Introdução
Em indústrias como geração de energia, petróleo e gás, petroquímica e refinarias, tubos sem costura são componentes essenciais, especialmente em equipamentos que devem suportar temperaturas extremas, altas pressões e ambientes agressivos e corrosivos. Caldeiras, trocadores de calor, condensadores, superaquecedores, pré-aquecedores de ar e economizadores usam esses tubos. Cada uma dessas aplicações exige propriedades específicas do material para garantir desempenho, segurança e longevidade. A seleção de tubos sem costura para a caldeira e o trocador de calor depende da temperatura, pressão, resistência à corrosão e resistência mecânica específicas.
Este guia fornece uma visão aprofundada dos vários materiais usados para tubos sem costura, incluindo aço carbono, aço de liga, aço inoxidável, ligas de titânio, ligas à base de níquel, ligas de cobre e ligas de zircônio. Também exploraremos os padrões e graus relevantes, ajudando você a tomar decisões mais informadas para seus projetos de caldeira e trocador de calor.
Visão geral de CS, AS, SS, ligas de níquel, ligas de titânio e zircônio, cobre e ligas de cobre
1. Propriedades de resistência à corrosão
Cada material usado em tubos sem costura possui propriedades específicas de resistência à corrosão que determinam sua adequação a diferentes ambientes.
Aço carbono: Resistência limitada à corrosão, normalmente usada com revestimentos ou forros de proteção. Sujeito a enferrujar na presença de água e oxigênio, a menos que seja tratado.
Liga de aço: Resistência moderada à oxidação e corrosão. Adições de ligas como cromo e molibdênio melhoram a resistência à corrosão em altas temperaturas.
Aço inoxidável: Excelente resistência à corrosão geral, corrosão sob tensão e pitting devido ao seu conteúdo de cromo. Graus mais altos, como 316L, têm resistência melhorada à corrosão induzida por cloreto.
Ligas à base de níquel: Excelente resistência a ambientes agressivos como ambientes ácidos, alcalinos e ricos em cloreto. Aplicações altamente corrosivas usam ligas como Inconel 625, Hastelloy C276 e Alloy 825.
Titânio e Zircônio: Resistência superior a salmouras de água do mar e outros meios altamente corrosivos. O titânio é especialmente resistente a cloretos e ambientes ácidos, enquanto as ligas de zircônio se destacam em condições altamente ácidas.
Cobre e ligas de cobre: Excelente resistência à corrosão em água doce e salgada, com ligas de cobre-níquel apresentando resistência excepcional em ambientes marinhos.
2. Propriedades físicas e térmicas
Aço carbono:
Densidade: 7,85 g/cm³
Ponto de fusão: 1.425-1.500°C
Condutividade térmica: ~50 W/m·K
Liga de aço:
Densidade: Varia ligeiramente de acordo com os elementos de liga, normalmente em torno de 7,85 g/cm³
Ponto de fusão: 1.450-1.530°C
Condutividade térmica: Menor que o aço carbono devido aos elementos de liga.
Aço inoxidável:
Densidade: 7,75-8,0 g/cm³
Ponto de fusão: ~1.400-1.530°C
Condutividade térmica: ~16 W/m·K (menor que o aço carbono).
Ligas à base de níquel:
Densidade: 8,4-8,9 g/cm³ (depende da liga)
Ponto de fusão: 1.300-1.400°C
Condutividade térmica: Normalmente baixa, ~10-16 W/m·K.
Titânio:
Densidade: 4,51 g/cm³
Ponto de fusão: 1.668°C
Condutividade térmica: ~22 W/m·K (relativamente baixa).
Cobre:
Densidade: 8,94 g/cm³
Ponto de fusão: 1.084°C
Condutividade térmica: ~390 W/m·K (excelente condutividade térmica).
3. Composição química
Aço carbono: Principalmente ferro com 0,3%-1,2% de carbono e pequenas quantidades de manganês, silício e enxofre.
Liga de aço: Inclui elementos como cromo, molibdênio, vanádio e tungstênio para melhorar a resistência e a temperatura.
Aço inoxidável: Normalmente contém cromo 10,5%-30%, juntamente com níquel, molibdênio e outros elementos, dependendo do grau.
Ligas à base de níquel: Predominantemente níquel (40%-70%) com cromo, molibdênio e outros elementos de liga para aumentar a resistência à corrosão.
