Microstructuurontwikkeling van P92-staal bij verschillende isotherme temperaturen
P92 staal wordt voornamelijk gebruikt in ultra-superkritische boilers, ultra-hogedruk pijpleidingen en andere hogetemperatuur- en hogedrukapparatuur. P92-staal is in de chemische samenstelling van P91-staal gebaseerd op de toevoeging van sporenelementen van W- en B-elementen, vermindert het gehalte aan Mo, door de korrelgrenzen van de versterkte en dispersie versterkte op verschillende manieren, om de algehele prestatie van het P92-staal te verbeteren, P92-staal dan het P91-staal heeft een betere weerstand tegen oxidatieprestaties en corrosiebestendigheid. Een warmbewerkingsproces is essentieel voor het produceren van de P92-stalen pijp. Thermische verwerkingstechnologie kan de interne defecten die tijdens het productieproces worden gegenereerd, elimineren en de staalprestaties laten voldoen aan de behoeften van de werkomstandigheden. Het type en de staat van de organisatie in het warmbewerkingsproces zijn de belangrijkste factoren die de prestaties beïnvloeden om aan de norm te voldoen. In dit artikel wordt de organisatie van P92-stalen buizen bij verschillende isotherme temperaturen geanalyseerd om de organisatie-evolutie van P92-stalen buizen bij verschillende temperaturen te onthullen. Dit biedt niet alleen informatieve ondersteuning voor de organisatieanalyse en prestatiecontrole van het daadwerkelijke warmbewerkingsproces, maar legt ook de experimentele basis voor de ontwikkeling van het warmbewerkingsproces.
1. Testmaterialen en -methoden
1.1 Testmateriaal
Het geteste staal is een P92-stalen buis in gebruiksomstandigheden (1060 ℃ gehard + 760 ℃ getemperd) en de chemische samenstelling ervan wordt weergegeven in Tabel 1. Een cilindrisch monster van ϕ4 mm × 10 mm werd in het middengedeelte van de voltooide buis op een bepaalde positie langs de lengterichting gesneden en de blusexpansiemeter werd gebruikt om de weefseltransformatie bij verschillende temperaturen te bestuderen.
Tabel 1 Belangrijkste chemische samenstelling van P92-staal op basis van massafractie (%)
Element |
C |
Si |
Mn |
Cr |
Ni |
ma |
V |
Al |
B |
Nb |
W |
Fe |
% |
0.13 |
0.2 |
0.42 |
8.67 |
0.25 |
0.48 |
0.19 |
0.008 |
0.002 |
0.05 |
1.51 |
Evenwicht |
1.2 Testproces
Met behulp van L78 blusthermische expansiemeter, 0,05 ℃ / s opwarmen tot 1050 ℃ isolatie 15 min, 200 ℃ / s afkoelen tot kamertemperatuur. Meet het kritische punt van faseverandering van het materiaal Ac1 is 792,4 ℃, Ac3 is 879,8 ℃, Ms is 372,3 ℃. De monsters werden verwarmd tot 1050 °C met een snelheid van 10 °C/s en 15 minuten op die temperatuur gehouden, en vervolgens afgekoeld tot verschillende temperaturen (770, 740, 710, 680, 650, 620, 520, 430, 400, 370, 340, 310, 280, 250, 190 en 160 °C) met een snelheid van 150 °C/s en gedurende verschillende tijdsperioden op die temperatuur gehouden (620 °C en lager gedurende 1 uur, 620 °C en hoger gedurende 25 uur). 620 ℃ en hoger gedurende 25 uur), het isotherme uiteinde van de stroom is uitgeschakeld, zodat het monster luchtgekoeld wordt tot kamertemperatuur.1.3 Testmethoden
Na het slijpen en polijsten van het oppervlak van de specimens onder verschillende processen, werd het oppervlak van de specimens gecorrodeerd met behulp van koningswater. AXIOVERT 25 Zeiss-microscoop en QWANTA 450 milieuscanning-elektronenmicroscoop werden gebruikt om de organisatie te observeren en analyseren; met behulp van HVS-50 Vickers-hardheidsmeter (laadgewicht van 1 kg) werden hardheidsmetingen uitgevoerd op verschillende locaties op het oppervlak van elk specimen en de gemiddelde waarde werd genomen als de hardheidswaarde van het specimen.
