SAE 4140 saumattoman teräsputken putken päässä olevan renkaan muotoisen halkeaman syytä tutkittiin kemiallisen koostumuksen tutkimuksella, kovuustestillä, metallografisella havainnolla, pyyhkäisyelektronimikroskoopilla ja energiaspektrianalyysillä. Tulokset osoittavat, että saumattoman SAE 4140 -teräsputken rengasmainen halkeama on sammutushalkeama, joka esiintyy yleensä putken päässä. Syynä sammutushalkeamiseen ovat erilaiset jäähdytysnopeudet sisä- ja ulkoseinien välillä, ja ulkoseinän jäähtymisnopeus on paljon suurempi kuin sisäseinän, mikä johtaa halkeiluvikaan, joka johtuu jännityskeskittymisestä lähellä sisäseinän sijaintia. Renkaan muotoinen halkeama voidaan poistaa lisäämällä teräsputken sisäseinän jäähdytysnopeutta karkaisun aikana, parantamalla jäähdytysnopeuden tasaisuutta sisä- ja ulkoseinän välillä ja säätämällä lämpötila sammutuksen jälkeen 150 ~ 200 asteeseen. ℃ vähentää sammutusjännitystä itsekarkaisulla.
SAE 4140 on niukkaseosteinen CrMo-rakenneteräs, joka on amerikkalainen ASTM A519 -standardilaatu, kansallisessa standardissa 42CrMo, joka perustuu Mn-pitoisuuden kasvuun; siksi SAE 4140 -karkenevuutta on edelleen parannettu. SAE 4140 saumaton teräsputki, sen sijaan, että kiinteät takeet, erilaisten onttojen akselien, sylinterien, holkkien ja muiden osien valssaus aihion tuotanto voi merkittävästi parantaa tuotannon tehokkuutta ja säästää terästä; SAE 4140 -teräsputkia käytetään laajalti öljy- ja kaasukenttien kaivosruuvinporaustyökaluissa ja muissa porauslaitteissa. SAE 4140 saumaton teräsputkien karkaisukäsittely voi täyttää eri teräslujuuksien ja sitkeyssovituksen vaatimukset optimoimalla lämpökäsittelyprosessia. Silti sen havaitaan usein vaikuttavan tuotteiden toimitusvirheisiin tuotantoprosessissa. Tämä artikkeli keskittyy pääasiassa SAE 4140 -teräsputkeen sammutusprosessissa putken pään seinämän paksuuden keskellä, tuottaa rengasmaisen halkeaman vikaanalyysin ja esittää parannustoimenpiteitä.
1. Testausmateriaalit ja -menetelmät
Yritys valmisti tekniset tiedot ∅ 139,7 × 31,75 mm SAE 4140 -teräslaadun saumattomalle teräsputkelle, aihion lämmityksen tuotantoprosessille → lävistys → valssaus → mitoitus → karkaisu (850 ℃ liotusaika 70 min sammutus + putken pyöriminen vesisuihkun jäähdytyksen ulkopuolella +735 ℃ liotusaika 2 h karkaisu) → Vikojen havaitseminen ja tarkastus. Karkaisukäsittelyn jälkeen vikojen havaitsemistarkastus paljasti, että seinämän paksuuden keskellä putken päässä oli rengasmainen halkeama, kuten kuvassa 1; rengasmainen halkeama ilmestyi noin 21-24 mm:n etäisyydelle ulkopuolelta, ympyröi putken kehän ja oli osittain epäjatkuva, kun taas putken rungosta ei löytynyt tällaista vikaa.
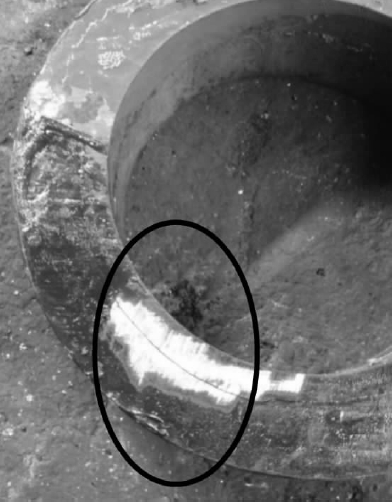
Kuva 1 Renkaan muotoinen halkeama putken päässä
Ota erä teräsputkien sammutusnäytteitä sammutusanalyysiä ja sammutusorganisaation tarkkailua varten sekä teräsputken koostumuksen spektrianalyysiä samanaikaisesti karkaistun teräsputken halkeamista varten, jotta voit ottaa suuritehoisia näytteitä halkeaman mikromorfologian tarkkailemiseksi. , raekokotaso, ja pyyhkäisyelektronimikroskoopissa spektrometrillä mikroalueanalyysin sisäisen koostumuksen halkeamien selvittämiseksi.
