異なる等温温度における P92 鋼の微細構造の進化
P92鋼 主に超々臨界ボイラー、超高圧パイプライン、その他の高温高圧設備に使用されています。P92鋼は、P91鋼の化学組成にW元素とB元素の微量元素の添加を基本とし、Mo含有量を減らし、粒界強化と分散強化をさまざまな方法で行い、P92鋼の総合性能を向上させています。P92鋼はP91鋼よりも耐酸化性能と耐腐食性が優れています。P92鋼管の製造には、熱間加工プロセスが不可欠です。熱処理技術により、製造プロセスで発生する内部欠陥を排除し、鋼の性能を作業条件のニーズに合わせることができます。熱間加工プロセスにおける組織の種類と状態は、性能が標準を満たすかどうかに影響を与える重要な要因です。したがって、本論文では、異なる等温温度における P92 鋼管の組織を分析し、さまざまな温度における P92 鋼管の組織の進化を明らかにします。これは、実際の熱間加工プロセスの組織分析と性能制御に情報サポートを提供するだけでなく、熱間加工プロセスの開発のための実験的基礎も築きます。
1. 試験材料と方法
1.1 試験材料
試験に使用した鋼材は使用状態のP92鋼管(1060℃焼入れ+760℃焼戻し)であり、その化学成分は表1に示すとおりである。完成した管の中央部の長さ方向の特定位置からφ4mm×10mmの円筒形試験片を切り出し、焼入れ膨張計を使用して異なる温度での組織変態を調べた。
表1 P92鋼の主な化学組成(質量分率別)(%)
要素 |
C |
シ |
ミネソタ |
Cr |
ニ |
モ |
五 |
アル |
B |
いいえ |
わ |
鉄 |
% |
0.13 |
0.2 |
0.42 |
8.67 |
0.25 |
0.48 |
0.19 |
0.008 |
0.002 |
0.05 |
1.51 |
バランス |
1.2 テストプロセス
L78急冷熱膨張計を使用し、0.05℃/sで1050℃まで15分間加熱し、200℃/sで室温まで冷却しました。材料の相変化の臨界点を測定したところ、Ac1は792.4℃、Ac3は879.8℃、Msは372.3℃でした。試験片は10℃/秒の速度で1050℃まで加熱され、15分間保持された後、150℃/秒の速度で異なる温度(770、740、710、680、650、620、520、430、400、370、340、310、280、250、190、および160℃)まで冷却され、異なる時間(620℃以下で1時間、620℃以上で25時間保持)保持された。620℃以上で25時間保持)、等温端の電源をオフにして、試験片を室温まで空冷する。1.3 試験方法
異なる工程で試験片の表面を研磨した後、王水を使用して試験片の表面を腐食しました。AXIOVERT 25 Zeiss 顕微鏡と QWANTA 450 環境走査型電子顕微鏡を使用して組織を観察および分析しました。HVS-50 ビッカース硬度計 (荷重 1kg) を使用して、各試験片の表面の数か所で硬度を測定し、その平均値を試験片の硬度値としました。
