปอร์ออสเทนนิติก SS |
(6%Mo 254 สโม)
เอ เอส ที เอ 276 |
เอ เอส ที เอ 194 |
|
โลหะผสมนิกเกิล |
ASTM B164 ASTM B408 (Monel K-500 หรือ Incoloy 625, Inconel 718, Incoloy 925) |
โมเนล K-500 หรือ อินโคลอย 625, อินโคลอย 718, อินโคลอย 925 |
|
ข้อมูลจำเพาะของวัสดุ
มาตรฐานวัสดุที่ระบุไว้ในภาพวาด ใบสั่งซื้อ หรือเอกสารอื่นๆ จะต้องระบุไว้โดยครบถ้วนตามแนวทางที่กำหนดไว้ในมาตรา 10 11 และ 12 รวมถึงข้อกำหนดเพิ่มเติมทั้งหมดที่เกี่ยวข้องกับมาตรฐาน สำหรับวัสดุที่ระบุด้วยหมายเลขรหัสมาตรฐานวัสดุและอุปกรณ์ (MESC) จะต้องเป็นไปตามข้อกำหนดเพิ่มเติมที่ระบุไว้ในนั้นด้วย
ให้ใช้ฉบับล่าสุดของมาตรฐานวัสดุที่เลือก เนื่องจากฉบับล่าสุดนี้ (รวมทั้งฉบับแก้ไข) มีผลใช้บังคับเสมอ จึงไม่จำเป็นต้องแสดงปีที่ออกมาตรฐาน
ขีดจำกัดอุณหภูมิของโลหะ
ขีดจำกัดอุณหภูมิที่แสดงในตาราง A.1 แสดงถึงขีดจำกัดขั้นต่ำที่อนุญาตสำหรับอุณหภูมิเฉลี่ยผ่านหน้าตัดของวัสดุก่อสร้างในระหว่างการทำงานปกติ
ตาราง A.1 – ขีดจำกัดอุณหภูมิขั้นต่ำสำหรับท่อและอุปกรณ์เหล็ก
อุณหภูมิ (°ซ) |
รายการ |
วัสดุ |
สูงถึง -29 |
ระบบท่อ/อุปกรณ์ |
ซีเอส |
-29 ถึง -46 |
ระบบท่อ/อุปกรณ์ |
แอลทีซีเอส |
< -46 |
งานท่อ |
ออสเทนนิติก SS |
สูงถึง -60 |
ภาชนะรับความดัน |
LTCS (การเชื่อม WPQR ตัวอย่าง HAZ จะต้องได้รับการทดสอบแรงกระแทกที่อุณหภูมิต่ำสุดที่ออกแบบ เกณฑ์การยอมรับขั้นต่ำที่ 27J นอกจากนี้ จะต้องดำเนินการ LTCS พร้อม CTOD และการประเมินความสำคัญทางวิศวกรรม) |
< -60 |
ภาชนะรับความดัน |
ออสเทนนิติก SS |
-101°C ถึง -196°C |
งานท่อ/อุปกรณ์ |
เหล็กกล้าออสเทนนิติก SS/Ni พร้อมการทดสอบแรงกระแทก |
ควรสังเกตว่าขีดจำกัดอุณหภูมิที่ระบุไม่จำเป็นต้องยกเว้นการใช้งานวัสดุเกินกว่าขีดจำกัดเหล่านี้ โดยเฉพาะอย่างยิ่งสำหรับชิ้นส่วนที่ไม่กักเก็บแรงดัน เช่น ชิ้นส่วนภายในของคอลัมน์ แผ่นกั้นของเครื่องแลกเปลี่ยนความร้อน และโครงสร้างรองรับ
ขีดจำกัดอุณหภูมิสูงสุดจะแสดงไว้ในส่วนที่ 2, 3 และ 4 อุณหภูมิที่แสดงในวงเล็บ เช่น (+400) ถือเป็นอุณหภูมิที่ไม่ปกติสำหรับการใช้งานที่ระบุ แต่สามารถอนุญาตได้จากมุมมองของวัสดุ หากจำเป็น
ควรให้ความสนใจเป็นพิเศษกับคุณลักษณะและการใช้งานโลหะสำหรับการบริการที่อุณหภูมิต่ำ สำหรับการใช้งานที่อุณหภูมิต่ำ โปรดดูภาคผนวกของข้อกำหนด 'การเชื่อม NDE และการป้องกันการแตกแบบเปราะของภาชนะรับแรงดันและตัวแลกเปลี่ยนความร้อน' และ 'การเชื่อม NDE และการป้องกันการแตกแบบเปราะของท่อ'
หมวดหมู่ของโลหะ
ข้อกำหนดนี้ครอบคลุมถึงหมวดหมู่โลหะต่อไปนี้:
- โลหะเหล็ก – ไม่ผสมโลหะ
- โลหะเหล็ก – โลหะผสม
- โลหะที่ไม่ใช่เหล็ก
ในแต่ละหมวดหมู่จะมีการจัดการผลิตภัณฑ์ต่อไปนี้:
- แผ่น, แผ่นบาง และแถบ;
- ท่อและท่อ;
- ท่อ;
- ชิ้นส่วนโลหะตีขึ้นรูป หน้าแปลน และอุปกรณ์ประกอบ;
- การหล่อ;
- เหล็กเส้น เหล็กรูปพรรณ และลวด
ลำดับของวัสดุ
ลำดับของวัสดุในคอลัมน์ 'การกำหนด' ในหัวข้อที่ 2, 3 และ 4 โดยทั่วไปจะเป็นแบบที่หมายเลขถัดไประบุถึงวัสดุที่มีปริมาณและ/หรือจำนวนของธาตุโลหะผสมเพิ่มขึ้น
องค์ประกอบทางเคมี
ข้อกำหนดองค์ประกอบทางเคมีที่แสดงในส่วนที่ 2, 3 และ 4 เกี่ยวข้องกับการวิเคราะห์ผลิตภัณฑ์ องค์ประกอบเปอร์เซ็นต์ที่แสดงในส่วนที่ 2, 3 และ 4 เป็นตามมวล
ข้อจำกัดเพิ่มเติมเกี่ยวกับวัสดุ
จะต้องปฏิบัติตามข้อกำหนดต่อไปนี้ เว้นแต่จะได้รับการอนุมัติจากบริษัทสำหรับการเบี่ยงเบนดังกล่าว:
- ห้ามใช้เหล็กกล้าคาร์บอนเกรด 70 ยกเว้น SA-516 เกรด 70 (ขึ้นอยู่กับการอนุมัติของบริษัทสำหรับการใช้งานเฉพาะ เงื่อนไขที่บังคับใช้กับเกรด 65 และเงื่อนไขเพิ่มเติม a และ b ที่ระบุไว้ด้านล่าง) ASTM A350 LF2 (ตามที่ระบุ) และ ASTM A537 Cl.1 สำหรับถัง วัสดุหรือการใช้งานเกรด 70 อื่นๆ ต้องได้รับการอนุมัติจากบริษัท ยกเว้นการตีขึ้นรูปและการหล่อเหล็กกล้าคาร์บอนมาตรฐาน เช่น ASTM A105, A216 WCB, A350 LF2 และ A352 LCC
- ผู้ผลิตเหล็กจะจัดทำข้อมูลความสามารถในการเชื่อมสำหรับ SA-516 เกรด 70 ที่ใช้ในโครงการที่ประสบความสำเร็จก่อนหน้านี้
- เงื่อนไขการอบชุบด้วยความร้อน: ปกติแล้ว โดยไม่คำนึงถึง
- ปริมาณคาร์บอนเทียบเท่าและปริมาณคาร์บอนสูงสุดสำหรับส่วนประกอบเหล็กกล้าคาร์บอนทั้งหมดในบริการที่ไม่เป็นกรดจะต้องเป็นไปตามตารางต่อไปนี้:
ตาราง A.2 – ปริมาณคาร์บอนสูงสุดและค่าเทียบเท่าสำหรับส่วนประกอบเหล็ก
ส่วนประกอบ |
ปริมาณคาร์บอนสูงสุด (%) |
คาร์บอนเทียบเท่าสูงสุด (%) |
แผ่น แผ่นแถบ ท่อ อุปกรณ์ดัด ทนแรงดัน |
0.23% |
0.43% |
แผ่น แท่ง รูปทรงโครงสร้าง และส่วนประกอบอื่นๆ ที่ต้องเชื่อมโดยปราศจากแรงกด |
0.23% |
ไม่มีข้อมูล |
งานตีขึ้นรูปและงานหล่อที่มีแรงดัน |
0.25% |
0.43% |
หมายเหตุ:
- บริการและวัสดุต่างๆ ต้องมีข้อกำหนดเพิ่มเติมในการทำให้เป็นมาตรฐานและ/หรือข้อกำหนดเหล่านี้ครอบคลุมอยู่ในข้อมูลจำเพาะของอุปกรณ์และท่อ หรือโดยการอ้างอิงถึงข้อมูลจำเพาะ DGS-MW-004 'ข้อกำหนดด้านวัสดุและการผลิตสำหรับท่อเหล็กกล้าคาร์บอนและอุปกรณ์ในการใช้งานที่รุนแรง'
- วัสดุสเตนเลสสตีลที่คงสภาพทางเคมีทั้ง 300 ซีรีส์ที่จะใช้ในงานที่มีอุณหภูมิการทำงานสูงกว่า 425°C จะต้องได้รับการอบด้วยความร้อนเพื่อคงสภาพที่อุณหภูมิ 900°C เป็นเวลา 4 ชั่วโมง หลังการอบด้วยความร้อนด้วยสารละลาย
- ห้ามใช้แผ่นยางบุในกล่องน้ำของคอนเดนเซอร์พื้นผิวและตัวแลกเปลี่ยนอื่น ๆ เว้นแต่จะได้รับอนุมัติจากบริษัท
- ท่อสแตนเลสซีรีส์ 300 ไม่ควรใช้สำหรับการผลิตไอน้ำหรือการให้ความร้อนด้วยไอน้ำสูงเกินไป
- ห้ามใช้เหล็กหล่อในน้ำทะเล
- เมื่อใดก็ตามที่มีการระบุ 'SS' หรือ 'สแตนเลสสตีล' ในข้อมูลจำเพาะหรือเอกสารโครงการอื่นๆ โดยไม่อ้างอิงถึงเกรดที่เฉพาะเจาะจง จะหมายถึง 316L SS
- การทดแทนวัสดุ 9Cr-1Mo-V เกรด '91' สำหรับการใช้งานที่มีการระบุ 9Cr-1Mo เกรด '9' ไว้นั้นไม่ได้รับอนุญาต
- ท่อและอุปกรณ์ SS ทั้งหมด โดยเฉพาะ 316/316L และ 321 ที่ผ่านการรับรองทั้งสองแบบ จะต้องมีมาตรฐานเป็นแบบไร้รอยต่อจนถึง 6' NPS (ASTM A312) และแบบเชื่อมคลาส 1 สำหรับ 8' NPS ขึ้นไป (ASTM A358 คลาส 1)
วิธีการเลือกวัสดุ วัสดุที่ควรเลือก เหตุใดจึงควรเลือกวัสดุนี้ และคำถามอื่นๆ เหล่านี้ล้วนสร้างความกังวลให้กับเราเสมอมา แนวทางการเลือกวัสดุเป็นตัวช่วยที่ครอบคลุมซึ่งสามารถช่วยให้คุณเลือกท่อ อุปกรณ์ประกอบ หน้าแปลน วาล์ว ตัวยึด แผ่นเหล็ก แท่ง แถบ แท่งเหล็ก ชิ้นงานหล่อ และวัสดุอื่นๆ สำหรับโครงการของคุณได้อย่างถูกต้องและมีประสิทธิภาพ มาใช้แนวทางการเลือกวัสดุในการเลือกวัสดุที่เหมาะสมสำหรับคุณจากวัสดุโลหะที่มีธาตุเหล็กและไม่มีธาตุเหล็กสำหรับใช้งานในอุตสาหกรรมน้ำมันและก๊าซ ปิโตรเคมี การแปรรูปทางเคมี วิศวกรรมทางทะเลและนอกชายฝั่ง วิศวกรรมชีวภาพ วิศวกรรมเภสัช พลังงานสะอาด และสาขาอื่นๆ
แนวทางการเลือกวัสดุ: โลหะเหล็ก – ไม่ผสมโลหะ
แผ่น, แผ่นโลหะ และแถบ
การกำหนดชื่อ |
อุณหภูมิโลหะ (°C) |
เอส ที เอส ที |
หมายเหตุ |
ข้อกำหนดเพิ่มเติม |
แผ่นเหล็กกล้าคาร์บอนคุณภาพโครงสร้าง ชุบสังกะสี |
100 |
เอ 446 – เอ/จี 165 |
สำหรับการใช้งานทั่วไป |
C เนื้อหา 0.23% สูงสุด |
แผ่นเหล็กกล้าคาร์บอนคุณภาพโครงสร้าง |
(+350) |
เอ 283 – ซี |
สำหรับชิ้นส่วนที่ไม่กักเก็บแรงดันที่มีความหนาสูงสุด 50 มม. |
ถูกฆ่าหรือถูกฆ่ากึ่งตาย |
แผ่นเหล็กกล้าคาร์บอน (ฆ่าหรือกึ่งฆ่า) |
400 |
เอ 285 – ซี |
สำหรับชิ้นส่วนที่รักษาแรงดัน สำหรับความหนาสูงสุด 50 มม. (การใช้งานขึ้นอยู่กับการอนุมัติของบริษัทเฉพาะ) |
C เนื้อหา 0.23% สูงสุด |
แผ่นเหล็กกล้าคาร์บอน (Si-killed) – ความแข็งแรงต่ำ/ปานกลาง |
400 |
เอ 515 – 60/65 |
สำหรับชิ้นส่วนที่รักษาแรงดัน (การใช้งานขึ้นอยู่กับการอนุมัติของบริษัทเฉพาะ) |
C เนื้อหา 0.23% สูงสุด |
แผ่นเหล็ก C-Mn (Si-killed) – มีความแข็งแรงปานกลาง/สูง |
400 |
เอ 515 -70 |
สำหรับแผ่นท่อที่ไม่ได้เชื่อมกับเปลือกและ/หรือท่อ สำหรับแผ่นท่อที่ต้องเชื่อมกับเปลือก โปรดดู 8.4.3 |
|
แผ่นเหล็ก C-Mn (แบบฆ่าหรือกึ่งฆ่า) – มีความแข็งแรงสูง |
400 |
เอ 299 |
สำหรับชิ้นส่วนรักษาแรงดันและสำหรับแผ่นท่อที่จะเชื่อมกับท่อ |
ปริมาณ C สูงสุด 0.23% ปริมาณ Mn สูงสุด 1.30% |
เหล็กกล้า C-Mn เนื้อละเอียด – ความแข็งแรงต่ำ |
400 |
เอ 516 55/60, เอ 662 – เอ |
สำหรับชิ้นส่วนที่รักษาแรงดันแม้ในอุณหภูมิต่ำ |
ปริมาณ C สูงสุด 0.23% ระบุ V+Ti+Nb<0.15% |
เหล็กกล้า C-Mn เนื้อละเอียด – ความแข็งแรงปานกลาง |
400 |
เอ 516 – 65/70 |
สำหรับชิ้นส่วนที่รักษาแรงดันแม้ในอุณหภูมิต่ำ |
ปริมาณ C สูงสุด 0.23% ระบุ V+Ti+Nb<0.15% |
เหล็กกล้า C-Mn เนื้อละเอียด – ความแข็งแรงต่ำ (ปกติ) |
400 |
A 537 – ชั้น 1 |
สำหรับชิ้นส่วนที่รักษาแรงดันแม้ในอุณหภูมิต่ำ (การใช้งานขึ้นอยู่กับการอนุมัติเฉพาะ) |
ระบุ V+Ti+Nb<0.15% |
เหล็กกล้า C-Mn เนื้อละเอียด – มีความแข็งแรงสูงมาก (Q+T) |
400 |
A 537 – ชั้น 2 |
สำหรับชิ้นส่วนที่รักษาแรงดัน (ใช้ตามการอนุมัติเฉพาะ) |
ระบุ V+Ti+Nb<0.15% |
แผ่นและแถบเหล็กกล้าคาร์บอน |
— |
A1011/A1011M |
เพื่อวัตถุประสงค์ด้านโครงสร้าง |
|
แผ่นพื้นเหล็ก |
— |
เอ 786 |
เพื่อวัตถุประสงค์ด้านโครงสร้าง |
|
ท่อและท่อ
การกำหนดชื่อ |
อุณหภูมิโลหะ (°C) |
เอส ที เอส ที |
หมายเหตุ |
ข้อกำหนดเพิ่มเติม |
ท่อเหล็กกล้าคาร์บอนเชื่อมด้วยความต้านทานไฟฟ้า |
400 |
เอ 214 |
สำหรับอุปกรณ์ถ่ายเทความร้อนแบบไม่ได้เผา |
ต้องถูกฆ่า ต้องทำการทดสอบไฟฟ้าแบบไม่ทำลายตามมาตรฐาน ASTM A450 หรือเทียบเท่า นอกเหนือไปจากการทดสอบไฮโดรสแตติก |
ท่อเหล็กกล้าคาร์บอนดึงเย็นแบบไร้รอยต่อ |
400 |
เอ 179 |
สำหรับอุปกรณ์ถ่ายเทความร้อนแบบไม่ได้เผา |
จะถูกฆ่า เฉพาะสำหรับแอปพลิเคชัน ASME VIII – Div 1 เท่านั้น |
ท่อเหล็กกล้าคาร์บอนเชื่อมด้วยความต้านทานไฟฟ้า |
400 |
เอ 178 – เอ |
สำหรับท่อหม้อไอน้ำและซุปเปอร์ฮีตเตอร์ที่มีเส้นผ่านศูนย์กลางภายนอกสูงสุดถึง 102 มม. |
จะต้องดำเนินการทดสอบไฟฟ้าแบบไม่ทำลายตามมาตรฐาน ASTM A450 หรือเทียบเท่าควบคู่ไปกับการทดสอบไฮโดรสแตติก จะต้องถูกทำให้ตายหรือกึ่งตาย คุณสมบัติอุณหภูมิสูง (ความแข็งแรงผลผลิตตามมาตรฐาน ASME II ส่วน D) |
ท่อเหล็กกล้าคาร์บอนเชื่อมด้วยความต้านทานไฟฟ้า (Si-killed) |
400 |
เอ 226 |
สำหรับท่อหม้อไอน้ำและซุปเปอร์ฮีตเตอร์ที่แรงดันใช้งานสูงถึงและรวมถึงเส้นผ่านศูนย์กลางภายนอก 102 มม. |
จะต้องดำเนินการทดสอบไฟฟ้าแบบไม่ทำลายตามมาตรฐาน ASTM A450 หรือเทียบเท่าควบคู่ไปกับการทดสอบไฮโดรสแตติก คุณสมบัติอุณหภูมิสูง (ความแข็งแรงผลผลิตตามมาตรฐาน ASME II ส่วน D) |
ท่อเหล็กกล้าคาร์บอนไร้รอยต่อ (Si-killed) |
400 |
เอ 192 |
สำหรับเครื่องทำความเย็นอากาศ หม้อไอน้ำ และเครื่องทำความร้อนสูงที่แรงดันสูง |
จะต้องดำเนินการทดสอบไฟฟ้าแบบไม่ทำลายตามข้อกำหนดของวัสดุควบคู่ไปกับการทดสอบไฮโดรสแตติก คุณสมบัติอุณหภูมิสูง (ความแข็งแรงผลผลิตตาม ASME II ส่วน D) |
ท่อเหล็กกล้าคาร์บอนไร้รอยต่อ (Si-killed) |
400 |
A 334-6 (ไร้ตะเข็บ) |
สำหรับอุปกรณ์ถ่ายเทความร้อนแบบไม่ได้เผาที่ทำงานที่อุณหภูมิบริการต่ำ |
ปริมาณ C สูงสุด 0.23% จะต้องดำเนินการทดสอบไฟฟ้าแบบไม่ทำลายตามข้อกำหนดของวัสดุควบคู่ไปกับการทดสอบไฮโดรสแตติก |
ท่อเหล็กกล้าคาร์บอนไร้รอยต่อ (Si-killed) |
400 |
เกรด A-1 A210 |
สำหรับเครื่องทำความเย็นอากาศ หม้อไอน้ำ และเครื่องทำความร้อนสูงที่แรงดันสูง |
ปริมาณ C สูงสุด 0.23% สำหรับหม้อไอน้ำและเครื่องทำความร้อนสูงเกิน คุณสมบัติอุณหภูมิสูง (ความแข็งแรงผลผลิตต้องเป็นไปตามข้อกำหนดของ ASME II ส่วน D) |
ท่อ
การกำหนดชื่อ |
อุณหภูมิโลหะ (°C) |
เอส ที เอส ที |
หมายเหตุ |
ข้อกำหนดเพิ่มเติม |
ท่อเหล็กกล้าคาร์บอนไร้รอยต่อหรือเชื่อมด้วยอาร์ค |
400 |
API 5L-บี |
สำหรับท่อลมและน้ำเท่านั้น ท่อสังกะสีพร้อมข้อต่อเกลียวเท่านั้น |
ระบุท่อ API 5L-B แบบไร้รอยต่อพร้อมข้อต่อเกลียว NPT ชุบสังกะสีตามมาตรฐาน ASTM A53 ข้อ 17 ท่อไร้รอยต่อต้องผ่านการทำให้เป็นมาตรฐานหรือผ่านการอบร้อน ท่อ SAW ต้องผ่านการทำให้เป็นมาตรฐานหรือผ่านการชุบแข็งด้วยความร้อนหลังจากเชื่อม |
ท่อเหล็กกล้าคาร์บอนเชื่อมด้วยไฟฟ้า |
400 |
A 672 – C 65 ชั้น 32/22 |
สำหรับสายผลิตภัณฑ์ภายในแปลง สำหรับขนาดที่ใหญ่กว่า NPS 16 |
C เนื้อหา 0.23% สูงสุด |
ท่อเหล็กกล้าคาร์บอนไร้รอยต่อ |
400 |
เกรด ASTM A106 B |
สำหรับสายสาธารณูปโภคภายในส่วนใหญ่ มักไม่สามารถหาแบบไร้รอยต่อได้ในขนาดที่ใหญ่กว่า NPS 16 |
ปริมาณคาร์บอนสูงสุด 0.23% อาจเพิ่ม Mn เป็นสูงสุด 1.30% จะถูกฆ่าหรือถูกฆ่าแบบกึ่งฆ่า |
ท่อเหล็ก C-Mn ไร้รอยต่อ (Si-killed) |
400 |
แบบ 106-ข |
สำหรับท่อกระบวนการภายในส่วนใหญ่ รวมถึงไฮโดรคาร์บอน + ไฮโดรเจน ไฮโดรคาร์บอน + สารประกอบซัลเฟอร์ |
ปริมาณ C สูงสุด 0.23% อาจเพิ่ม Mn เป็นสูงสุด 1.30% |
ท่อเหล็ก C-Mn เนื้อละเอียดไร้รอยต่อ (Si-killed) |
(+400) |
A 333 – เกรด 1 หรือ 6 |
สำหรับสายกระบวนการที่อุณหภูมิใช้งานต่ำ มักไม่สามารถหาแบบไร้รอยต่อในขนาดที่ใหญ่กว่า NPS 16 ได้ |