Titânio: Os graus 1 e 2 são titânio comercialmente puro, enquanto o grau 5 (Ti-6Al-4V) inclui alumínio 6% e vanádio 4%.
Ligas de cobre: As ligas de cobre contêm vários elementos como níquel (10%-30%) para resistência à corrosão (por exemplo, Cu-Ni 90/10).
4. Propriedades mecânicas
Aço carbono: Resistência à tração: 400-500 MPa, Resistência ao escoamento: 250-350 MPa, Alongamento: 15%-25%
Liga de aço: Resistência à tração: 500-900 MPa, Resistência ao escoamento: 300-700 MPa, Alongamento: 10%-25%
Aço inoxidável: Resistência à tração: 485-690 MPa (304/316), Resistência ao escoamento: 170-300 MPa, Alongamento: 35%-40%
Ligas à base de níquel: Resistência à tração: 550-1.000 MPa (Inconel 625), Resistência ao escoamento: 300-600 MPa, Alongamento: 25%-50%
Titânio: Resistência à tração: 240-900 MPa (varia de acordo com o grau), Resistência ao escoamento: 170-880 MPa, Alongamento: 15%-30%
Ligas de cobre: Resistência à tração: 200-500 MPa (depende da liga), Resistência ao escoamento: 100-300 MPa, Alongamento: 20%-35%
5. Tratamento térmico (condição de entrega)
Aço carbono e liga: Entregue em condição recozida ou normalizada. Os tratamentos térmicos incluem têmpera e revenimento para melhorar a resistência e a tenacidade.
Aço inoxidável: Entregue em condições recozidas para remover tensões internas e melhorar a ductilidade.
Ligas à base de níquel: Solubilização recozida para otimizar propriedades mecânicas e resistência à corrosão.
Titânio e Zircônio: Normalmente entregue em condições recozidas para maximizar a ductilidade e a tenacidade.
Ligas de cobre: Entregue em condições de recozimento suave, especialmente para aplicações de conformação.
6. Formando
Aço carbono e liga: Podem ser conformados a quente ou a frio, mas os aços de liga exigem mais esforço devido à sua maior resistência.
Aço inoxidável: A conformação a frio é comum, embora as taxas de endurecimento por trabalho sejam maiores do que as do aço carbono.
Ligas à base de níquel: Mais desafiador de moldar devido à alta resistência e às altas taxas de endurecimento por trabalho; geralmente requer trabalho a quente.
Titânio: A conformação é melhor realizada em temperaturas elevadas devido à sua alta resistência à temperatura ambiente.
Ligas de cobre: Fácil de moldar devido à boa ductilidade.
7. Soldagem
Aço carbono e liga: Geralmente é fácil soldar usando técnicas convencionais, mas pode ser necessário pré-aquecimento e tratamento térmico pós-soldagem (PWHT).
Aço inoxidável: Métodos comuns de soldagem incluem TIG, MIG e soldagem a arco. Controle cuidadoso da entrada de calor é necessário para evitar sensibilização.
Ligas à base de níquel: Difícil de soldar devido à alta expansão térmica e suscetibilidade a rachaduras.
Titânio: Soldado em um ambiente blindado (gás inerte) para evitar contaminação. Precauções são necessárias devido à reatividade do titânio em altas temperaturas.
Ligas de cobre: Fácil de soldar, especialmente ligas de cobre-níquel, mas pode ser necessário pré-aquecimento para evitar rachaduras.
8. Corrosão de Soldas
Aço inoxidável: Pode sofrer corrosão localizada (por exemplo, corrosão por pites, corrosão por frestas) na zona afetada pelo calor da solda se não for controlada adequadamente.
Ligas à base de níquel: Suscetível a corrosão sob tensão se exposto a cloretos em altas temperaturas.
Titânio: As soldas devem ser devidamente protegidas do oxigênio para evitar fragilização.
9. Descalcificação, decapagem e limpeza
Aço carbono e liga: A decapagem remove óxidos de superfície após tratamento térmico. Ácidos comuns incluem ácido clorídrico e ácido sulfúrico.
Aço inoxidável e ligas de níquel: A decapagem com ácido nítrico/fluorídrico é usada para remover manchas causadas pelo calor e restaurar a resistência à corrosão após a soldagem.
Titânio: Soluções de decapagem ácida suave são usadas para limpar a superfície e remover óxidos sem danificar o metal.
Ligas de cobre: A limpeza ácida é usada para remover manchas e óxidos superficiais.