2. テスト結果と分析
2.1 異なる等温温度の構成と分析
図1は、1050℃で異なる時間と温度で完全オーステナイト化を行った後のP92鋼の微細構造を示しています。図1(a)は、190℃で1時間等温化した後のP92鋼の微細構造を示しています。図1(a2)から、常温組織はマルテンサイト(M)であることがわかります。図1(a3)から、マルテンサイトがラス状特性を示していることがわかります。鋼のMs点は約372℃であるため、Ms点未満の等温温度でマルテンサイト相変態が起こり、マルテンサイトが形成されます。P92鋼の炭素含有量は低炭素組成の範囲に属し、ラス状の形態がマルテンサイトの特徴です。
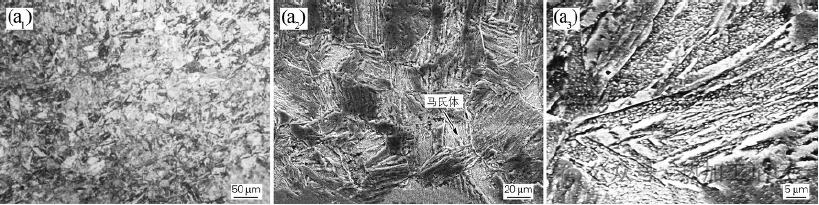
図1(a)は、190℃で1時間等温保持した後のP92鋼の微細組織を示す。
図1(b)は、430℃で1時間等温保持したP92鋼の微細組織です。等温温度が430℃まで上昇すると、P92鋼はベイナイト変態域に達します。鋼にはMo、B、W元素が含まれているため、これらの元素はベイナイト変態にほとんど影響を与えず、パーライト変態を遅らせます。そのため、P92鋼を430℃で1時間保持すると、一定量のベイナイトが組織化されます。その後、残りの過冷却オーステナイトは空冷時にマルテンサイトに変態します。
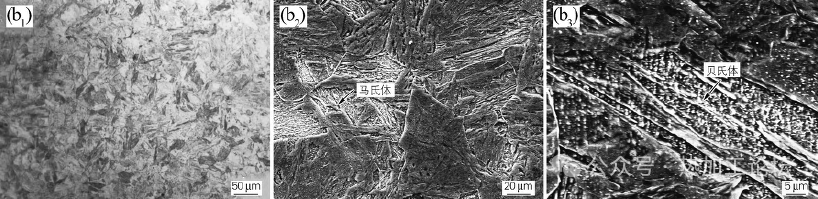
図1(b) P92鋼の430℃等温1時間における微細組織
図1(c)は、520℃で1時間等温保持したP92鋼の微細組織を示す。等温保持温度が520℃になると、Cr、Mo、Mnなどの合金元素によってパーライト変態が抑制され、ベイナイト変態開始点(Bs点)が下がるため、特定の温度範囲で過冷却オーステナイトの安定化領域が現れる。図1(c)は、520℃で1時間保持した後、過冷却オーステナイト変態が起こらず、その後空冷してマルテンサイトを形成し、最終的に室温でマルテンサイト組織になった様子を示している。
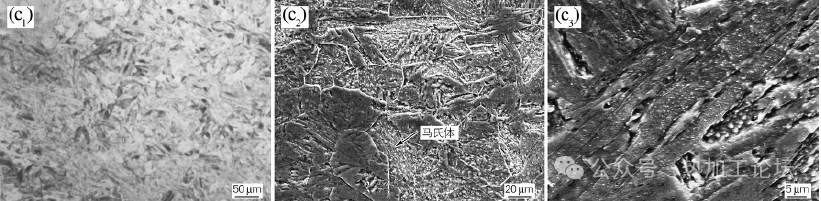
図1(c)は、520℃等温1時間におけるP92鋼の微細組織を示す。
図1(d)はP92鋼の650℃等温25hのマルテンサイト+パーライトの微細組織である。図1(d3)に示すように、パーライトは不連続なラメラ特性を示し、表面の炭化物は短棒状の析出を示している。これは、P92鋼のCr、Mo、Vなどの合金元素が過冷却オーステナイトの安定性を同時に向上させ、P92鋼のパーライト形態が変化することによるもので、つまり、パーライト体中の炭化物が短棒状の炭化物になり、このパーライト体はパーライト類と呼ばれる。同時に、組織中に多くの微細な第二相粒子が見られた。
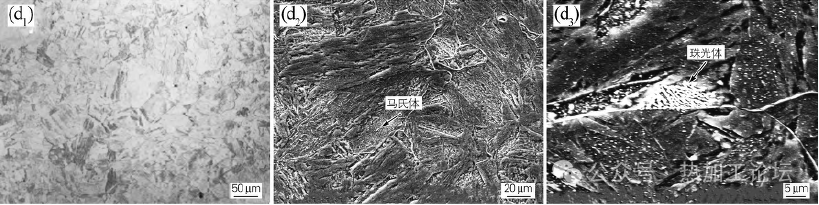
図1(d)P92鋼の650℃等温25時間におけるマルテンサイト+パーライトの微細組織