ปริมาณ C สูงสุด 0.23% อาจเพิ่ม Mn เป็นสูงสุด 1.30% ระบุ V+Ti+Nb < 0.15% |
ท่อเหล็ก C-Mn เนื้อละเอียดเชื่อมด้วยไฟฟ้าฟิวชั่น (Si-killed) |
(+400) |
เอ 671 ซี 65 คลาส 32 |
สำหรับสายกระบวนการที่อุณหภูมิบริการปานกลางหรือต่ำที่มีขนาดใหญ่กว่า NPS 16 |
ปริมาณ C สูงสุด 0.23% อาจเพิ่ม Mn เป็นสูงสุด 1.30% ระบุ V+Ti+Nb < 0.15% |
ท่อเหล็กกล้าคาร์บอน |
— |
เอ 53 |
สำหรับใช้โครงสร้างเป็นราวจับเท่านั้น |
|
งานตีขึ้นรูป หน้าแปลน และอุปกรณ์ประกอบ
การกำหนด |
อุณหภูมิโลหะ (°C) |
เอส ที เอส ที |
หมายเหตุ |
เพิ่มข้อกำหนด |
อุปกรณ์ท่อเชื่อมชนเหล็กกล้าคาร์บอน |
400 |
A 234 – WPB หรือ WPBW |
สำหรับการใช้งานทั่วไป ขนาดสูงสุดถึง NPS 16 รวมถึงต้องไร้รอยต่อ ขนาดที่มากกว่า NPS 16 อาจเป็นแบบไร้รอยต่อหรือแบบเชื่อมก็ได้ |
ปริมาณคาร์บอนสูงสุด 0.23% อาจเพิ่ม Mn เป็นสูงสุด 1.30% ชุบแบบปกติหรือชุบแบบร้อน วัสดุแผ่นสำหรับ A 234 WPB-W เพื่อตอบสนองข้อกำหนดการใช้งานที่เป็นกรด: ปริมาณคาร์บอนสูงสุด 0.23% คาร์บอนเทียบเท่าสูงสุด 0.43 |
อุปกรณ์ท่อเชื่อมชนเหล็กกล้าคาร์บอน |
(+400) |
A 420 – WPL6 หรือ WPL6W |
สำหรับอุณหภูมิการใช้งานต่ำ ขนาดสูงสุดถึง NPS 16 รวมถึงต้องไร้รอยต่อ ขนาดที่มากกว่า NPS 16 อาจเป็นแบบไร้รอยต่อหรือแบบเชื่อมก็ได้ |
ปริมาณ C สูงสุด 0.23% อาจเพิ่ม Mn เป็นสูงสุด 1.30% |
เหล็กกล้าคาร์บอน |
400 |
เอ 105 |
สำหรับส่วนประกอบท่อต่างๆ เช่น หน้าแปลน ข้อต่อ วาล์ว และชิ้นส่วนอื่นๆ ที่ทำหน้าที่กักเก็บแรงดัน และยังรวมถึงแผ่นท่อที่จะเชื่อมกับเปลือกด้วย |
ปริมาณคาร์บอนสูงสุด 0.23% อาจเพิ่ม Mn เป็นสูงสุด 1.20% จะต้องได้รับการทำให้เป็นมาตรฐานใน H2S เปียก อะมีน โซดาไฟ และบริการ Criticality 1 การอบชุบด้วยความร้อนตามข้อกำหนด ASTM ตามคะแนน |
เหล็กกล้าคาร์บอน |
400 |
A 266 – ชั้น 2 |
สำหรับส่วนประกอบภาชนะรับแรงดันและอุปกรณ์รักษาแรงดันที่เกี่ยวข้อง รวมถึงแผ่นท่อ |
C เนื้อหา 0.25% สูงสุด |
เหล็กกล้าคาร์บอน-แมงกานีส |
(+400) |
A 350 – LF2 คลาส 1 |
สำหรับส่วนประกอบท่อต่างๆ รวมถึงหน้าแปลน ข้อต่อ วาล์ว และชิ้นส่วนอื่นๆ ที่รักษาแรงดันไว้ที่อุณหภูมิใช้งานต่ำ |
เนื้อหา C 0.23% สูงสุด ปกติแล้ว |
เหล็กกล้าคาร์บอน-แมงกานีส |
350 |
A 765 – เกรด II |
สำหรับส่วนประกอบภาชนะรับแรงดันและอุปกรณ์รักษาแรงดันที่เกี่ยวข้อง รวมถึงแผ่นท่อ ที่อุณหภูมิใช้งานต่ำ |
C เนื้อหา 0.23% สูงสุด |
การหล่อ
การกำหนด |
อุณหภูมิโลหะ (°C) |
เอส ที เอส ที |
หมายเหตุ |
เพิ่มข้อกำหนด |
เหล็กหล่อเทา |
300 |
A 48 – ชั้น 30 หรือ 40 |
สำหรับชิ้นส่วนที่ไม่กักเก็บแรงดัน (ภายใน) |
|
เหล็กหล่อเทา |
650 |
A 319 – ชั้น 2 |
สำหรับชิ้นส่วนที่ไม่กักเก็บแรงดัน (ภายใน) ที่อุณหภูมิสูง |
|
เหล็กหล่อเทา |
350 |
A 278 – ชั้น 40 |
สำหรับชิ้นส่วนรักษาแรงดันและท่อระบายความร้อน เหล็กหล่อไม่ควรใช้ในงานอันตรายหรือแรงดันเกิน 10 บาร์ |
|
เหล็กหล่อเหนียว |
400 |
เอ 395 |
สำหรับชิ้นส่วนรักษาแรงดันรวมถึงอุปกรณ์และวาล์ว |
ควรทำการตรวจสอบโลหะวิทยาตามมาตรฐาน ASTM A395 นอกเหนือไปจากการทดสอบแรงดึง |
เหล็กหล่อ |
(+400) |
A 216 – WCA, WCB* หรือ WCC |
สำหรับชิ้นส่วนที่รักษาแรงดัน |
*เนื้อหา C 0.25% สูงสุด |
เหล็กหล่อ |
(+400) |
A 352 – LCB* หรือ LCC |
สำหรับชิ้นส่วนที่รักษาแรงดันไว้ที่อุณหภูมิใช้งานต่ำ |
*เนื้อหา C 0.25% สูงสุด |
แท่ง, ส่วนและลวด
การกำหนด |
อุณหภูมิโลหะ (°C) |
เอส ที เอส ที |
หมายเหตุ |
เพิ่มข้อกำหนด |
เหล็กกล้าคาร์บอนแท่ง เหล็กรูปพรรณ และแผ่นเหยียบยกคุณภาพโครงสร้าง |
350 |
เอ 36 |
สำหรับวัตถุประสงค์โครงสร้างทั่วไป |
ปริมาณคาร์บอน 0.23% สูงสุด สำหรับสินค้าที่ไม่ได้เชื่อม และสำหรับสินค้าที่จะไม่เชื่อม อาจไม่ต้องคำนึงถึงข้อจำกัดเกี่ยวกับปริมาณคาร์บอน จะถูกฆ่าหรือฆ่ากึ่งหนึ่ง |
เหล็กกล้าคาร์บอนต่ำ |
400 |
A 576 – 1022 หรือ 1117 |
สำหรับชิ้นส่วนที่ผ่านการกลึง |
เป็นแบบฆ่าหรือกึ่งฆ่า หากต้องการคุณภาพการกลึงแบบอิสระ ให้ระบุเกรด 1117 |
เหล็กกล้าคาร์บอนปานกลาง |
400 |
เอ 576 – 1035, 1045, 1055, 1137 |
สำหรับชิ้นส่วนที่ผ่านการกลึง |
เป็นแบบฆ่าหรือกึ่งฆ่า หากต้องการคุณภาพการกลึงแบบอิสระ ให้ระบุเกรด 1137 |
เหล็กกล้าคาร์บอนสูง |
230 |
เอ 689/เอ 576 – 1095 |
สำหรับสปริง |
ถูกฆ่าหรือถูกฆ่ากึ่งตาย |
ลวดเหล็กคุณภาพสปริงดนตรี |
230 |
เอ 228 |
สำหรับสปริง |
|
เหล็กกล้าคาร์บอนแท่งและส่วนต่างๆ |
(+230) |
เอ 36 |
สำหรับการยกห่วง, แถบเลื่อน ฯลฯ |
ปริมาณ C สูงสุด 0.23% สำหรับสินค้าที่ไม่ได้เชื่อม และสำหรับสินค้าที่จะไม่เชื่อม อาจไม่ต้องคำนึงถึงข้อจำกัดเกี่ยวกับปริมาณ C |
ลวดเชื่อมเหล็ก ผ้า |
— |
— |
|
|
ท่อโครงสร้างเหล็กกล้าคาร์บอน |
— |
เอ 500 |
สำหรับการใช้โครงสร้างเท่านั้น |
|
เหล็กเส้น |
— |
เอ 615 |
สำหรับการเสริมแรงคอนกรีต |
|
การยึดน็อต
การกำหนด |
อุณหภูมิโลหะ (°C) |
เอส ที เอส ที |
หมายเหตุ |
เพิ่มข้อกำหนด |
น็อตเหล็กกล้าคาร์บอน |
230 |
เอ 307 – บี |
สำหรับวัตถุประสงค์เชิงโครงสร้าง คุณภาพการตัดเฉือนฟรีที่ได้รับการรับรองเป็นที่ยอมรับ |
|
น็อตเหล็กกล้าคาร์บอน |
230 |
เอ 563 – เอ |
สำหรับสลักเกลียวตามที่กำหนดภายใต้ 8.7.1 |
|
น็อตเหล็กกล้าคาร์บอนปานกลาง |
450 |
เอ 194 – 2เอช |
สำหรับการยึดด้วยสลักเกลียวตามที่กำหนดภายใต้ 8.7.1 |
|
สลักเกลียวโครงสร้างที่มีความแข็งแรงสูง |
— |
แอสทาม F3125 |
เพื่อวัตถุประสงค์ด้านโครงสร้าง |
|
น็อตโครงสร้างเหล็กผ่านการอบด้วยความร้อน |
— |
เอ 490 |
เพื่อวัตถุประสงค์ด้านโครงสร้าง |
|
แหวนรองเหล็กกล้าชุบแข็ง |
— |
เอฟ 436 |
เพื่อวัตถุประสงค์ด้านโครงสร้าง |
|
แผ่น, แผ่นและแถบ
การกำหนด |
อุณหภูมิโลหะ (°C) |
เอส ที เอส ที |
หมายเหตุ |
เพิ่มข้อกำหนด |
แผ่นเหล็ก 1 Cr – 0.5 Mo |
600 |
A387 – 12 ชั้น 2 |
สำหรับอุณหภูมิการให้บริการที่สูงและ/หรือความต้านทานต่อการโจมตีของไฮโดรเจน |
กำหนดให้เป็นปกติและอบอ่อน หรือ ดับและอบอ่อน |
แผ่นเหล็ก 1.25 Cr – 0.5 Mo |
600 |
A 387 – 11 ชั้น 2 |
สำหรับอุณหภูมิการให้บริการที่สูงและ/หรือความต้านทานต่อการโจมตีของไฮโดรเจน |
ระบุว่าจะต้องทำให้เป็นมาตรฐานและอบอ่อนหรือดับและอบอ่อน ระบุค่าสูงสุด P 0.005% แผ่นจะต้องอบอ่อนด้วยสารละลาย |
แผ่นเหล็ก 2.25 Cr – 1 Mo |
625 |
A 387 – 22 ชั้น 2 |
สำหรับอุณหภูมิการให้บริการที่สูงและ/หรือความต้านทานต่อการโจมตีของไฮโดรเจน |
กำหนดให้เป็นปกติและอบอ่อน หรือ ดับและอบอ่อน |
แผ่นเหล็ก 3 Cr – 1 Mo |
625 |
A 387 – 21 ชั้น 2 |
สำหรับอุณหภูมิในการให้บริการที่สูง จำเป็นต้องมีความต้านทานการไหลหนืดและ/หรือความต้านทานต่อการโจมตีของไฮโดรเจนในระดับที่เหมาะสม |
กำหนดให้เป็นปกติและอบอ่อน หรือ ดับและอบอ่อน |
แผ่นเหล็ก 5 Cr – 0.5 Mo |
650 |
A 387 – 5 ชั้น 2 |
สำหรับอุณหภูมิการให้บริการที่สูงและ/หรือความต้านทานต่อการกัดกร่อนของกำมะถัน |
ระบุว่าจะต้องผ่านกระบวนการทำให้เป็นมาตรฐานและอบอ่อน หรือผ่านการดับและอบอ่อน แผ่นโลหะจะต้องผ่านการอบอ่อนด้วยสารละลาย |
แผ่นเหล็ก Ni 3.5 |
(+400) |
เอ 203 – ดี |
สำหรับชิ้นส่วนที่รักษาแรงดันไว้ที่อุณหภูมิใช้งานต่ำ |
ระบุ: C 0.10% สูงสุด, Si 0.30% สูงสุด, P 0.002% สูงสุด, S 0.005% สูงสุด |
แผ่นเหล็ก Ni 9 |
-200 |
เอ 353 |
สำหรับชิ้นส่วนที่รักษาแรงดันไว้ที่อุณหภูมิใช้งานต่ำ |
ระบุ: C 0.10% สูงสุด, Si 0.30% สูงสุด, P 0.002% สูงสุด, S 0.005% สูงสุด |
เหล็กแผ่น 13Cr แผ่นและแถบ |
540 |
A 240 – ประเภท 410S หรือ 405 |
สำหรับการหุ้มชิ้นส่วนที่กักเก็บแรงดันภายใต้สภาวะกัดกร่อนบางประเภท ห้ามใช้ประเภท 405 ที่อุณหภูมิสูงกว่า 400°C |
|
แผ่นเหล็ก 18 Cr-8 Ni แผ่นและแถบ |
-200 (+400) |
A 240 – ประเภท 304 หรือ 304N |
สำหรับชิ้นส่วนที่ไม่เชื่อมและคงแรงดันไว้ที่อุณหภูมิใช้งานต่ำหรือเพื่อป้องกันการปนเปื้อนของผลิตภัณฑ์ |
วัสดุจะต้องผ่านการทดสอบการกัดกร่อนตามขอบเกรน Practice E ที่ระบุใน ASTM A262 แผ่นเหล็กต้องผ่านการอบด้วยสารละลาย |
แผ่นเหล็ก 18 Cr-8 Ni แผ่นและแถบ |
-0.4 |
A 240 – ประเภท 304L |
สำหรับชิ้นส่วนที่รักษาแรงดันภายใต้สภาวะการกัดกร่อนบางอย่าง และ/หรืออุณหภูมิการใช้งานที่ต่ำและปานกลาง |
วัสดุจะต้องสามารถผ่านการทดสอบการกัดกร่อนตามเกรน Practice E ตามที่กำหนดไว้ใน ASTM A262 |
แผ่นเหล็ก 18 Cr-8 Ni แผ่นและแถบ |
(-100) / +600 |
A 240 – แบบ 321 หรือ 347 |
สำหรับชิ้นส่วนที่รักษาแรงดันภายใต้สภาวะการกัดกร่อนบางประการ และ/หรืออุณหภูมิการให้บริการที่สูง |
หากต้องการความทนทานต่อการกัดกร่อนระหว่างเม็ดเกรนอย่างเหมาะสมที่สุดเมื่ออุณหภูมิในการทำงานอยู่ที่ >426°C ให้ใช้การอบชุบด้วยความร้อนเพื่อคงสภาพที่อุณหภูมิ 900°C เป็นเวลา 4 ชั่วโมง หลังจากนั้นจึงใช้การอบชุบด้วยความร้อนด้วยสารละลาย วัสดุจะต้องผ่านการทดสอบการกัดกร่อนระหว่างเม็ดเกรน Practice E ตามที่ระบุไว้ใน ASTM A262 |
แผ่นเหล็ก แผ่น และแถบ 18 Cr-10 Ni-2 Mo |
-0.4 |
A 240 – ประเภท 316 หรือ 316L |
สำหรับชิ้นส่วนที่รักษาแรงดันภายใต้สภาวะการกัดกร่อนบางประการ และ/หรืออุณหภูมิการให้บริการที่สูง |
ต้องใช้ประเภท 316L สำหรับชิ้นส่วนที่เชื่อมทั้งหมด วัสดุจะต้องผ่านการทดสอบการกัดกร่อนตามเกรน Practice E ตามที่ระบุไว้ใน ASTM A262 แผ่นเหล็กจะต้องผ่านการอบด้วยสารละลาย |
แผ่นเหล็กแผ่นและแถบที่ปรับเสถียรด้วย 18 Cr-10 Ni-2 Mo |
(-200) / +500 |
A 240 – ประเภท 316Ti หรือ 316Cb |
สำหรับชิ้นส่วนที่รักษาแรงดันภายใต้สภาวะการกัดกร่อนบางประการ และ/หรืออุณหภูมิการให้บริการที่สูง |
เพื่อให้ทนทานต่อการกัดกร่อนระหว่างเม็ดเกรนได้ดีที่สุด ควรระบุการอบด้วยความร้อนเพื่อรักษาเสถียรภาพที่อุณหภูมิ 900°C เป็นเวลา 4 ชั่วโมง หลังจากอบด้วยความร้อนด้วยสารละลาย วัสดุจะต้องผ่านการทดสอบการกัดกร่อนระหว่างเม็ดเกรน Practice E ตามที่ระบุไว้ใน ASTM A262 |
แผ่นเหล็ก แผ่น และแถบ 18 Cr-10 Ni-3 Mo |
(-200) / +500 |
A 240 – ประเภท 317 หรือ 317L |
สำหรับชิ้นส่วนที่รักษาแรงดันภายใต้สภาวะการกัดกร่อนบางประการ และ/หรืออุณหภูมิการให้บริการที่สูง |
วัสดุจะต้องสามารถผ่านการทดสอบการกัดกร่อนตามเกรน Practice E ตามที่กำหนดไว้ใน ASTM A262 |
แผ่นเหล็ก 25 Cr-20 Ni แผ่นและแถบ |
1000 |
A 240 – ประเภท 310S |
สำหรับชิ้นส่วนที่รักษาแรงดันภายใต้สภาวะการกัดกร่อนบางประเภทและ/หรืออุณหภูมิการใช้งานที่รุนแรง |
|
แผ่นเหล็ก 18 Cr-8 Ni แผ่นและแถบ |
700 |
A 240 – แบบ 304H |
สำหรับชิ้นส่วนที่รักษาแรงดันในอุณหภูมิการใช้งานที่รุนแรงภายใต้สภาวะกัดกร่อนบางประการ |
ระบุ C 0.06% สูงสุด และ Mo+Ti+Nb 0.4% สูงสุด |
แผ่นเหล็ก 22 Cr-5 Ni-Mo-N แผ่นและแถบ |
(-30) / +300 |
เอ 240 – S31803 |
สำหรับชิ้นส่วนที่รักษาแรงดันภายใต้สภาวะกัดกร่อนบางประเภท |
ระบุ N 0.15% ขั้นต่ำ ระบุการทดสอบเฟอร์ริกคลอไรด์ตาม ASTM G 48 วิธี A แผ่นโลหะต้องได้รับการอบด้วยความร้อนด้วยสารละลายและระบายความร้อนด้วยน้ำ |
แผ่นเหล็ก 25 Cr-7 Ni-Mo-N แผ่นและแถบ |
(-30) / +300 |
เอ 240 – S32750 |
สำหรับชิ้นส่วนที่รักษาแรงดันภายใต้สภาวะกัดกร่อนบางประเภท |
ระบุการทดสอบเฟอร์ริกคลอไรด์ตาม ASTM G 48 วิธี A แผ่นที่ต้องได้รับการอบด้วยความร้อนด้วยสารละลายและระบายความร้อนด้วยน้ำ |
แผ่นเหล็ก แผ่น และแถบ 20 Cr-18 Ni-6 Mo-Cu-N |
-0.5 |
เอ 240 – S31254 |
สำหรับชิ้นส่วนที่รักษาแรงดันภายใต้สภาวะกัดกร่อนบางประเภท |
แผ่นเหล็กที่ต้องผ่านการอบด้วยความร้อนและระบายความร้อนด้วยน้ำ |
แผ่นเหล็กกล้าคาร์บอนหรือเหล็กกล้าผสมต่ำพร้อมแผ่นหุ้มสแตนเลสเฟอร์ริติก |
— |
เอ 263 |
สำหรับอุณหภูมิการให้บริการที่สูงและ/หรือสภาวะการกัดกร่อนบางประการ |
ระบุโลหะพื้นฐานและวัสดุหุ้ม |
แผ่นเหล็กกล้าคาร์บอนหรือเหล็กกล้าผสมต่ำพร้อมแผ่นหุ้มสเตนเลสออสเทนนิติก |
400 |
เอ 264 |
สำหรับอุณหภูมิการใช้งานที่สูงและ/หรือสภาวะกัดกร่อนบางประเภท ระบุโลหะพื้นฐานและวัสดุหุ้ม |
|
ท่อเหล็ก 25Cr – 5 Ni Mo-N ไร้รอยต่อสำหรับงานกัดกร่อนบางประเภท |
|
|
ต้องผ่านการอบอ่อนและระบายความร้อนด้วยน้ำ ต้องผ่านกระบวนการทำให้เฉื่อยทางเคมี ระบุการทดสอบเฟอร์ริกคลอไรด์ตามวิธี ASTM G 48 |
|
ท่อและท่อ
การกำหนดชื่อ |
อุณหภูมิโลหะ (°C) |
เอส ที เอส ที |
หมายเหตุ |
ข้อกำหนดเพิ่มเติม |
ท่อเหล็กไร้รอยต่อ 1Cr-0.5Mo |
600 |
เอ 213 – ที 12 |
สำหรับหม้อไอน้ำ ซุปเปอร์ฮีตเตอร์ และอุปกรณ์ถ่ายเทความร้อนที่ไม่ผ่านการเผาไหม้ที่อุณหภูมิใช้งานสูงและ/หรือต้องทนทานต่อการโจมตีของไฮโดรเจน |
ระบุว่าจะต้องผ่านกระบวนการทำให้เป็นมาตรฐานและอบคืนตัว หรือผ่านการดับและอบคืนตัว สำหรับความต้านทานต่อการโจมตีของไฮโดรเจน โปรดดู API 941 |
ท่อเหล็กไร้รอยต่อ 1.25 Cr-0.5 Mo |
600 |
เอ 213 – ที 11 |
สำหรับหม้อไอน้ำ ซุปเปอร์ฮีตเตอร์ และอุปกรณ์ถ่ายเทความร้อนที่ไม่ผ่านการเผาไหม้ที่อุณหภูมิใช้งานสูงและ/หรือต้องทนทานต่อการโจมตีของไฮโดรเจน |
กำหนดให้เป็นปกติและอบคืนตัวหรือดับและอบคืนตัว ระบุ P 0.005% สูงสุด |
ท่อเหล็กไร้รอยต่อ 2.25 Cr-1 Mo |