10. Processo de superfície (AP, BA, MP, EP, etc.)
AP (recozido e decapado): Acabamento padrão para a maioria das ligas de aço inoxidável e níquel após recozimento e decapagem.
BA (recozido brilhante): Obtido por recozimento em atmosfera controlada para produzir uma superfície lisa e reflexiva.
MP (Polido Mecanicamente): O polimento mecânico melhora a lisura da superfície, reduzindo o risco de contaminação e início de corrosão.
EP (Eletropolido): Um processo eletroquímico que remove o material da superfície para criar um acabamento ultra-liso, reduzindo a rugosidade da superfície e melhorando a resistência à corrosão.
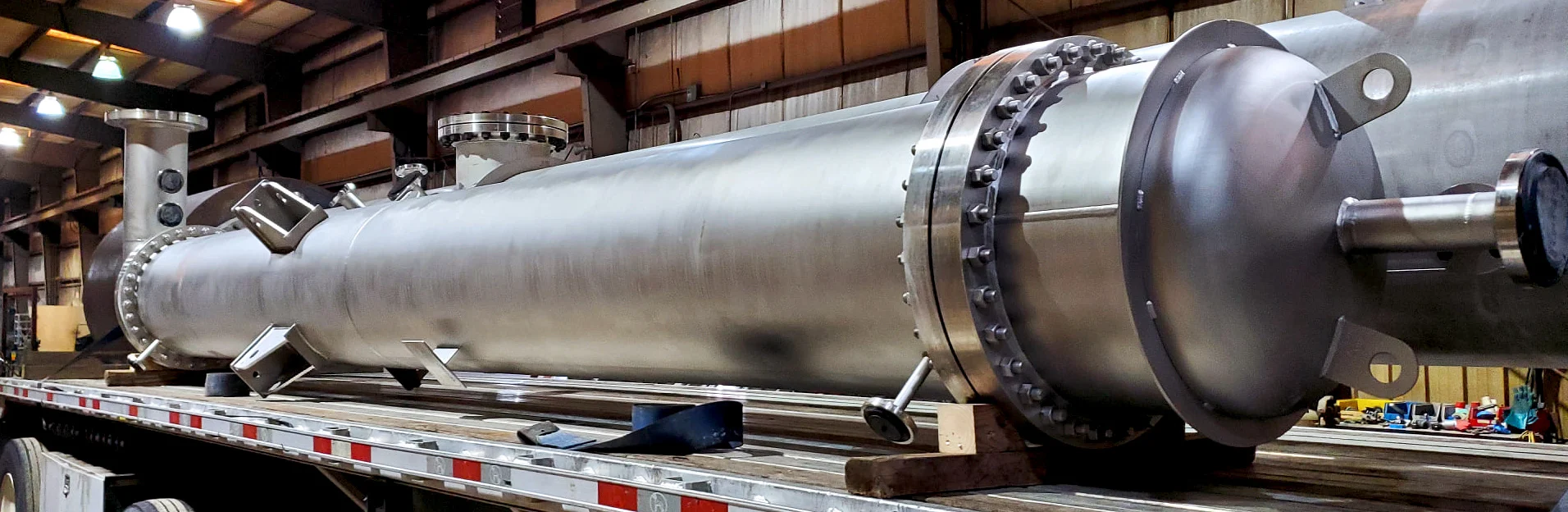
Trocador de calor inoxidável
I. Compreendendo tubos sem costura
Tubos sem costura diferem de tubos soldados porque não têm uma costura soldada, o que pode ser um ponto fraco em algumas aplicações de alta pressão. Tubos sem costura são inicialmente formados a partir de um tarugo sólido, que é então aquecido e, subsequentemente, é extrudado ou desenhado sobre um mandril para criar o formato do tubo. A ausência de costuras lhes dá resistência e confiabilidade superiores, tornando-os ideais para ambientes de alta pressão e alta temperatura.
Aplicações comuns:
Caldeiras: Tubos sem costura são essenciais na construção de caldeiras aquatubulares e flamotubulares, onde altas temperaturas e pressões estão presentes.
Trocadores de calor: Usados para transferir calor entre dois fluidos, tubos sem costura em trocadores de calor devem resistir à corrosão e manter a eficiência térmica.
Condensadores: Tubos sem costura ajudam a condensar vapor em água em sistemas de geração de energia e refrigeração.
Superaquecedores: Tubos sem costura são usados para superaquecer vapor em caldeiras, aumentando a eficiência de turbinas em usinas de energia.
