Oil and gas drilling involves complex equipment and techniques to reach reservoirs beneath the earth’s surface. The drill string, casing, and tubing are the most critical components of any drilling operation. Each plays a pivotal role in ensuring a drilling project’s safety, efficiency, and success. Understanding Drilling Guidelines and the best practices for their use is essential for drilling engineers and operators alike.
This guide covers the critical aspects of drill strings, casing, and tubing, providing solutions to common challenges encountered in oil and gas exploration. Whether you’re managing a drilling operation or working in exploration, these Drilling Guidelines will help you navigate the complexities of each component and ensure smooth, efficient drilling processes.
The Drill String: Backbone of the Drilling Operation
A drill string is an assembly that transmits rotary motion from the surface to the drill bit at the bottom of the well. It comprises several interconnected parts, including drill pipes, collars, and tool joints. The drill string is essential for drilling wells, as it not only rotates the drill bit but also facilitates the circulation of drilling fluids.
Critical Components of the Drill String:
- Drill Pipe: A hollow pipe that transmits rotational power and circulates drilling fluid.
- Drill Collars: Heavier, thick-walled pipes that provide weight on the bit, helping it cut through rock.
- Tool Joints: Threaded connections that link segments of drill pipe together.
Common Issues with Drill Strings and Solutions:
- Fatigue and Failure: Due to the immense stress placed on drill strings, fatigue failure is common, especially in deeper wells.
- Solution: To reduce stress concentrations, regularly inspect and rotate drill pipes, use premium connections, and consider higher-grade steel for deeper wells.
- Stuck Pipe: Drill strings can become stuck due to differential sticking, mechanical sticking, or hole collapse.
- Solution: Use appropriate drilling fluid to manage wellbore pressure, monitor torque and drag for signs of sticking, and apply back-off techniques early to free the pipe before a significant issue arises.
- Twisting and Buckling: Drill strings can experience buckling or twisting, leading to tool joint failure.
- Solution: To prevent axial buckling, ensure proper weight distribution using the correct number of drill collars and downhole stabilizers.
The drill string is the most dynamic part of the drilling process, requiring careful planning and ongoing monitoring to ensure safe and effective drilling operations.
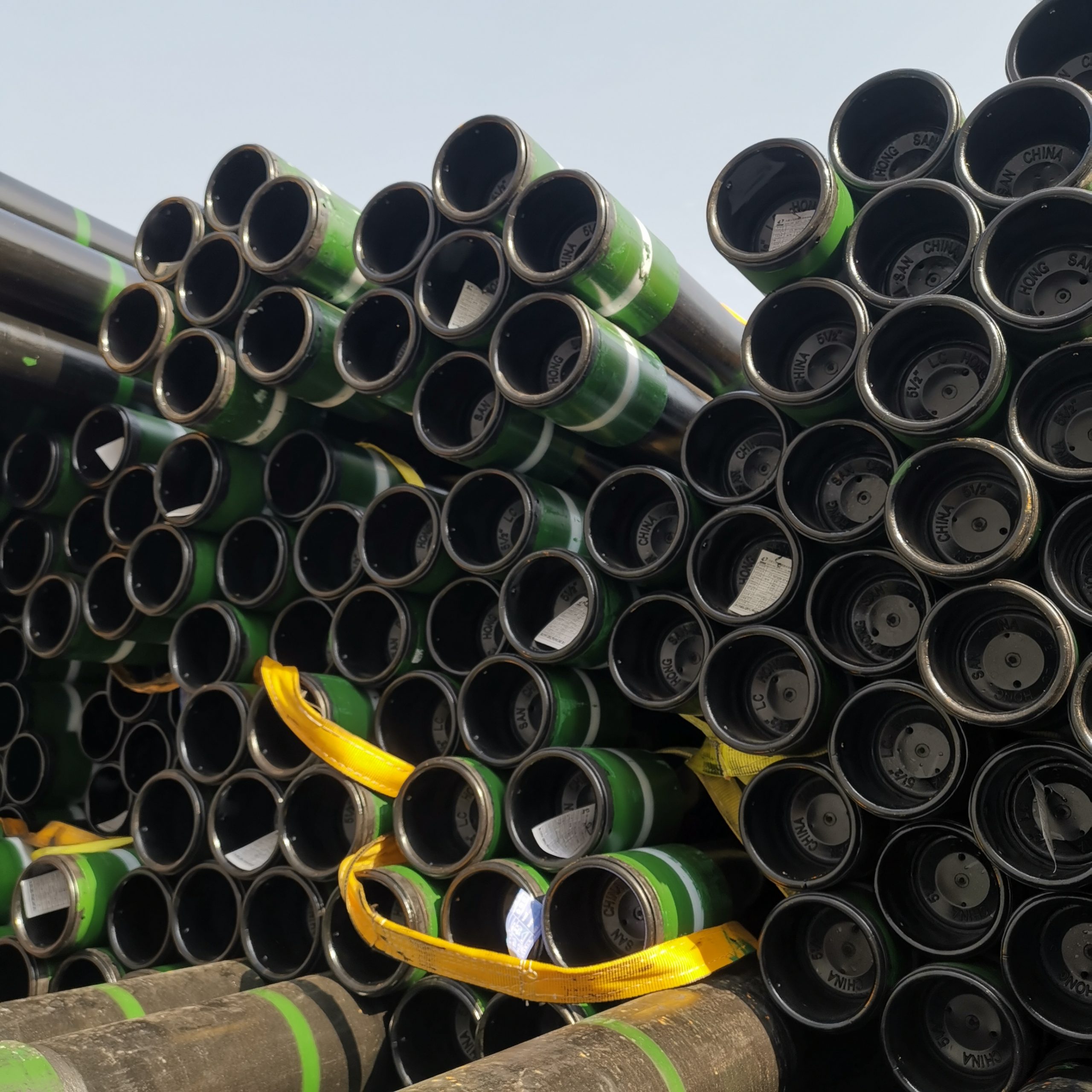
Casing: Protecting the Wellbore and Preventing Collapse
The casing is a large-diameter pipe inserted into a drilled well and cemented to stabilize the wellbore and prevent it from collapsing. The casing also isolates different subsurface formations, prevents fluid migration, and maintains good integrity.
