Evolusi Mikrostruktur Baja P92 pada Temperatur Isotermal yang Berbeda
Baja P92 terutama digunakan dalam boiler ultra-superkritis, pipa bertekanan ultra tinggi, dan peralatan suhu tinggi dan tekanan tinggi lainnya. Baja P92 berada dalam komposisi kimia baja P91 berdasarkan penambahan elemen jejak elemen W dan B, mengurangi kandungan Mo, melalui batas butir yang diperkuat dan dispersi yang diperkuat dalam berbagai cara, untuk meningkatkan kinerja komprehensif baja P92, baja P92 daripada baja P91 memiliki ketahanan yang lebih baik terhadap kinerja oksidasi dan ketahanan korosi. Proses pengerjaan panas sangat penting untuk memproduksi pipa baja P92. Teknologi pemrosesan termal dapat menghilangkan cacat internal yang dihasilkan dalam proses produksi dan membuat kinerja baja memenuhi kebutuhan kondisi kerja. Jenis dan keadaan organisasi dalam proses pengerjaan panas merupakan faktor utama yang memengaruhi kinerja untuk memenuhi standar. Oleh karena itu, makalah ini menganalisis organisasi pipa baja P92 pada berbagai suhu isotermal untuk mengungkap evolusi organisasi pipa baja P92 pada berbagai suhu, yang tidak hanya memberikan dukungan informasi untuk analisis organisasi dan pengendalian kinerja proses pengerjaan panas yang sebenarnya tetapi juga meletakkan dasar eksperimental untuk pengembangan proses pengerjaan panas.
1. Bahan dan Metode Uji
1.1 Bahan Uji
Baja yang diuji adalah pipa baja P92 dalam kondisi pemakaian (1060 ℃ dikeraskan + 760 ℃ ditempa), dan komposisi kimianya ditunjukkan dalam Tabel 1. Spesimen silinder dengan ukuran ϕ4 mm × 10 mm dipotong di bagian tengah pipa yang sudah jadi pada posisi tertentu sepanjang arah panjang, dan pengukur ekspansi pendinginan digunakan untuk mempelajari transformasi jaringan pada suhu yang berbeda.
Tabel 1 Komposisi Kimia Utama Baja P92 Berdasarkan Fraksi Massa (%)
Elemen |
C |
Ya |
M N |
Kr |
Tidak |
Mo |
V |
Al |
B |
Catatan |
W |
Fe |
% |
0.13 |
0.2 |
0.42 |
8.67 |
0.25 |
0.48 |
0.19 |
0.008 |
0.002 |
0.05 |
1.51 |
Keseimbangan |
1.2 Proses Pengujian
Menggunakan meteran ekspansi termal pendinginan L78, pemanasan 0,05 ℃/detik hingga 1050 ℃ selama 15 menit, pendinginan 200 ℃/detik hingga suhu ruangan. Ukur titik kritis perubahan fase material Ac1 adalah 792,4℃, Ac3 adalah 879,8℃, Ms adalah 372,3℃. Spesimen dipanaskan hingga 1050 °C pada laju 10 °C/detik dan ditahan selama 15 menit, lalu didinginkan hingga suhu yang berbeda (770, 740, 710, 680, 650, 620, 520, 430, 400, 370, 340, 310, 280, 250, 190, dan 160 °C) pada laju 150 °C/detik dan ditahan selama periode waktu yang berbeda (620 °C dan di bawahnya selama 1 jam, 620 °C dan di atasnya selama 25 jam). 620 ℃ dan di atasnya ditahan selama 25 jam), ujung daya isotermal dimatikan sehingga spesimen didinginkan dengan udara hingga suhu ruangan.1.3 Metode pengujian
Setelah permukaan spesimen digiling dan dipoles dengan berbagai proses, permukaan spesimen dikorosi menggunakan aqua regia. Mikroskop AXIOVERT 25 Zeiss dan mikroskop elektron pemindai lingkungan QWANTA 450 digunakan untuk mengamati dan menganalisis susunannya; menggunakan alat uji kekerasan Vickers HVS-50 (beban 1 kg), pengukuran kekerasan dilakukan di beberapa lokasi pada permukaan setiap spesimen dan nilai rata-rata diambil sebagai nilai kekerasan spesimen.