625 |
เอ 213 – ที 22 |
สำหรับหม้อไอน้ำ เตาเผา เครื่องทำความร้อนสูง และอุปกรณ์ถ่ายเทความร้อนแบบไม่เผาที่อุณหภูมิใช้งานสูง ซึ่งต้องมีคุณสมบัติต้านทานการไหลหนืดและ/หรือต้านทานการโจมตีของไฮโดรเจนอย่างเหมาะสม |
กำหนดให้เป็นปกติและอบอ่อน หรือ ดับและอบอ่อน |
ท่อเหล็กไร้รอยต่อ 5 Cr-0.5 Mo |
650 |
เอ 213 – ที 5 |
สำหรับอุณหภูมิการให้บริการที่สูง และ/หรือความต้านทานต่อการกัดกร่อนของกำมะถัน เช่น ท่อเตาเผา |
กำหนดให้เป็นปกติและอบอ่อน หรือ ดับและอบอ่อน |
ท่อเหล็กไร้รอยต่อ 9 Cr-1 Mo |
650 |
เอ 213 – ที 9 |
สำหรับอุณหภูมิการให้บริการที่สูง และ/หรือความต้านทานต่อการกัดกร่อนของกำมะถัน เช่น ท่อเตาเผา |
กำหนดให้เป็นปกติและอบอ่อน หรือ ดับและอบอ่อน |
ท่อเหล็ก 3.5 Ni ไร้รอยต่อ |
(+400) |
– |
สำหรับอุณหภูมิบริการต่ำ |
– |
ท่อเหล็ก Ni 9 ไร้รอยต่อ |
-200 |
– |
สำหรับอุณหภูมิบริการต่ำ |
– |
ท่อเหล็ก 12Cr ไร้รอยต่อ |
540 |
A 268 – TP 405 หรือ 410 |
สำหรับอุปกรณ์ถ่ายเทความร้อนที่ไม่ถูกเผาภายใต้สภาวะกัดกร่อนบางประการ |
ห้ามใช้ TP 405 ที่อุณหภูมิสูงกว่า 400°C TP 410 จะต้องระบุค่า C สูงสุด 0.08 |
ท่อเหล็ก 18 Cr-10 N-2Mo ไร้รอยต่อและเชื่อม |
(-200) +500 |
A 269 – TP 316 หรือ TP 316L หรือ TP 317 หรือ TP 317L |
สำหรับการใช้งานทั่วไปบางประเภท |
สำหรับท่อที่ออกแบบมาเพื่อใช้กับอุปกรณ์อัด ความแข็งจะต้องไม่เกิน 90 HRB สำหรับท่อที่ต้องเชื่อม ดัด หรือคลายความเค้น ควรใช้ TP316L หรือ TP 317L |
ท่อเหล็ก 18 Cr-8 Ni เชื่อม |
-200 (+400) |
A 249 – TP 304 หรือ TP 304L |
สำหรับเครื่องทำความร้อนสูงพิเศษและอุปกรณ์ถ่ายเทความร้อนแบบไม่ใช้ไฟเพื่อป้องกันการปนเปื้อนของผลิตภัณฑ์หรือสำหรับอุณหภูมิบริการต่ำ |
เนื่องจากท่อถูกเชื่อมโดยไม่เติมโลหะเติม ดังนั้นเส้นผ่านศูนย์กลางภายในและความหนาของผนังท่อจะต้องถูกจำกัดไว้ที่สูงสุด NPS 4 และสูงสุด 5.5 มม. ตามลำดับ |
ท่อเหล็กเชื่อม 18 Cr-8 Ni ที่ได้รับการเสริมความแข็งแรง |
(-100) +600 |
A 249 – TP 321 หรือ TP 347 |
สำหรับเครื่องทำความร้อนสูงเกินและอุปกรณ์ถ่ายเทความร้อนที่ไม่ผ่านการเผาไหม้ภายใต้สภาวะกัดกร่อนบางประการ |
เนื่องจากท่อถูกเชื่อมโดยไม่เติมโลหะเติม ดังนั้นเส้นผ่านศูนย์กลางภายในและความหนาของผนังท่อจะต้องถูกจำกัดไว้ที่สูงสุด NPS 4 และสูงสุด 5.5 มม. ตามลำดับ
ควรดำเนินการทดสอบไฟฟ้าแบบไม่ทำลายตามมาตรฐาน ASTM A450 นอกเหนือไปจากการทดสอบไฮโดรสแตติก
วัสดุจะต้องสามารถผ่านการทดสอบการกัดกร่อนตามเกรน Practice E ตามที่กำหนดไว้ใน ASTM A262 |
ท่อเหล็กเชื่อม 18 Cr-10 Ni-2 Mo |
300 |
A 249 – TP 316 หรือ TP 316L |
สำหรับเครื่องทำความร้อนสูงเกินและอุปกรณ์ถ่ายเทความร้อนที่ไม่ผ่านการเผาไหม้ภายใต้สภาวะกัดกร่อนบางประการ |
เนื่องจากท่อเชื่อมโดยไม่เติมโลหะเติม เส้นผ่านศูนย์กลางภายในและความหนาของผนังท่อจึงควรจำกัดไว้ที่ NPS 4 สูงสุดและ 5.5 มม. ตามลำดับ จะต้องดำเนินการทดสอบไฟฟ้าแบบไม่ทำลายตามมาตรฐาน ASTM A450 นอกเหนือไปจากการทดสอบไฮโดรสแตติก วัสดุจะต้องผ่านการทดสอบการกัดกร่อนตามเกรน Practice E ตามที่ระบุไว้ใน ASTM A262 |
เชื่อมท่อเหล็ก 20 Cr-18 Ni-6 Mo Cu-N |
(-200) (+400) |
เอ 249 – S31254 |
สำหรับเครื่องทำความร้อนสูงเกินและอุปกรณ์ถ่ายเทความร้อนที่ไม่ผ่านการเผาไหม้ภายใต้สภาวะกัดกร่อนบางประการ |
เนื่องจากท่อเชื่อมโดยไม่เติมโลหะเติม เส้นผ่านศูนย์กลางภายในและความหนาของผนังท่อจึงควรจำกัดไว้ที่ NPS 4 สูงสุดและ 5.5 มม. ตามลำดับ ควรดำเนินการทดสอบไฟฟ้าแบบไม่ทำลายตามมาตรฐาน ASTM A450 ร่วมกับการทดสอบไฮโดรสแตติก |
ท่อเหล็ก 18 Cr-8 Ni ไร้รอยต่อ |
200 |
A 213 – TP 304 หรือ TP 304L |
สำหรับอุปกรณ์ถ่ายเทความร้อนแบบไม่ได้เผาเพื่อป้องกันการปนเปื้อนของผลิตภัณฑ์หรือสำหรับอุณหภูมิบริการต่ำ |
วัสดุจะต้องสามารถผ่านการทดสอบการกัดกร่อนตามเกรน Practice E ตามที่กำหนดไว้ใน ASTM A262 |
การกำหนดชื่อ |
อุณหภูมิโลหะ (°C) |
เอส ที เอส ที |
หมายเหตุ |
ข้อกำหนดเพิ่มเติม |
ท่อเหล็ก 18 Cr-8 Ni ที่ผ่านการปรับเสถียรแบบไร้รอยต่อ |
(-100) +600 |
ก.213 – ทีพี 321, ทีพี 347 |
สำหรับเครื่องทำความร้อนสูงเกินและอุปกรณ์ถ่ายเทความร้อนที่ไม่ได้เผาภายใต้สภาวะกัดกร่อนบางประการและ/หรือที่อุณหภูมิใช้งานสูง |
วัสดุจะต้องผ่านการทดสอบการกัดกร่อนระหว่างเม็ดเกรน Practice E ตามที่ระบุไว้ใน ASTM A262 เพื่อให้ทนทานต่อการกัดกร่อนระหว่างเม็ดเกรนได้ดีที่สุด ควรระบุวิธีการอบชุบด้วยความร้อนเพื่อคงสภาพภายหลังการอบชุบด้วยความร้อนด้วยสารละลาย |
ท่อเหล็ก 18 Cr-8 Ni ไร้รอยต่อ |
815 |
เอ 213 – ทีพี 304เอช |
สำหรับหม้อไอน้ำ ซุปเปอร์ฮีตเตอร์ และอุปกรณ์ถ่ายเทความร้อนที่ไม่ผ่านการเผาไหม้ที่อุณหภูมิการใช้งานที่รุนแรงภายใต้สภาวะกัดกร่อนบางประการ |
ระบุ C 0.06% สูงสุด และ Mo+Ti+Nb 0.4% สูงสุด |
ท่อเหล็ก 18 Cr-8 Ni ที่ผ่านการปรับเสถียรแบบไร้รอยต่อ |
815 |
A 213 – TP 321H หรือ TP 347H |
สำหรับหม้อไอน้ำ ซุปเปอร์ฮีตเตอร์ และอุปกรณ์ถ่ายเทความร้อนที่ไม่ผ่านการเผาไหม้ที่อุณหภูมิการใช้งานที่รุนแรงภายใต้สภาวะกัดกร่อนบางประการ |
ระบุ C 0.06% สูงสุด และ Mo+Ti+Nb 0.4% สูงสุด |
ท่อเหล็ก 18 Cr-10 Ni-2 Mo ไร้รอยต่อ |
300 |
A 213 – TP 316 หรือ TP 316L |
สำหรับเครื่องทำความร้อนสูงเกินและอุปกรณ์ถ่ายเทความร้อนที่ไม่ได้เผาภายใต้สภาวะกัดกร่อนบางประการและ/หรือที่อุณหภูมิใช้งานสูง |
ควรใช้ TP 316 สำหรับชิ้นส่วนที่ไม่ได้เชื่อมเท่านั้น วัสดุจะต้องผ่านการทดสอบการกัดกร่อนตามเกรน Practice E ตามที่ระบุไว้ใน ASTM A262 |
ท่อเหล็ก 18 Cr-8 Ni ไร้รอยต่อ |
815 |
A 271 – TP 321H หรือ TP 347H |
สำหรับเตาเผาภายใต้สภาวะกัดกร่อนบางอย่างโดยมีความหนาของผนังสูงสุด 25 มม. |
– |
ท่อเหล็ก 25Cr-5 Ni-Mo ไร้รอยต่อ |
300 |
เอ 789 – S31803 |
สำหรับสภาวะกัดกร่อนบางประการ |
ระบุแบบไร้รอยต่อ |
ท่อเหล็ก 25Cr-7 Ni-Mo-N ไร้รอยต่อ |
300 |
เอ 789 – S32750 |
สำหรับสภาวะกัดกร่อนบางประการ |
ระบุแบบไร้รอยต่อ |
ท่อเหล็กไร้รอยต่อ 20 Cr-18 Ni-6 Mo-Cu-N |
(-200) (+400) |
เอ 269 – S31254 |
สำหรับสภาวะกัดกร่อนบางประการ |
ระบุแบบไร้รอยต่อ |
ท่อเหล็ก 25Cr-5NiMo-N ไร้รอยต่อ |
300 |
เอ 789 – S32550 |
สำหรับการบริการที่มีฤทธิ์กัดกร่อนบางประเภท |
ระบุแบบไร้รอยต่อ |
ท่อ
การกำหนดชื่อ |
อุณหภูมิโลหะ (°C) |
เอส ที เอส ที |
หมายเหตุ |
ข้อกำหนดเพิ่มเติม |
ท่อเหล็ก 1 Cr-0.5 Mo เชื่อมด้วยไฟฟ้าขนาด NPS 16 และใหญ่กว่า |
600 |
A 691 1Cr ชั้น 22 หรือ 42 |
สำหรับอุณหภูมิการให้บริการที่สูง ต้องมีคุณสมบัติต้านทานการไหลซึมและ/หรือต้านทานการโจมตีของไฮโดรเจนได้อย่างเหมาะสม |
สำหรับคลาส 22 วัสดุฐานจะต้องอยู่ในสภาพ N & T หรือ Q&T โดยมีการอบที่อุณหภูมิอย่างน้อย 730°C
รอยเชื่อมต้องเป็น PWHT ในช่วงอุณหภูมิ 680-780°C
สำหรับคลาส 42 อุณหภูมิการอบต้องอยู่ที่ 680°C ขึ้นไป
ระบุ P 0.01% สูงสุด |
ท่อเหล็ก 1.25 Cr-0.5 Mo เชื่อมด้วยไฟฟ้าขนาด NPS 16 และใหญ่กว่า |
600 |
A 691 – 1.25Cr ชั้น 22 หรือ 42 |
สำหรับอุณหภูมิการให้บริการที่สูง ต้องมีคุณสมบัติต้านทานการไหลซึมและ/หรือต้านทานการโจมตีของไฮโดรเจนได้อย่างเหมาะสม |
สำหรับคลาส 22 วัสดุฐานจะต้องอยู่ในสภาพ N & T หรือ Q&T โดยมีการอบที่อุณหภูมิอย่างน้อย 730°C
รอยเชื่อมต้องเป็น PWHT ในช่วงอุณหภูมิ 680-780°C
สำหรับคลาส 42 อุณหภูมิการอบต้องอยู่ที่ 680°C ขึ้นไป
ระบุ P 0.01% สูงสุด |
ท่อเหล็ก 2.25 Cr เชื่อมด้วยไฟฟ้าฟิวชั่น ขนาด NPS 16 และใหญ่กว่า |
625 |
A 691 – 2.25 Cr ชั้น 22 หรือ 42 |
สำหรับอุณหภูมิการให้บริการที่สูง ต้องมีคุณสมบัติต้านทานการไหลซึมและ/หรือต้านทานการโจมตีของไฮโดรเจนได้อย่างเหมาะสม |
สำหรับคลาส 22 วัสดุฐานจะต้องอยู่ในสภาพ N & T หรือ Q&T โดยมีการอบที่อุณหภูมิอย่างน้อย 730°C
รอยเชื่อมต้องเป็น PWHT ในช่วงอุณหภูมิ 680-780°C
สำหรับคลาส 42 อุณหภูมิการอบต้องอยู่ที่ 680°C ขึ้นไป
ระบุ P 0.01% สูงสุด |
ท่อเหล็ก 5 Cr-0.5 Mo เชื่อมด้วยไฟฟ้าขนาด NPS 16 และใหญ่กว่า |
650 |
A 691 – 5 Cr ชั้น 22 หรือ 42 |
สำหรับอุณหภูมิการให้บริการที่สูงและ/หรือความต้านทานต่อการกัดกร่อนของกำมะถัน |
สำหรับคลาส 22 วัสดุฐานจะต้องอยู่ในสภาพ N & T หรือ Q&T โดยมีการอบที่อุณหภูมิอย่างน้อย 730°C
รอยเชื่อมต้องเป็น PWHT ในช่วงอุณหภูมิ 680-780°C
สำหรับคลาส 42 อุณหภูมิการอบต้องอยู่ที่ 680°C ขึ้นไป
ระบุ P 0.01% สูงสุด |
ท่อเหล็ก 18 Cr-8 Ni เชื่อมด้วยไฟฟ้าแบบฟิวชั่นในขนาดที่สูงกว่า NPS 12 |
-200 ถึง +400 |
A 358 – เกรด 304 หรือ 304L ชั้น 1 |
สำหรับสภาวะกัดกร่อนบางประการและ/หรืออุณหภูมิในการให้บริการที่สูง |
วัสดุจะต้องสามารถผ่านการทดสอบการกัดกร่อนตามเกรน Practice E ตามที่กำหนดไว้ใน ASTM A262 |
ท่อเหล็ก 18 Cr-8 Ni ที่ผ่านการเชื่อมด้วยไฟฟ้าแบบฟิวชั่นในขนาดที่สูงกว่า NPS 12 |
-100 ถึง +600 |
A 358 – เกรด 321 หรือ 347 ชั้น 1 |
สำหรับสภาวะกัดกร่อนบางประการและ/หรืออุณหภูมิในการให้บริการที่สูง |
เพื่อให้ทนทานต่อการกัดกร่อนระหว่างเม็ดเกรนได้ดีที่สุด ควรระบุการอบด้วยความร้อนเพื่อรักษาเสถียรภาพที่อุณหภูมิ 900°C เป็นเวลา 4 ชั่วโมงหลังจากการอบด้วยความร้อนด้วยสารละลาย ตามรายละเอียดใน ASTM A358 ข้อกำหนดเพิ่มเติม S6 วัสดุจะต้องผ่านการทดสอบการกัดกร่อนระหว่างเม็ดเกรน Practice E ตามที่ระบุไว้ใน ASTM A262 |
ท่อเหล็ก 18 Cr-10 Ni-2 Mo เชื่อมด้วยไฟฟ้าแบบฟิวชั่นในขนาดที่สูงกว่า NPS 12 |
-200 ถึง +500 |
A 358 – เกรด 316 หรือ 316L ชั้น 1 |
สำหรับสภาวะกัดกร่อนบางประการและ/หรืออุณหภูมิในการให้บริการที่สูง |
วัสดุจะต้องสามารถผ่านการทดสอบการกัดกร่อนตามเกรน Practice E ตามที่กำหนดไว้ใน ASTM A262 |
ท่อเหล็ก 18 Cr-8 Ni เชื่อมด้วยไฟฟ้าแบบฟิวชั่นในขนาดที่สูงกว่า NPS 12 |
-200 ถึง +500 |
A 358 – เกรด 304L ชั้น 1 |
สำหรับสภาวะกัดกร่อนบางประการและ/หรืออุณหภูมิในการให้บริการที่สูง |
ระบุ C 0.06% สูงสุดและ Mo+Ti+Nb 0.04% สูงสุด |
ท่อเหล็กไร้รอยต่อ 0.3 Mo |
500 |
|
ไม่เหมาะสำหรับการใช้งานไฮโดรเจน สำหรับอุณหภูมิการใช้งานที่สูง |
ระบุปริมาณ Al ทั้งหมด 0.012% สูงสุด |
ท่อเหล็กไร้รอยต่อ 0.5 Mo |
500 |
เอ 335 – พี 1 |
ไม่เหมาะสำหรับการใช้งานไฮโดรเจน สำหรับอุณหภูมิการใช้งานที่สูง |
ระบุปริมาณ Al ทั้งหมด 0.012% สูงสุด |
ท่อเหล็กไร้รอยต่อ 1Cr-0.5Mo |
500 |
เอ 335 – พี 12 |
สำหรับอุณหภูมิการให้บริการที่สูงและ/หรือความต้านทานต่อการโจมตีของไฮโดรเจน |
กำหนดให้ทำแบบ normalized และ temperized
สำหรับความต้านทานต่อการโจมตีของไฮโดรเจน โปรดดู API 941
ผู้ซื้อต้องแจ้งผู้ผลิตหากจะให้บริการ
อุณหภูมิต้องสูงกว่า 600°C |
ท่อเหล็กไร้รอยต่อ 1.25 Cr-0.5 Mo |
600 |
เอ 335 – พี 11 |
สำหรับอุณหภูมิการให้บริการที่สูงและ/หรือความต้านทานต่อการโจมตีของไฮโดรเจน
โดยทั่วไปแล้วไม่มีรอยต่อในขนาดต่างๆ
ใหญ่กว่า NPS 16 สำหรับขนาดที่ใหญ่กว่า ให้ใช้ ASTM A691 – 1.25 CR-Class 22 หรือ 42
(9.3.2). |
กำหนดให้ทำแบบ normalized และ temperized
กำหนด P 0.005% สูงสุด
สำหรับความต้านทานต่อการโจมตีของไฮโดรเจน โปรดดู API 941
ผู้ซื้อต้องแจ้งผู้ผลิตหากจะให้บริการ
อุณหภูมิต้องสูงกว่า 600°C |
ท่อเหล็กไร้รอยต่อ 2.25 Cr-1 Mo |
625 |
เอ 335 – พี 22 |
สำหรับอุณหภูมิการให้บริการที่สูง ต้องมีคุณสมบัติต้านทานการไหลซึมและ/หรือต้านทานการโจมตีของไฮโดรเจนได้อย่างเหมาะสม
โดยปกติแล้ว จะไม่มีรอยต่อในขนาดที่ใหญ่กว่า NPS 16 สำหรับขนาดที่ใหญ่กว่า ให้ใช้ ASTM A691 – 2.25 Cr-Class 22 หรือ 42 (ดู 9.3.3) |
กำหนดให้ทำแบบ normalized และ temperized
สำหรับความต้านทานต่อการโจมตีของไฮโดรเจน โปรดดู API 941
ผู้ซื้อต้องแจ้งผู้ผลิตหากจะให้บริการ
อุณหภูมิต้องสูงกว่า 600°C |
ท่อเหล็กไร้รอยต่อ 5Cr-0.5Mo |
650 |
เอ 335 – พี 5 |
สำหรับอุณหภูมิการให้บริการที่สูงและ/หรือความต้านทานต่อการกัดกร่อนของกำมะถัน
โดยปกติแล้วจะไม่สามารถหาแบบไร้รอยต่อได้ในขนาดที่ใหญ่กว่า NPS 16 สำหรับขนาดที่ใหญ่กว่า ให้ใช้ ASTM A691 – 5 Cr-Class 22 หรือ 42 (ดู 9.3.4) |
กำหนดให้เป็นปกติและอบอ่อน หรือ ดับและอบอ่อน |
ท่อเหล็กไร้รอยต่อ 9Cr-1Mo |
650 |
เอ 335 – พี 9 |
สำหรับอุณหภูมิการให้บริการที่สูงและ/หรือความต้านทานต่อการกัดกร่อนของกำมะถัน |
กำหนดให้ทำแบบ normalized และ temperized
ผู้ซื้อต้องแจ้งผู้ผลิตหากจะให้บริการ
อุณหภูมิต้องสูงกว่า 600°C |
ท่อเหล็กไร้ตะเข็บ 3.5 Ni |
400 |
A 333 – เกรด 3 ไร้รอยต่อ |
สำหรับอุณหภูมิการให้บริการต่ำ |
|
ท่อเหล็กไร้รอยต่อ 9 Ni |
-200 |
A 333 – เกรด 8 ไร้รอยต่อ |
สำหรับอุณหภูมิการให้บริการต่ำ |
ระบุ : C 0.10% สูงสุด S 0.002% สูงสุด P 0.005% สูงสุด |
ท่อเหล็กกล้า 18 Cr-8 Ni ไร้รอยต่อและเชื่อมในขนาด NPS 12 รวมถึง |
-200 ถึง +400 |
เอ 312 – ทีพี 304 |
สำหรับอุณหภูมิบริการต่ำหรือเพื่อป้องกันการปนเปื้อนของผลิตภัณฑ์ |
ท่อเชื่อมสามารถใช้ได้กับผนังที่มีความหนาสูงสุดถึง 5.5 มม.
