Oleoducto submarino: una exploración en profundidad
Introducción
Los oleoductos submarinos transportan petróleo, gas y otros fluidos a través de grandes distancias submarinas. Estos oleoductos son esenciales para conectar plataformas petroleras y gasíferas en alta mar con instalaciones en tierra, lo que permite la transferencia eficiente y segura de recursos desde ubicaciones remotas al mercado global. Sin embargo, el diseño, la construcción y el mantenimiento de oleoductos submarinos presentan desafíos únicos debido al duro y dinámico entorno marino. Este blog ofrece una descripción general completa de los oleoductos submarinos, incluidas sus aplicaciones, consideraciones de diseño, materiales, métodos de instalación y estrategias de mantenimiento.
1. El papel de los oleoductos submarinos en la industria energética
1.1 Importancia de los ductos submarinos
Los oleoductos submarinos son la vía vital de la industria del petróleo y el gas en alta mar. Proporcionan una ruta directa y segura para transportar hidrocarburos desde los yacimientos en alta mar hasta las refinerías y plantas de procesamiento en tierra. Estos oleoductos son esenciales para la cadena de suministro de energía global, en particular a medida que aumenta la demanda de petróleo y gas.
1.2 Aplicaciones clave
Transporte de petróleo y gas: Los ductos submarinos se utilizan principalmente para transportar petróleo crudo, gas natural y condensados desde plataformas de producción en alta mar hasta instalaciones en tierra para su procesamiento y distribución.
Líneas de inyección de agua: En las operaciones de recuperación mejorada de petróleo (EOR), los ductos submarinos inyectan agua en el yacimiento para mantener la presión y mejorar las tasas de recuperación de petróleo.
Umbilicales submarinos: Estas tuberías especializadas transportan fluidos de control, energía eléctrica y señales de comunicación entre el equipo submarino y las instalaciones de superficie.
2. Consideraciones de diseño para tuberías submarinas
2.1 Factores ambientales y geotécnicos
Medio ambiente marino: Las tuberías submarinas deben estar diseñadas para soportar los efectos corrosivos del agua de mar, las fuertes corrientes y los posibles impactos de buques u objetos marinos. Las condiciones de temperatura y presión en el fondo marino también influyen en la selección de materiales y el diseño de las tuberías.
Topografía del fondo marino: La topografía del lecho marino, incluidas las pendientes, los valles y las zanjas, afecta el trazado y la estabilidad de las tuberías. Los estudios geotécnicos son esenciales para evaluar las condiciones del lecho marino y determinar la mejor ruta para las tuberías.
Actividad sísmica: En regiones propensas a terremotos, las tuberías submarinas deben diseñarse para adaptarse al movimiento del suelo y evitar daños durante eventos sísmicos.
2.2 Integridad y seguridad de las tuberías
Selección de materiales: Las tuberías submarinas generalmente se construyen con acero al carbono de alta resistencia, recubierto con materiales anticorrosión como epoxi unido por fusión (FBE) o polietileno de tres capas (3LPE) para proteger contra la corrosión y el daño mecánico.
Estabilidad de la tubería: La estabilidad es una cuestión crítica, en particular en zonas con fuertes corrientes o terrenos marinos irregulares. Técnicas como excavar zanjas, enterrar o agregar capas de hormigón para estabilizar la tubería.
Sistemas de detección de fugas: Los ductos submarinos están equipados con sistemas avanzados de detección de fugas que monitorean la presión, los caudales y otros parámetros en tiempo real para detectar fugas o anomalías.
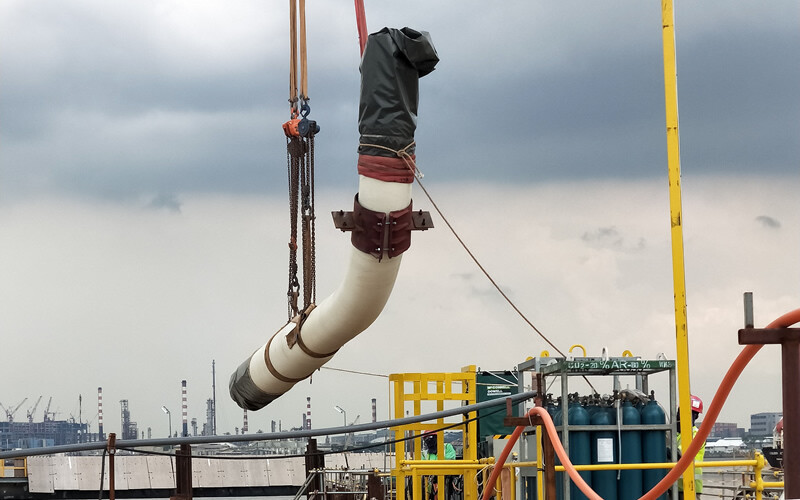
Tubería submarina o submarina
3. Materiales utilizados en la construcción de tuberías submarinas
3.1 Acero al carbono
El acero al carbono es el material más común para tuberías submarinas debido a su resistencia, durabilidad y rentabilidad. Generalmente se recubre con capas anticorrosión para protegerlo del duro entorno marino.
3.2 Aleaciones resistentes a la corrosión (CRA)
En aquellas áreas donde las tuberías están expuestas a fluidos altamente corrosivos, como gas agrio o agua de mar, se utilizan aleaciones resistentes a la corrosión como acero inoxidable, acero inoxidable dúplex o Inconel. Estos materiales ofrecen una excelente resistencia a la corrosión y una alta resistencia mecánica.