図1(e)は、740℃等温25時間におけるP92鋼の微細組織を示しています。740℃等温では、最初に共晶塊状フェライト析出が起こり、その後オーステナイト共晶分解が起こり、パーライト様組織になります。650℃等温(図1(d3)参照)と比較すると、等温温度の上昇に伴いパーライト組織は粗くなり、パーライトの2相特性、すなわちフェライトと短い棒状の炭化物がはっきりと見えます。
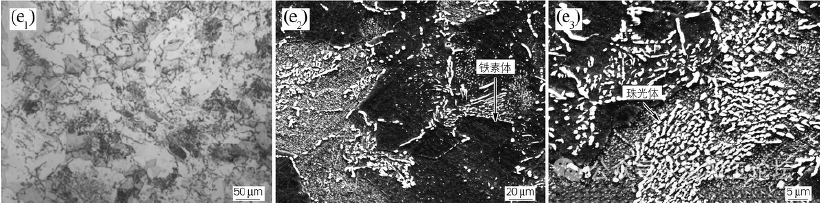
図1(e)はP92鋼の740℃等温25時間における微細組織を示す。
図1(f)は、770℃等温で25時間保持したP92鋼の微細組織を示しています。770℃等温では、等温時間が長くなるにつれて、最初にフェライトの析出が起こり、次に過冷却オーステナイトが共晶分解してフェライト+パーライト組織を形成します。等温温度の上昇に伴い、最初の共晶フェライト含有量が増加し、パーライト含有量が減少します。P92鋼の合金元素、つまりオーステナイトに溶解してオーステナイトの硬化性を高める合金元素のために、共晶分解の難しさはより広範囲に及ぶため、共晶分解、つまりパーライト組織の形成を起こすには、十分に長い等温時間が必要です。
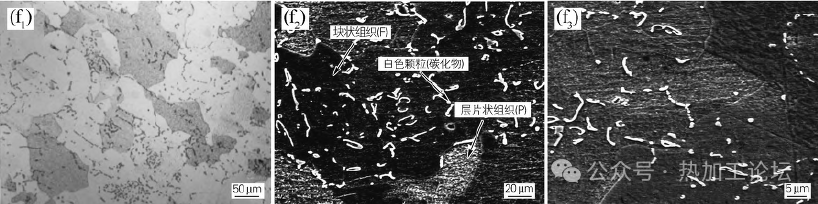
図1(f)は、770℃の等温温度で25時間保持したP92鋼の微細組織を示す。
図1(f2)の異なる形態の組織に対してエネルギースペクトル分析を行い、組織の種類をさらに識別しました。表2に示します。表2から、白い粒子の炭素含有量が他の組織よりも高く、合金元素のCr、Mo、Vが多いことがわかります。この粒子を冷却過程で析出した複合炭化物粒子について分析すると、比較すると、不連続なラメラ組織の炭素含有量は2番目に低く、塊状組織の炭素含有量は最も低いです。パーライトは炭化物とフェライトの2相組織であるため、平均炭素含有量はフェライトよりも高く、等温温度と形態分析を組み合わせると、ラメラ組織はパーライト様であり、塊状組織は第一共晶フェライトであることがさらに判明しました。
770 °C で 25 時間等温処理した P92 鋼のスペクトル分析 (原子分率による表形式で記述) (%)
構造 |
C |
いいえ |
モ |
ティ |
五 |
Cr |
ミネソタ |
鉄 |
わ |
白い顆粒 |
11.07 |
0.04 |
0.94 |
0.02 |
2.16 |
8.36 |
2.64 |
54.77 |
2.84 |
ブロック構造 |
9.31 |
0.04 |
0.95 |
0.2 |
0.32 |
8.42 |
0.74 |
85.51 |
10.21 |
階層構造 |
5.1 |
0 |
0.09 |
0.1 |
0.33 |
7.3 |
0.35 |
85.65 |
0.69 |
2.2 微小硬度と分析