Types of Casing:
- Conductor Casing: This is the first casing string set in the well. It prevents surface formations from caving in and protects shallow groundwater.
- Surface Casing: Installed next, it extends deeper into the well, safeguarding against blowouts and preventing surface contamination.
- Intermediate Casing: This is run between the surface and production casing to prevent the well from encountering problematic zones, such as unstable formations or high-pressure zones.
- Production Casing: The final casing string isolates the producing formation and provides a pathway for hydrocarbons to flow through the well.
Common Issues with Casing and Solutions:
- Wellbore Instability: In high-pressure formations, improper casing design can lead to wellbore collapse or uncontrolled fluid influx.
- Solution: Use a properly designed casing program, considering well depth, pressure conditions, and formation properties to ensure adequate wellbore stabilization.
- Casing Wear: Prolonged drilling operations or excessive side loads can wear down the casing, weakening its structure.
- Solution: Use wear-resistant casing or employ centralizers to keep the casing centered in the wellbore, minimizing sidewall contact.
- Casing Leaks: Poor cementing or casing failure can cause leaks, leading to pressure issues or cross-contamination of formations.
- Solution: Conduct regular pressure tests and cement bond logs to ensure casing integrity and repair any leaks promptly using cement squeezes or other intervention techniques.
The casing is essential for maintaining good integrity, and following best practices can help avoid many costly issues associated with casing failure.
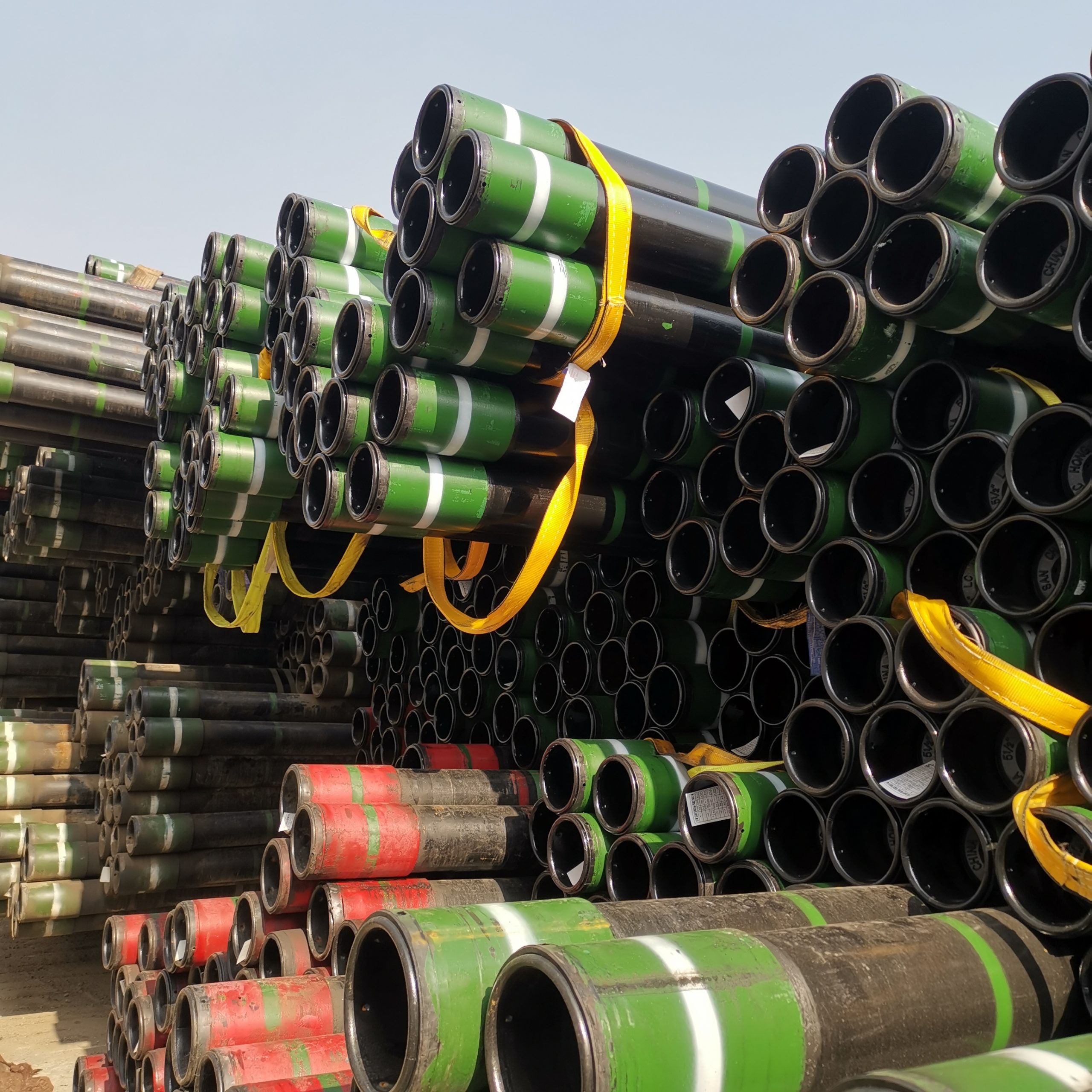
Tubing: The Pathway to Production
Tubing is a smaller-diameter pipe placed inside the casing that transports oil, gas, or other produced fluids from the well to the surface. Tubing is designed to withstand the high pressures and corrosive environments often found in producing wells, making it a critical component for the production phase of a well’s lifecycle.
Critical Considerations for Tubing:
- Tubing Size: The diameter of the tubing must be chosen carefully to maximize production while minimizing pressure drops.
- Corrosion Resistance: Tubing is often exposed to corrosive environments, particularly in wells producing sour gas or those with high CO₂ or H₂S levels. Corrosion-resistant alloys like 13Cr, Super 13Cr, or nickel-based alloys can help extend the tubing’s life.
- Tubing Connections: High-quality threaded connections ensure leak-proof joints and maintain good integrity under pressure.
Common Tubing Issues and Solutions:
- Corrosion and Erosion: Tubing is susceptible to corrosion and erosion due to the harsh fluids and high velocities involved in production.
- Solution: Select corrosion-resistant materials, apply internal coatings or linings, and monitor fluid properties to prevent rapid deterioration of the tubing.
- Tubing Collapse: Excessive external pressure or inadequate wall thickness can cause tubing to collapse, halting production.
