Oleoduto submarino: uma exploração em profundidade
Introdução
Os oleodutos submarinos transportam petróleo, gás e outros fluidos por vastas distâncias submarinas. Esses oleodutos são essenciais para conectar plataformas offshore de petróleo e gás a instalações onshore, permitindo a transferência eficiente e segura de recursos de locais remotos para o mercado global. No entanto, projetar, construir e manter oleodutos submarinos apresentam desafios únicos devido ao ambiente marinho hostil e dinâmico. Este blog fornece uma visão geral abrangente dos oleodutos submarinos, incluindo suas aplicações, considerações de design, materiais, métodos de instalação e estratégias de manutenção.
1. O papel do gasoduto submarino na indústria energética
1.1 Importância dos Oleodutos Submarinos
Os oleodutos submarinos são as linhas de vida da indústria de petróleo e gás offshore. Eles fornecem uma rota direta e segura para transportar hidrocarbonetos de campos offshore para refinarias e plantas de processamento em terra. Esses oleodutos são essenciais para a cadeia global de fornecimento de energia, particularmente à medida que a demanda por petróleo e gás cresce.
1.2 Principais aplicações
Transporte de Petróleo e Gás: Os oleodutos submarinos são usados principalmente para transportar petróleo bruto, gás natural e condensados de plataformas de produção offshore para instalações terrestres para processamento e distribuição.
Linhas de injeção de água: Em operações de recuperação avançada de petróleo (EOR), oleodutos submarinos injetam água no reservatório para manter a pressão e melhorar as taxas de recuperação de petróleo.
Umbilicais submarinos: Essas tubulações especializadas transportam fluidos de controle, energia elétrica e sinais de comunicação entre equipamentos submarinos e instalações de superfície.
2. Considerações de projeto para oleoduto submarino
2.1 Fatores ambientais e geotécnicos
Ambiente Marinho: Os oleodutos submarinos devem ser projetados para suportar os efeitos corrosivos da água do mar, correntes fortes e impactos potenciais de embarcações ou objetos marinhos. As condições de temperatura e pressão no fundo do mar também influenciam a seleção de materiais e o projeto do oleoduto.
Topografia do fundo do mar: A topografia do leito marinho, incluindo declives, vales e trincheiras, afeta o roteamento e a estabilidade do oleoduto. Levantamentos geotécnicos são essenciais para avaliar as condições do leito marinho e determinar a melhor rota do oleoduto.
Atividade sísmica: Em regiões propensas a terremotos, os oleodutos submarinos devem ser projetados para acomodar o movimento do solo e evitar danos durante eventos sísmicos.
2.2 Integridade e segurança do gasoduto
Seleção de materiais: Os oleodutos submarinos são normalmente construídos em aço carbono de alta resistência, revestidos com materiais anticorrosivos, como epóxi fundido (FBE) ou polietileno de três camadas (3LPE), para proteger contra corrosão e danos mecânicos.
Estabilidade do gasoduto: Estabilidade é uma preocupação crítica, particularmente em áreas com correntes fortes ou terrenos irregulares no fundo do mar. Técnicas como abertura de valas, enterramento ou adição de revestimentos de peso de concreto estabilizam o oleoduto.
Sistemas de detecção de vazamentos: Os oleodutos submarinos são equipados com sistemas avançados de detecção de vazamentos que monitoram pressão, taxas de fluxo e outros parâmetros em tempo real para detectar vazamentos ou anomalias.
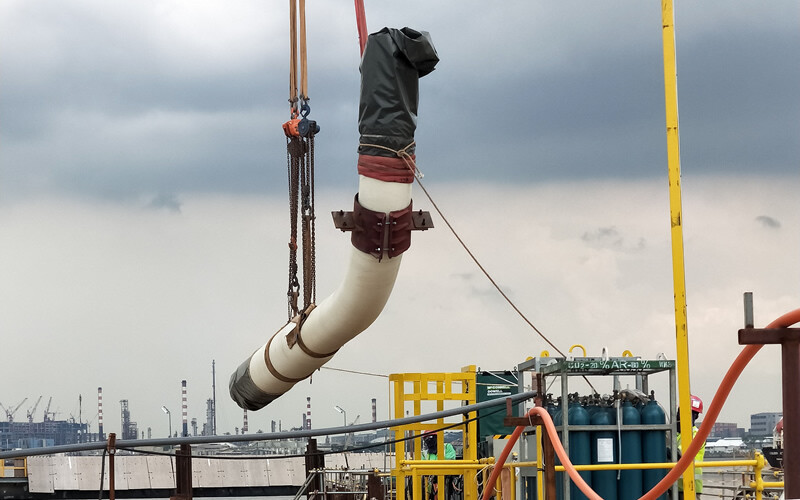
Submarino ou Pipeline Submarino
3. Materiais usados na construção de oleodutos submarinos
3.1 Aço Carbono
Aço carbono é o material mais comum para tubulações submarinas devido à sua resistência, durabilidade e custo-benefício. Ele é tipicamente revestido com camadas anticorrosivas para proteger contra o ambiente marinho severo.
3.2 Ligas resistentes à corrosão (CRAs)
Em áreas onde os oleodutos são expostos a fluidos altamente corrosivos, como gás ácido ou água do mar, ligas resistentes à corrosão, como aço inoxidável, aço inoxidável duplex ou Inconel, são usadas. Esses materiais oferecem excelente resistência à corrosão e alta resistência mecânica.