一般的に言えば、WやMoなどの元素を含む合金鋼の冷却過程で、過冷却オーステナイトに3種類の組織変態が発生します。低温域ではマルテンサイト変態、中温域ではベイナイト変態、高温域ではパーライト変態です。異なる組織進化は異なる硬度につながります。図2は、異なる等温温度におけるP92鋼の硬度曲線の変化を示しています。図2から、等温温度の上昇に伴い、硬度は最初に低下し、次に増加し、最後に低下する傾向を示していることがわかります。等温温度が160〜370℃の場合、マルテンサイト変態が発生し、ビッカース硬度は516HVから457HVに増加します。等温温度が400〜620℃の場合、少量のベイナイト変態が発生し、硬度478HVが484HVに増加します。ベイナイト変態が小さいため、硬度はあまり変化しません。等温温度が 650 ℃のとき、少量のパーライトが形成され、硬度は 410 HV です。等温温度が 680 ~ 770 ℃のとき、フェライト + パーライト組織が形成され、硬度は 242 HV から 163 HV です。P92 鋼の変態により、異なる温度での組織遷移が異なり、低温マルテンサイト変態の領域では、等温温度が Ms 点よりも低い場合、温度の上昇とともに、マルテンサイト含有量が減少し、硬度が低下します。P92 鋼の異なる温度での変態の途中で、等温温度が Ms 点よりも低い場合、温度の上昇とともに、マルテンサイト含有量が減少し、硬度が低下します。中温ベイナイト変態領域では、ベイナイト変態量が少ないため、硬度はあまり変化しません。高温パーライト変態領域では、等温温度の上昇に伴い、第一共晶フェライト含有量が増加し、硬度が低下し続けるため、等温温度の上昇に伴い、材料の硬度は一般的に低下傾向にあり、硬度の変化の傾向と組織の分析はその傾向と一致しています。
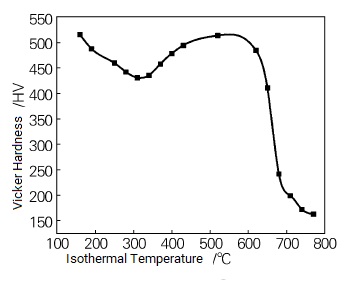
異なる等温温度における P92 鋼の硬度曲線の変化
3. 結論
1) P92鋼の臨界点Ac1は792.4℃、Ac3は879.8℃、Msは372.3℃である。
2) P92 鋼は、異なる等温温度で得られる室温組織が異なります。160 ~ 370 ℃ 等温 1 時間では、室温組織はマルテンサイトです。400 ~ 430 ℃ 等温 1 時間では、少量のベイナイト + マルテンサイトの組織です。520 ~ 620 ℃ 等温 1 時間では、組織は比較的安定しており、短時間 (1 時間) 内に変態は発生せず、室温組織はマルテンサイトです。650 ℃ 等温 25 時間では、室温組織はパーライトです。h、室温組織はパーライト + マルテンサイトです。680 ~ 770 ℃ 等温 25 時間では、組織はパーライト + 第一共晶フェライトに変態しました。
3) P92鋼はAc1以下の等温でオーステナイト化され、等温温度の低下とともに、材料全体の硬度が増加する傾向があり、等温770℃で最初の共晶フェライト析出、パーライト変態が発生した後、硬度は最低の約163HVになります。等温160℃でマルテンサイト変態が発生した後、硬度は最高の約516HVになります。