เนื้อหาจะต้องสามารถผ่านเกณฑ์ปฏิบัติ E ได้
การทดสอบการกัดกร่อนระหว่างเกรนตามที่กำหนดใน ASTM A 262 |
ท่อเหล็กกล้า 18 Cr-8 Ni ไร้รอยต่อและเชื่อมในขนาด NPS 12 รวมถึง |
-200 ถึง +400 |
เอ 312 – ทีพี 304แอล |
สำหรับสภาวะกัดกร่อนบางประการและ/หรืออุณหภูมิในการให้บริการที่สูง |
ท่อเชื่อมสามารถใช้ได้กับผนังที่มีความหนาสูงสุดถึง 5.5 มม.
วัสดุจะต้องสามารถผ่านการทดสอบการกัดกร่อนระหว่างเม็ดเกรน Practice E ตามที่ระบุไว้ใน ASTM A 262 |
ท่อเหล็กเสริมความแข็ง Ni 18 Cr-8 เชื่อมไร้รอยต่อในขนาด NPS 12 รวมถึง |
-100 ถึง +600 |
A 312 – TP 321 หรือ TP 347 |
สำหรับสภาวะกัดกร่อนบางประการและ/หรืออุณหภูมิในการให้บริการที่สูง |
ท่อเชื่อมสามารถใช้ได้กับผนังที่มีความหนาสูงสุดถึง 5.5 มม.
สำหรับความต้านทานการกัดกร่อนระหว่างเม็ดเกรนที่เหมาะสมที่สุด ให้ระบุการอบด้วยความร้อนเพื่อคงสภาพที่อุณหภูมิ 900°C เป็นเวลา 4 ชั่วโมงภายหลังการอบด้วยความร้อนด้วยสารละลาย ตามรายละเอียดในข้อกำหนดเสริม ASTM A358
S5 วัสดุจะต้องสามารถผ่านการทดสอบการกัดกร่อนระหว่างเม็ดเกรนตามแนวทางปฏิบัติ E ตามที่ระบุไว้ใน ASTM A 262 |
ท่อเหล็กเสริมความแข็ง Ni 18 Cr-8 เชื่อมไร้รอยต่อในขนาด NPS 12 รวมถึง |
815 |
A 312 – TP 321H หรือ TP 347H |
สำหรับสภาวะกัดกร่อนบางประเภทและ/หรืออุณหภูมิการให้บริการที่รุนแรง |
ท่อเชื่อมสามารถใช้ได้กับผนังที่มีความหนาสูงสุดถึง 5.5 มม. |
การใช้เกรดนี้ต้องขึ้นอยู่กับข้อตกลงของบริษัท |
ท่อเหล็ก 18 Cr-10 Ni-2 Mo ไร้รอยต่อและเชื่อมในขนาด NPS 12 รวมถึง |
-200 ถึง +500 |
A 312 – TP 316 หรือ TP 316L |
สำหรับสภาวะกัดกร่อนบางประการและ/หรืออุณหภูมิในการให้บริการที่สูง |
ท่อเชื่อมสามารถใช้ได้กับผนังที่มีความหนาสูงสุดถึง 5.5 มม. |
วัสดุจะต้องสามารถผ่านการทดสอบการกัดกร่อนตามเกรน Practice E ตามที่กำหนดไว้ใน ASTM A262 |
ท่อเหล็กกล้า 18 Cr-8 Ni ไร้รอยต่อและเชื่อมในขนาด NPS 12 รวมถึง |
+500 (+815) |
เอ 312 – ทีพี 304เอช |
สำหรับสภาวะกัดกร่อนบางประการและ/หรืออุณหภูมิในการให้บริการที่สูง |
ระบุ C 0.06% สูงสุด และ Mo+Ti+Nb 0.4% สูงสุด |
ท่อเหล็ก 22Cr-5Ni-Mo-N แบบไร้รอยต่อและเชื่อม |
300 |
เอ 790 – เอส 31803 |
สำหรับสภาวะกัดกร่อนบางประเภท |
ระบุ N 0.15% ขั้นต่ำ |
ท่อเชื่อมสามารถใช้ได้กับผนังที่มีความหนาสูงสุดถึง 5.5 มม. |
ระบุในสภาวะการอบละลายและการดับด้วยน้ำ |
ท่อเหล็ก 25Cr-7 Ni-Mo-N ไร้รอยต่อและเชื่อม |
300 |
เอ 790 – เอส 32750 |
สำหรับสภาวะกัดกร่อนบางประเภท |
ระบุ N 0.15% ขั้นต่ำ |
ท่อเชื่อมสามารถใช้ได้กับผนังที่มีความหนาสูงสุดถึง 5.5 มม. |
ระบุในสภาวะการอบละลายและการดับด้วยน้ำ |
ท่อเหล็ก 20Cr-18 Ni-6 Mo-Cu-N ไร้รอยต่อและเชื่อม |
-200 (+400) |
เอ 312 – S31254 |
สำหรับสภาวะกัดกร่อนบางประเภท |
ท่อเชื่อมสามารถใช้ได้กับผนังที่มีความหนาสูงสุดถึง 5.5 มม. |
งานตีขึ้นรูป หน้าแปลน และอุปกรณ์ประกอบ
การกำหนดชื่อ |
อุณหภูมิโลหะ (°C) |
เอส ที เอส ที |
หมายเหตุ |
ข้อกำหนดเพิ่มเติม |
อุปกรณ์เชื่อมชนเหล็ก 0.5 Mo |
500 |
A 234 – WP1 หรือ WP1W |
ไม่เหมาะสำหรับการใช้กับไฮโดรเจน สำหรับอุณหภูมิในการให้บริการที่สูง |
ขนาดสูงสุดถึง NPS 16 รวมถึงจะต้องไร้รอยต่อ
ขนาดที่ใหญ่กว่าอาจเป็นแบบไร้รอยต่อหรือแบบเชื่อมก็ได้
ระบุปริมาณ Al ทั้งหมด 0.012% สูงสุด |
ข้อต่อเชื่อมชนเหล็ก 1 Cr-0.5 Mo |
600 |
A 234 – WP12 คลาส 2 หรือ WP12W คลาส 2 |
สำหรับอุณหภูมิการให้บริการที่สูงและ/หรือความต้านทานต่อการโจมตีของไฮโดรเจน |
ขนาดสูงสุดถึง NPS 16 รวมถึงจะต้องไร้รอยต่อ
ขนาดที่ใหญ่กว่าอาจเป็นแบบไร้รอยต่อหรือแบบเชื่อมก็ได้
กำหนดให้เป็นปกติและอบอ่อน หรือ ดับและอบอ่อน
กำหนด P 0.005% สูงสุด
สำหรับความต้านทานต่อการโจมตีของไฮโดรเจน โปรดดู API 941 |
ข้อต่อเชื่อมชนเหล็ก 1.25Cr-0.5Mo |
600 |
A 234 – WP11 คลาส 2 หรือ WP11W คลาส 2 |
สำหรับอุณหภูมิการให้บริการที่สูงและ/หรือความต้านทานต่อการโจมตีของไฮโดรเจน |
ขนาดสูงสุดถึง NPS 16 รวมถึงจะต้องไร้รอยต่อ
กำหนด P 0.005% สูงสุด
สำหรับโลหะในบ่อน้ำ ให้ระบุ 10P+55Pb+5Sn+As (1400 ppm) |
2.25 อุปกรณ์เชื่อมชนเหล็ก Cr-1 Mo |
625 |
A 234 – WP22 คลาส 3 หรือ WP22W คลาส 3 |
สำหรับอุณหภูมิการให้บริการที่รุนแรงและ/หรือความต้านทานต่อการกัดกร่อนของกำมะถัน |
ขนาดสูงสุดถึง NPS 16 รวมถึงจะต้องไร้รอยต่อ
ขนาดที่ใหญ่กว่าอาจเป็นแบบไร้รอยต่อหรือแบบเชื่อมก็ได้
กำหนดให้เป็นปกติและอบอ่อน หรือ ดับและอบอ่อน
สำหรับความต้านทานต่อการโจมตีของไฮโดรเจน โปรดดู API 941 |
ข้อต่อเชื่อมชนเหล็ก 5 Cr-0.5 Mo |
650 |
A 234 – WP5 หรือ WP5W |
สำหรับอุณหภูมิการให้บริการที่สูงและ/หรือความต้านทานต่อการกัดกร่อนของกำมะถัน |
ขนาดสูงสุดถึง NPS 16 รวมถึงจะต้องไร้รอยต่อ
ขนาดที่ใหญ่กว่าอาจเป็นแบบไร้รอยต่อหรือแบบเชื่อมก็ได้
กำหนดให้เป็นปกติและอบอ่อน หรือ ดับและอบอ่อน |
3.5 อุปกรณ์เชื่อมชนเหล็ก Ni |
(+400) |
A 420 – WPL3 หรือ WPL3W |
สำหรับอุณหภูมิบริการต่ำ |
ขนาดสูงสุดถึง NPS 16 รวมถึงจะต้องไร้รอยต่อ
ขนาดที่ใหญ่กว่าอาจเป็นแบบไร้รอยต่อหรือแบบเชื่อมก็ได้
กำหนดให้เป็นปกติ |
อุปกรณ์เชื่อมชนเหล็ก Ni 9 |
-200 |
A 420 – WPL8 หรือ WPL8W |
สำหรับอุณหภูมิบริการต่ำ |
ขนาดสูงสุดถึง NPS 16 รวมถึงจะต้องไร้รอยต่อ
ขนาดที่ใหญ่กว่าอาจเป็นแบบไร้รอยต่อหรือแบบเชื่อมก็ได้
ระบุว่าให้ผ่านกระบวนการทำให้เป็นมาตรฐานสองชั้นหรือชุบแข็งและอบคืนตัว
ระบุ C สูงสุด 0.10%, S สูงสุด 0.002%, P สูงสุด 0.005% |
อุปกรณ์เชื่อมปลายชนเหล็ก Cr-8 Ni 18 |
-200 ถึง +400 |
เอ 403 – WP304-S/WX/WU |
สำหรับอุณหภูมิบริการต่ำหรือเพื่อป้องกันการปนเปื้อนของผลิตภัณฑ์ |
ขนาดสูงสุดถึง NPS 16 รวมถึงจะต้องไร้รอยต่อ
ขนาดที่ใหญ่กว่าอาจเป็นแบบไร้รอยต่อหรือแบบเชื่อมก็ได้
วัสดุจะต้องผ่านการทดสอบการกัดกร่อนตามเกรน Practice E ตามที่ระบุไว้ใน ASTM A262
ทดสอบรอยเชื่อมทั้งหมดของสแตนเลสออสเทนนิติก |
อุปกรณ์เชื่อมปลายชนเหล็ก Cr-8 Ni 18 |
-200 ถึง +400 |
403 – WP304L-S/WX/WU |
สำหรับสภาวะกัดกร่อนบางประการและ/หรืออุณหภูมิในการให้บริการที่สูง |
ขนาดสูงสุดถึง NPS 16 รวมถึงจะต้องไร้รอยต่อ
ขนาดที่ใหญ่กว่าอาจเป็นแบบไร้รอยต่อหรือแบบเชื่อมก็ได้
วัสดุจะต้องสามารถผ่านการทดสอบการกัดกร่อนตามเกรน Practice E ตามที่กำหนดไว้ใน ASTM A262 |
อุปกรณ์เชื่อมปลายชนเหล็ก Cr-8 Ni 18 |
815 |
เอ 403 – WP304H-S/WX/WU |
สำหรับสภาวะกัดกร่อนบางประการและ/หรืออุณหภูมิการให้บริการที่รุนแรง |
ขนาดสูงสุดถึง NPS 16 รวมถึงจะต้องไร้รอยต่อ
ขนาดที่ใหญ่กว่าอาจเป็นแบบไร้รอยต่อหรือแบบเชื่อมก็ได้
ระบุ: C 0.06% สูงสุด และ Mo+Ti+Nb 0.4% สูงสุด |
อุปกรณ์เชื่อมชนเหล็กกล้า 18Cr-8Ni ที่เสถียร |
(-100) ถึง +600 |
A 403 – WP321-S/WX/WU หรือ WP347-S/WX/WU |
สำหรับสภาวะกัดกร่อนบางประการและ/หรืออุณหภูมิการให้บริการที่รุนแรง |
ขนาดสูงสุดถึง NPS 16 รวมถึงจะต้องไร้รอยต่อ
ขนาดที่ใหญ่กว่าอาจเป็นแบบไร้รอยต่อหรือแบบเชื่อมก็ได้
สำหรับความต้านทานการกัดกร่อนระหว่างเม็ดเกรนที่เหมาะสมที่สุด ควรระบุการอบความร้อนเพื่อคงตัวที่อุณหภูมิ 900°C เป็นเวลา 4 ชั่วโมง โดยอยู่ภายใต้การอบความร้อนด้วยสารละลาย |
อุปกรณ์เชื่อมชนเหล็กกล้า 18Cr-8Ni ที่เสถียร |
815 |
A 403 – WP321H-S/WX/WU หรือ WP347H-S/WX/WU |
สำหรับสภาวะกัดกร่อนบางประการและ/หรืออุณหภูมิการให้บริการที่รุนแรง |
การใช้เกรดนี้ต้องได้รับความยินยอมจากบริษัท |
ข้อต่อเชื่อมปลายเหล็ก 18 Cr-10 Ni-2 Mo |
-200 ถึง +500 |
A 403 – WP316-S/WX/WU หรือ WP316L-S/WX/WU |
สำหรับสภาวะการกัดกร่อนบางประการและ/หรือสภาวะการบริการที่สูง |
ขนาดสูงสุดถึง NPS 16 รวมถึงจะต้องไร้รอยต่อ
ขนาดที่ใหญ่กว่าอาจเป็นแบบไร้รอยต่อหรือแบบเชื่อมก็ได้
วัสดุจะต้องสามารถผ่านการทดสอบการกัดกร่อนตามเกรน Practice E ตามที่กำหนดไว้ใน ASTM A262 |
ข้อต่อเชื่อมชนเหล็ก 22 Cr-5 Ni-Mo-N |
300 |
A815 – S31803 คลาส WP-S หรือ WP-WX |
สำหรับสภาวะกัดกร่อนบางประการ |
ขนาดสูงสุดถึง NPS 16 รวมถึงจะต้องไร้รอยต่อ
ขนาดที่ใหญ่กว่าอาจเป็นแบบไร้รอยต่อหรือแบบเชื่อมก็ได้
ระบุ N 0.15% ขั้นต่ำ |
ข้อต่อเชื่อมปลายเหล็ก 25 Cr-7 Ni-Mo-N สำหรับสภาวะที่กัดกร่อน |
300 |
A815 – S32750 คลาส WP-S หรือ WP-WX |
สำหรับสภาวะที่มีฤทธิ์กัดกร่อน |
ระบุแบบไร้รอยต่อ |
20 Cr-18 Ni-6 Mo-Cu-N อุปกรณ์เชื่อมชนเหล็ก |
(-200) ถึง +400 |
A403 – WPS 31254-S/WX/WU |
สำหรับสภาวะกัดกร่อนบางประการ |
ขนาดสูงสุดถึง NPS 16 รวมถึงจะต้องไร้รอยต่อ
ขนาดที่ใหญ่กว่าอาจเป็นแบบไร้รอยต่อหรือแบบเชื่อมก็ได้ |
เหล็กกล้าหลอม 0.5 โมลาร์ |
500 |
เอ 182-F1 |
ไม่เหมาะสำหรับใช้กับไฮโดรเจน สำหรับแผ่นท่อ หน้าแปลน ข้อต่อ วาล์ว และชิ้นส่วนอื่นๆ ที่รักษาแรงดันในระดับสูง
อุณหภูมิการให้บริการ |
|
เหล็กกล้าหลอม 0.5 โมลาร์ |
+500 |
เอ 336 – เอฟ 1 |
สำหรับชิ้นส่วนที่มีน้ำหนักมาก เช่น การตีขึ้นรูปถัง เพื่ออุณหภูมิการใช้งานที่สูง ไม่เหมาะสำหรับการใช้งานไฮโดรเจน |
ระบุปริมาณ Al ทั้งหมด 0.012% สูงสุด |
เหล็กกล้า 1 Cr-0.5 Mo สำหรับการตีขึ้นรูป |
+600 |
A 182 – F12 ชั้น 2 |
สำหรับแผ่นท่อ หน้าแปลน ข้อต่อ วาล์ว และชิ้นส่วนที่รักษาแรงดันที่อุณหภูมิใช้งานสูง ทนทานต่อการโจมตีของไฮโดรเจน |
กำหนดให้ทำเป็นมาตรฐานและอบให้แข็ง สำหรับความทนทานต่อการโจมตีของไฮโดรเจน โปรดดู API 941 |
เหล็กกล้า 1 Cr-0.5 Mo สำหรับการตีขึ้นรูป |
+600 |
เอ 336 – เอฟ 12 |
สำหรับชิ้นส่วนที่มีน้ำหนักมาก เช่น การตีขึ้นรูปถัง เพื่ออุณหภูมิการใช้งานที่สูง และ/หรือความต้านทานต่อการโจมตีของไฮโดรเจน |
กำหนดให้ทำเป็นมาตรฐานและอบให้แข็ง สำหรับความทนทานต่อการโจมตีของไฮโดรเจน โปรดดู API 941 |
เหล็กกล้าหลอม 1.25 Cr-0.5 Mo |
+600 |
เอ 182 – เอฟ 11 |
สำหรับแผ่นท่อ หน้าแปลน ข้อต่อ วาล์ว และชิ้นส่วนที่รักษาแรงดันที่อุณหภูมิใช้งานสูง ทนทานต่อการโจมตีของไฮโดรเจน |
กำหนดให้เป็นมาตรฐานและอบให้แข็ง กำหนดให้ P 0.005% สูงสุด สำหรับความต้านทานต่อการโจมตีของไฮโดรเจน โปรดดู API 941 |
เหล็กกล้าหลอม 1.25 Cr-0.5 Mo |
+600 |
เอ 336 – เอฟ 11 |
สำหรับชิ้นส่วนที่มีน้ำหนักมาก เช่น การตีขึ้นรูปถัง เพื่ออุณหภูมิการใช้งานที่สูง และ/หรือความต้านทานต่อการโจมตีของไฮโดรเจน |
ระบุว่าเป็นแบบปกติและอบชุบหรือชุบแข็งและอบชุบ การใช้เกรดชุบแข็งและอบชุบด้วยของเหลวต้องได้รับการตกลง ระบุ P 0.005% สูงสุด |
2.25 เหล็กกล้า Cr-1 Mo สำหรับการตีขึ้นรูป |
+625 |
เอ 182 – เอฟ 22 |
สำหรับแผ่นท่อ หน้าแปลน ข้อต่อ วาล์ว และชิ้นส่วนที่รักษาแรงดันที่อุณหภูมิใช้งานสูง ทนทานต่อการโจมตีของไฮโดรเจน |
ระบุว่าจะต้องทำให้เป็นมาตรฐานและอบให้แข็ง อ้างอิง API 934 สำหรับข้อกำหนดด้านวัสดุและการผลิต |
2.25 เหล็กกล้า Cr-1 Mo สำหรับการตีขึ้นรูป |
+625 |
เอ 336 – เอฟ 22 |
สำหรับชิ้นส่วนที่มีน้ำหนักมาก เช่น การตีขึ้นรูปถัง เพื่ออุณหภูมิการใช้งานที่สูง และ/หรือความต้านทานต่อการโจมตีของไฮโดรเจน |
ระบุว่าจะต้องผ่านกระบวนการทำให้เป็นมาตรฐานและอบคืนตัว หรือผ่านการชุบแข็งและอบคืนตัว การใช้เกรดที่ผ่านการชุบแข็งและอบคืนตัวด้วยของเหลวต้องเป็นไปตามข้อตกลง อ้างอิง API 934 |
เหล็กกล้า 3Cr-1Mo สำหรับการตีขึ้นรูป |
+625 |
เอ 182 – เอฟ 21 |
สำหรับแผ่นท่อ หน้าแปลน ข้อต่อ วาล์ว และชิ้นส่วนที่รักษาแรงดันที่อุณหภูมิใช้งานสูง ทนทานต่อการโจมตีของไฮโดรเจน |
ระบุว่าจะต้องทำให้เป็นมาตรฐานและอบให้แข็ง อ้างอิง API 934 สำหรับข้อกำหนดด้านวัสดุและการผลิต |
เหล็กกล้า 5 Cr-0.5 Mo สำหรับการตีขึ้นรูป |
+650 |
เอ 182 – เอฟ5 |
สำหรับแผ่นท่อ หน้าแปลน ข้อต่อ วาล์ว และชิ้นส่วนรักษาแรงดันที่อุณหภูมิใช้งานสูง ทนทานต่อการกัดกร่อนของซัลเฟอร์ |
กำหนดให้ทำแบบ normalized และ temperized |
3.5 การตีขึ้นรูปเหล็ก Ni |
(-400) |
เอ 350 – LF3 |
สำหรับแผ่นท่อ หน้าแปลน ข้อต่อ วาล์ว และชิ้นส่วนที่รักษาแรงดันที่อุณหภูมิใช้งานต่ำ |
ระบุ: C 0.10% สูงสุด, Si 0.30% สูงสุด, Mn 0.90% สูงสุด, S 0.005% สูงสุด |
เหล็กกล้า Ni 9 ชิ้น |
(-200) |
A 522 – ประเภท 1 |
สำหรับแผ่นท่อ หน้าแปลน ข้อต่อ วาล์ว และชิ้นส่วนที่รักษาแรงดันที่อุณหภูมิใช้งานต่ำ |
ระบุ: C 0.10% สูงสุด, Si 0.30% สูงสุด, Mn 0.90% สูงสุด, S 0.005% สูงสุด |
เหล็กกล้า 12Cr สำหรับการตีขึ้นรูป |
+540 |
เอ 182 เอฟ 6 เอ |
สำหรับสภาวะกัดกร่อนบางประการ |
|
เหล็กกล้า 12Cr สำหรับการตีขึ้นรูป |
+540 |
เอ 182 – เอฟ 6 เอ |
สำหรับแผ่นท่อ หน้าแปลน ข้อต่อ วาล์ว และชิ้นส่วนอื่นๆ ที่รักษาแรงดันภายใต้สภาวะที่กัดกร่อนและ/หรืออุณหภูมิการใช้งานที่สูง |
วัสดุจะต้องสามารถผ่านการทดสอบการกัดกร่อนตามเกรน Practice E ตามที่กำหนดไว้ใน ASTM A262 |
เหล็กกล้า 18 Cr-8 Ni ที่ถูกตีขึ้นรูป |