2. Testitulokset
2.1 Kemiallinen koostumus
Taulukossa 1 on esitetty kemiallisen koostumuksen spektrianalyysitulokset, ja alkuaineiden koostumus on ASTM A519 -standardin vaatimusten mukainen.
Taulukko 1 Kemiallisen koostumuksen analyysitulokset (massafraktio, %)
Elementti |
C |
Si |
Mn |
P |
S |
Cr |
Mo |
Cu |
Ni |
Sisältö |
0.39 |
0.20 |
0.82 |
0.01 |
0.005 |
0.94 |
0.18 |
0.05 |
0.02 |
ASTM A519 -vaatimus |
0.38-0.43 |
0.15-0.35 |
0.75-1.00 |
≤ 0,04 |
≤ 0,04 |
0.8-1.1 |
0.15-0.25 |
≤ 0,35 |
≤ 0,25 |
2.2 Putken kovettumistesti
Kokonaisseinämäpaksuuden karkaisukovuustestin sammutetuissa näytteissä seinämän paksuuden kokonaiskovuustulokset, kuten kuvassa 2, näkyvät kuvassa 2, 21 ~ 24 mm:n päässä ulkopuolelta sammutuskovuus alkoi laskea merkittävästi, ja ulkopuolelta 21 ~ 24 mm on putken korkean lämpötilan karkaisu, joka löytyy rengashalkeaman alueelta, alue seinämän paksuuden alapuolella ja yläpuolella seinämän paksuuden kovuuden äärimmäisen eron seinämän paksuuden sijainnin välillä alueella saavutti 5 (HRC) tai niin. Tämän alueen alemman ja ylemmän seinämän paksuuden välinen kovuusero on noin 5 (HRC). Metallografinen organisaatio sammutetussa tilassa on esitetty kuvassa 3. Metallografisesta organisaatiosta kuviossa 3; voidaan nähdä, että putken ulkoalueella oleva organisaatio on pieni määrä ferriittiä + martensiittia, kun taas sisäpinnan lähellä oleva organisaatio ei ole sammutettu, ja siinä on pieni määrä ferriittiä ja bainiittia, mikä johtaa alhaiseen karkaisukovuuteen. putken ulkopinnasta putken sisäpinnalle 21 mm etäisyydellä. Rengashalkeamien korkea konsistenssi putken seinämässä ja äärimmäisen eron sijainti karkaisukovuudessa viittaavat siihen, että karkaisuprosessissa syntyy todennäköisesti rengashalkeamia. Rengashalkeamien sijainnin ja heikomman karkaisukovuuden välinen korkea konsistenssi osoittaa, että rengashalkeamia on saatettu syntyä sammutusprosessin aikana.