Pré-aquecedores de ar: Esses tubos transferem calor dos gases de combustão para o ar, melhorando a eficiência da caldeira.
Economizadores: Tubos sem costura em economizadores pré-aquecem a água de alimentação usando o calor residual da exaustão da caldeira, aumentando a eficiência térmica.
Caldeiras, trocadores de calor, condensadores, superaquecedores, pré-aquecedores de ar e economizadores são componentes integrais em várias indústrias, particularmente aquelas envolvidas em transferência de calor, produção de energia e gerenciamento de fluidos. Especificamente, esses componentes encontram uso primário nas seguintes indústrias:
1. Indústria de geração de energia
Caldeiras: Usadas em usinas de energia para converter energia química em energia térmica, geralmente para geração de vapor.
Superaquecedores, economizadores e pré-aquecedores de ar: esses componentes melhoram a eficiência pré-aquecendo o ar de combustão, recuperando o calor dos gases de exaustão e aquecendo ainda mais o vapor.
Trocadores de calor e condensadores: usados para resfriamento e recuperação de calor em usinas termelétricas, particularmente em turbinas a vapor e ciclos de resfriamento.
2. Indústria de petróleo e gás
Trocadores de calor: cruciais em processos de refino, onde o calor é transferido entre fluidos, como na destilação de petróleo bruto ou em plataformas offshore para processamento de gás.
Caldeiras e economizadores: encontrados em refinarias e plantas petroquímicas para geração de vapor e recuperação de energia.
Condensadores: Usados para condensar gases em líquidos durante os processos de destilação.
3. Indústria Química
Trocadores de calor: amplamente utilizados para aquecer ou resfriar reações químicas e para recuperar calor de reações exotérmicas.
Caldeiras e superaquecedores: usados para produzir o vapor necessário para vários processos químicos e para fornecer energia para etapas de destilação e reação.
Pré-aquecedores de ar e economizadores: melhoram a eficiência em processos químicos que consomem muita energia recuperando o calor dos gases de escape e reduzindo o consumo de combustível.
4. Indústria Marítima
Caldeiras e trocadores de calor: essenciais em embarcações marítimas para sistemas de geração de vapor, aquecimento e resfriamento. Trocadores de calor marítimos são frequentemente usados para resfriar os motores do navio e gerar energia.
Condensadores: Usados para converter o vapor de exaustão de volta em água para reutilização nos sistemas de caldeiras do navio.
5. Indústria de alimentos e bebidas
Trocadores de calor: comumente usados para processos de pasteurização, esterilização e evaporação.
Caldeiras e economizadores: usados para produzir vapor para operações de processamento de alimentos e para recuperar calor do escapamento para economizar no consumo de combustível.
6. HVAC (Aquecimento, Ventilação e Ar Condicionado)
Trocadores de calor e pré-aquecedores de ar: usados em sistemas HVAC para transferência eficiente de calor entre fluidos ou gases, fornecendo aquecimento ou resfriamento para edifícios e instalações industriais.
Condensadores: Usados em sistemas de ar condicionado para rejeitar o calor do refrigerante.
7. Indústria de Celulose e Papel
Caldeiras, trocadores de calor e economizadores: fornecem recuperação de vapor e calor em processos como polpação, secagem de papel e recuperação química.
Superaquecedores e pré-aquecedores de ar: aumentam a eficiência energética nas caldeiras de recuperação e o equilíbrio térmico geral das fábricas de papel.
8. Indústria Metalúrgica e Siderúrgica
Trocadores de calor: Usados para resfriar gases e líquidos quentes na produção de aço e processos metalúrgicos.
Caldeiras e economizadores: fornecem calor para vários processos, como operação de alto-forno, tratamento térmico e laminação.
9. Indústria Farmacêutica
Trocadores de calor: usados para controlar a temperatura durante a produção de medicamentos, processos de fermentação e ambientes estéreis.
Caldeiras: Geram o vapor necessário para esterilização e aquecimento de equipamentos farmacêuticos.
10. Usinas de conversão de resíduos em energia
Caldeiras, condensadores e economizadores: usados para converter resíduos em energia por meio da combustão, ao mesmo tempo em que recuperam calor para melhorar a eficiência.
Agora, vamos nos aprofundar nos materiais que tornam os tubos sem costura adequados para essas aplicações exigentes.