2. Hasil Uji dan Analisis
2.1 Organisasi dan Analisis Suhu Isotermal yang Berbeda
Gambar 1 menunjukkan struktur mikro baja P92 setelah austenitisasi lengkap pada 1050 °C untuk waktu yang berbeda pada suhu yang berbeda. Gambar 1(a) menunjukkan struktur mikro baja P92 setelah isotermalisasi pada 190℃ selama 1 jam. Dari Gambar 1(a2), dapat dilihat bahwa organisasi suhu ruangannya adalah martensit (M). Dari Gambar 1(a3), dapat dilihat bahwa martensit menunjukkan karakteristik seperti bilah. Karena titik Ms baja sekitar 372 °C, transformasi fase martensit terjadi pada suhu isotermal di bawah titik Ms, membentuk martensit, dan kandungan karbon baja P92 termasuk dalam kisaran komposisi karbon rendah; morfologi seperti bilah mencirikan martensit.
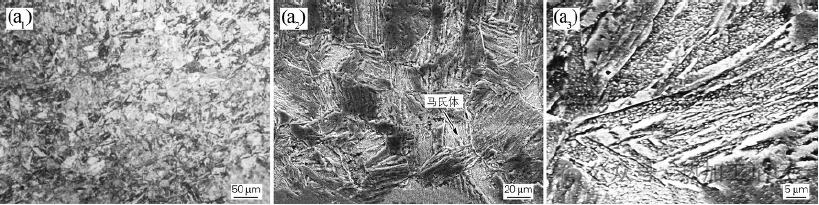
Gambar 1(a) menunjukkan struktur mikro baja P92 setelah 1 jam isotermal pada suhu 190°C
Gambar 1(b) untuk struktur mikro baja P92 pada suhu 430 ℃ isotermal 1 jam. Saat suhu isotermal meningkat hingga 430°C, baja P92 mencapai zona transformasi bainit. Karena baja mengandung unsur Mo, B, dan W, unsur-unsur ini memiliki sedikit pengaruh pada transformasi bainit sambil menunda transformasi perlit. Oleh karena itu, baja P92 pada suhu 430 ℃ isolasi 1 jam, organisasi sejumlah bainit tertentu. Kemudian austenit superdingin yang tersisa diubah menjadi martensit saat didinginkan dengan udara.
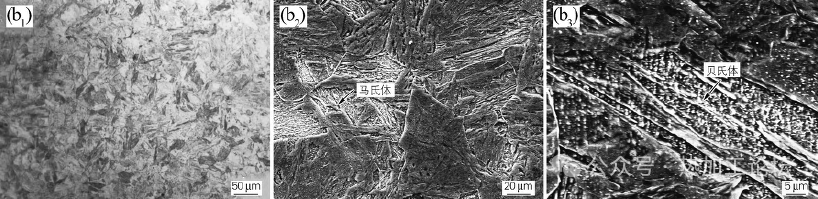
Gambar 1(b) untuk struktur mikro baja P92 pada suhu isotermal 430 ℃ 1 jam
Gambar 1(c) menunjukkan struktur mikro baja P92 pada suhu isotermal 520 ℃ selama 1 jam. Ketika suhu isotermal 520 ℃, elemen paduan Cr, Mo, Mn, dll., sehingga transformasi perlit terhambat, permulaan titik transformasi bainit (titik Bs) berkurang, sehingga dalam kisaran suhu tertentu akan muncul di zona stabilisasi austenit superdingin. Gambar 1(c) dapat dilihat pada isolasi 520 ℃ selama 1 jam setelah austenit superdingin tidak terjadi setelah transformasi, diikuti oleh pendinginan udara untuk membentuk martensit; organisasi suhu ruangan terakhir adalah martensit.
