Pokyny pro žebrované trubky: Zvýšení účinnosti přenosu tepla
Zavedení
A žebrovaná trubka maximalizuje účinnost přenosu tepla mezi dvěma kapalinami ve výměnících tepla. Tyto trubky zlepšují tepelný výkon zvětšením povrchové plochy dostupné pro výměnu tepla. Ať už se používají v elektrárnách, systémech HVAC nebo chemickém zpracování, žebrované trubky výrazně zlepšují účinnost přenosu tepla. Tato příručka se ponoří do podrobností o žebrovaných trubkách, zahrnuje jejich normy a třídy, typy žeber, materiály, specifikace a vhodné rozměry trubek.
Co jsou žebrované trubky?
Žebrované trubky se skládají ze základní trubky s prodlouženými žebry připojenými k její vnější části. Žebra zvětšují povrch a zlepšují rychlost přenosu tepla. Tyto trubky jsou nezbytné v aplikacích vyžadujících účinnou tepelnou výměnu a omezený prostor.
Standardy a stupně
Různé normy a třídy se používají ke kategorizaci žebrovaných trubek na základě jejich materiálu, konstrukce a použití:
EN 10216-2: Bezešvé trubky pro tlakové účely:
P235GH TC1/TC2: Používá se v kotlích a tlakových nádobách.
P265GH TC1/TC2: Nabízí vyšší pevnost pro prostředí s vysokým tlakem.
Normy ASTM:
ASTM A179: Nízkouhlíkové ocelové trubky pro výměníky tepla a kondenzátory.
ASTM A192: Podobné jako A179, ale navrženo pro vyšší tlaky.
ASTM A213: Bezešvé trubky z feritické a austenitické legované oceli, včetně:
TP304/304L: Běžně se používá pro svou odolnost proti korozi a snadné svařování.
TP316/316L: Preferováno v prostředí s vyšším rizikem koroze.
EN 10216-5: Trubky z nerezové oceli:
EN 1.4301 (304): Evropský ekvivalent ASTM TP304, odolný proti korozi.
EN 1.4307 (304L): Nízkouhlíková varianta 1.4301, ideální pro svařování.
EN 1.4401 (316): Nabízí zvýšenou odolnost vůči chloridům.
EN 1.4404 (316L): Nízkouhlíková verze 1.4401, vhodná pro svařování.
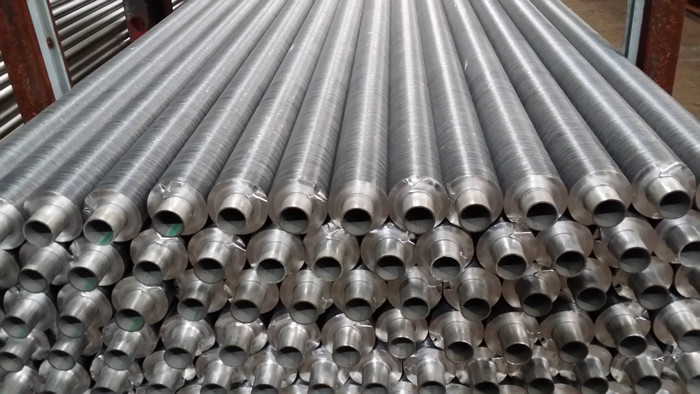
Žebrované trubky
Druhy ploutví
Žebra použitá v žebrovaných trubkách se mohou lišit v závislosti na způsobu připevnění a použití:
Zabudované ploutve: Mechanicky zapuštěné do povrchu trubky, nabízí robustní spojení a vysokou tepelnou účinnost.
Svařované ploutve: Žebra jsou přivařena k trubce, což zajišťuje odolnost a mechanickou pevnost, což je ideální pro drsná prostředí.
Extrudované ploutve: Žebra jsou vytlačena z materiálu trubky, což zajišťuje rovnoměrné vlastnosti přenosu tepla.
Materiály pro ploutve
Materiál žeber se vybírá na základě požadovaného tepelného výkonu a podmínek prostředí:
Hliníkové slitiny:
AA1100: Známý pro svou vynikající tepelnou vodivost a odolnost proti korozi.
AA1080, AA1060, AA1050: Tyto třídy poskytují podobné vlastnosti s malými rozdíly v pevnosti a vodivosti.