II. Tubos de Aço Carbono para Caldeira e Trocador de Calor
O aço carbono é um dos materiais mais amplamente utilizados para tubos sem costura em aplicações industriais, principalmente devido à sua excelente resistência, bem como à sua acessibilidade e ampla disponibilidade. Os tubos de aço carbono oferecem resistência moderada à temperatura e à pressão, tornando-os adequados para uma ampla gama de aplicações.
Propriedades do aço carbono:
Alta resistência: tubos de aço carbono podem suportar pressão e estresse significativos, tornando-os ideais para uso em caldeiras e trocadores de calor.
Custo-benefício: Comparado a outros materiais, o aço carbono é relativamente barato, o que o torna uma escolha popular em aplicações industriais de larga escala.
Resistência moderada à corrosão: embora o aço carbono não seja tão resistente à corrosão quanto o aço inoxidável, ele pode ser tratado com revestimentos ou forros para aumentar sua longevidade em ambientes corrosivos.
Principais Padrões e Notas:
ASTM A179: Este padrão abrange tubos de aço de baixo carbono trefilados a frio sem costura usados para aplicações de trocadores de calor e condensadores. Esses tubos têm excelentes propriedades de transferência de calor e são comumente usados em aplicações de baixa a moderada temperatura e pressão.
ASTM A192: Tubos de caldeira de aço carbono sem costura projetados para serviço de alta pressão. Esses tubos são usados em geração de vapor e outros ambientes de alta pressão.
ASTM A210: Este padrão abrange tubos de aço de médio carbono sem costura para aplicações de caldeira e superaquecedor. Os graus A-1 e C oferecem níveis variados de resistência e resistência à temperatura.
ASTM A334 (Graus 1, 3, 6): Tubos de aço carbono sem costura e soldados projetados para serviço de baixa temperatura. Esses graus são usados em trocadores de calor, condensadores e outras aplicações de baixa temperatura.
EN 10216-2 (P235GH, P265GH TC1/TC2): Norma europeia para tubos de aço sem costura usados em aplicações de pressão, particularmente em caldeiras e serviços de alta temperatura.
Tubos de aço carbono são uma excelente escolha para aplicações de caldeiras e trocadores de calor onde alta resistência e resistência moderada à corrosão são necessárias. No entanto, para aplicações que envolvem não apenas temperaturas extremamente altas, mas também ambientes corrosivos severos, tubos de liga ou aço inoxidável são frequentemente preferidos devido à sua resistência e durabilidade superiores.
III. Tubos de Aço Ligado para Caldeira e Trocador de Calor
Tubos de aço de liga são projetados para aplicações de caldeiras e trocadores de calor de alta temperatura e alta pressão. Esses tubos são ligados com elementos como cromo, molibdênio e vanádio para aumentar sua força, dureza e resistência à corrosão e ao calor. Tubos de aço de liga são amplamente usados em aplicações críticas, como superaquecedores, economizadores e trocadores de calor de alta temperatura, devido à sua força e resistência excepcionais ao calor e à pressão.
Propriedades do aço de liga:
Alta resistência ao calor: elementos de liga como cromo e molibdênio melhoram o desempenho em altas temperaturas desses tubos, tornando-os adequados para aplicações com temperaturas extremas.
Resistência à corrosão aprimorada: tubos de aço-liga oferecem melhor resistência à oxidação e corrosão em comparação ao aço carbono, especialmente em ambientes de alta temperatura.
Resistência aprimorada: elementos de liga também aumentam a resistência desses tubos, permitindo que eles suportem alta pressão em caldeiras e outros equipamentos essenciais.
Principais Padrões e Notas:
ASTM A213 (Graus T5, T9, T11, T22, T91, T92): Este padrão abrange tubos de liga de aço ferrítico e austenítico sem costura para uso em caldeiras, superaquecedores e trocadores de calor. Os graus diferem em sua composição de liga e são selecionados com base nos requisitos específicos de temperatura e pressão.
T5 e T9: Adequados para serviços em temperaturas moderadas a altas.
T11 e T22: comumente usados em aplicações de alta temperatura, oferecendo maior resistência ao calor.
T91 e T92: Ligas avançadas de alta resistência projetadas para serviços em temperaturas ultra-altas em usinas de energia.
EN 10216-2 (16Mo3, 13CrMo4-5, 10CrMo9-10, 15NiCuMoNb5-6-4, X20CrMoV11-1): Padrões europeus para tubos de aço de liga sem costura usados em aplicações de alta temperatura. Esses tubos são comumente usados em caldeiras, superaquecedores e economizadores em usinas de energia.