3.3 Sistemas de recubrimiento
Epoxi adherido por fusión (FBE): Los recubrimientos FBE brindan una excelente protección contra la corrosión y se utilizan comúnmente para tuberías submarinas.
Polietileno Tricapa (3LPE): Los recubrimientos 3LPE constan de una imprimación epoxi, un adhesivo polimérico y una capa superior de polietileno, ofreciendo una protección mecánica y una resistencia a la corrosión superiores.
Recubrimiento de peso de hormigón: A menudo se aplican recubrimientos de peso de hormigón para garantizar la estabilidad y proteger la tubería de daños externos, especialmente en áreas con fuertes corrientes o donde la tubería se coloca sobre el lecho marino.
4. Métodos de instalación
4.1 Método S-Lay
El método de tendido en S es una de las técnicas más comunes para instalar tuberías submarinas. La tubería se suelda a una barcaza de tendido y se baja gradualmente hasta el fondo marino en una curva en forma de S. Este método es adecuado para profundidades de agua de poco profundas a medias.
4.2 Método J-Lay
En el método J-lay, la tubería se baja verticalmente al agua y se coloca horizontalmente sobre el fondo marino. Esta técnica es ideal para instalaciones en aguas profundas, ya que reduce la tensión en la tubería durante el proceso de colocación.
4.3 Método de colocación de bobinas
El método de tendido de tuberías en carrete consiste en enrollar la tubería en un carrete grande y luego desenrollarla durante la instalación. Este método rápido y eficiente lo hace adecuado para tuberías cortas o instalaciones en lugares remotos.
4.4 Zanjas y enterramientos
En áreas con alto riesgo ambiental o donde la estabilidad del lecho marino es un problema, la tubería se entierra en una zanja para brindar protección adicional contra fuerzas externas. La excavación de zanjas se puede realizar utilizando arados, herramientas de chorro de agua o zanjadoras mecánicas.
5. Gestión de mantenimiento e integridad
5.1 Técnicas de inspección
Inspección en línea (ILI): Las herramientas ILI, comúnmente conocidas como “smart pigs”, se utilizan para inspeccionar el estado interno de las tuberías submarinas. Estas herramientas pueden detectar corrosión, grietas y otras anomalías que pueden comprometer la integridad de las tuberías.
Inspecciones de ROV y AUV: Los vehículos operados a distancia (ROV) y los vehículos submarinos autónomos (AUV) inspeccionan el estado externo de las tuberías submarinas. Estos vehículos cuentan con cámaras y sensores para monitorear el estado de la tubería e identificar posibles problemas.
5.2 Monitoreo de la corrosión
Protección catódica: Los sistemas de protección catódica evitan la corrosión en la superficie externa de las tuberías submarinas. Estos sistemas utilizan ánodos de sacrificio o corrientes impresas para proteger la tubería del agua de mar corrosiva.
Inhibidores de corrosión: En algunos casos, se inyectan inhibidores de corrosión en la tubería para proteger las superficies internas de los fluidos corrosivos.
5.3 Detección de fugas y respuesta ante emergencias
Monitoreo en tiempo real: Los ductos submarinos cuentan con sistemas de monitoreo en tiempo real que detectan fugas, caídas de presión y otras anomalías. La detección temprana es fundamental para prevenir daños ambientales y garantizar la seguridad del ducto.
Planes de respuesta a emergencias: Existen planes integrales de respuesta a emergencias para abordar posibles fugas o roturas en tuberías submarinas. Estos planes incluyen procedimientos para cerrar la tubería, contener la fuga y mitigar el impacto ambiental.
6. Conclusión: El futuro de los oleoductos submarinos
A medida que la demanda de energía continúa creciendo, no se puede subestimar la importancia de los oleoductos submarinos en la cadena de suministro de energía global. Los avances en materiales, técnicas de instalación y gestión de la integridad están mejorando la confiabilidad y seguridad de estas infraestructuras críticas. Sin embargo, los desafíos actuales, como la corrosión, el impacto ambiental y las instalaciones en aguas más profundas, requieren innovación y mejora continuas.
Al comprender las complejidades de los ductos submarinos y adoptar las mejores prácticas en diseño, construcción y mantenimiento, la industria puede garantizar el transporte seguro y eficiente de recursos desde los yacimientos marinos a los mercados de todo el mundo.
7. Preguntas frecuentes
P1: ¿Cuáles son los principales desafíos en la construcción de ductos submarinos?
Los principales desafíos incluyen factores ambientales como la corrosión, las fuertes corrientes, la estabilidad del lecho marino y desafíos técnicos relacionados con la selección de materiales, los métodos de instalación y el mantenimiento de la integridad de las tuberías a lo largo del tiempo.
P2: ¿Cómo se protegen las tuberías submarinas contra la corrosión?
Las tuberías submarinas están protegidas contra la corrosión mediante el uso de recubrimientos anticorrosión como FBE y 3LPE, sistemas de protección catódica y materiales resistentes a la corrosión en entornos altamente corrosivos.
P3: ¿Cuál es la importancia del monitoreo en tiempo real en ductos submarinos?
El monitoreo en tiempo real es fundamental para detectar fugas, caídas de presión y otras anomalías que podrían comprometer la integridad de las tuberías. La detección temprana permite una respuesta y mitigación rápidas, evitando daños ambientales y garantizando la seguridad de las tuberías.