-200 / +400 |
เอ 182 – เอฟ 304 |
สำหรับอุณหภูมิบริการต่ำหรือเพื่อป้องกันการปนเปื้อนของผลิตภัณฑ์ |
วัสดุจะต้องสามารถผ่านการทดสอบการกัดกร่อนตามเกรน Practice E ตามที่กำหนดไว้ใน ASTM A262 |
เหล็กกล้า 18 Cr-8 Ni ที่ถูกตีขึ้นรูป |
-200 / +400 |
เอ 182 – เอฟ 304 ล |
สำหรับสภาวะกัดกร่อนบางประการและ/หรืออุณหภูมิในการให้บริการที่สูง |
วัสดุจะต้องสามารถผ่านการทดสอบการกัดกร่อนตามเกรน Practice E ตามที่กำหนดไว้ใน ASTM A262 |
เหล็กกล้า 18 Cr-8 Ni ที่ถูกตีขึ้นรูป |
-200 / +500 |
เอ 182 – เอฟ 304 ล |
สำหรับแผ่นท่อ หน้าแปลน ข้อต่อ วาล์ว และชิ้นส่วนอื่นๆ ที่รักษาแรงดันภายใต้สภาวะที่กัดกร่อนและ/หรืออุณหภูมิการใช้งานที่สูง |
วัสดุจะต้องสามารถผ่านการทดสอบการกัดกร่อนตามเกรน Practice E ตามที่กำหนดไว้ใน ASTM A262 |
เหล็กกล้า 18 Cr-8 Ni ที่ถูกตีขึ้นรูป |
+815 |
เอ 182 – เอฟ 304เอช |
สำหรับแผ่นท่อ หน้าแปลน ข้อต่อ วาล์ว และชิ้นส่วนอื่นๆ ที่รักษาแรงดันภายใต้อุณหภูมิการใช้งานที่รุนแรง |
ระบุ C 0.06% สูงสุด Mo+Ti+Nb 0.4% สูงสุด |
เหล็กกล้าหลอมเสถียร 18 Cr-8 Ni |
+600 |
เอ 182 – เอฟ 321 / เอฟ 347 |
สำหรับแผ่นท่อ หน้าแปลน ข้อต่อ วาล์ว และชิ้นส่วนอื่นๆ ที่รักษาแรงดันภายใต้สภาวะที่กัดกร่อนและ/หรืออุณหภูมิการใช้งานที่สูง |
เพื่อให้ทนทานต่อการกัดกร่อนระหว่างเม็ดเกรนได้ดีที่สุด ควรระบุการอบด้วยความร้อนเพื่อรักษาเสถียรภาพที่อุณหภูมิ 870-900°C เป็นเวลา 4 ชั่วโมง แล้วจึงอบด้วยความร้อนด้วยสารละลาย วัสดุจะต้องผ่านการทดสอบการกัดกร่อนระหว่างเม็ดเกรน Practice E ตามที่ระบุไว้ใน ASTM A262 |
เหล็กกล้าหลอมเสถียร 18 Cr-8 Ni |
+815 |
เอ 182 – เอฟ321เอช / เอฟ347เอช |
สำหรับแผ่นท่อ หน้าแปลน ข้อต่อ วาล์ว และชิ้นส่วนอื่นๆ ที่รักษาแรงดันภายใต้อุณหภูมิการใช้งานที่รุนแรง |
การใช้เกรดนี้ต้องขึ้นอยู่กับข้อตกลงของบริษัท |
เหล็กกล้า 18 Cr-10 Ni-2 Mo สำหรับการตีขึ้นรูป |
-200 / +500 |
เอ 182 – เอฟ 316 |
สำหรับสภาวะกัดกร่อนบางประการและ/หรืออุณหภูมิในการให้บริการที่สูง |
วัสดุจะต้องสามารถผ่านการทดสอบการกัดกร่อนตามเกรน Practice E ตามที่กำหนดไว้ใน ASTM A262 |
เหล็กกล้า 18 Cr-10 Ni-2 Mo สำหรับการตีขึ้นรูป |
-200 / +500 |
เอ 182 – เอฟ 316 ล |
สำหรับสภาวะกัดกร่อนบางประการและ/หรืออุณหภูมิในการให้บริการที่สูง |
วัสดุจะต้องสามารถผ่านการทดสอบการกัดกร่อนตามเกรน Practice E ตามที่กำหนดไว้ใน ASTM A262 |
เหล็กกล้า 18 Cr-10 Ni-2 Mo สำหรับการตีขึ้นรูป |
-200 / +500 |
เอ 182 – เอฟ 316 เอช |
สำหรับสภาวะกัดกร่อนบางประการและ/หรืออุณหภูมิในการให้บริการที่สูง |
วัสดุจะต้องสามารถผ่านการทดสอบการกัดกร่อนตามเกรน Practice E ตามที่กำหนดไว้ใน ASTM A262 |
เหล็กกล้า 22 Cr-5 Ni-Mo-N ที่ถูกตีขึ้นรูป |
-30 / +300 |
เอ 182 – เอฟ 51 |
สำหรับแผ่นท่อ หน้าแปลน ข้อต่อ วาล์ว และชิ้นส่วนอื่นๆ ที่รักษาแรงดันภายใต้สภาวะที่กัดกร่อน |
ระบุ N 0.15% ขั้นต่ำ |
เหล็กกล้า 25 Cr-7 Ni-Mo-N ที่ถูกตีขึ้นรูป |
(-30) ถึง +300 |
เอ 182 – เอฟ 53 |
สำหรับแผ่นท่อ หน้าแปลน ข้อต่อ วาล์ว และชิ้นส่วนอื่นๆ ที่ทำหน้าที่กักเก็บแรงดันภายใต้สภาวะกัดกร่อนบางประเภท |
– |
การตีเหล็ก 20 Cr-18 Ni-6 Mo-Cu-N |
(-200) ถึง (+400) |
เอ 182 – เอฟ 44 |
สำหรับแผ่นท่อ หน้าแปลน ข้อต่อ วาล์ว และชิ้นส่วนอื่นๆ ที่ทำหน้าที่กักเก็บแรงดันภายใต้สภาวะกัดกร่อนบางประเภท |
– |
เหล็กกล้า 9Cr Mo สำหรับการตีขึ้นรูป |
+650 |
เอเอสทีเอ182-F9 |
สำหรับแผ่นท่อ หน้าแปลน ข้อต่อ วาล์ว และชิ้นส่วนอื่นๆ ที่รักษาแรงดันไว้ที่อุณหภูมิการใช้งานที่รุนแรง และ/หรือต้องทนทานต่อการกัดกร่อนของซัลเฟอร์ |
ทำให้เป็นมาตรฐานและปรับอุณหภูมิ |
โลหะผสม Ni-Cr-Mo-Nb ขึ้นรูป (โลหะผสม 625) สำหรับสภาวะกัดกร่อน |
425 |
แอสทาม B366 |
ผ่านกระบวนการทางเคมีและปราศจากตะกรันหรือออกไซด์ใดๆ ระบุในเงื่อนไขการอบอ่อนของสารละลาย |
– |
การตีขึ้นรูปโลหะผสม Ni-Cr-Fe (โลหะผสม 600) สำหรับสภาวะที่กัดกร่อน |
+650 |
แอสทาม B564 N06600 |
ระบุการขึ้นรูปในสภาวะอบละลาย |
– |
การหล่อ
การกำหนดชื่อ |
อุณหภูมิโลหะ (°C) |
ข้อกำหนดมาตรฐาน ASTM |
หมายเหตุ |
ข้อกำหนดเพิ่มเติม |
14.5 การหล่อซิลิกอน |
+250 |
เอ 518 – 1 |
สำหรับชิ้นส่วนที่ไม่กักเก็บแรงดัน (ภายใน) |
ระบุปริมาณ Si ขั้นต่ำ 14.5% ธาตุโลหะผสมอื่นสำหรับ Mo ที่กำหนด |
18-16-6 Cu-2 Cr-Nb (ประเภท 1) ชิ้นส่วนหล่อ |
+500 |
A 436 – ประเภท 1 |
สำหรับชิ้นส่วนที่ไม่กักเก็บแรงดัน (ภายใน) ภายใต้สภาวะกัดกร่อนบางประการ |
– |
การหล่อ 18-20 Cr-2 Ni-Nb-Ti (ประเภท D-2) |
+500 |
A 439 – แบบ D-2 |
สำหรับชิ้นส่วนที่รักษาแรงดันภายใต้สภาวะกัดกร่อนบางประเภท |
– |
หล่อ Ni-4 Mn จำนวน 22 ชิ้น |
+500 |
A 571 – แบบ D2-M |
สำหรับชิ้นส่วนที่รักษาแรงดันไว้ที่อุณหภูมิใช้งานต่ำ |
– |
เหล็กหล่อ 0.5 โมลาร์ |
+500 |
เอ 217 – WC1 |
ไม่เหมาะสำหรับการใช้งานกับไฮโดรเจน สำหรับอุปกรณ์ วาล์ว และชิ้นส่วนอื่นๆ ที่ทำหน้าที่รักษาแรงดันในอุณหภูมิการใช้งานที่สูงและ/หรือทนต่อการโจมตีของไฮโดรเจน |
ระบุปริมาณ Al ทั้งหมด 0.012% สูงสุด |
เหล็กหล่อ 1.25 Cr-0.5 Mo |
+550 |
เอ 217 – WC6 |
สำหรับอุปกรณ์วาล์วและชิ้นส่วนอื่นๆ ที่รักษาแรงดันไว้ที่อุณหภูมิใช้งานสูงและ/หรือต้องทนทานต่อการกัดกร่อนของกำมะถัน |
ระบุค่าสูงสุด 0.01% Al. ปรับมาตรฐานและอบให้ร้อน |
เหล็กหล่อ 2.25 Cr-1 Mo |
+650 |
เอ 217 – WC9 |
สำหรับอุปกรณ์วาล์ว และชิ้นส่วนอื่นๆ ที่รักษาแรงดันไว้ที่อุณหภูมิใช้งานสูงและ/หรือทนทานต่อการโจมตีของไฮโดรเจน |
ระบุค่าสูงสุด 0.01% ต้านทานการโจมตีของไฮโดรเจนตาม API 941 |
เหล็กหล่อ 5 Cr-0.5 Mo |
+650 |
เอ 217 – ซี 5 |
สำหรับอุปกรณ์วาล์วและชิ้นส่วนรักษาแรงดันอื่นๆ ที่อุณหภูมิใช้งานสูงและ/หรือทนทานต่อการกัดกร่อนของกำมะถัน |
– |
เหล็กหล่อ 9 Cr-1 Mo |
+650 |
เอ 217 – ซี 12 |
สำหรับอุปกรณ์วาล์วและชิ้นส่วนรักษาแรงดันอื่นๆ ที่อุณหภูมิใช้งานสูงและ/หรือทนทานต่อการกัดกร่อนของกำมะถัน |
– |
3.5 เหล็กหล่อ Ni |
(+400) |
เอ 352 – แอลซี 3 |
สำหรับอุณหภูมิบริการต่ำ |
– |
เหล็กหล่อ Ni 9 |
(+400) |
เอ 352 – LC9 |
สำหรับอุณหภูมิบริการต่ำ |
ระบุ : C 0.10% สูงสุด, S 0.002% สูงสุด, P 0.005% สูงสุด |
เหล็กหล่อ 12Cr |
+540 |
เอ 743 – ซีเอ 15 |
สำหรับชิ้นส่วนที่ไม่กักเก็บแรงดันภายใต้สภาวะที่กัดกร่อน |
– |
เหล็กหล่อ 12 Cr-4 Ni |
+540 |
เอ 217 – CA15 |
สำหรับชิ้นส่วนที่รักษาแรงดันภายใต้สภาวะกัดกร่อนบางประเภท |
– |
เหล็กหล่อ 18 Cr-8 Ni |
+200 |
744 – ซีเอฟบี |
สำหรับชิ้นส่วนที่ไม่กักเก็บแรงดัน (ภายใน) ภายใต้สภาวะกัดกร่อนบางประการ และ/หรือ ที่อุณหภูมิใช้งานสูง |
การหล่อสำหรับงานกัดกร่อนจะต้องสามารถตอบสนองข้อกำหนดของ ASTM A262, Practice E ได้ |
เหล็กหล่อ 18 Cr-10 Ni-Nb (คงตัว) |
+1000 |
เครื่องบิน 744 – ซีเอฟบีซี |
หากใช้สำหรับงานไฮโดรเจน ให้ระบุปริมาณ Al สูงสุด 0.012% เพื่อต้านทานการกัดกร่อนของไฮโดรเจน ชิ้นส่วนหล่อสำหรับงานกัดกร่อนจะต้องสามารถปฏิบัติตามข้อกำหนดของ ASTM A262, Practice E |
|
เหล็กหล่อ 18 Cr-10 Ni-2 Mo |
+500 |
เครื่องบิน 744 – ซีบีเอฟเอ็ม |
สำหรับชิ้นส่วนที่ไม่กักเก็บแรงดัน (ภายใน) ภายใต้สภาวะกัดกร่อนบางประการ และ/หรือ ที่อุณหภูมิใช้งานสูง |
การหล่อสำหรับงานกัดกร่อนจะต้องสามารถตอบสนองข้อกำหนดของ ASTM A262, Practice E ได้ |
เหล็กหล่อ 25 Cr-20 Ni |
+1000 |
A 297 – ฮ่องกง |
สำหรับชิ้นส่วนที่ไม่กักเก็บแรงดัน (ภายใน) ที่ต้องการความทนทานต่อความร้อน |
– |
เหล็กหล่อ 25 Cr-12 Ni |
+1000 |
A447-ประเภท II |
สำหรับรองรับท่อเตาเผา |
|
เหล็กหล่อ 18 Cr-8 Ni |
-200 ถึง +500 |
A351-CF8 |
สำหรับชิ้นส่วนที่รักษาแรงดันภายใต้สภาวะการกัดกร่อนบางประเภทและ/หรือที่อุณหภูมิใช้งานสูง |
การหล่อสำหรับงานกัดกร่อนจะต้องสามารถตอบสนองข้อกำหนดของ ASTM A262, Practice E ได้ |
เหล็กหล่อ 18 Cr-8 Ni-Nb ที่เสถียร |
(-100) ถึง +600 |
A351-CF8C |
สำหรับชิ้นส่วนที่รักษาแรงดันภายใต้สภาวะการกัดกร่อนบางประเภทและ/หรือที่อุณหภูมิใช้งานสูง |
หากต้องการใช้งานในอุณหภูมิที่สูงกว่า 500°C ต้องมีปริมาณ Si เฉพาะ 1.0% สูงสุด ชิ้นส่วนหล่อสำหรับงานกัดกร่อนจะต้องสามารถปฏิบัติตามข้อกำหนดของ ASTM A262, Practice E |
เหล็กหล่อ 18 Cr-10 Ni-2 Mo |
-200 ถึง +500 |
A351-CF8M |
สำหรับชิ้นส่วนที่รักษาแรงดันภายใต้สภาวะการกัดกร่อนบางประเภทและ/หรือที่อุณหภูมิใช้งานสูง |
การหล่อสำหรับงานกัดกร่อนจะต้องสามารถตอบสนองข้อกำหนดของ ASTM A262, Practice E ได้ |
เหล็กหล่อ 22 Cr-5 Ni-Mo-N |
+300 |
A890-4A, S32 และ S33 |
สำหรับชิ้นส่วนที่รักษาแรงดันภายใต้สภาวะกัดกร่อนบางประเภท |
|
เหล็กหล่อ 25 Cr-7 Ni-Mo-N |
+300 |
A890-5A, S32 และ S33 |
สำหรับชิ้นส่วนที่รักษาแรงดันภายใต้สภาวะกัดกร่อนบางประเภท |
|
การหล่อเหล็กกล้า 20 Cr-18 Ni-6 Mo-Cu-N |
(-200) ถึง (+400) |
A351-CK3MCuN |
สำหรับชิ้นส่วนที่รักษาแรงดันภายใต้สภาวะกัดกร่อนบางประเภท |
|
เหล็กหล่อ 25 Cr-20 Ni |
+1000 |
A351-CH20 |
สำหรับชิ้นส่วนที่รักษาแรงดันภายใต้สภาวะการกัดกร่อนบางประการที่อุณหภูมิการใช้งานที่รุนแรง |
|
เหล็กหล่อ 25 Cr-20 Ni |
+1000 |
A351-CK20 |
สำหรับชิ้นส่วนที่รักษาแรงดันภายใต้สภาวะการกัดกร่อนบางประการที่อุณหภูมิการใช้งานที่รุนแรง |
|
เหล็กหล่อ 25 Cr-20 Ni |
+1000 |
A351-HK40 |
สำหรับชิ้นส่วนที่รักษาแรงดันภายใต้สภาวะการกัดกร่อนบางประการที่อุณหภูมิการใช้งานที่รุนแรง |
|
การหล่อเหล็ก Ni-Mo-Cu 20 Cr-29 |
(+400) |
A744-CN7M |
สำหรับอุปกรณ์วาล์วและชิ้นส่วนรักษาแรงดันอื่นๆ ที่ต้องทนทานต่อการกัดกร่อนของกรดซัลฟิวริก |
|
เหล็กหล่อ Cr-Ni แบบแรงเหวี่ยงและแบบคงที่
20Cr-33Ni-Nb นิกเกิล-นิเกิล
25Cr-30Ni
25Cr-35Ni-Nb นิกเกิล- ... |
|
|
สำหรับชิ้นส่วนเตาที่รักษาแรงดันไว้ที่อุณหภูมิใช้งานที่รุนแรง |
|
แท่ง, ส่วนและลวด
การกำหนด |
อุณหภูมิโลหะ (°C) |
เอส ที เอส ที |
หมายเหตุ |
เพิ่มข้อกำหนด |
แท่งเหล็ก 1Cr-0.25 Mo |
+450 (+540) |
เอ 322 – 4140 |
สำหรับชิ้นส่วนที่ผ่านการกลึง |
|
แท่งเหล็ก Ni 9 |
-200 |
เอ 322 |
สำหรับชิ้นส่วนที่ผ่านการกลึง เพื่อการบริการที่อุณหภูมิต่ำ |
|
เหล็กเส้น 12Cr |
+425 |
A 276 – แบบ 410 หรือ แบบ 420 |
คุณภาพการกลึงแบบอิสระ ASTM A582 ประเภท 416 หรือ 416Se เป็นที่ยอมรับ โดยต้องได้รับการอนุมัติจากบริษัท |
สำหรับชิ้นงานที่เชื่อม ระบุ Type 405 |
แท่งเหล็ก 18 Cr-8 Ni |
-200 ถึง +500 |
A 479 – แบบ 304 |
สำหรับชิ้นส่วนที่ผ่านการกลึง |
วัสดุจะต้องสามารถตอบสนองข้อกำหนดของ ASTM A262 Practice E ได้ |
แท่งเหล็ก 18 Cr-8 Ni |
-200 ถึง +500 |
A 479 – ประเภท 304L |
สำหรับชิ้นส่วนที่ผ่านการกลึง |
วัสดุจะต้องสามารถตอบสนองข้อกำหนดของ ASTM A262 Practice E ได้ |
แท่งเหล็ก 18 Cr-8 Ni |
+500 (+815) |
A 479 – แบบ 304H |
สำหรับชิ้นส่วนที่ผ่านการกลึง |
ระบุ C: 0.06% สูงสุด, Mo+Ti+Nb: 0.4% สูงสุด |
แท่งเหล็กเสริมความแข็ง 18 Cr-8 Ni |
-200 (+815) |
A 479 – แบบ 321 หรือ แบบ 347 |
สำหรับชิ้นส่วนที่ผ่านการกลึง |
วัสดุจะต้องสามารถตอบสนองข้อกำหนดของ ASTM A262 Practice E ได้ |
แท่งเหล็กเสริมความแข็ง 18 Cr-8 Ni |
+500 (+815) |
A 479 – แบบ 321H หรือ แบบ 347H |
สำหรับชิ้นส่วนเครื่องจักรกล การใช้เกรดนี้ขึ้นอยู่กับข้อตกลงของบริษัท |
|
แท่งเหล็ก 18 Cr-10 Ni-2 Mo |
-200 ถึง +500 |
A 479 – แบบ 316 |
สำหรับชิ้นส่วนที่ผ่านการกลึง |
วัสดุจะต้องสามารถตอบสนองข้อกำหนดของ ASTM A262 Practice E ได้ |
แท่งเหล็ก 18 Cr-10 Ni-2 Mo |
-200 ถึง +500 |
A 479 – ประเภท 316L |
สำหรับชิ้นส่วนที่ผ่านการกลึง |
วัสดุจะต้องสามารถตอบสนองข้อกำหนดของ ASTM A262 Practice E ได้ |
แท่งเหล็ก 22 Cr-5 Ni-Mo-N |
-30 ถึง +300 |
เอ 479 – S31803 |
สำหรับชิ้นส่วนที่ผ่านการกลึง |
N 0.15% นาที. |
แท่งเหล็ก 25 Cr-7 Ni-Mo-N |
-30 ถึง +300 |
เอ 479 – S32750 |
สำหรับชิ้นส่วนที่ผ่านการกลึง |
N 0.15% นาที. |
เหล็กเส้น 20 Cr-18 Ni-6 Mo-Cu-N |
-200 (+400) |
เอ 276 – S31254 |
สำหรับชิ้นส่วนที่ผ่านการกลึง |
|
เหล็กเส้น Si-Mn |
+230 |
เอ 689/เอ 322-9260 |
สำหรับสปริง |
|
ลวดเหล็กดึงเย็น |
+230 |
เอ 227 |
สำหรับสปริง |
|
ลวดเหล็ก 18Cr-8Ni ดึงเย็น |
+230 |
ประเภท 302 |
สำหรับสปริง |
วัสดุจะต้องสามารถตอบสนองข้อกำหนดของ ASTM A262 Practice E ได้ |
การยึดน็อต
การกำหนดชื่อ |
อุณหภูมิโลหะ (°C) |
เอส ที เอส ที |
หมายเหตุ |
ข้อกำหนดเพิ่มเติม |
วัสดุยึดสลักเกลียวเหล็ก 1Cr-0.25Mo |
+450 (+540) |
เอ 193 – บี 7 |
สำหรับการใช้งานทั่วไป สำหรับน็อต โปรดดู 8.7.3 |
– |
วัสดุยึดสลักเกลียวเหล็ก 1Cr-0.25Mo |
+450 (+540) |