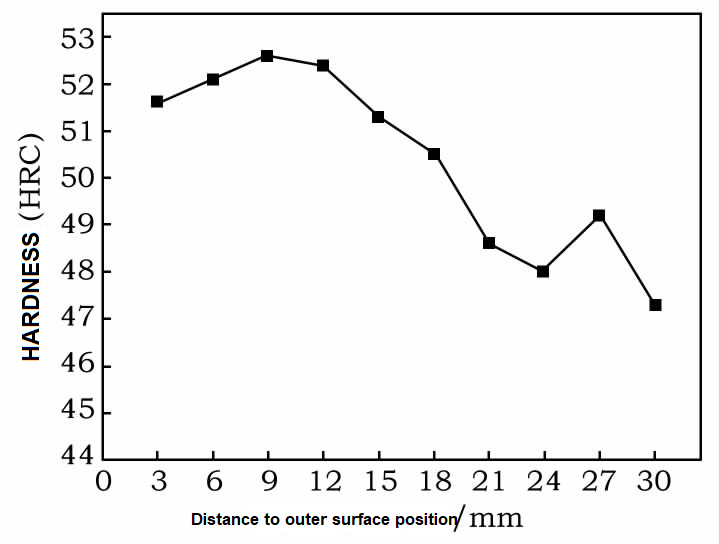
Kuva 2 Karkaisukovuuden arvo koko seinämän paksuudella
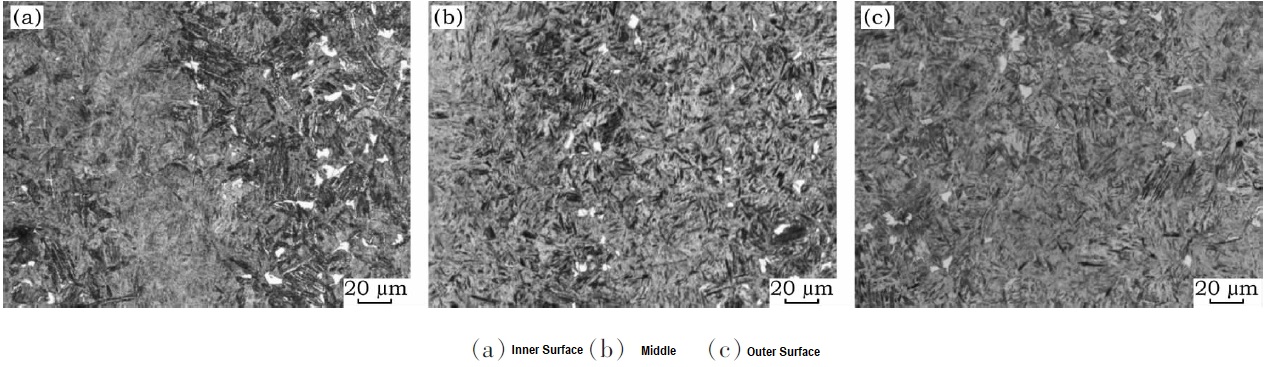
Kuva 3 Teräsputken karkaisurakenne
2.3 Teräsputken metallografiset tulokset on esitetty kuvassa 4 ja kuvassa 5, vastaavasti.
Teräsputken matriisiorganisaatio on karkaistua austeniittia + pieni määrä ferriittiä + pieni määrä bainiittia, jonka raekoko on 8, mikä on keskimääräinen karkaistu organisaatio; halkeamat ulottuvat pitkittäissuuntaa pitkin, joka kuuluu kiteisen halkeaman varrelle, ja halkeamien kahdella sivulla on tyypilliset kiinnittymisominaisuudet; molemmilla puolilla on hiilenpoistoilmiö, ja halkeamien pinnalla on havaittavissa korkean lämpötilan harmaa oksidikerros. Molemmilla puolilla on hiilenpoistoa ja halkeaman pinnalla on havaittavissa korkean lämpötilan harmaa oksidikerros, eikä halkeaman läheisyydessä ole havaittavissa ei-metallisia sulkeumia.
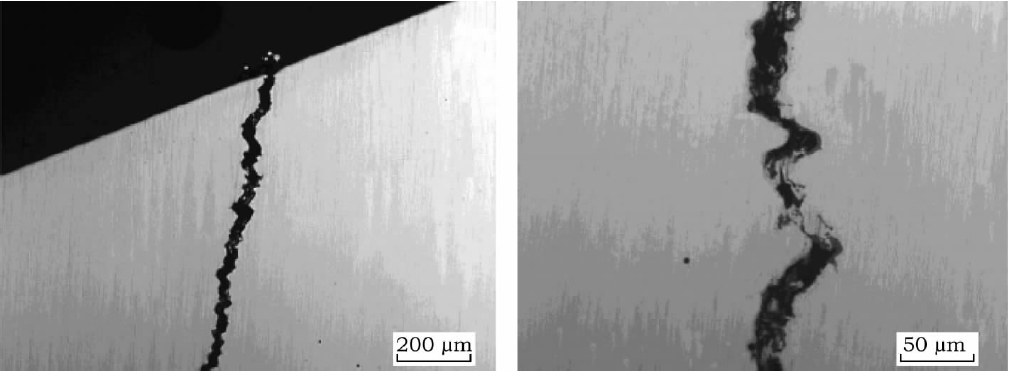
Kuva 4 Halkeamien morfologian havainnot
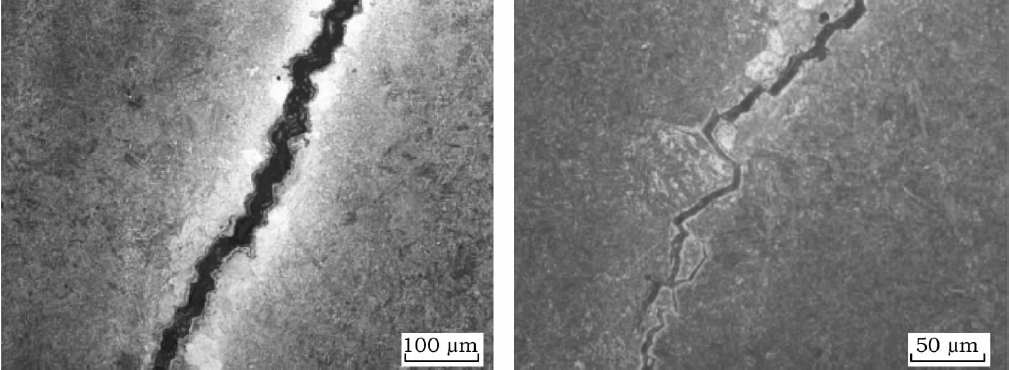
Kuva 5 Halkeaman mikrorakenne
2.4 Halkeamien morfologia ja energiaspektrianalyysin tulokset
Murtuman avaamisen jälkeen halkeaman mikromorfologiaa tarkkaillaan pyyhkäisyelektronimikroskoopilla kuvan 6 mukaisesti, mikä osoittaa, että murtuma on altistunut korkeille lämpötiloille ja pinnalla on tapahtunut korkean lämpötilan hapettumista. Murtuma on pääosin kidemurtuman varrella, raekoko vaihtelee 20-30 μm, eikä karkeita rakeita eikä epänormaalia organisatorisia vikoja löydy; Energiaspektrianalyysi