Zinc-Aluminum-Magnesium (ZAM) vs Hot-dip galvanizing (HDG)
Определение
What is Zinc-Aluminum-Magnesium (ZAM)?
Zinc-aluminum-magnesium (ZAM) is a high-performance metallic coating applied to steel designed to offer superior corrosion resistance, durability, and heat resistance compared to traditional galvanizing (zinc-only coatings). The coating combines zinc (Zn), aluminum (Al), and magnesium (Mg), which provides unique advantages in various applications.
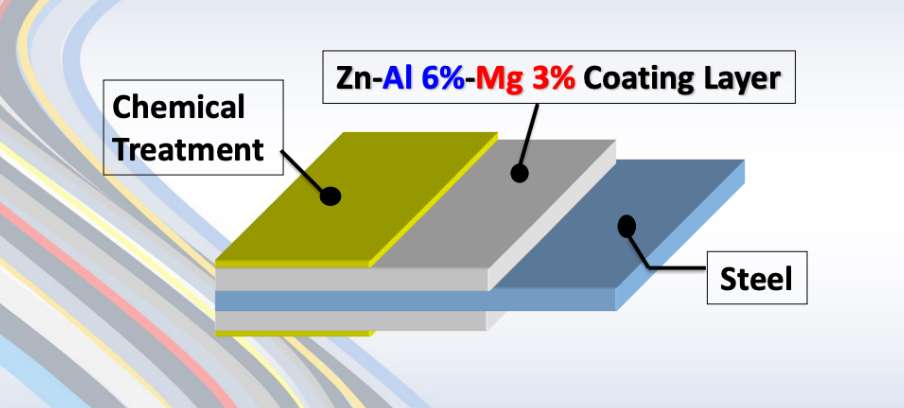
ZAM Coating
What is Hot-dip galvanizing? (HDG)?
Hot-dip galvanization is a form of galvanization. It is the process of coating iron and steel with zinc, which alloys with the base metal surface when immersing the metal in a bath of molten zinc at a temperature of around 450 °C (842 °F). When exposed to the atmosphere, the pure zinc (Zn) reacts with oxygen (O2) to form zinc oxide (ZnO), which further reacts with carbon dioxide (CO2) to form zinc carbonate (ZnCO3), a usually dull grey, fairly strong material that protects the steel underneath from further corrosion in many circumstances.
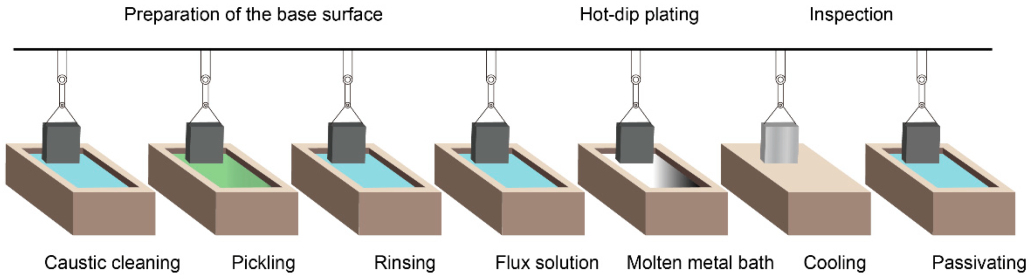
Hot-dip Galvanizing
Main Differences: Zinc-Aluminum-Magnesium (ZAM) vs Hot-dip galvanizing (HDG)
The comparison between zinc-aluminum-magnesium (ZAM) и hot-dip galvanizing (HDG) revolves around their coating composition, corrosion resistance, applications, cost, и environmental impact. Below is a detailed comparison to help understand their differences:
1. Coating Composition
Zinc-Aluminum-Magnesium (ZAM):
ZAM coatings are made of a combination of zinc (Zn), aluminum (Al), и magnesium (Mg). Typically, the composition is about 80-90% Zinc, 5-11% Aluminum, и 1-3% Magnesium. Including aluminum and magnesium gives the coating superior properties compared to zinc alone.
Hot-Dip Galvanizing (HDG):
HDG involves immersing steel into a molten bath of zinc (Zn) to form a protective zinc coating. The coating consists almost entirely of zinc, with small amounts of iron from the substrate, forming a zinc-iron alloy layer.
2. Коррозионная стойкость
Zinc-Aluminum-Magnesium (ZAM):
Superior corrosion resistance compared to hot-dip galvanized steel. Adding aluminum increases the coating’s resistance to high temperatures and oxidation, while magnesium improves its resistance to corrosion in harsh environments like coastal, industrial, and chemical settings. ZAM has self-healing properties—if the coating is damaged, the magnesium component reacts with moisture to help prevent further corrosion.