2. Testresultaten en analyse
2.1 Organisatie en analyse van verschillende isotherme temperaturen
Figuur 1 toont de microstructuur van P92-staal na volledige austenitisatie bij 1050°C gedurende verschillende tijden bij verschillende temperaturen. Figuur 1(a) toont de microstructuur van P92-staal na isothermalisatie bij 190℃ gedurende 1 uur. Uit figuur 1(a2) blijkt dat de kamertemperatuurorganisatie martensiet (M) is. Uit figuur 1(a3) blijkt dat de martensiet lat-achtige kenmerken vertoont. Omdat het Ms-punt van het staal ongeveer 372°C is, vindt de martensietfasetransformatie plaats bij isotherme temperaturen onder het Ms-punt, waarbij martensiet wordt gevormd, en het koolstofgehalte van het P92-staal behoort tot het bereik van koolstofarme samenstellingen; een lat-achtige morfologie kenmerkt de martensiet.
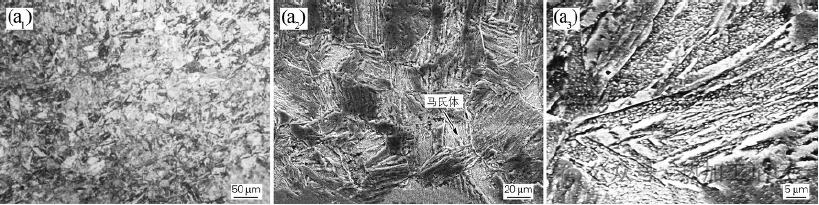
Figuur 1(a) toont de microstructuur van P92-staal na 1 uur isotherme verwerking bij 190°C
Figuur 1(b) voor de microstructuur van P92-staal bij 430 ℃ isotherm 1u. Naarmate de isotherme temperatuur stijgt tot 430°C, bereikt P92-staal de bainiettransformatiezone. Omdat het staal Mo-, B- en W-elementen bevat, hebben deze elementen weinig effect op de bainiettransformatie, terwijl ze de perlitische transformatie vertragen. Daarom is P92-staal bij 430 ℃ isolatie 1u, de organisatie van een bepaalde hoeveelheid bainiet. Vervolgens wordt het resterende onderkoelde austeniet omgezet in martensiet wanneer het met lucht wordt gekoeld.
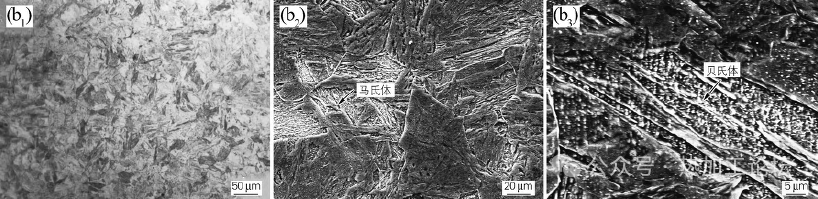
Figuur 1(b) voor de microstructuur van P92-staal bij 430 ℃ isotherm 1u
Figuur 1(c) toont de microstructuur van P92-staal bij 520 ℃ isotherm 1 uur. Wanneer de isotherme temperatuur van 520 ℃, de legeringselementen Cr, Mo, Mn, enz., zodat de perliettransformatie wordt geremd, wordt het begin van het bainiettransformatiepunt (Bs-punt) verlaagd, zodat in een specifiek temperatuurbereik in de stabilisatiezone van de onderkoelde austeniet zal verschijnen. Figuur 1(c) is te zien in 520 ℃ isolatie 1 uur nadat onderkoelde austeniet niet optrad na de transformatie, gevolgd door luchtkoeling om martensiet te vormen; de uiteindelijke kamertemperatuurorganisatie is de martensiet.