Specifikace: Rozměry trubky, výška žebra, tloušťka a hustota
Účinnost žebrovaných trubek závisí na různých faktorech, včetně vnějšího průměru, tloušťky stěny, výšky žebra, tloušťky a počtu žeber na palec nebo metr.
Vnější průměr trubky (OD): Žebrované trubky jsou obvykle dostupné ve vnějších průměrech od 16 mm až 219 mm (přibližně 5/8″ až 8,625″). Tato řada pokrývá většinu standardních aplikací.
Tloušťka stěny trubky: Tloušťka stěny trubek vhodných pro žebrování se obecně pohybuje od 1 mm až 8 mm. Tenčí stěny jsou běžnější v aplikacích, kde je kritická hmotnost a tepelná vodivost. Pro srovnání, silnější stěny se používají pro vysokotlaká prostředí.
Výška ploutve: Obvykle se pohybuje od 6 mm až 30 mm. Vyšší žebra zvětšují povrch, ale mohou vést k výraznějším poklesům tlaku.
Tloušťka ploutve: Rozsah od 0,2 mm až 0,6 mm. Silnější žebra nabízejí lepší odolnost, ale mohou mírně snížit tepelnou účinnost.
Počet ploutví na palec (FPI) nebo na metr (FPM) je obvykle mezi 8 až 16 FPI nebo 250 až 500 FPM. Vyšší hustoty poskytují větší plochu, ale mohou také zvýšit tlakovou ztrátu.
Délka žebrovaných sekcí: Žebrovanou část trubky lze přizpůsobit, se standardními délkami od 1 metr až 12 metrů.
Aplikace a výhody
Žebrované trubky se používají v různých průmyslových odvětvích pro jejich vynikající schopnosti přenosu tepla:
Výroba elektřiny: Používá se v ekonomizérech a kotlích ke zlepšení rekuperace tepla a účinnosti.
HVAC systémy: Vylepšete výkon výměníků tepla, přispíváte k lepší kontrole teploty a úspoře energie.
Chemické zpracování: V reaktorech a kondenzátorech usnadňují efektivní tepelné řízení, optimalizují reakční podmínky a kvalitu produktu.
Často kladené otázky (FAQ)
1. K čemu slouží žebrované trubky?
Žebrované trubky zvětšují povrch výměníků tepla a zlepšují účinnost přenosu tepla mezi kapalinami.
2. Jaké jsou nejběžnější materiály používané na ploutve?
Slitiny hliníku, jako jsou AA1100, AA1080, AA1060 a AA1050, se běžně používají kvůli jejich vynikající tepelné vodivosti a odolnosti proti korozi.
3. Jaké jsou běžné normy pro žebrované trubky?
Žebrované trubky jsou vyráběny podle norem jako EN 10216-2 pro bezešvé trubky a ASTM A179, A192 a A213 pro různé aplikace.
4. Jak výška a hustota ploutví ovlivňují výkon?
Vyšší žebra zvětšují povrchovou plochu pro přenos tepla, zatímco počet žeber na palec nebo metr ovlivňuje celkovou účinnost. Vyšší hustota však může také zvýšit pokles tlaku.
5. Jaké jsou typické aplikace žebrovaných trubek?
Žebrované trubky se běžně používají při výrobě energie, systémech HVAC a chemickém zpracování pro zvýšení účinnosti přenosu tepla.
6. Jaká je typická délka žebrované trubky?
Žebrovaná část trubky se obvykle pohybuje od 1 metru do 12 metrů, v závislosti na aplikaci.
Závěr
Žebrované trubky jsou nezbytné v systémech, kde je rozhodující účinný přenos tepla. Pochopení různých typů žeber, materiálů a specifikací umožňuje inženýrům vybrat nejvhodnější žebrovanou trubku pro jejich aplikaci, což zajišťuje optimální výkon, dlouhou životnost a nákladovou efektivitu.
Při výběru žebrovaných trubek je důležité vzít v úvahu specifické požadavky vašeho systému, jako je provozní teplota, tlak a použité kapaliny. Tímto způsobem lze dosáhnout nejlepší možné tepelné účinnosti a výkonu systému.
Pro řešení na míru a podrobnější informace o žebrovaných trubkách se důrazně doporučuje konzultovat se specializovaným výrobcem nebo dodavatelem. Mohou poskytnout odborné vedení a pomoci vám vybrat perfektní konfiguraci žebrované trubky.