osoittaa, että murtuman pinta koostuu pääosin raudasta ja sen oksideista, eikä siinä ole havaittavissa epänormaaleja vieraita alkuaineita. Spektrianalyysi osoittaa, että murtumapinta on pääasiassa rautaa ja sen oksideja, eikä siinä ole epänormaalia vierasta elementtiä.
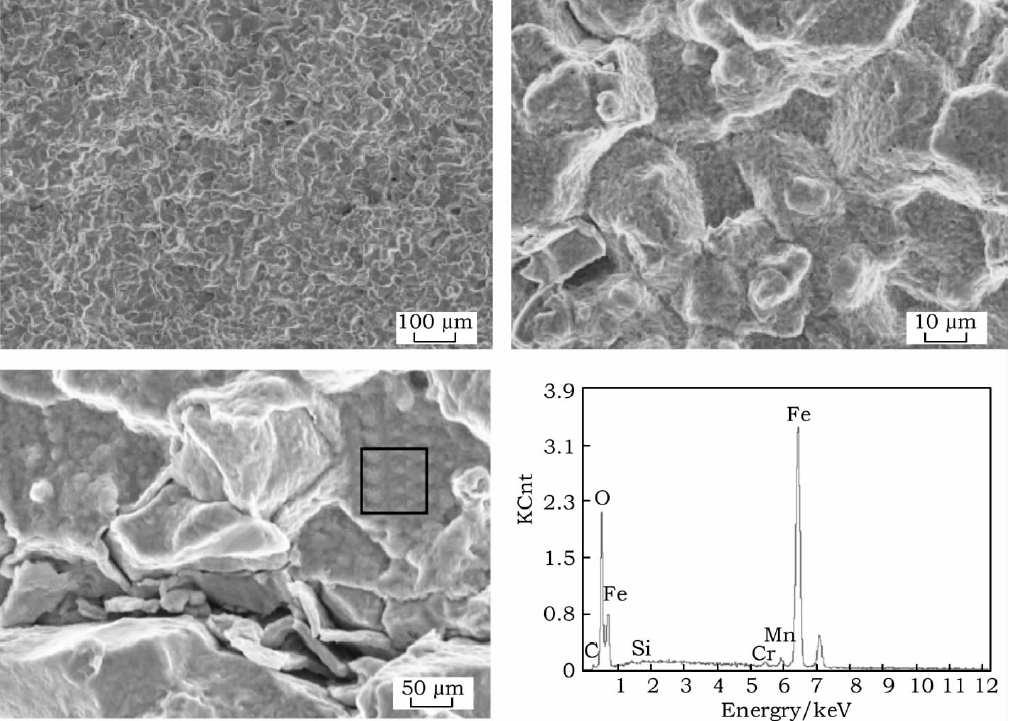
Kuva 6 Halkeaman murtuman morfologia
3 Analyysi ja keskustelu
3.1 Halkeamien analyysi
Halkeaman mikromorfologian näkökulmasta halkeama on suora; häntä on kaareva ja terävä; halkeaman laajenemisreitti näyttää halkeilun ominaisuudet kiteen varrella, ja halkeaman kahdella sivulla on tyypillisiä niveltymisominaisuuksia, jotka ovat tavanomaisia sammutushalkeamien ominaisuuksia. Silti metallografisessa tutkimuksessa havaittiin, että halkeaman molemmilla puolilla on hiilenpoistoilmiöitä, mikä ei ole linjassa perinteisten karkaisuhalkeamien ominaisuuksien kanssa, kun otetaan huomioon se, että teräsputken karkaisulämpötila on 735 ℃, ja Ac1 on 738 ℃ standardissa SAE 4140, mikä ei ole sopusoinnussa halkeamien sammuttamisen tavanomaisten ominaisuuksien kanssa. Ottaen huomioon, että putken karkaisulämpötila on 735 °C ja SAE 4140:n Ac1 on 738 °C, jotka ovat hyvin lähellä toisiaan, oletetaan, että hiilenpoisto halkeaman molemmilla puolilla liittyy korkeaan lämpötilaan. lämpötilakarkaisu karkaisun aikana (735 °C) eikä se ole halkeama, joka oli olemassa jo ennen putken lämpökäsittelyä.
3.2 Halkeilun syyt
Karkaisuhalkeamien syyt liittyvät yleensä sammutuksen lämmityslämpötilaan, sammutuksen jäähdytysnopeuteen, metallurgisiin vaurioihin ja sammutusjännityksiin. Koostumusanalyysin tulosten perusteella putken kemiallinen koostumus täyttää ASTM A519 -standardin SAE 4140 -teräslaadun