3.3 Sistemas de revestimento
Epóxi ligado por fusão (FBE): Os revestimentos FBE oferecem excelente proteção contra corrosão e são comumente usados em tubulações submarinas.
Polietileno de três camadas (3LPE): Os revestimentos 3LPE consistem em um primer epóxi, um adesivo de polímero e uma camada superior de polietileno, oferecendo proteção mecânica e resistência à corrosão superiores.
Revestimento de peso de concreto: Revestimentos de peso de concreto são frequentemente aplicados para garantir estabilidade e proteger a tubulação de danos externos, especialmente em áreas com correntes fortes ou onde a tubulação é colocada no fundo do mar.
4. Métodos de instalação
4.1 Método S-Lay
O método S-lay é uma das técnicas mais comuns para instalar tubulações submarinas. A tubulação é soldada em uma barcaça de assentamento e gradualmente abaixada até o fundo do mar em uma curva em forma de S. Este método é adequado para profundidades de água rasas a médias.
4.2 Método J-Lay
No método J-lay, o oleoduto é abaixado verticalmente na água e colocado horizontalmente no leito marinho. Essa técnica é ideal para instalações em águas profundas, pois reduz o estresse no oleoduto durante o processo de assentamento.
4.3 Método Reel-Lay
O método reel-lay envolve enrolar o pipeline em um grande carretel e então desenrolá-lo durante a instalação. Este método rápido e eficiente o torna adequado para pipelines curtos ou instalações em locais remotos.
4.4 Abertura de valas e enterramento
Em áreas com alto risco ambiental ou onde a estabilidade do leito marinho é uma preocupação, o oleoduto é enterrado em uma vala para fornecer proteção adicional contra forças externas. A abertura de valas pode ser realizada usando arados, ferramentas de jato ou valas mecânicas.
5. Gestão de Manutenção e Integridade
5.1 Técnicas de Inspeção
Inspeção em linha (ILI): Ferramentas ILI, comumente conhecidas como “smart pigs”, são usadas para inspecionar a condição interna de oleodutos submarinos. Essas ferramentas podem detectar corrosão, rachaduras e outras anomalias que podem comprometer a integridade do oleoduto.
Inspeções de ROV e AUV: Veículos operados remotamente (ROVs) e veículos subaquáticos autônomos (AUVs) inspecionam a condição externa de oleodutos submarinos. Esses veículos têm câmeras e sensores para monitorar a condição do oleoduto e identificar problemas potenciais.
5.2 Monitoramento de Corrosão
Proteção catódica: Sistemas de proteção catódica previnem corrosão na superfície externa de tubulações submarinas. Esses sistemas usam anodos de sacrifício ou correntes impressas para proteger a tubulação da água do mar corrosiva.
Inibidores de corrosão: Em alguns casos, inibidores de corrosão são injetados na tubulação para proteger as superfícies internas de fluidos corrosivos.
5.3 Detecção de vazamentos e resposta a emergências
Monitoramento em tempo real: Os oleodutos submarinos têm sistemas de monitoramento em tempo real que detectam vazamentos, quedas de pressão e outras anomalias. A detecção precoce é essencial para evitar danos ambientais e garantir a segurança do oleoduto.
Planos de resposta a emergências: Planos abrangentes de resposta a emergências estão em vigor para lidar com potenciais vazamentos ou rupturas em oleodutos submarinos. Esses planos incluem procedimentos para fechar o oleoduto, conter o vazamento e mitigar o impacto ambiental.
6. Conclusão: O Futuro do Oleoduto Submarino
À medida que a demanda por energia continua a crescer, a importância dos oleodutos submarinos na cadeia global de fornecimento de energia não pode ser exagerada. Avanços em materiais, técnicas de instalação e gerenciamento de integridade estão aumentando a confiabilidade e a segurança dessas infraestruturas críticas. No entanto, desafios contínuos, como corrosão, impacto ambiental e instalações em águas mais profundas, exigem inovação e melhoria contínuas.
Ao compreender as complexidades dos oleodutos submarinos e adotar as melhores práticas em projeto, construção e manutenção, o setor pode garantir o transporte seguro e eficiente de recursos de campos offshore para mercados em todo o mundo.
7. Perguntas frequentes
Q1: Quais são os principais desafios na construção de oleodutos submarinos?
Os principais desafios incluem fatores ambientais como corrosão, correntes fortes, estabilidade do fundo do mar e desafios técnicos relacionados à seleção de materiais, métodos de instalação e manutenção da integridade da tubulação ao longo do tempo.
Q2: Como os oleodutos submarinos são protegidos contra corrosão?
Os oleodutos submarinos são protegidos contra corrosão por meio do uso de revestimentos anticorrosivos, como FBE e 3LPE, sistemas de proteção catódica e materiais resistentes à corrosão em ambientes altamente corrosivos.
Q3: Qual é a importância do monitoramento em tempo real em oleodutos submarinos?
O monitoramento em tempo real é crucial para detectar vazamentos, quedas de pressão e outras anomalias que podem comprometer a integridade do oleoduto. A detecção precoce permite resposta e mitigação rápidas, prevenindo danos ambientais e garantindo a segurança do oleoduto.