- Solution: Perform regular pressure tests to ensure tubing is within operational limits and select tubing with a higher collapse rating for wells with higher downhole pressures.
- Scaling: Mineral scale can build up inside the tubing, reducing flow rates and potentially causing blockages.
- Solution: To minimize scale formation in the wellbore, use chemical inhibitors or mechanical descaling techniques and consider preventative treatments.
Tubing provides the critical path for hydrocarbons to travel to the surface, making it vital to the well’s production performance. Careful material selection and regular maintenance can significantly extend the tubing’s lifespan.
Drilling Guidelines for Optimizing Well Integrity and Efficiency
When drilling a well, the interplay between the drill string, casing, and tubing must be carefully managed to ensure successful and safe drilling operations. Here are some best practices and Drilling Guidelines to keep in mind:
- Plan the Well Design Carefully: Understanding the subsurface conditions, such as pressure, temperature, and formation stability, is critical to selecting the right equipment. Proper, healthy design ensures the appropriate casing sizes and grades are used, preventing unnecessary delays or equipment failure.
- Monitor Well Conditions Constantly: Throughout drilling, it’s crucial to monitor downhole conditions such as torque, drag, and pressure. These metrics can provide early warning signs of problems like stuck pipes or wellbore collapse, allowing corrective actions to be taken before issues escalate.
- Conduct Regular Inspections: Drill strings, casings, and tubing are all subject to wear and tear. Routine inspections—visual and with specialized tools like calipers and ultrasonics—can help identify early signs of fatigue or corrosion, preventing catastrophic failures.
- Optimize Drilling Fluids: Drilling fluids play a significant role in good integrity, as they help manage downhole pressure, cool the drill bit, and transport cuttings to the surface. The suitable fluid properties can prevent wellbore instability, protect casing and tubing from corrosion, and reduce the risk of pipe sticking.
- Choose High-Quality Materials: In high-stress or corrosive environments, the quality of materials used for drill string, casing, and tubing becomes critical. Investing in high-strength steel, corrosion-resistant alloys, and premium connections will pay off by increasing longevity and reducing the need for costly interventions.
Conclusion
In the oil and gas industry, drill string, casing, and tubing are the unsung heroes that ensure the success and safety of drilling operations. Understanding their roles and how to address common issues is critical for healthy integrity and efficient production. By following these Drilling Guidelines and best practices, drilling engineers and operators can optimize their operations, minimize risks, and enhance sound performance.
Whether drilling exploratory wells in remote regions or managing high-production wells offshore, the right approach to selecting and maintaining these essential components will improve both short-term success and long-term profitability.