เอ 193 – บี 7 เอ็ม |
สำหรับบริการที่มีรสเปรี้ยว สำหรับถั่ว ดู 9.7.13 |
– |
วัสดุยึดสลักเกลียวเหล็ก 1 Cr-0.5 Mo-0.25 |
+525 (+600) |
เอ 193 – บี 16 |
สำหรับการทำงานที่อุณหภูมิสูง สำหรับน็อต โปรดดู 9.7.14 |
– |
วัสดุยึดสลักเกลียวเหล็ก 1Cr-0.25Mo |
-105 ถึง +450 (+540) |
เอ 320 – แอล 7 |
สำหรับบริการที่อุณหภูมิต่ำ สำหรับน็อต โปรดดู 9.7.15 |
– |
วัสดุยึดสลักเกลียวเหล็ก 1Cr-0.25Mo |
-30 ถึง +450 |
เอ 320 – แอล 7 เอ็ม |
สำหรับบริการที่มีรสเปรี้ยวและบริการที่อุณหภูมิต่ำ สำหรับถั่ว โปรดดู 9.7.16 |
– |
วัสดุยึดน็อตเหล็ก Ni 9 |
-200 |
– |
สำหรับบริการที่อุณหภูมิต่ำ สำหรับน็อต โปรดดู 9.7.17 |
– |
วัสดุยึดน็อตเหล็ก 12Cr |
+425 (+540) |
เอ 193 – บี 6 เอ็กซ์ |
สำหรับสภาวะกัดกร่อนบางประเภท สำหรับน็อต โปรดดู 9.7.18 |
– |
วัสดุยึดสลักเกลียวเหล็ก 18 Cr-8 Ni (ชุบแข็งด้วยความเครียด) |
-200 ถึง +815 |
A 193 – B8 ชั้น 2 |
สำหรับสภาวะกัดกร่อนบางประเภทและ/หรือการใช้งานที่อุณหภูมิสูงสุด สำหรับน็อต โปรดดู 9.7.19 |
วัสดุจะต้องสามารถตอบสนองข้อกำหนดของ ASTM A262 Practice E ได้ |
วัสดุยึดสลักเกลียวเหล็ก 18 Cr-8 Ni ที่ได้รับการปรับเสถียรภาพ |
-200 ถึง +815 |
A 193 – B8T หรือ B8C |
สำหรับสภาวะกัดกร่อนบางประเภทและ/หรือการใช้งานที่อุณหภูมิสูงสุด สำหรับน็อต โปรดดู 9.7.21 |
วัสดุจะต้องสามารถตอบสนองข้อกำหนดของ ASTM A262 Practice E ได้ |
วัสดุยึดสลักเกลียวเหล็ก 18 Cr-10 Ni-2 Mo (ชุบแข็งด้วยความเครียด) |
-200 ถึง +500 |
A 193 – BBM คลาส 2 |
สำหรับสภาวะกัดกร่อนบางประเภทและ/หรือการใช้งานที่อุณหภูมิสูง สำหรับน็อต โปรดดู 9.7.22 |
วัสดุจะต้องสามารถตอบสนองข้อกำหนดของ ASTM A262 Practice E ได้ |
วัสดุยึดสลักเกลียวเหล็ก 18 Cr-8 Ni |
-200 |
เอ 193 – บีบีเอ็น |
สำหรับบริการที่อุณหภูมิต่ำ สำหรับน็อต โปรดดู 9.7.20 |
วัสดุจะต้องสามารถตอบสนองข้อกำหนดของ ASTM A262 Practice E ได้ |
การตกตะกอนเพื่อชุบแข็งวัสดุยึดเหล็กออสเทนนิติก Ni-Cr |
+540 |
เอ 453-660 คลาสเอ |
สำหรับสภาวะกัดกร่อนบางประเภทและ/หรือการใช้งานที่อุณหภูมิสูง ค่าสัมประสิทธิ์การขยายตัวเทียบได้กับเหล็กออสเทนนิติก สำหรับน็อต โปรดดู 9.7.23 |
– |
น็อตเหล็ก 0.25 Mo |
+525 |
เอ 194 – 2เอชเอ็ม |
สำหรับการยึดด้วยสลักเกลียวที่ทำจากวัสดุตามที่กำหนดไว้ในข้อ 9.7.2 |
– |
น็อตเหล็ก 0.25 Mo |
+525 (+600) |
เอ 194 – 4 |
สำหรับการยึดด้วยสลักเกลียวที่ทำจากวัสดุตามที่กำหนดภายใต้ 9.7.3 |
– |
น็อตเหล็ก 0.25 Mo |
-105 ถึง +525 (+540) |
เอ 194 – 4, เอส 4 |
สำหรับการยึดด้วยสลักเกลียวที่ทำจากวัสดุตามที่กำหนดภายใต้ 9.7.4 |
– |
น็อตเหล็ก 0.25 Mo |
+525 |
เอ 194 – 7เอ็ม, เอส4 |
สำหรับการยึดด้วยวัสดุตามที่กำหนดในข้อ 9.7.5 |
– |
น็อตเหล็ก Ni 9 ตัว |
-200 |
– |
สำหรับการยึดด้วยสลักเกลียวที่ทำจากวัสดุตามที่กำหนดภายใต้ 9.7.6 |
– |
น็อตเหล็ก 12Cr |
+425 (+540) |
เอ 194 – 6 |
สำหรับการยึดด้วยสลักเกลียวที่ทำจากวัสดุตามที่กำหนดภายใต้ 9.7.7 ยอมรับการกลึงแบบอิสระเกรด 6F โดยต้องได้รับการอนุมัติจากบริษัท |
– |
น็อตเหล็ก 18 Cr-8 Ni (ผ่านการชุบแข็ง) |
-200 ถึง +815 |
เอ 194 – 8, เอส 1 |
สำหรับการยึดด้วยสลักเกลียวที่ทำจากวัสดุตามที่กำหนดในข้อ 9.7.8 ยอมรับการกลึงแบบอิสระเกรด 8F โดยต้องได้รับการอนุมัติจากบริษัท |
วัสดุจะต้องสามารถตอบสนองข้อกำหนดของ ASTM A262 Practice E ได้ |
น็อตเหล็ก 18 Cr-8 Ni |
-200 |
เอ 194 – 8N |
สำหรับการให้บริการอุณหภูมิต่ำ |
วัสดุจะต้องสามารถตอบสนองข้อกำหนดของ ASTM A262 Practice E ได้ |
น็อตเหล็กเสริมความแข็ง 18 Cr-8 Ni |
-200 ถึง +815 |
A 194 – 8T หรือ 8C |
สำหรับการยึดด้วยสลักเกลียวที่ทำจากวัสดุตามที่กำหนดในข้อ 9.7.9 ยอมรับการกลึงแบบอิสระเกรด 8F โดยต้องได้รับการอนุมัติจากบริษัท |
วัสดุจะต้องสามารถตอบสนองข้อกำหนดของ ASTM A262 Practice E ได้ |
น็อตเหล็ก 18 Cr-10 Ni-2 Mo (ผ่านการชุบแข็ง) |
-200 ถึง +500 |
เอ 194 – 8M, S1 |
สำหรับการยึดด้วยสลักเกลียวที่ทำจากวัสดุตามที่กำหนดภายใต้ 9.7.10 |
วัสดุจะต้องสามารถตอบสนองข้อกำหนดของ ASTM A262 Practice E ได้ |
น็อตเหล็กออสเทนนิติก Ni-Cr ชุบแข็งโดยการตกตะกอน |
+540 |
เอ 453-660 คลาสเอ |
สำหรับการยึดด้วยสลักเกลียวที่ทำจากวัสดุตามที่กำหนดภายใต้ 9.7.12 |
– |
วัสดุยึดสลักเกลียวเหล็ก 0.75 Cr-1.75 Ni, 0.25 Mo สำหรับบริการอุณหภูมิต่ำ |
+400 |
A320-L43 |
– |
– |
แนวทางการเลือกวัสดุ: โลหะที่ไม่ใช่เหล็ก
แผ่น, แผ่นและแถบ
การกำหนดชื่อ |
อุณหภูมิโลหะ (°C) |
เอส ที เอส ที |
หมายเหตุ |
ข้อกำหนดเพิ่มเติม |
แผ่นและแผ่นอลูมิเนียม |
-200 ถึง +200 |
B 209 – อัลลอย 1060 |
สำหรับสภาวะกัดกร่อนบางประเภท |
ระบุเงื่อนไขการอบอ่อนสำหรับทุกเกรด |
แผ่นและแผ่นโลหะผสม Al-2.5Mg |
-200 ถึง +200 |
B 209 – โลหะผสม 5052 |
สำหรับการใช้งานทั่วไปภายใต้สภาวะกัดกร่อนบางประการ |
ระบุเงื่อนไขการอบอ่อนสำหรับทุกเกรด |
แผ่นและแผ่นโลหะผสม Al-2.7Mg-Mn |
-200 ถึง +200 |
B 209 – อัลลอย 5454 |
สำหรับการใช้งานทั่วไปภายใต้สภาวะกัดกร่อนบางประการ |
ระบุเงื่อนไขการอบอ่อนสำหรับทุกเกรด |
แผ่นและแผ่นโลหะผสม Al-4.5Mg-Mn |
-200 ถึง +65 |
B 209 – โลหะผสม 5083 |
สำหรับการใช้งานที่อุณหภูมิต่ำ |
ระบุเงื่อนไขการอบอ่อนสำหรับทุกเกรด |
แผ่นทองแดง แผ่นบาง และแถบทองแดง |
-200 ถึง +150 |
บี 152 – ซี 12200 |
สำหรับสภาวะกัดกร่อนบางประเภท |
ระบุเงื่อนไขการอบอ่อนสำหรับทุกเกรด |
แผ่นและแผ่นโลหะผสม Cu-Zn |
-200 ถึง +175 |
บี 171 – ซี 46400 |
สำหรับแผ่นกั้นของเครื่องทำความเย็นและคอนเดนเซอร์ในระบบน้ำกร่อยและน้ำทะเล และสำหรับการใช้งานทั่วไปภายใต้สภาวะกัดกร่อนบางประการ |
ระบุเงื่อนไขการอบอ่อนสำหรับทุกเกรด |
แผ่นและแผ่นโลหะผสม Cu-Al |
-200 ถึง +250 |
บี 171 – ซี 61400 |
สำหรับแผ่นท่อของเครื่องทำความเย็นและคอนเดนเซอร์ในระบบน้ำจืดและน้ำกร่อย และสำหรับการใช้งานทั่วไปภายใต้สภาวะกัดกร่อนบางประการ |
ระบุเงื่อนไขการอบอ่อนสำหรับทุกเกรด |
แผ่นและแผ่นโลหะผสม Cu-Al |
-200 ถึง +350 |
บี 171 – ซี 63000 |
สำหรับแผ่นท่อของเครื่องทำความเย็นและคอนเดนเซอร์ในน้ำทะเลและน้ำกร่อย และสำหรับการใช้งานทั่วไปภายใต้สภาวะกัดกร่อนบางประเภท แผ่นท่อที่ผลิตโดยใช้วิธีการหล่อพิเศษจากผู้ผลิตที่ได้รับการรับรองเป็นที่ยอมรับ โดยต้องมีคุณสมบัติทางกลและองค์ประกอบทางเคมีที่สอดคล้องกับข้อกำหนดนี้ |
เนื้อหาทั้งหมดสูงสุด 10.0% |
แผ่นและแผ่นโลหะผสม Cu-Ni (90/10) |
-200 ถึง +350 |
บี 171 – ซี 70600 |
สำหรับแผ่นท่อของเครื่องทำความเย็นและคอนเดนเซอร์ในระบบน้ำกร่อยและน้ำทะเล และสำหรับการใช้งานทั่วไปภายใต้สภาวะกัดกร่อนบางประการ |
– |
แผ่นและแผ่นโลหะผสม Cu-Ni (70/30) |
-200 ถึง +350 |
บี 171 – ซี 71500 |
สำหรับสภาวะกัดกร่อนบางประเภท |
– |
แผ่นนิกเกิล แผ่น และแถบ |
-200 ถึง (+350) |
บี 162 – N02200 |
สำหรับสภาวะกัดกร่อนบางประเภท |
ระบุเงื่อนไขการอบอ่อนสำหรับทุกเกรด |
แผ่น แผ่น และแถบนิกเกิลคาร์บอนต่ำ |
-200 ถึง (+350) |
บี 162 – N02201 |
สำหรับสภาวะกัดกร่อนบางประเภท |
ระบุเงื่อนไขการอบอ่อนสำหรับทุกเกรด |
โลหะผสม Ni-Cu |
-200 |
บี 127 – |
สำหรับสภาวะกัดกร่อนบางประเภท |
ระบุเงื่อนไขการอบอ่อนสำหรับทุกเกรด |
แผ่น แผ่น และแถบโมเนล (400) |
+400 |
N04400 |
สำหรับสภาวะกัดกร่อนบางประเภท |
ระบุเงื่อนไขการอบอ่อนสำหรับทุกเกรด |
แผ่น แผ่น และแถบโลหะผสม Ni-Cr-Fe (Inconel 600) |
+650 |
บี 168 – N06600 |
สำหรับสภาวะอุณหภูมิสูงและ/หรือสภาวะกัดกร่อนบางประการ |
ระบุเงื่อนไขการอบอ่อนสำหรับทุกเกรด |
แผ่น แผ่น และแถบโลหะผสม Ni-Fe-Cr (Incoloy 800) |
+815 |
บี 409 – N08800 |
สำหรับสภาวะอุณหภูมิสูงและ/หรือสภาวะกัดกร่อนบางประการ |
ระบุ C 0.05% สูงสุด ระบุเงื่อนไขการอบอ่อนสำหรับทุกเกรด |
แผ่น แผ่น และแถบโลหะผสม Ni-Fe-Cr (Incoloy 800H) |
+1000 |
บี 409 – N08810 |
สำหรับสภาวะอุณหภูมิสูงและ/หรือสภาวะกัดกร่อนบางประการ |
ระบุเงื่อนไขการอบอ่อนสำหรับทุกเกรด |
แผ่น แผ่น และแถบโลหะผสม Ni-Fe-Cr (Incoloy 800HT) |
(+1000) |
บี 409 – N08811 |
สำหรับสภาวะอุณหภูมิสูงและ/หรือสภาวะกัดกร่อนบางประการ |
ระบุเงื่อนไขการอบอ่อนสำหรับทุกเกรด |
แผ่น แผ่น และแถบโลหะผสม Ni-Fe-Cr-Mo-Cu (Incoloy 825) |
+425 |
บี 424 – N08825 |
สำหรับสภาวะกัดกร่อนบางประเภท |
วัสดุจะต้องผ่านการทดสอบการกัดกร่อนตามเกรน Practice C ตามมาตรฐาน ASTM A262 (อัตราการกัดกร่อน ≤ 0.3 มม./ปี) |
แผ่น แผ่น และแถบโลหะผสม Ni-Cr-Mo-Nb (Inconel 625) |
+425 |
บี 443 – N06625 |
สำหรับสภาวะกัดกร่อนบางประเภท |
ไม่มีข้อมูล |
แผ่น แผ่น และแถบโลหะผสม Ni-Mo (Hastelloy B2) |
+425 |
บี 333 – N10665 |
สำหรับสภาวะกัดกร่อนบางประเภท |
ไม่มีข้อมูล |
แผ่น แผ่น และแถบโลหะผสม Ni-Mo-Cr (Hastelloy C4) |
+425 |
บี 575 – N06455 |
สำหรับสภาวะกัดกร่อนบางประเภท |
ไม่มีข้อมูล |
แผ่น แผ่น และแถบโลหะผสม Ni-Mo-Cr (Hastelloy C276) |
+425 (+650) |
บี 575 – น 10276 |
สำหรับสภาวะกัดกร่อนบางประเภท |
ไม่มีข้อมูล |
แผ่น แผ่น และแถบโลหะผสม Ni-Cr-Mo (Hastelloy C22) |
(+425) |
บี 575 – N06022 |
สำหรับสภาวะกัดกร่อนบางประเภท |
ไม่มีข้อมูล |
แผ่น,แผ่นและแถบไททาเนียม |
(+300) |
B 265 – เกรด 2 |
สำหรับสภาวะกัดกร่อนบางประเภท สำหรับซับใน คุณสมบัติแรงดึงที่ระบุไว้ในข้อมูลจำเพาะของวัสดุเป็นเพียงข้อมูลเท่านั้น |
สำหรับซับใน ให้ระบุวัสดุที่ผ่านการอบอ่อนที่มีความแข็งสูงสุด 140 HV10 วัสดุที่อ่อนกว่าเกรด 1 อาจใช้สำหรับการซับในได้เช่นกัน |
แผ่นแทนทาลัม แผ่นบาง และแถบ |
ขีดจำกัดอุณหภูมิขึ้นอยู่กับบริการ |
บี 708 – R05200 |
สำหรับสภาวะกัดกร่อนบางประเภท สำหรับซับใน คุณสมบัติแรงดึงที่ระบุไว้ในข้อมูลจำเพาะของวัสดุเป็นเพียงข้อมูลเท่านั้น |
สำหรับซับใน ให้ระบุวัสดุที่ผ่านการอบอ่อนที่มีความแข็งสูงสุด 120 HV10 |
ท่อและท่อ
การกำหนดชื่อ |
อุณหภูมิโลหะ (°C) |
เอส ที เอส ที |
หมายเหตุ |
ข้อกำหนดเพิ่มเติม |
ท่ออลูมิเนียมไร้รอยต่อ |
-200 ถึง +200 |
B 234 – อัลลอย 1060 |
สำหรับอุปกรณ์ถ่ายเทความร้อนที่ไม่ได้เผาภายใต้สภาวะกัดกร่อนบางประการ |
ระบุเงื่อนไขการอบอ่อนสำหรับทุกเกรด |
ท่อโลหะผสม Al-2.5 Mg ไร้รอยต่อ |
-200 ถึง +200 |
B 234 – โลหะผสม 5052 |
สำหรับอุปกรณ์ถ่ายเทความร้อนที่ไม่ได้เผาภายใต้สภาวะกัดกร่อนบางประการ |
ระบุเงื่อนไขการอบอ่อนสำหรับทุกเกรด |
ท่อโลหะผสม Al-2.7 Mg-Mn ไร้รอยต่อ |
-200 ถึง +200 |
B 234 – โลหะผสม 5454 |
สำหรับอุปกรณ์ถ่ายเทความร้อนที่ไม่ได้เผาภายใต้สภาวะกัดกร่อนบางประการ |
ระบุเงื่อนไขการอบอ่อนสำหรับทุกเกรด |
ท่อทองแดงไร้รอยต่อขนาดเล็ก |
-200 ถึง +150 |
บี 68 – ซี 12200 06 0 |
สำหรับสายเครื่องมือ |
ระบุเงื่อนไขการอบอ่อนสำหรับทุกเกรด |
โลหะผสม Cu-Zn-Al ไร้รอยต่อ (อลูมิเนียมทองเหลือง) |
(+200) ถึง +175 |
บี 111 – ซี 68700 |
สำหรับเครื่องทำความเย็นและคอนเดนเซอร์ในระบบน้ำกร่อยและน้ำทะเล |
ระบุเงื่อนไขการอบอ่อนสำหรับทุกเกรด |
ท่อโลหะผสมทองแดง-นิกเกิล (90/10 Cu-Ni) ไร้รอยต่อ |
-200 ถึง +350 |
บี 111 – ซี 70600 |
สำหรับอุปกรณ์ถ่ายเทความร้อนที่ไม่ได้เผาภายใต้สภาวะกัดกร่อนบางประการ |
ระบุเงื่อนไขการอบอ่อนสำหรับทุกเกรด |
ท่อโลหะผสมทองแดง-นิกเกิล (70/30 Cu-Ni) ไร้รอยต่อ |
-200 ถึง +350 |
บี 111 – ซี 71500 |
สำหรับอุปกรณ์ถ่ายเทความร้อนที่ไม่ได้เผาภายใต้สภาวะกัดกร่อนบางประการ |
ระบุเงื่อนไขการอบอ่อนสำหรับทุกเกรด |
ท่อโลหะผสมทองแดง-นิกเกิล (66/30/2/2 Cu-Ni-Fe-Mn) ไร้รอยต่อ |
-200 ถึง +350 |
บี 111 – ซี 71640 |
สำหรับอุปกรณ์ถ่ายเทความร้อนที่ไม่ได้เผาภายใต้สภาวะกัดกร่อนบางประการ |
ระบุเงื่อนไขการอบอ่อนสำหรับทุกเกรด |
ท่อโลหะนิเกิลไร้รอยต่อ |
-200 ถึง +350 |
บี 163 – N02200 |
สำหรับอุปกรณ์ถ่ายเทความร้อนที่ไม่ได้เผาภายใต้สภาวะกัดกร่อนบางประการ |
ระบุเงื่อนไขการอบอ่อนของสารละลายสำหรับทุกเกรด สำหรับท่อที่ตั้งใจใช้กับอุปกรณ์ต่อแบบอัด ความแข็งจะต้องไม่เกิน 90 HRB |
ท่อนิกเกิลคาร์บอนต่ำแบบไร้รอยต่อ |
-200 ถึง +350 |
บี 163 – N02201 |
สำหรับอุปกรณ์ถ่ายเทความร้อนที่ไม่ได้เผาภายใต้สภาวะกัดกร่อนบางประการ |
ระบุเงื่อนไขการอบอ่อนของสารละลายสำหรับทุกเกรด สำหรับท่อที่ตั้งใจใช้กับอุปกรณ์ต่อแบบอัด ความแข็งจะต้องไม่เกิน 90 HRB |
ท่อโลหะผสม Ni-Cu ไร้รอยต่อ (Monel 400) |
-200 ถึง +400 |
บี 163 – N04400 |
สำหรับอุปกรณ์ถ่ายเทความร้อนที่ไม่ได้เผาภายใต้สภาวะกัดกร่อนบางประการ |
ระบุเงื่อนไขการอบอ่อนของสารละลายสำหรับทุกเกรด สำหรับท่อที่ตั้งใจใช้กับอุปกรณ์ต่อแบบอัด ความแข็งจะต้องไม่เกิน 90 HRB |
ท่อโลหะผสม Ni-Cr-Fe (Inconel 600) ไร้รอยต่อ |
+650 |