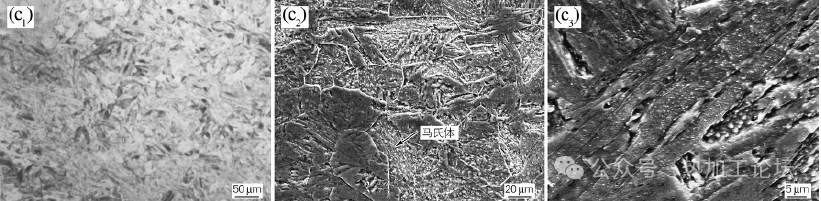
Gambar 1(c) menunjukkan struktur mikro baja P92 pada suhu isotermal 520 ℃ 1 jam
Gambar 1 (d) untuk baja P92 pada mikrostruktur isotermal 25 jam 650 ℃ untuk martensit + perlit. Seperti yang ditunjukkan pada Gambar 1(d3), perlit menunjukkan karakteristik lamelar terputus-putus, dan karbida pada permukaan menunjukkan presipitasi batang pendek. Hal ini disebabkan oleh unsur paduan baja P92 Cr, Mo, V, dll. untuk meningkatkan stabilitas austenit superdingin pada saat yang sama sehingga morfologi perlit baja P92 berubah, yaitu, karbida dalam badan perlit karbida untuk batang pendek, badan perlit ini dikenal sebagai perlit kelas. Pada saat yang sama, banyak partikel fase kedua halus ditemukan dalam organisasi.
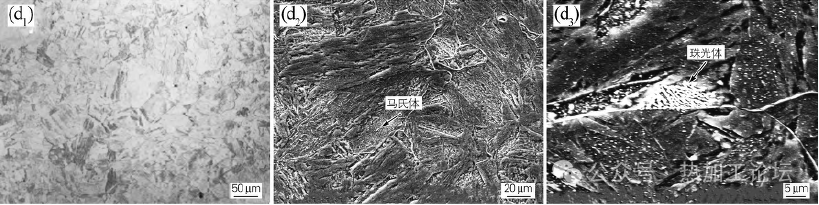
Gambar 1 (d) untuk baja P92 pada 650 ℃ isotermal 25 jam mikrostruktur untuk martensit + perlit
Gambar 1(e) menunjukkan struktur mikro baja P92 pada suhu isotermal 740 ℃ selama 25 jam. Pada suhu isotermal 740 °C, pertama-tama akan terjadi presipitasi ferit masif eutektik dan kemudian dekomposisi eutektik austenit, yang menghasilkan organisasi seperti perlit. Dibandingkan dengan suhu isotermal 650 °C (lihat Gambar 1(d3)), organisasi perlit menjadi lebih kasar saat suhu isotermal dinaikkan, dan karakter dua fase perlit, yaitu ferit dan karburit dalam bentuk batang pendek, terlihat jelas.