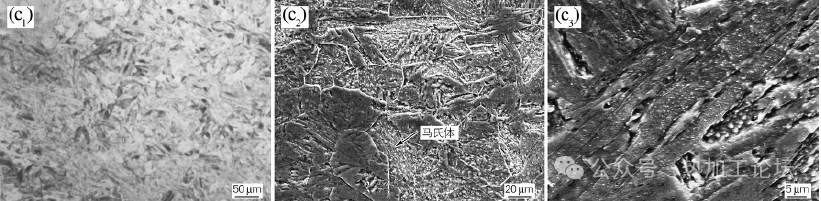
Figuur 1(c) toont de microstructuur van P92-staal bij 520 ℃ isotherme 1u
Figuur 1 (d) voor het P92-staal bij 650 ℃ isotherme 25h-microstructuur voor martensiet + perliet. Zoals weergegeven in Figuur 1 (d3), vertoont perliet discontinue lamellaire kenmerken en vertoont het carbide op het oppervlak een korte staafprecipitatie. Dit komt doordat de P92-staallegeringselementen Cr, Mo, V, enz. de stabiliteit van onderkoelde austeniet verbeteren, zodat de P92-staalperlietmorfologie verandert, dat wil zeggen het carbide in het perlitische lichaam van het carbide voor de korte staaf, dit perlitische lichaam staat bekend als de klasse perliet. Tegelijkertijd werden veel fijne tweede-fasedeeltjes in de organisatie gevonden.
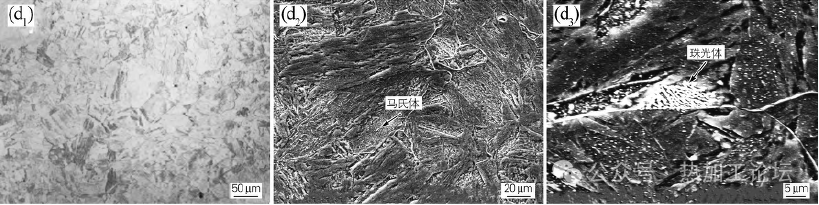
Figuur 1 (d) voor het P92-staal bij 650 ℃ isotherme 25h-microstructuur voor martensiet + perliet
Figuur 1(e) toont de microstructuur van P92-staal bij 740 ℃ isotherme 25 uur. Bij 740°C isotherme zal er eerst eutectische massieve ferrietprecipitatie zijn en vervolgens austeniet-eutectische ontleding, wat resulteert in een perlietachtige organisatie. Vergeleken met de 650°C isotherme (zie figuur 1(d3)) wordt de perlitische organisatie grover naarmate de isotherme temperatuur wordt verhoogd, en het tweefasenkarakter van perliet, d.w.z. ferriet en carburiet in de vorm van een korte staaf, is duidelijk zichtbaar.
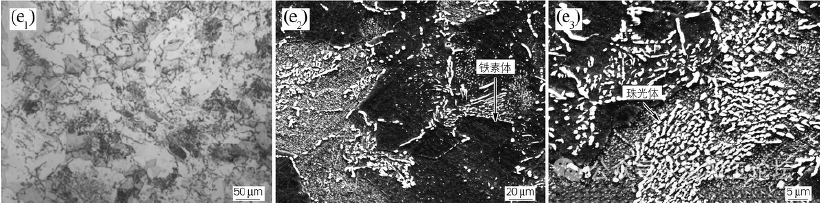
Figuur 1(e) toont de microstructuur van P92-staal bij 740 ℃ isotherme 25h
Figuur 1(f) toont de microstructuur van P92-staal bij een isotherme temperatuur van 770°C gedurende 25 uur. Bij 770°C isotherm vindt, met de verlenging van de isotherme tijd, eerst de neerslag van ferriet plaats, en vervolgens ondergaat het onderkoelde austeniet eutectische ontleding om een ferriet + perlietorganisatie te vormen. Met de toename van de isotherme temperatuur neemt het eerste eutectische ferrietgehalte toe en neemt het perlietgehalte af. Vanwege de P92-staallegeringselementen, legeringselementen opgelost in het austeniet om de austeniethardbaarheid te vergroten, wordt de moeilijkheid van de eutectische ontleding uitgebreider, dus moet er een voldoende lange isotherme tijd zijn om de eutectische ontleding te maken, de vorming van de perlietorganisatie.