Hot-Dip Galvanizing (HDG):
It provides good corrosion resistance but not as high as ZAM, especially in aggressive environments. The zinc coating is sacrificial, meaning it corrodes first to protect the underlying steel, but its effectiveness can be limited in humid, salty, или chemical environments. HDG does not have the advanced self-healing properties that ZAM offers.
3. Durability and Longevity
Zinc-Aluminum-Magnesium (ZAM):
ZAM-coated products can last 2 to 4 times longer than traditional galvanized steel in harsh environments (e.g., coastal areas, chemical plants, etc.). The coating’s enhanced resistance to environmental factors contributes to a longer service life.
Hot-Dip Galvanizing (HDG):
The lifespan of HDG products is good but generally shorter than ZAM, particularly in extreme conditions. HDG can last for many years in less corrosive environments (e.g., mild climates), but its protection may degrade faster in severe environments.
4. Applications
Zinc-Aluminum-Magnesium (ZAM):
Ideal for суровые условия such as Coastal areas (where saltwater exposure is high), Chemical and industrial environments (where exposure to aggressive substances is every day), Solar panel mounts (due to its superior durability), Heavy-duty industrial applications (e.g., agricultural and mining equipment, steel structures exposed to extreme weather conditions).
Hot-Dip Galvanizing (HDG):
It is commonly used in general construction, automotive industries, outdoor infrastructure, и agricultural applications. It is suitable for general-purpose corrosion protection in outdoor conditions but not recommended for extreme or coastal environments.
5. Cost
Zinc-Aluminum-Magnesium (ZAM):
It is more expensive than traditional hot-dip galvanizing due to the inclusion of aluminum and magnesium and the more advanced coating process. The longer lifespan and lower maintenance costs in harsh environments often justify the higher initial cost.
Hot-Dip Galvanizing (HDG):
It is cheaper than ZAM, making it more suitable for projects where cost-efficiency is a priority and the environment is less aggressive. The relatively lower cost makes it ideal for large-scale production.
6. Environmental Impact
Zinc-Aluminum-Magnesium (ZAM):
The production of ZAM coatings is more environmentally friendly than hot-dip galvanizing, as it involves lower emissions of harmful gases and waste materials. The production process for ZAM generally generates less waste и fewer harmful emissions compared to traditional galvanizing methods.
Hot-Dip Galvanizing (HDG):
It is more environmentally intensive than ZAM, producing more waste gases and wastewater. However, modern improvements in the HDG process have aimed to reduce the environmental footprint, though it remains higher than ZAM.
7. Aesthetic Appearance
Zinc-Aluminum-Magnesium (ZAM):
ZAM has a matte gray finish with a smoother, more uniform appearance. This appearance can be more desirable in specific applications like architectural structures or solar panel mounts.
Hot-Dip Galvanizing (HDG):
HDG often has a shiny or dull metallic finish, depending on the thickness of the coating. While durable, its aesthetic appearance may be less appealing than ZAM’s, especially if the finish is uneven.
8. Ease of Processing and Welding
Zinc-Aluminum-Magnesium (ZAM):
ZAM coatings can be more challenging to process, weld, и paint than traditional galvanized steel, creating issues in some applications.
Hot-Dip Galvanizing (HDG):
HDG products are easier to weld and process than ZAM. However, the zinc coating can make welding and cutting more difficult due to zinc fumes, and special precautions may be required.
Summary Comparison Table: Zinc-Aluminum-Magnesium (ZAM) vs Hot-dip Galvanizing (HDG)
Особенность | Zinc-Aluminum-Magnesium (ZAM) | Hot-Dip Galvanizing (HDG) |
Coating Composition | Zinc, Aluminum, Magnesium | Zinc (with some iron from the substrate) |
Устойчивость к коррозии | Superior, especially in harsh environments | Good, but less effective in aggressive settings |
Durability and Longevity | 2-4 times longer than HDG in extreme environments | Moderate lifespan, shorter in harsh conditions |
Приложения | Coastal areas, chemical environments, heavy-duty | General outdoor infrastructure, agriculture |
Расходы | Higher initial cost | Lower initial cost |
Воздействие на окружающую среду | Lower emissions and waste | Higher emissions and waste |
Aesthetic Appearance | Matte gray, smoother finish | Shiny or dull metallic finish |
Ease of Processing | It can be more challenging, especially with welding | It is more straightforward to process and weld |
Заключение
ZAM is the best choice for extreme environments where superior corrosion resistance and durability are needed. Its long-term performance can justify the higher upfront cost.
HDG remains the go-to solution for general corrosion protection in less aggressive environments, providing a cost-effective and widely available option for most standard applications.