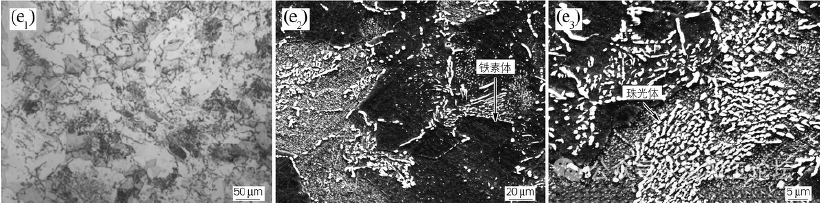
Gambar 1(e) menunjukkan struktur mikro baja P92 pada suhu isotermal 740 ℃ 25 jam
Gambar 1(f) menunjukkan struktur mikro baja P92 pada suhu isotermal 770°C selama 25 jam. Pada suhu isotermal 770°C, dengan perpanjangan waktu isotermal, presipitasi ferit terjadi terlebih dahulu, kemudian austenit superdingin mengalami dekomposisi eutektik untuk membentuk organisasi ferit + perlit. Dengan peningkatan suhu isotermal, kandungan ferit eutektik pertama meningkat, dan kandungan perlit menurun. Karena elemen paduan baja P92, elemen paduan terlarut ke dalam austenit untuk membuat pengerasan austenit meningkat, kesulitan dekomposisi eutektik menjadi lebih luas, sehingga harus ada waktu isotermal yang cukup lama untuk membuat dekomposisi eutektiknya, pembentukan organisasi perlit.
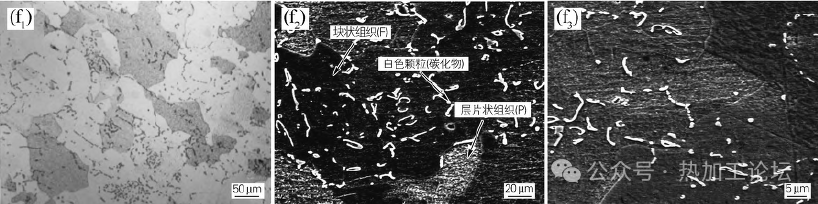
Gambar 1(f) menunjukkan struktur mikro baja P92 pada suhu isotermal 770°C selama 25 jam.
Analisis spektrum energi dilakukan pada jaringan dengan morfologi yang berbeda pada Gambar 1(f2) untuk mengidentifikasi jenis jaringan lebih lanjut, seperti yang ditunjukkan pada Tabel 2. Dari Tabel 2, dapat dilihat bahwa kandungan karbon dari partikel putih lebih tinggi daripada organisasi lain, dan elemen paduan Cr, Mo, dan V lebih banyak, menganalisis partikel ini untuk partikel karbida komposit yang diendapkan selama proses pendinginan; secara komparatif, kandungan karbon dalam organisasi lamelar terputus-putus adalah yang terendah kedua, dan kandungan karbon dalam organisasi masif adalah yang paling sedikit. Karena perlit adalah organisasi dua fase karburisasi dan ferit, kandungan karbon rata-rata lebih tinggi daripada ferit; dikombinasikan dengan analisis suhu dan morfologi isotermal, lebih lanjut ditentukan bahwa organisasi lamelar seperti perlit, dan organisasi masif pertama-tama adalah ferit eutektik.
Analisis Spektrum Baja P92, Diperlakukan Secara Isotermal Pada Suhu 770 °C Selama 25 Jam, Ditulis Dalam Format Tabel Dengan Fraksi Atom (%)
Struktur |
C |
Catatan |
Mo |
Ti |
V |
Kr |
M N |
Fe |
W |
Butiran Putih |
11.07 |
0.04 |
0.94 |
0.02 |
2.16 |
8.36 |
2.64 |
54.77 |
2.84 |
Struktur Blok |
9.31 |
0.04 |
0.95 |
0.2 |
0.32 |
8.42 |
0.74 |
85.51 |
10.21 |
Struktur Berlapis |
5.1 |
0 |
0.09 |
0.1 |
0.33 |
7.3 |
0.35 |
85.65 |
0.69 |
2.2 Mikrokekerasan dan Analisis
Secara umum, selama proses pendinginan baja paduan yang mengandung unsur-unsur seperti W dan Mo, tiga jenis transformasi organisasi terjadi dalam austenit superdingin: transformasi martensit di zona suhu rendah, transformasi bainit di zona suhu sedang, dan transformasi perlit di zona suhu tinggi. Evolusi organisasi yang berbeda mengarah pada kekerasan yang berbeda. Gambar 2 menunjukkan variasi kurva kekerasan baja P92 pada suhu isotermal yang berbeda. Dari