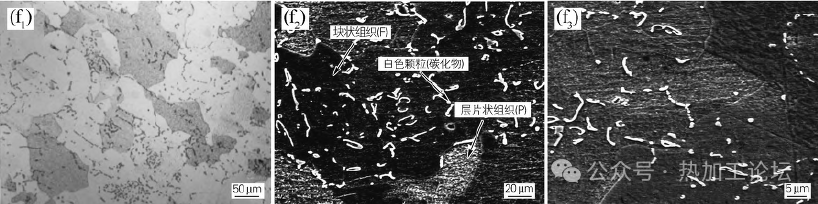
Figuur 1(f) toont de microstructuur van P92-staal bij een isotherme temperatuur van 770°C gedurende 25 uur.
Energiespectrumanalyse werd uitgevoerd op de weefsels met verschillende morfologieën in Fig. 1(f2) om het weefseltype verder te identificeren, zoals weergegeven in Tabel 2. Uit Tabel 2 blijkt dat het koolstofgehalte van de witte deeltjes hoger is dan bij andere organisaties, en de legeringselementen Cr, Mo en V zijn meer, door dit deeltje te analyseren voor de samengestelde carbidedeeltjes die tijdens het koelproces zijn neergeslagen; relatief gesproken is het koolstofgehalte in de discontinue lamellaire organisatie op één na het laagste, en is het koolstofgehalte in de massieve organisatie het minst. Omdat perliet een tweefasenorganisatie is van carburize en ferriet, is het gemiddelde koolstofgehalte hoger dan dat van ferriet; gecombineerd met isotherme temperatuur- en morfologieanalyse, wordt verder bepaald dat de lamellaire organisatie perlietachtig is, en de massieve organisatie is eerst eutectisch ferriet.
Spectrumanalyse van het P92-staal, isothermisch behandeld bij 770 °C gedurende 25 uur, geschreven in tabelvorm met atoomfracties (%)
Structuur |
C |
Nb |
ma |
Ti |
V |
Cr |
Mn |
Fe |
W |
Witte korrels |
11.07 |
0.04 |
0.94 |
0.02 |
2.16 |
8.36 |
2.64 |
54.77 |
2.84 |
Blokstructuur |
9.31 |
0.04 |
0.95 |
0.2 |
0.32 |
8.42 |
0.74 |
85.51 |
10.21 |
Gelaagde structuur |
5.1 |
0 |
0.09 |
0.1 |
0.33 |
7.3 |
0.35 |
85.65 |
0.69 |
2.2 Microhardheid en analyse
Over het algemeen vinden er tijdens het koelproces van gelegeerde staalsoorten die elementen zoals W en Mo bevatten, drie soorten organisatorische transformaties plaats in de onderkoelde austeniet: martensitische transformatie in de lagetemperatuurzone, bainiettransformatie in de gemiddeldetemperatuurzone en perliettransformatie in de hogetemperatuurzone. De verschillende organisatorische evoluties leiden tot verschillende hardheden. Figuur 2 toont de variatie van de hardheidscurve van P92-staal bij verschillende isotherme temperaturen. Uit figuur 2 blijkt dat met de toename van de isotherme temperatuur de hardheid de trend vertoont van eerst afnemen, vervolgens toenemen en ten slotte afnemen. Wanneer de isotherme temperatuur 160 ~ 370 ℃ is, het optreden van martensitische transformatie, Vickers-hardheid van 516HV tot 457HV. Wanneer de isotherme temperatuur 400 ~ 620 ℃ is, vindt er een kleine hoeveelheid bainiettransformatie plaats en neemt de hardheid van 478HV toe tot 484HV; door de kleine bainiettransformatie verandert de hardheid niet veel. Wanneer de isotherme temperatuur 650 ℃ is, vormt zich een kleine hoeveelheid