16Mo3: Um aço de liga com boas propriedades de alta temperatura, adequado para uso em caldeiras e vasos de pressão.
13CrMo4-5 e 10CrMo9-10: Ligas de cromo-molibdênio que oferecem excelente resistência ao calor e à corrosão para aplicações de alta temperatura.
Tubos de aço-liga são a opção ideal para ambientes de alta temperatura e alta pressão, onde o aço carbono pode não fornecer desempenho suficiente para a caldeira e o trocador de calor.
IV. Tubos de Aço Inoxidável para Caldeira e Trocador de Calor
Tubos de aço inoxidável oferecem resistência excepcional à corrosão, tornando-os ideais para aplicações de caldeiras e trocadores de calor envolvendo fluidos corrosivos, altas temperaturas e ambientes severos. Eles são amplamente usados em trocadores de calor, superaquecedores e caldeiras, onde, além da resistência à corrosão, a resistência a altas temperaturas também é necessária para um desempenho ideal.
Propriedades do aço inoxidável:
Resistência à corrosão: a resistência do aço inoxidável à corrosão vem do seu teor de cromo, que forma uma camada protetora de óxido na superfície.
Alta resistência em temperaturas elevadas: o aço inoxidável mantém suas propriedades mecânicas mesmo em altas temperaturas, tornando-o adequado para superaquecedores e outras aplicações que exigem muito calor.
Durabilidade a longo prazo: a resistência do aço inoxidável à corrosão e à oxidação garante uma longa vida útil, mesmo em ambientes adversos.
Principais Padrões e Notas:
ASTM A213 / ASTM A249: Esses padrões abrangem tubos de aço inoxidável sem costura e soldados para uso em caldeiras, superaquecedores e trocadores de calor. Os graus comuns incluem:
TP304 / TP304L (EN 1.4301 / 1.4307): Os aços inoxidáveis austeníticos são amplamente utilizados por sua resistência à corrosão e resistência.
TP310S / TP310MoLN (EN 1.4845 / 1.4466): Graus de aço inoxidável para altas temperaturas com excelente resistência à oxidação.
TP316 / TP316L (EN 1.4401 / 1.4404): Graus contendo molibdênio com maior resistência à corrosão, especialmente em ambientes com cloreto.
TP321 (EN 1.4541): Classe de aço inoxidável estabilizado usado em ambientes de alta temperatura para evitar corrosão intergranular.
TP347H / TP347HFG (EN 1.4550 / 1.4961): Graus estabilizados com alto teor de carbono para aplicações de alta temperatura, como superaquecedores e caldeiras.
UNS N08904 (904L) (EN 1.4539): Aço inoxidável superaustenítico com excelente resistência à corrosão, especialmente em ambientes ácidos.
ASTM A269: Abrange tubos de aço inoxidável austenítico sem costura e soldados para serviços gerais resistentes à corrosão.
Norma ASTM A789: Padrão para tubos de aço inoxidável duplex, oferecendo uma combinação de excelente resistência à corrosão e alta resistência.
UNS S31803, S32205, S32750, S32760: Graus de aço inoxidável duplex e super duplex, oferecendo resistência superior à corrosão, especialmente em ambientes contendo cloreto.
EN 10216-5: Norma europeia que abrange tubos de aço inoxidável sem costura, incluindo os seguintes graus:
1.4301 / 1.4307 (TP304 / TP304L)
1.4401 / 1.4404 (TP316 / TP316L)
1.4845 (TP310S)
1,4466 (TP310MoLN)
1.4539 (UNS N08904 / 904L)
Tubos de aço inoxidável são altamente versáteis e são usados em uma ampla gama de aplicações, incluindo trocadores de calor, caldeiras e superaquecedores, onde tanto a resistência à corrosão quanto a resistência a altas temperaturas não são apenas necessárias, mas também essenciais para um desempenho ideal.
V. Ligas à base de níquel para caldeiras e trocadores de calor
Ligas à base de níquel estão entre os materiais mais resistentes à corrosão disponíveis e são comumente usadas em aplicações de caldeiras e trocadores de calor envolvendo temperaturas extremas, ambientes corrosivos e condições de alta pressão. Ligas de níquel fornecem excelente resistência à oxidação, sulfetação e carburação, tornando-as ideais para trocadores de calor, caldeiras e superaquecedores em ambientes severos.