บี 163 – N06600 |
สำหรับอุปกรณ์ถ่ายเทความร้อนที่ไม่ได้เผาภายใต้สภาวะกัดกร่อนบางประการ |
ระบุเงื่อนไขการอบอ่อนของสารละลายสำหรับทุกเกรด สำหรับท่อที่ตั้งใจใช้กับอุปกรณ์ต่อแบบอัด ความแข็งจะต้องไม่เกิน 90 HRB |
ท่อโลหะผสม Ni-Fe-Cr ไร้รอยต่อ (Incoloy 800) |
+815 |
บี 163 – N08800 |
สำหรับอุปกรณ์ถ่ายเทความร้อนที่ไม่ได้เผาภายใต้สภาวะกัดกร่อนบางประการ |
ระบุ C สูงสุด 0.05% ระบุเงื่อนไขการอบอ่อนสำหรับเกรดทั้งหมด สำหรับท่อที่ตั้งใจใช้กับอุปกรณ์ต่อแบบอัด ความแข็งจะต้องไม่เกิน 90 HRB |
ท่อโลหะผสม Ni-Fe-Cr ไร้รอยต่อ (Incoloy 800H) |
+1000 |
บี 407 – N08810 |
สำหรับเตาเผาและอุปกรณ์ถ่ายเทความร้อนที่ยังไม่ได้เผาภายใต้สภาวะกัดกร่อนบางประการ |
ระบุเงื่อนไขการอบอ่อนของสารละลายสำหรับทุกเกรด สำหรับท่อที่ตั้งใจใช้กับอุปกรณ์ต่อแบบอัด ความแข็งจะต้องไม่เกิน 90 HRB |
ท่อโลหะผสม Ni-Fe-Cr ไร้รอยต่อ (Incoloy 800 HT) |
(+1000) |
บี 407 – N08811 |
สำหรับเตาเผาและอุปกรณ์ถ่ายเทความร้อนที่ยังไม่ได้เผาภายใต้สภาวะกัดกร่อนบางประการ |
ระบุเงื่อนไขการอบอ่อนของสารละลายสำหรับทุกเกรด สำหรับท่อที่ตั้งใจใช้กับอุปกรณ์ต่อแบบอัด ความแข็งจะต้องไม่เกิน 90 HRB |
ท่อโลหะผสม Ni-Cr-Mo-Cu (Incoloy 825) ไร้รอยต่อ |
-200 ถึง +425 |
บี 163 – N08825 |
สำหรับอุปกรณ์ถ่ายเทความร้อนที่ไม่ได้เผาภายใต้สภาวะกัดกร่อนบางประการ |
ระบุเงื่อนไขการอบอ่อนที่เสถียร หากจะเชื่อมท่อเข้ากับกล่องที่มีหัว จะต้องดำเนินการทดสอบการกัดกร่อนระหว่างเกรน |
ท่อโลหะผสม Ni-Cr-Mo-Nb (Inconel 625) ไร้รอยต่อ |
+425 |
บี 444 – N06625 |
สำหรับอุปกรณ์ถ่ายเทความร้อนที่ไม่ได้เผาภายใต้สภาวะกัดกร่อนบางประการ |
ควรใช้วัสดุเกรด 1 (อบอ่อน) ที่อุณหภูมิใช้งาน 539°C หรือน้อยกว่า จะต้องดำเนินการทดสอบการกัดกร่อนตามเกรน |
ท่อโลหะผสม Ni-Mo (Hastelloy B2) ไร้รอยต่อ |
+425 |
บี 622 – N10665 |
สำหรับอุปกรณ์ถ่ายเทความร้อนที่ไม่ได้เผาภายใต้สภาวะกัดกร่อนบางประการ |
การทดสอบการกัดกร่อนระหว่างเกรนที่จะดำเนินการ |
ท่อโลหะผสม Ni-Mo (Hastelloy B2) ที่เชื่อม |
+425 |
B 626 – N10665 ชั้น 1A |
สำหรับอุปกรณ์ถ่ายเทความร้อนที่ไม่ได้เผาภายใต้สภาวะกัดกร่อนบางประการ |
การทดสอบการกัดกร่อนระหว่างเกรนที่จะดำเนินการ |
ท่อโลหะผสม Ni-Mo-Cr (Hastelloy C4) ไร้รอยต่อ |
+425 |
บี 622 – N06455 |
สำหรับอุปกรณ์ถ่ายเทความร้อนที่ไม่ได้เผาภายใต้สภาวะกัดกร่อนบางประการ |
การทดสอบการกัดกร่อนระหว่างเกรนที่จะดำเนินการ |
ท่อโลหะผสม Ni-Mo-Cr (Hastelloy C4) ที่เชื่อม |
+425 |
B 626 – N06455 ชั้น 1A |
สำหรับอุปกรณ์ถ่ายเทความร้อนที่ไม่ได้เผาภายใต้สภาวะกัดกร่อนบางประการ |
การทดสอบการกัดกร่อนระหว่างเกรนที่จะดำเนินการ |
ท่อโลหะผสม Ni-Mo-Cr (Hastelloy C276) ไร้รอยต่อ |
+425 (+650) |
บี 622 – N10276 |
สำหรับอุปกรณ์ถ่ายเทความร้อนที่ไม่ได้เผาภายใต้สภาวะกัดกร่อนบางประการ |
ระบุเงื่อนไขการอบอ่อนของสารละลายสำหรับทุกเกรด สำหรับท่อที่ตั้งใจใช้กับอุปกรณ์ต่อแบบอัด ความแข็งจะต้องไม่เกิน 90 HRB |
ท่อโลหะผสม Ni-Mo-Cr เชื่อม (Hastelloy C276) |
+425 (+650) |
B 626 – N10276 ชั้น 1A |
สำหรับอุปกรณ์ถ่ายเทความร้อนที่ไม่ได้เผาภายใต้สภาวะกัดกร่อนบางประการ |
ระบุเงื่อนไขการอบอ่อนของสารละลายสำหรับทุกเกรด สำหรับท่อที่ตั้งใจใช้กับอุปกรณ์ต่อแบบอัด ความแข็งจะต้องไม่เกิน 90 HRB |
ท่อโลหะผสม Ni-Cr-Mo (Hastelloy C22) ไร้รอยต่อ |
(+425) |
บี 622 – N06022 |
สำหรับอุปกรณ์ถ่ายเทความร้อนที่ไม่ได้เผาภายใต้สภาวะกัดกร่อนบางประการ |
การทดสอบการกัดกร่อนระหว่างเกรนที่จะดำเนินการ |
ท่อโลหะผสม Ni-Cr-Mo (Hastelloy C22) แบบเชื่อม |
(+425) |
B 626 – N06022 ชั้น 1A |
สำหรับอุปกรณ์ถ่ายเทความร้อนที่ไม่ได้เผาภายใต้สภาวะกัดกร่อนบางประการ |
การทดสอบการกัดกร่อนระหว่างเกรนที่จะดำเนินการ |
ท่อไททาเนียมไร้รอยต่อ |
(+300) |
B 338 – เกรด 2 |
สำหรับอุปกรณ์ถ่ายเทความร้อนที่ไม่ได้เผาภายใต้สภาวะกัดกร่อนบางประการ |
ไม่มีข้อมูล |
ท่อไททาเนียมเชื่อม |
(+300) |
B 338 – เกรด 2 |
สำหรับอุปกรณ์ถ่ายเทความร้อนที่ไม่ได้เผาภายใต้สภาวะกัดกร่อนบางประการ |
ไม่มีข้อมูล |
ท่อ
การกำหนดชื่อ |
อุณหภูมิโลหะ (°C) |
เอส ที เอส ที |
หมายเหตุ |
ข้อกำหนดเพิ่มเติม |
ท่ออลูมิเนียมไร้รอยต่อ |
-200 ถึง +200 |
B 241 – อัลลอย 1060 |
สำหรับสภาวะกัดกร่อนบางประเภท |
ระบุเงื่อนไขการอบอ่อนสำหรับทุกเกรด |
ท่อโลหะผสม Al-Mg-Si ไร้รอยต่อ |
-200 ถึง +200 |
B 241 – โลหะผสม 6061 |
สำหรับสภาวะกัดกร่อนบางประเภท |
ระบุเงื่อนไขการอบอ่อนสำหรับทุกเกรด |
ท่อโลหะผสม Al-Mg-Si ไร้รอยต่อ |
-200 ถึง +200 |
B 241 – โลหะผสม 6063 |
สำหรับท่อภายใต้สภาวะกัดกร่อนบางประการ |
ระบุเงื่อนไขการอบอ่อนสำหรับทุกเกรด |
ท่อโลหะผสม Al-Mg ไร้รอยต่อ |
-200 ถึง +200 |
B 241 – โลหะผสม 5052 |
สำหรับการใช้งานทั่วไปภายใต้สภาวะกัดกร่อนบางประการ |
ระบุเงื่อนไขการอบอ่อนสำหรับทุกเกรด |
ท่อโลหะผสม Al-2.7Mg-Mn ไร้รอยต่อ |
-200 ถึง +200 |
B 241 – โลหะผสม 5454 |
สำหรับการใช้งานทั่วไปภายใต้สภาวะกัดกร่อนบางประการ |
ระบุเงื่อนไขการอบอ่อนสำหรับทุกเกรด |
ท่อโลหะผสม Al-4.5Mg-Mn ไร้รอยต่อ |
-200 ถึง +65 |
B 241 – โลหะผสม 5083 |
สำหรับบริการอุณหภูมิต่ำเท่านั้น |
ระบุเงื่อนไขการอบอ่อนสำหรับทุกเกรด |
ท่อทองแดงไร้รอยต่อ |
-200 ถึง +200 |
บี 42 – ซี 12200 |
สำหรับสภาวะกัดกร่อนบางประเภท |
ระบุเงื่อนไขการอบอ่อนสำหรับทุกเกรด |
ท่อโลหะผสม Cu-Zn-Al ไร้รอยต่อ (อลูมิเนียม ทองเหลือง) |
-200 ถึง +175 |
บี 111 – ซี 68700 |
สำหรับบริการน้ำกร่อยและน้ำทะเล |
ระบุเงื่อนไขการอบอ่อนสำหรับทุกเกรด |
ท่อโลหะผสม Cu-Ni (90/10 Cu-Ni) ไร้รอยต่อ |
-200 ถึง +350 |
บี 466 – ซี 70600 |
สำหรับบริการน้ำทะเล |
ระบุเงื่อนไขการอบอ่อนสำหรับทุกเกรด |
ท่อโลหะผสม Cu-Ni (70/30 Cu-Ni) ไร้รอยต่อ |
-200 ถึง +350 |
บี 466 – ซี 71500 |
สำหรับสภาวะกัดกร่อนบางประเภท |
ระบุเงื่อนไขการอบอ่อนสำหรับทุกเกรด |
ท่อนิกเกิลไร้รอยต่อ |
-200 ถึง +350 |
บี 161 – N02200 |
สำหรับสภาวะกัดกร่อนบางประเภท |
ระบุเงื่อนไขการแปรรูปแบบเย็น อบอ่อน และดอง สำหรับทุกเกรด |
ท่อนิกเกิลคาร์บอนต่ำไร้รอยต่อ |
-200 ถึง +350 |
บี 161 – N02201 |
สำหรับสภาวะกัดกร่อนบางประเภท |
ระบุเงื่อนไขการแปรรูปแบบเย็น อบอ่อน และดอง สำหรับทุกเกรด |
ท่อโลหะผสม Ni-Fe-Cr ไร้รอยต่อ (Incoloy 800) |
-200 ถึง +815 |
บี 407 – N08800 |
สำหรับสภาวะอุณหภูมิสูงและ/หรือสภาวะกัดกร่อนบางประการ |
ระบุเงื่อนไขการขึ้นรูปเย็น อบอ่อน และดองสำหรับเกรดทั้งหมด ระบุ C 0.05% สูงสุด |
ท่อโลหะผสม Ni-Fe-Cr ไร้รอยต่อ (Incoloy 800H) |
+1000 |
บี 407 – N08810 |
สำหรับสภาวะอุณหภูมิสูงและ/หรือสภาวะกัดกร่อนบางประการ |
ระบุเงื่อนไขการแปรรูปแบบเย็น อบอ่อน และดอง สำหรับทุกเกรด |
ท่อโลหะผสม Ni-Fe-Cr ไร้รอยต่อ (Incoloy 800HT) |
+1000 |
บี 407 – N08811 |
สำหรับสภาวะอุณหภูมิสูงและ/หรือสภาวะกัดกร่อนบางประการ |
ระบุเงื่อนไขการแปรรูปแบบเย็น อบอ่อน และดอง สำหรับทุกเกรด |
ท่อโลหะผสม Ni-Cr-Fe ไร้รอยต่อ (Inconel 600) |
+650 |
บี 167 – N06600 |
สำหรับสภาวะอุณหภูมิสูงและ/หรือสภาวะกัดกร่อนบางประการ |
ระบุเงื่อนไขการแปรรูปแบบเย็น อบอ่อน และดอง สำหรับทุกเกรด |
ท่อโลหะผสมทองแดง (โมเนล 400) |
+400 |
N04400 |
สำหรับสภาวะกัดกร่อนบางประเภท |
ระบุเงื่อนไขการอบและดองสำหรับเกรดทั้งหมด |
ท่อโลหะผสม Ni-Fe-Cr-Mo-Cu (Incoloy 825) ไร้รอยต่อ |
-200 ถึง +425 |
บี 423 – N08825 |
สำหรับสภาวะกัดกร่อนบางประเภท |
ระบุเงื่อนไขการขึ้นรูปเย็น อบอ่อน และดองสำหรับเกรดทั้งหมด ต้องผ่านการทดสอบการกัดกร่อนตามเกรนเกรน (ASTM A262) อัตราการกัดกร่อน ≤ 0.3 มม./ปี |
ท่อโลหะผสม Ni-Fe-Cr-Mo-Cu (Incoloy 825) เชื่อม |
-200 ถึง +425 |
B 705 – N08825 ชั้น 2 |
สำหรับสภาวะกัดกร่อนบางประเภท |
ระบุเงื่อนไขการขึ้นรูปเย็นและการอบอ่อน ต้องผ่านการทดสอบการกัดกร่อนตามเกรนเกรน (ASTM A262) อัตราการกัดกร่อน ≤ 0.3 มม./ปี |
ท่อโลหะผสม Ni-Cr-Mo-Nb ไร้รอยต่อ (Inconel 625) |
+425 |
บี 444 – N06625 |
สำหรับสภาวะกัดกร่อนบางประเภท |
ระบุเงื่อนไขการขึ้นรูปเย็นและอบอ่อนสำหรับทุกเกรด |
ท่อโลหะผสม Ni-Cr-Mo-Nb (Inconel 625) ที่เชื่อมแล้ว |
+425 |
B 705 – N06625 ชั้น 2 |
สำหรับสภาวะกัดกร่อนบางประเภท |
ระบุเงื่อนไขการขึ้นรูปเย็นและการอบอ่อนแบบสดใส |
ท่อโลหะผสม Ni-Mo ไร้รอยต่อ (Hastelloy B2) |
+425 |
บี 622 – N10665 |
สำหรับสภาวะกัดกร่อนบางประเภท |
|
ท่อโลหะผสม Ni-Mo (Hastelloy B2) เชื่อม |
+425 |
บี 619 – N10665 |
สำหรับสภาวะกัดกร่อนบางประเภท |
|
ท่อโลหะผสม Ni-Mo ไร้รอยต่อ (Hastelloy C4) |
+425 |
บี 622 – N06455 |
สำหรับสภาวะกัดกร่อนบางประเภท |
|
ท่อโลหะผสม Ni-Mo-Cr (Hastelloy C4) ที่เชื่อมแล้ว |
+425 |
B 619 – N06455 คลาส II |
สำหรับสภาวะกัดกร่อนบางประเภท |
|
ท่อโลหะผสม Ni-Mo-Cr (Hastelloy C276) ไร้รอยต่อ |
+425 ถึง +650 |
บี 622 – N10276 |
สำหรับสภาวะกัดกร่อนบางประเภท |
|
ท่อโลหะผสม Ni-Mo-Cr เชื่อม (Hastelloy C276) |
+425 ถึง +650 |
B 619 – N10276 คลาส II |
สำหรับสภาวะกัดกร่อนบางประเภท |
|
ท่อโลหะผสม Ni-Cr-Mo (Hastelloy C22) ไร้รอยต่อ |
+425 |
บี 622 – N06022 |
สำหรับสภาวะกัดกร่อนบางประเภท |
|
ท่อโลหะผสม Ni-Cr-Mo (Hastelloy C22) ที่เชื่อมแล้ว |
+425 |
B 619 – N06022 คลาส II |
สำหรับสภาวะกัดกร่อนบางประเภท |
|
ท่อไททาเนียมไร้รอยต่อ |
(+300) |
B 338 – เกรด 2 |
สำหรับสภาวะกัดกร่อนบางประเภท |
|
ท่อไททาเนียมเชื่อม |
(+300) |
B 338 – เกรด 2 |
สำหรับสภาวะกัดกร่อนบางประเภท |
|
ท่อไททาเนียมไร้รอยต่อสำหรับสภาวะกัดกร่อน |
+300 |
B861 เกรด 2 อบอ่อน |
|
|
ท่อไททาเนียมเชื่อมสำหรับสภาวะกัดกร่อน |
+300 |
B862 เกรด 2 อบอ่อน |
|
|
งานตีขึ้นรูป หน้าแปลน และอุปกรณ์ประกอบ
การกำหนดชื่อ |
อุณหภูมิโลหะ (°C) |
เอส ที เอส ที |
หมายเหตุ |
ข้อกำหนดเพิ่มเติม |
การตีขึ้นรูปโลหะผสม Al-2.5Mg |
-200 ถึง +200 |
โลหะผสม 5052 |
สำหรับการใช้งานทั่วไปภายใต้สภาวะกัดกร่อนบางประการ |
ระบุเงื่อนไขการอบอ่อนสำหรับทุกเกรด สั่งซื้อตามมาตรฐาน ASTM B 247, ASME VIII, Div. 1, para UG 15 |
การตีขึ้นรูปโลหะผสม Al-2.7Mg-Mn |
-200 ถึง +200 |
อัลลอย 5454 |
สำหรับการใช้งานทั่วไปภายใต้สภาวะกัดกร่อนบางประการ |
ระบุเงื่อนไขการอบอ่อนสำหรับทุกเกรด สั่งซื้อตามมาตรฐาน ASTM B 247, ASME VIII, Div. 1, para UG 15 |
การตีขึ้นรูปโลหะผสม Al-4.5Mg-Mn |
-200 ถึง +65 |
B 247 – โลหะผสม 5083 |
สำหรับบริการอุณหภูมิต่ำเท่านั้น |
ระบุเงื่อนไขการอบอ่อนสำหรับทุกเกรด |
การตีขึ้นรูปโลหะผสม Al-Mg-Si |
-200 ถึง +200 |
B 247 – โลหะผสม 6061 |
สำหรับสภาวะกัดกร่อนบางประการและ/หรือบริการที่อุณหภูมิต่ำ |
ระบุเงื่อนไขการอบอ่อนสำหรับทุกเกรด |
อุปกรณ์เชื่อมโลหะผสม Al-Mg-Si |
-200 ถึง +200 |
บี 361 – วพ 6061 |
สำหรับสภาวะกัดกร่อนบางประการและ/หรือบริการที่อุณหภูมิต่ำ |
ระบุเงื่อนไขการอบอ่อนสำหรับทุกเกรด |
อุปกรณ์เชื่อมโลหะผสม Al-2.5Mg |
-200 ถึง +200 |
โลหะผสม WP 5052 หรือ WP 5052W |
สำหรับบรรยากาศทางทะเลและการใช้งานทั่วไปภายใต้สภาวะกัดกร่อนบางประการ |
ระบุเงื่อนไขการอบอ่อนสำหรับทุกเกรด สั่งซื้อตามมาตรฐาน ASTM B 361, ASME VIII, Div. 1, para UG 15 |
อุปกรณ์เชื่อมโลหะผสม Al-2.7Mg-Mn |
-200 ถึง +200 |
โลหะผสม WP 5454 หรือ WP 5454W |
สำหรับบรรยากาศทางทะเลและการใช้งานทั่วไปภายใต้สภาวะกัดกร่อนบางประการ |
ระบุเงื่อนไขการอบอ่อนสำหรับทุกเกรด สั่งซื้อตามมาตรฐาน ASTM B 361, ASME VIII, Div. 1, para UG 15 |
อุปกรณ์เชื่อมนิเกิล |
(+325) |
B 366 – WPNS หรือ WPNW |
สำหรับสภาวะกัดกร่อนบางประเภท |
ระบุเงื่อนไขการอบอ่อนสำหรับทุกเกรด |
อุปกรณ์เชื่อมนิเกิลคาร์บอนต่ำ |
(+600) |
B 366 – WPNL หรือ WPNLW |
สำหรับสภาวะกัดกร่อนบางประเภท |
ระบุเงื่อนไขการอบอ่อนสำหรับทุกเกรด |
การตีขึ้นรูปโลหะผสม Ni-Cu (Monel 400) |
-200 ถึง +400 |
บี 564 – N04400 |
สำหรับสภาวะกัดกร่อนบางประเภท |
ระบุเงื่อนไขการอบอ่อนของสารละลายสำหรับทุกเกรด |
อุปกรณ์เชื่อมโลหะผสม Ni-Cu (Monel 400) |
-200 ถึง +400 |
B 366 – WPNCS หรือ WPNCW |
สำหรับสภาวะกัดกร่อนบางประเภท |
ระบุเงื่อนไขการอบอ่อนของสารละลายสำหรับทุกเกรด |
การตีขึ้นรูปโลหะผสม Ni-Cu (Monel 400) |
+650 |
บี 564 – N06600 |
สำหรับสภาวะอุณหภูมิสูงและ/หรือสภาวะกัดกร่อนบางประการ |
ระบุเงื่อนไขการอบอ่อนของสารละลายสำหรับทุกเกรด |
การตีขึ้นรูปโลหะผสม Ni-Cr-Fe (Inconel 600) |
+650 |
B 366 – WPNCS หรือ WPNC1W |
สำหรับสภาวะอุณหภูมิสูงและ/หรือสภาวะกัดกร่อนบางประการ |
ระบุเงื่อนไขการอบอ่อนของสารละลายสำหรับทุกเกรด |