perliet, met een hardheid van 410HV. wanneer de isotherme temperatuur 680 ~ 770 ℃ is, de vorming van ferriet + perlietorganisatie, hardheid van 242HV tot 163HV. vanwege de transformatie van P92-staal bij verschillende temperaturen in de organisatie van de overgang is anders, in het gebied van de martensitische transformatie bij lage temperatuur, wanneer de isotherme temperatuur lager is dan het punt van Ms, met de toename van de temperatuur, neemt het martensietgehalte af, neemt de hardheid af; in het midden van de transformatie van P92-staal bij verschillende temperaturen, wanneer de isotherme temperatuur lager is dan het Ms-punt, neemt het martensitische gehalte af met de temperatuurstijging, neemt de hardheid af; in het bainiettransformatiegebied met gemiddelde temperatuur verandert de hardheid niet veel omdat de hoeveelheid bainiettransformatie klein is; in het perlitische transformatiegebied met hoge temperatuur neemt het eerste eutectische ferrietgehalte toe met de stijging van de isotherme temperatuur, zodat de hardheid blijft afnemen, dus met de toename van de isotherme temperatuur is de materiaalhardheid over het algemeen een dalende trend, en de trend van de verandering in hardheid en de analyse van de organisatie is in lijn met de trend.
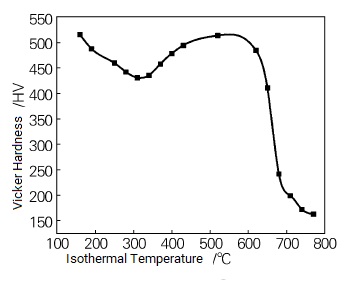
Variatie van hardheidscurven van P92-staal bij verschillende isotherme temperaturen
3. Conclusie
1) Het kritische punt Ac1 van P92-staal is 792,4 ℃, Ac3 is 879,8 ℃ en Ms is 372,3 ℃.
2) P92-staal bij verschillende isotherme temperaturen om de kamertemperatuurorganisatie te verkrijgen is anders; in de 160 ~ 370 ℃ isotherme 1 uur is de kamertemperatuurorganisatie martensiet; in de 400 ~ 430 ℃ isotherme 1 uur is de organisatie van een kleine hoeveelheid bainiet + martensiet; in de 520 ~ 620 ℃ isotherme 1 uur is de organisatie relatief stabiel, een korte periode (1 uur) treedt niet op binnen de transformatie, de kamertemperatuurorganisatie is martensiet; in de 650 ℃ isotherme 25 uur is de kamertemperatuurorganisatie perliet. h, kamertemperatuurorganisatie voor perliet + martensiet; in 680 ~ 770 ℃ isotherme 25 uur is de organisatie getransformeerd in perliet + eerste eutectische ferriet.
3) Austenitisatie van P92-staal in Ac1 onder de isotherme temperatuur, met de verlaging van de isotherme temperatuur, heeft de hardheid van het materiaal als geheel de neiging toe te nemen, isotherm bij 770 ℃ na het optreden van de eerste eutectische ferrietprecipitatie, perlitische transformatie, de hardheid is het laagst, ongeveer 163HV; isotherm bij 160 ℃ na het optreden van de martensitische transformatie, de hardheid is het hoogst, ongeveer 516HV.