Propriedades das ligas à base de níquel:
Resistência excepcional à corrosão: ligas de níquel resistem à corrosão em ambientes ácidos, alcalinos e clorados.
Estabilidade em altas temperaturas: as ligas de níquel mantêm sua resistência e resistência à corrosão mesmo em temperaturas elevadas, tornando-as adequadas para aplicações em altas temperaturas.
Resistência à oxidação e sulfetação: As ligas de níquel são resistentes à oxidação e sulfetação, que podem ocorrer em ambientes de alta temperatura envolvendo compostos contendo enxofre.
Principais Padrões e Notas:
ASTM B163 / ASTM B407 / ASTM B444: Esses padrões abrangem ligas à base de níquel para tubos sem costura usados em caldeiras, trocadores de calor e superaquecedores. Os graus comuns incluem:
Inconel 600 / 601: Excelente resistência à oxidação e corrosão em alta temperatura, tornando essas ligas ideais para superaquecedores e trocadores de calor de alta temperatura.
Inconel 625: Oferece resistência superior a uma ampla gama de ambientes corrosivos, incluindo ambientes ácidos e ricos em cloreto.
Incoloy 800 / 800H / 800HT: Utilizados em aplicações de alta temperatura devido à sua excelente resistência à oxidação e à cementação.
Hastelloy C276 / C22: Essas ligas de níquel-molibdênio-cromo são conhecidas por sua excelente resistência à corrosão em ambientes altamente corrosivos, incluindo meios ácidos e contendo cloreto.
ASTM B423: Abrange tubos sem costura feitos de ligas de níquel-ferro-cromo-molibdênio, como a Liga 825, que oferece excelente resistência à corrosão sob tensão e corrosão geral em vários ambientes.
EN 10216-5: Norma europeia para ligas à base de níquel usadas em tubos sem costura para aplicações corrosivas e de alta temperatura, incluindo graus como:
2.4816 (Inconel 600)
2.4851 (Inconel 601)
2.4856 (Inconel 625)
2.4858 (Liga 825)
Ligas à base de níquel são frequentemente escolhidas para aplicações críticas onde a resistência à corrosão e o desempenho em altas temperaturas são essenciais, como em usinas de energia, processamento químico e refinarias de petróleo e gás. Caldeiras e trocadores de calor.
VI. Ligas de titânio e zircônio para caldeiras e trocadores de calor
As ligas de titânio e zircônio oferecem uma combinação única de resistência, resistência à corrosão e propriedades leves, tornando-as ideais para aplicações específicas em trocadores de calor, condensadores e caldeiras.
Propriedades das ligas de titânio:
Alta relação resistência-peso: o titânio é tão forte quanto o aço, mas significativamente mais leve, o que o torna adequado para aplicações sensíveis ao peso.
Excelente resistência à corrosão: as ligas de titânio são altamente resistentes à corrosão em água do mar, ambientes ácidos e meios contendo cloreto.
Boa resistência ao calor: as ligas de titânio mantêm suas propriedades mecânicas em temperaturas elevadas, tornando-as adequadas para tubos de trocadores de calor em usinas de energia e processamento químico.
Propriedades das ligas de zircônio:
Excelente resistência à corrosão: as ligas de zircônio são altamente resistentes à corrosão em ambientes ácidos, incluindo ácido sulfúrico, ácido nítrico e ácido clorídrico.
Estabilidade em altas temperaturas: as ligas de zircônio mantêm sua resistência e resistência à corrosão em temperaturas elevadas, tornando-as ideais para aplicações de trocadores de calor de alta temperatura.
Principais Padrões e Notas:
ASTM B338: Este padrão abrange tubos de liga de titânio sem costura e soldados para uso em trocadores de calor e condensadores. Graus comuns incluem:
Grau 1 / Grau 2: Graus de titânio comercialmente puro com excelente resistência à corrosão.
Grau 5 (Ti-6Al-4V): Uma liga de titânio com resistência aprimorada e desempenho em altas temperaturas.
ASTM B523: Abrange tubos de liga de zircônio sem costura e soldados para uso em trocadores de calor e condensadores. Graus comuns incluem:
Zircônio 702: Uma liga de zircônio comercialmente pura com excelente resistência à corrosão.
Zircônio 705: Um grau de zircônio ligado com propriedades mecânicas aprimoradas e estabilidade em altas temperaturas.