vaatimukset, eikä ylimääräisiä elementtejä havaittu; halkeamien läheltä ei löytynyt ei-metallisia sulkeumia, ja halkeaman energiaspektrianalyysi osoitti, että halkeamien harmaat hapettumistuotteet olivat Fe ja sen oksideja, eikä epänormaaleja vieraita alkuaineita näkynyt, joten voidaan sulkea pois, että metallurgiset viat aiheuttivat rengasmaisia halkeamia; putken raekokoluokka oli Grade 8 ja raekoko Grade 7 ja raekoko Grade 8 ja raekoko Grade 8. Putken raekoko on 8; jyvät ovat hienojakoisia eikä karkeita, mikä osoittaa, että sammutushalkeamalla ei ole mitään tekemistä sammuttamisen kuumennuslämpötilan kanssa.
Karkaisuhalkeamien muodostuminen liittyy läheisesti sammutusjännityksiin, jotka on jaettu lämpö- ja organisatorisiin jännityksiin. Lämpöjännitys johtuu teräsputken jäähdytysprosessista; teräsputken pintakerroksen ja sydämen jäähdytysnopeus eivät ole yhdenmukaiset, mikä johtaa materiaalin epätasaiseen kutistumiseen ja sisäisiin jännityksiin; tuloksena teräsputken pintakerrokseen kohdistuu puristusjännitys ja vetojännitysten sydän; kudosjännitykset on teräsputkiorganisaation vaimeneminen martensiittimuunnoksiin, samalla kun sisäisten jännitysten muodostumisen epäjohdonmukaisuuden tilavuus laajenee, tuloksen synnyttämien jännitysten organisoituminen on vetojännitysten pintakerros, keskus vetojännityksistä. Nämä kaksi jännitystyyppiä teräsputkessa esiintyvät samassa osassa, mutta suuntarooli on päinvastainen; tuloksen yhteisvaikutus on, että toinen kahdesta jännityksen hallitsevasta tekijästä, lämpöjännityksen hallitseva rooli on seurausta työkappaleen sydämen vetolujuudesta, pintapaineesta; kudosten jännitys hallitseva rooli on seurausta työkappaleen sydämen vetopaineen pintavetovoimasta.