Gambar 2, dapat dilihat bahwa dengan peningkatan suhu isotermal, kekerasan menunjukkan tren menurun terlebih dahulu, kemudian meningkat, dan akhirnya menurun. Ketika suhu isotermal 160 ~ 370 ℃, terjadinya transformasi martensit, kekerasan Vickers dari 516HV menjadi 457HV. Ketika suhu isotermal 400 ~ 620 ℃, sejumlah kecil transformasi bainit terjadi, dan kekerasan 478HV meningkat menjadi 484HV; karena transformasi bainit kecil, kekerasan tidak banyak berubah. Ketika suhu isotermal 650 ℃, sejumlah kecil perlit terbentuk, dengan kekerasan 410HV. ketika suhu isotermal 680 ~ 770 ℃, pembentukan organisasi ferit + perlit, kekerasan dari 242HV menjadi 163HV. karena transformasi baja P92 pada suhu yang berbeda dalam organisasi transisi berbeda, di wilayah transformasi martensit suhu rendah, ketika suhu isotermal lebih rendah dari titik Ms, dengan peningkatan suhu, kandungan martensit berkurang, kekerasan berkurang; di tengah transformasi baja P92 dalam suhu yang berbeda, ketika suhu isotermal lebih rendah dari titik Ms, dengan peningkatan suhu, kandungan martensit menurun, kekerasan menurun; di wilayah transformasi bainit suhu sedang, karena jumlah transformasi bainit kecil, kekerasan tidak banyak berubah; di wilayah transformasi perlitik suhu tinggi, dengan kenaikan suhu isotermal, kandungan ferit eutektik pertama meningkat sehingga kekerasan terus menurun, jadi dengan peningkatan suhu isotermal, kekerasan material umumnya merupakan tren menurun, dan tren perubahan kekerasan dan analisis organisasi sejalan dengan tren.
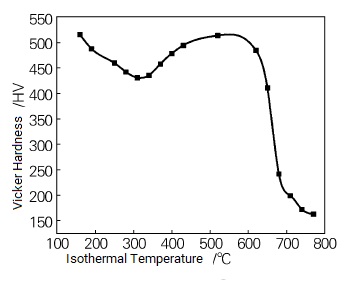
Variasi Kurva Kekerasan Baja P92 Pada Temperatur Isotermal Yang Berbeda
3. Kesimpulan
1) Titik kritis Ac1 baja P92 adalah 792,4 ℃, Ac3 adalah 879,8 ℃, dan Ms adalah 372,3 ℃.
2) Baja P92 pada temperatur isotermal yang berbeda memperoleh organisasi temperatur ruangan yang berbeda; pada 1h isotermal 160 ~ 370 ℃, organisasi temperatur ruangan adalah martensit; pada 1h isotermal 400 ~ 430 ℃, organisasi sejumlah kecil bainit + martensit; pada 1h isotermal 520 ~ 620 ℃, organisasi relatif stabil, dalam waktu singkat (1 jam) tidak terjadi transformasi, organisasi temperatur ruangan adalah martensit; pada 25h isotermal 650 ℃, organisasi temperatur ruangan adalah perlit. h, organisasi temperatur ruangan untuk perlit + martensit; pada 25h isotermal 680 ~ 770 ℃, organisasi diubah menjadi perlit + ferit eutektik pertama.
3) Austenitisasi baja P92 pada Ac1 di bawah isotermal, dengan pengurangan suhu isotermal, kekerasan material secara keseluruhan cenderung meningkat, isotermal pada 770 ℃ setelah terjadinya presipitasi ferit eutektik pertama, transformasi perlitik, kekerasannya paling rendah, sekitar 163HV; isotermal pada 160 ℃ setelah terjadinya transformasi martensit, kekerasannya paling tinggi, sekitar 516HV.