การตีขึ้นรูปโลหะผสม Ni-Fe-Cr (Incoloy 800) |
+815 |
B 564 – อัลลอยด์ N08800 |
สำหรับการบริการที่อุณหภูมิที่รุนแรง |
ระบุเงื่อนไขการอบอ่อนของสารละลายสำหรับทุกเกรด ระบุ C ≤ 0.05% |
การตีขึ้นรูปโลหะผสม Ni-Fe-Cr (Incoloy 800H) |
+1000 |
บี 564 – N08810 |
สำหรับการบริการที่อุณหภูมิที่รุนแรง |
ระบุเงื่อนไขการอบอ่อนของสารละลายสำหรับทุกเกรด ต้องทำการทดสอบการกัดกร่อนที่เหมาะสม |
การตีขึ้นรูปโลหะผสม Ni-Fe-Cr-Mo-Cu (Incoloy 825) |
(-200) ถึง +450 |
บี 564 – N08825 |
สำหรับการบริการที่อุณหภูมิที่รุนแรง |
ระบุเงื่อนไขการอบอ่อนของสารละลายสำหรับทุกเกรด วัสดุจะต้องผ่านการทดสอบการกัดกร่อนตามเกรน Practice C ตามที่ระบุไว้ใน ASTM A262 (อัตราการกัดกร่อนในการทดสอบนี้จะต้องไม่เกิน 0.3 มม./ปี) |
โลหะผสม Ni-Fe-Cr-Mo |
(-200) |
บี 366 – |
สำหรับการบริการที่อุณหภูมิที่รุนแรง |
ระบุเงื่อนไขการอบอ่อนของสารละลาย ดำเนินการทดสอบการกัดกร่อนระหว่างเกรน |
อุปกรณ์เชื่อมโลหะผสมทองแดง (Incoloy 825) |
+450 |
WPNI CMCS หรือ WPNI CMCW |
|
ระบุเงื่อนไขการอบอ่อนของสารละลายสำหรับทุกเกรด วัสดุจะต้องผ่านการทดสอบการกัดกร่อนตามเกรน Practice C ตามที่ระบุไว้ใน ASTM A262 (อัตราการกัดกร่อนในการทดสอบนี้จะต้องไม่เกิน 0.3 มม./ปี) |
อุปกรณ์เชื่อมโลหะผสม Ni-Mo (Hastelloy B2) |
+425 |
B 366 – WPHB2S หรือ WPHB2W |
สำหรับสภาวะกัดกร่อนบางประเภท |
ระบุเงื่อนไขการอบอ่อนของสารละลายสำหรับทุกเกรด |
อุปกรณ์เชื่อมโลหะผสม Ni-Mo-Cr (Hastelloy C4) |
+425 |
บี 366 – WPHC4 |
สำหรับสภาวะกัดกร่อนบางประเภท |
ระบุเงื่อนไขการอบอ่อนของสารละลายสำหรับทุกเกรด ต้องทำการทดสอบการกัดกร่อนระหว่างเกรน |
อุปกรณ์เชื่อมโลหะผสม Ni-Mo-Cr (Hastelloy C276) |
+800 |
บี 366 – WPHC276 |
สำหรับสภาวะกัดกร่อนบางประเภท |
ระบุเงื่อนไขการอบอ่อนของสารละลายสำหรับทุกเกรด ต้องทำการทดสอบการกัดกร่อนระหว่างเกรน |
การตีขึ้นรูปโลหะผสม Ni-Cr-Mo (Hastelloy C22) |
+425 |
บี 564 – N06022 |
สำหรับสภาวะกัดกร่อนบางประเภท |
ระบุเงื่อนไขการอบอ่อนของสารละลายสำหรับทุกเกรด |
อุปกรณ์เชื่อมโลหะผสม Ni-Cr-Mo (Hastelloy C22) |
+425 |
B 366 – WPHC22S หรือ WPHC22W |
สำหรับสภาวะกัดกร่อนบางประเภท |
ระบุเงื่อนไขการอบอ่อนของสารละลายสำหรับทุกเกรด ต้องทำการทดสอบการกัดกร่อนระหว่างเกรน |
การตีขึ้นรูปด้วยไทเทเนียม |
+300 |
B 381 – เกรด F2 |
สำหรับสภาวะกัดกร่อนบางประเภท |
ระบุเงื่อนไขการอบอ่อนสำหรับทุกเกรด |
อุปกรณ์เชื่อมไททาเนียม |
+300 |
B 363 – WPT2 หรือ WPT2W |
สำหรับสภาวะกัดกร่อนบางประเภท |
ระบุเงื่อนไขการอบอ่อนสำหรับทุกเกรด |
การหล่อ
การกำหนด |
อุณหภูมิโลหะ (°C) |
เอส ที เอส ที |
หมายเหตุ |
เพิ่มข้อกำหนด |
การหล่อโลหะผสม Al-Si |
-200 ถึง +200 |
B 26 – โลหะผสม B443.0 |
สำหรับสภาวะกัดกร่อนบางประเภท |
ระบุโลหะผสม B100 B443.0 สำหรับการหล่อแม่พิมพ์แบบถาวร |
การหล่อโลหะผสม Al-12Si |
-200 ถึง +200 |
– |
สำหรับสภาวะกัดกร่อนบางประเภท |
– |
งานหล่อบรอนซ์ผสม (บรอนซ์ 85/5/5/5) |
-200 ถึง +175 |
บี 62 – ซี 83600 |
สำหรับหน้าแปลน อุปกรณ์ และวาล์ว |
– |
หล่อบรอนซ์ดีบุก (บรอนซ์ 88/10/2) |
-200 ถึง +175 |
บี 584 – ซี 90500 |
สำหรับชิ้นส่วนอุปกรณ์ที่ใช้ในงานน้ำกร่อยและน้ำทะเลและสำหรับสภาวะกัดกร่อนบางประเภท |
– |
งานหล่อบรอนซ์ Ni-Al |
-200 ถึง +350 |
บี 148 – ซี 95800 |
สำหรับชิ้นส่วนอุปกรณ์ที่ใช้ในงานน้ำกร่อยและน้ำทะเลและสำหรับสภาวะกัดกร่อนบางประเภท |
– |
ตะกั่วในรูปหมู |
+100 |
B 29 – สารเคมี – ทองแดง ตะกั่ว UNS L55112 |
สำหรับการบุอุปกรณ์ที่เป็นเนื้อเดียวกันภายใต้สภาวะกัดกร่อนบางประการ |
– |
การหล่อโลหะผสม Ni-Cu (Monel 400) |
-200 ถึง +400 |
เอ 494 – เอ็ม 35-1 |
สำหรับสภาวะกัดกร่อนบางประเภท |
– |
การหล่อโลหะผสม Ni-Mo (Hastelloy B2) |
+425 |
A 494 – N-7M ชั้น 1 |
สำหรับสภาวะกัดกร่อนบางประเภท |
– |
การหล่อโลหะผสม Ni-Mo-Cr (Hastelloy C4) |
+425 |
เอ 494 – ซีดับเบิลยู-2เอ็ม |
สำหรับสภาวะกัดกร่อนบางประเภท |
– |
การหล่อโลหะผสม Ni-Mo-Cr (Hastelloy C276) |
+425 ถึง +650 |
A 494 – CW-12MW คลาส 1 |
สำหรับสภาวะกัดกร่อนบางประเภท |
– |
การหล่อโลหะผสม 50Cr-50Ni-Nb |
+1000 |
A560 – 50Cr-50Ni-Cb |
สำหรับรองรับท่อเตาเผาที่สัมผัสกับการโจมตีของวาเนเดียม |
– |
งานหล่อไททาเนียม |
+250 |
B367 – เกรด C2 |
สำหรับสภาวะกัดกร่อนบางประเภท |
– |
แท่ง, ส่วนและลวด
การกำหนด |
อุณหภูมิโลหะ (°C) |
เอส ที เอส ที |
หมายเหตุ |
เพิ่มข้อกำหนด |
แท่งอลูมิเนียมรีดขึ้นรูป แท่งเหล็ก รูปตัด (รวมถึงรูปกลวง) ท่อ และลวด |
-200 ถึง +200 |
B 221 – อัลลอย 1060 |
สำหรับสภาวะกัดกร่อนบางประเภท |
สำหรับเหล็กเส้น แท่งเหล็ก และเหล็กแผ่น ให้ระบุเงื่อนไขการอบอ่อนสำหรับทุกเกรด สำหรับลวด ให้ระบุเงื่อนไขสำหรับแต่ละกรณีแยกกัน |
แท่งโลหะผสม Al-2.5 Mg รีดขึ้นรูป แท่งยาว ส่วนต่างๆ (รวมถึงส่วนกลวง) ท่อ และลวด |
-200 ถึง +200 |
B 221 – โลหะผสม 5052 |
สำหรับการใช้งานทั่วไปภายใต้สภาวะกัดกร่อนบางประการ |
สำหรับเหล็กเส้น แท่งเหล็ก และเหล็กแผ่น ให้ระบุเงื่อนไขการอบอ่อนสำหรับทุกเกรด สำหรับลวด ให้ระบุเงื่อนไขสำหรับแต่ละกรณีแยกกัน |
แท่งโลหะผสม Al-2.7 Mg-Mn รีดขึ้นรูป แท่ง ส่วนต่างๆ (รวมถึงส่วนกลวง) ท่อ และลวด |
-200 ถึง +200 |
B 221 – อัลลอย 5454 |
สำหรับการใช้งานทั่วไปภายใต้สภาวะกัดกร่อนบางประการ |
สำหรับเหล็กเส้น แท่งเหล็ก และเหล็กแผ่น ให้ระบุเงื่อนไขการอบอ่อนสำหรับทุกเกรด สำหรับลวด ให้ระบุเงื่อนไขสำหรับแต่ละกรณีแยกกัน |
แท่งโลหะผสม Al-Mg-Si รีดขึ้นรูป |
-200 ถึง +200 |
B 221 – โลหะผสม 6063 |
สำหรับวัตถุประสงค์ทั่วไป |
สำหรับเหล็กเส้น เหล็กเส้น และเหล็กรูปพรรณต่างๆ ให้ระบุเงื่อนไขการอบอ่อนสำหรับเกรดทั้งหมด |
แท่งทองแดง, แท่งทองแดง และแผ่นทองแดง |
-200 ถึง +150 |
บี 133 – ซี 11000 |
เพื่อวัตถุประสงค์ทางไฟฟ้า |
สำหรับเหล็กเส้น แท่งเหล็ก และเหล็กแผ่น ให้ระบุเงื่อนไขการอบอ่อนสำหรับทุกเกรด สำหรับลวด ให้ระบุเงื่อนไขสำหรับแต่ละกรณีแยกกัน |
แท่งทองแดง, แท่งทองแดง และแผ่นทองแดง |
-200 ถึง +150 |
บี 133 – ซี 12200 |
สำหรับวัตถุประสงค์ทั่วไป |
สำหรับเหล็กเส้น แท่งเหล็ก และเหล็กแผ่น ให้ระบุเงื่อนไขการอบอ่อนสำหรับทุกเกรด สำหรับลวด ให้ระบุเงื่อนไขสำหรับแต่ละกรณีแยกกัน |
แท่งโลหะผสม Cu-Zn, แท่งเหล็ก และส่วนตัดต่างๆ ได้ฟรี |
-200 ถึง +175 |
บี 16 – ซี 36000 |
สำหรับวัตถุประสงค์ทั่วไป |
สำหรับเหล็กเส้น แท่งเหล็ก และเหล็กแผ่น ให้ระบุเงื่อนไขการอบอ่อนสำหรับทุกเกรด สำหรับลวด ให้ระบุเงื่อนไขสำหรับแต่ละกรณีแยกกัน |
แท่งโลหะผสม Cu-Zn-Pb และส่วนตัดขวาง |
-200 ถึง +150 |
B140 – C32000 หรือ C31400 |
สำหรับวัตถุประสงค์ทั่วไป |
สำหรับเหล็กเส้น แท่งเหล็ก และเหล็กแผ่น ให้ระบุเงื่อนไขการอบอ่อนสำหรับทุกเกรด สำหรับลวด ให้ระบุเงื่อนไขสำหรับแต่ละกรณีแยกกัน |
แท่งโลหะผสม Cu-Al และแท่งเหล็ก |
-200 ถึง +350 |
บี 150 – ซี 63200 |
สำหรับวัตถุประสงค์ทั่วไปภายใต้สภาวะกัดกร่อนบางประการ |
– |
แท่งโลหะผสม Cu-Ni (90/10) แท่งและส่วนต่างๆ |
-200 ถึง +350 |
บี 122 – ซี 706 |
สำหรับสภาวะกัดกร่อนบางประเภท |
– |
แท่งโลหะผสม Cu-Ni (70/30) แท่งและหน้าตัด |
-200 ถึง +350 |
บี 122 – ซี 71500 |
สำหรับสภาวะกัดกร่อนบางประเภท |
– |
ลวดฟอสเฟอร์บรอนซ์ |
-200 ถึง +175 |
B 159 – C51000 สภาพ H08 (Spring Temper) |
สำหรับสปริง |
– |
แท่งและแท่งนิกเกิล |
(+325) |
บี 160 – N02200 |
สำหรับสภาวะกัดกร่อนบางประเภท |
สำหรับแท่งและแท่งเหล็ก ให้ระบุเงื่อนไขการอบอ่อนสำหรับทุกเกรด สำหรับลวด ให้ตกลงเงื่อนไขสำหรับแต่ละกรณีเป็นรายบุคคล |
แท่งและแท่งนิกเกิลคาร์บอนต่ำ |
-200 +350 |
บี 160 – N02201 |
สำหรับสภาวะกัดกร่อนบางประเภท |
สำหรับแท่งและแท่งเหล็ก ให้ระบุเงื่อนไขการอบอ่อนสำหรับทุกเกรด สำหรับลวด ให้ตกลงเงื่อนไขสำหรับแต่ละกรณีเป็นรายบุคคล |
แท่ง แท่งเหล็ก และลวดโลหะผสม Ni-Cu (Monel 400) |
-200 +400 |
บี 164 – N04400 |
สำหรับสภาวะกัดกร่อนบางประเภท |
สำหรับแท่งและแท่งเหล็ก ให้ระบุเงื่อนไขการอบอ่อนสำหรับทุกเกรด สำหรับลวด เงื่อนไขต้องตกลงกันสำหรับแต่ละกรณี |
โลหะผสม Ni-Cu-Al (Monel K500) แท่ง แท่ง และลวด |
-200 +400 |
– |
สำหรับสภาวะกัดกร่อนบางประเภทที่ต้องการความแข็งแรงแรงดึงสูง |
ควรจัดหาแท่งและแท่งในสภาพที่ผ่านการบำบัดด้วยสารละลายและแข็งตัวโดยการตกตะกอน |
แท่ง แท่งเหล็ก และลวดโลหะผสม Ni-Cr-Fe (Inconel 600) |
+650 |
บี 166 – N06600 |
สำหรับสภาวะอุณหภูมิสูงและ/หรือสภาวะกัดกร่อนบางประการ |
สำหรับแท่งและแท่งเหล็ก ให้ระบุเงื่อนไขการอบอ่อนสำหรับทุกเกรด สำหรับลวด เงื่อนไขต้องตกลงกันสำหรับแต่ละกรณี |
แท่งและแท่งโลหะผสม Ni-Cr-Mo-Nb (Inconel 625) |
+425 |
บี 446 – N06625 |
สำหรับสภาวะกัดกร่อนบางประเภท |
สำหรับแท่งและแท่งเหล็ก ให้ระบุเงื่อนไขการอบอ่อนสำหรับทุกเกรด สำหรับลวด เงื่อนไขต้องตกลงกันสำหรับแต่ละกรณี |
แท่ง แท่งเหล็ก และลวดโลหะผสม Ni-Fe-Cr (Incoloy 800) |
+815 |
บี 408 – N08800 |
สำหรับสภาวะอุณหภูมิสูงและ/หรือสภาวะกัดกร่อนบางประการ |
ระบุ C 0.05% สูงสุด |
แท่ง แท่งเหล็ก และลวดโลหะผสม Ni-Fe-Cr (Incoloy 800HT) |
+1000 |
บี 408 – N08810 |
สำหรับสภาวะอุณหภูมิสูงและ/หรือสภาวะกัดกร่อนบางประการ |
– |
แท่ง แท่งเหล็ก และลวดโลหะผสม Ni-Fe-Cr (Incoloy 800H) |
(+1000) |
บี 408 – N08811 |
สำหรับสภาวะอุณหภูมิสูงและ/หรือสภาวะกัดกร่อนบางประการ |
– |
แท่ง แท่งเหล็ก และลวดโลหะผสม Ni-Fe-Cr-Mo-Cu (Incoloy 825) |
(+425) |
บี 425 – N08825 |
สำหรับสภาวะกัดกร่อนบางประเภท |
การทดสอบการกัดกร่อนระหว่างเกรนที่จะดำเนินการ |
แท่งและแท่งโลหะผสม Ni-Mo (Hastelloy B2) |
(+425) |
บี 335 – N10665 |
สำหรับสภาวะกัดกร่อนบางประเภท |
– |
แท่งโลหะผสม Ni-Mo-Cr (Hastelloy C4) |
(+425) |
บี 574 – N06455 |
สำหรับสภาวะกัดกร่อนบางประเภท |
– |
แท่งโลหะผสม Ni-Mo-Cr (Hastelloy C276) |
(+800) |
บี 574 – น 10276 |
สำหรับสภาวะกัดกร่อนบางประเภท |
– |
แท่งโลหะผสม Ni-Cr-Mo (Hastelloy C22) สำหรับสภาวะกัดกร่อนบางประเภท |
(+425) |
บี 574 – N06022 |
สำหรับสภาวะกัดกร่อนบางประเภท |
– |
แท่งไททาเนียม |
(+300) |
B 348 – เกรด 2 |
สำหรับสภาวะกัดกร่อนบางประเภท |
ระบุเงื่อนไขการอบอ่อน |
การยึดน็อต
การกำหนด |
อุณหภูมิโลหะ (°C) |
เอส ที เอส ที |
หมายเหตุ |
เพิ่มข้อกำหนด |
น็อตและน๊อตโลหะผสมอลูมิเนียม |
-200 +200 |
F467/468 – A96061 |
วัสดุการยึดสลักเกลียวอาจเลือกจากแท่งที่ระบุในตารางด้านบนได้ |
– |
สลักเกลียวและน็อตโลหะผสม Cu-Al |
-200 +365 |
F467/468 – C63000 |
วัสดุการยึดสลักเกลียวอาจเลือกจากแท่งที่ระบุในตารางด้านบนได้ |
– |
น็อตและสลักเกลียวโลหะผสม Cu-Ni (70/30) |
-200 +350 |
F467/468 – C71500 |
วัสดุการยึดสลักเกลียวอาจเลือกจากแท่งที่ระบุในตารางด้านบนได้ |
– |
สลักเกลียวและน็อตโลหะผสม Ni-Cu (Monel 400) |
-200 +400 |
F467/468 – N04400 |
วัสดุการยึดสลักเกลียวอาจเลือกจากแท่งที่ระบุในตารางด้านบนได้ |
– |
สลักเกลียวและน็อตโลหะผสม Ni-Cu-Al (Monel K500) |
-200 +400 |
F467/468 – N05500 |
วัสดุการยึดสลักเกลียวอาจเลือกจากแท่งที่ระบุในตารางด้านบนได้ |
– |
สลักเกลียวและน็อตโลหะผสม Ni-Mo (Hastelloy B) |
+425 |
F467/468 – N10001 |
วัสดุการยึดสลักเกลียวอาจเลือกจากแท่งที่ระบุในตารางด้านบนได้ |
– |
สลักเกลียวและน็อตโลหะผสม Ni-Mo-Cr (Hastelloy C276) |
(+800) |
F467/468 – N10276 |
วัสดุการยึดสลักเกลียวอาจเลือกจากแท่งที่ระบุในตารางด้านบนได้ |
– |
น็อตและน๊อตไททาเนียม |
(+300) |
F467/468 – โลหะผสม Ti 2 |
สลักเกลียวได้รับการออกแบบมาโดยเฉพาะเพื่อใช้ภายในอุปกรณ์ |
– |
บทสรุป: การเลือกวัสดุที่เหมาะสมสำหรับโครงการของคุณตามแนวทางการเลือกวัสดุ
การเลือกวัสดุที่ถูกต้องตามแนวทางการเลือกใช้วัสดุสำหรับการใช้งานในอุตสาหกรรมเป็นกระบวนการที่ละเอียดอ่อนซึ่งสร้างสมดุลให้กับปัจจัยต่างๆ เช่น ความต้านทานการกัดกร่อน ความแข็งแรงเชิงกล ความเสถียรทางความร้อน และความคุ้มทุน โลหะผสมนิกเกิล โมเนล ฮาสเทลลอย และไททาเนียมโดดเด่นด้วยความสามารถในการทำงานภายใต้สภาวะที่รุนแรง ทำให้มีค่าอย่างยิ่งสำหรับอุตสาหกรรมต่างๆ เช่น น้ำมันและก๊าซ อวกาศ และการแปรรูปทางเคมี การปรับคุณสมบัติของวัสดุให้สอดคล้องกับข้อกำหนดในการปฏิบัติงาน ธุรกิจต่างๆ จะสามารถเพิ่มความปลอดภัย ลดต้นทุนการบำรุงรักษา และยืดอายุการใช้งานของอุปกรณ์ได้ โดยในท้ายที่สุด การเลือกวัสดุอย่างรอบรู้จะนำไปสู่ประสิทธิภาพในการปฏิบัติงานที่สูงขึ้นและรับรองว่าระบบจะยังคงเชื่อถือได้ แม้ในสภาพแวดล้อมที่ท้าทายที่สุด