Ligas de titânio e zircônio são comumente usadas em ambientes altamente corrosivos, como usinas de dessalinização de água do mar, indústrias de processamento químico e caldeiras e trocadores de calor de usinas nucleares, devido à sua resistência superior à corrosão e propriedades leves.
VII. Cobre e Ligas de Cobre para Caldeira e Trocador de Calor
O cobre e suas ligas, incluindo latão, bronze e cobre-níquel, são amplamente utilizados em trocadores de calor, condensadores e caldeiras devido à sua excelente condutividade térmica e resistência à corrosão.
Propriedades das ligas de cobre:
Excelente condutividade térmica: as ligas de cobre são conhecidas por sua alta condutividade térmica, o que as torna ideais para trocadores de calor e condensadores.
Resistência à corrosão: ligas de cobre resistem à corrosão na água, incluindo água do mar, tornando-as adequadas para aplicações marítimas e de dessalinização.
Propriedades antimicrobianas: as ligas de cobre têm propriedades antimicrobianas naturais, tornando-as adequadas para aplicações em saúde e tratamento de água.
Principais Padrões e Notas:
ASTM B111: Este padrão abrange tubos de cobre sem costura e de liga de cobre para uso em trocadores de calor, condensadores e evaporadores. Os graus comuns incluem:
C44300 (Latão Admiralty): Uma liga de cobre e zinco com boa resistência à corrosão, especialmente em aplicações em água do mar.
C70600 (Cobre-Níquel 90/10): Uma liga de cobre-níquel com excelente resistência à corrosão em água do mar e ambientes marinhos.
C71500 (Cobre-Níquel 70/30): Outra liga de cobre-níquel com maior teor de níquel para maior resistência à corrosão.
Cobre e ligas de cobre são amplamente utilizados em aplicações de caldeiras e trocadores de calor marítimos, usinas de energia e sistemas HVAC devido à sua excelente condutividade térmica e resistência à corrosão da água do mar.
Além da caldeira e do trocador de calor, condensadores, superaquecedores, pré-aquecedores de ar e economizadores também são componentes vitais que otimizam significativamente a eficiência energética. Por exemplo, o condensador resfria os gases de exaustão da caldeira e do trocador de calor, enquanto o superaquecedor, por outro lado, aumenta a temperatura do vapor para melhor desempenho. Enquanto isso, o pré-aquecedor de ar utiliza gases de exaustão para aquecer o ar de entrada, aumentando ainda mais a eficiência geral do sistema da caldeira e do trocador de calor. Por fim, os economizadores desempenham um papel crucial ao recuperar o calor residual dos gases de combustão para pré-aquecer a água, o que, em última análise, reduz o consumo de energia e aumenta a eficiência da caldeira e do trocador de calor.
VIII. Conclusão: Escolhendo os materiais certos para a caldeira e o trocador de calor
Tubos sem costura são integrais ao desempenho de caldeiras, trocadores de calor, condensadores, superaquecedores, pré-aquecedores de ar e economizadores em indústrias como geração de energia, petróleo e gás e processamento químico. A escolha do material para tubos sem costura depende dos requisitos específicos da aplicação, incluindo temperatura, pressão, resistência à corrosão e resistência mecânica.
Aço carbono oferece preço acessível e resistência para aplicações de temperatura e pressão moderadas.
Liga de aço proporciona desempenho e resistência superiores em altas temperaturas em caldeiras e superaquecedores.
Aço inoxidável oferece excelente resistência à corrosão e durabilidade em trocadores de calor e superaquecedores.
Ligas à base de níquel são a melhor escolha para ambientes extremamente corrosivos e de alta temperatura.
Ligas de titânio e zircônio são ideais para aplicações leves e altamente corrosivas.
Cobre e ligas de cobre são preferidos por sua condutividade térmica e resistência à corrosão em trocadores de calor e condensadores.
Os sistemas de caldeira e trocador de calor desempenham um papel crucial em várias indústrias ao transferir calor de um meio para outro de forma eficiente. Uma caldeira e um trocador de calor trabalham juntos para gerar e transferir calor, fornecendo calor essencial para a produção de vapor em usinas de energia e processos de fabricação.
Ao entender as propriedades e aplicações desses materiais, engenheiros e designers podem tomar decisões informadas, garantindo a operação segura e eficiente de seus equipamentos. Ao selecionar materiais para a caldeira e o trocador de calor, é crucial considerar os requisitos específicos de sua aplicação. Além disso, você deve consultar os padrões relevantes para garantir compatibilidade e desempenho ideal.