SAE 4140 -teräsputkien sammutus pyörivän ulkosuihkun jäähdytystuotannon avulla, ulkopinnan jäähdytysnopeus on paljon suurempi kuin sisäpinnan, teräsputken ulompi metalli on kaikki sammutettu, kun taas sisämetallia ei ole täysin sammutettu osan tuottamiseksi ferriitti- ja bainiittiorganisaatio, sisäisestä metallista johtuvaa sisämetallia ei voida täysin muuttaa martensiittiseksi organisaatioksi, teräsputken sisämetalli joutuu väistämättä alttiiksi vetojännitykselle, joka syntyy martensiitin ulkoseinän laajenemisesta, ja Samanaikaisesti erityyppisistä organisaatiotyypeistä johtuen sen ominaistilavuus on erilainen sisä- ja ulkometallin välillä. Samanaikaisesti erityyppisten organisaatioiden vuoksi metallin sisä- ja ulkokerroksen tilavuus on erilainen. , ja kutistumisnopeus ei ole sama jäähdytyksen aikana, myös vetojännitys syntyy kahden organisaatiotyypin rajapinnassa, ja jännityksen jakautumista hallitsevat lämpöjännitykset ja vetojännitys, joka syntyy putken sisällä olevat kaksi organisaatiotyyppiä ovat suurimmat, mikä johtaa siihen, että rengas sammuttaa halkeamia putken seinämän paksuuden alueella lähellä sisäpintaa (21-24 mm etäisyydellä ulkopinnasta); lisäksi teräsputken pää on koko putken geometrialle herkkä osa, joka on altis rasitukselle. Lisäksi putken pää on geometrisesti herkkä osa koko putkea, joka on altis jännityskeskittymille. Tämä rengashalkeama esiintyy yleensä vain putken päässä, eikä sellaisia halkeamia ole löydetty putken rungosta.
Yhteenvetona voidaan todeta, että paksuseinäisten SAE 4140 teräsputkien renkaan muotoiset halkeamat johtuvat sisä- ja ulkoseinien epätasaisesta jäähtymisestä; ulkoseinän jäähdytysnopeus on paljon suurempi kuin sisäseinän; paksuseinäisen SAE 4140 teräsputken tuotanto nykyisen jäähdytysmenetelmän muuttamiseksi, ei voida käyttää vain jäähdytysprosessin ulkopuolella, tarve vahvistaa teräsputken sisäseinän jäähdytystä, parantaa jäähdytysnopeuden tasaisuutta. paksuseinäisen teräsputken sisä- ja ulkoseinät vähentämään jännityspitoisuutta ja poistamaan rengashalkeamia. Rengas halkeilee.
3.3 Parannustoimenpiteet
Karkaisuhalkeamien välttämiseksi karkaisuprosessin suunnittelussa kaikki olosuhteet, jotka vaikuttavat karkaisujen vetojännitysten kehittymiseen, ovat halkeamien muodostumisen tekijöitä, mukaan lukien lämmityslämpötila, jäähdytysprosessi ja poistolämpötila. Ehdotettuja parannettuja prosessitoimenpiteitä ovat: sammutuslämpötila 830-850 ℃; putken keskilinjaan sopivan sisäisen suuttimen käyttö, sopivan sisäisen suihkuvirtauksen hallinta, sisäreiän jäähdytysnopeuden parantaminen varmistaakseen, että paksuseinäisen teräsputken sisä- ja ulkoseinien jäähdytysnopeus yhtenäisyys; valvonta jälkisammutus lämpötila 150-200 ℃, käyttö teräsputken jäännöslämpötila itsekarkaisuun, vähentää sammutus jännitteitä teräsputki.
Parannetun tekniikan käyttö tuottaa ∅158,75 × 34,93 mm, ∅139,7 × 31,75 mm, ∅254 × 38,1 mm, ∅224 × 26 mm ja niin edelleen, kymmenien teräsputkien eritelmien mukaan. Ultraäänivirhetarkastuksen jälkeen tuotteet ovat päteviä, eikä niissä ole rengassammutushalkeamia.
4. Johtopäätös
(1) Putken halkeamien makroskooppisten ja mikroskooppisten ominaisuuksien mukaan SAE 4140 -teräsputkien putken päissä olevat rengashalkeamat kuuluvat jäähdytysjännityksen aiheuttamaan halkeamaan, jota yleensä esiintyy putken päissä.
(2) Karkaistu SAE 4140 paksuseinämäinen teräsputki rengasmaiset halkeamat johtuvat sisä- ja ulkoseinien epätasaisesta jäähtymisestä. Ulkoseinän jäähdytysnopeus on paljon suurempi kuin sisäseinän. Paksuseinäisen teräsputken sisä- ja ulkoseinien jäähdytysnopeuden yhtenäisyyden parantamiseksi paksuseinämäisen SAE 4140 -teräsputken valmistuksessa on vahvistettava sisäseinän jäähdytystä.