Pedoman untuk Tabung Bersirip: Meningkatkan Efisiensi Perpindahan Panas
Perkenalan
A tabung bersirip memaksimalkan efisiensi perpindahan panas antara dua fluida dalam penukar panas. Tabung ini meningkatkan kinerja termal dengan meningkatkan luas permukaan yang tersedia untuk pertukaran panas. Baik digunakan dalam pembangkit listrik, sistem HVAC, atau pemrosesan kimia, tabung bersirip meningkatkan efisiensi perpindahan panas secara signifikan. Panduan ini akan membahas secara rinci tentang tabung bersirip, yang mencakup standar dan mutunya, jenis sirip, bahan, spesifikasi, dan dimensi tabung yang sesuai.
Apa itu Tabung Bersirip?
Tabung bersirip terdiri dari tabung dasar dengan sirip yang diperpanjang yang terpasang di bagian luarnya. Sirip tersebut memperluas luas permukaan, sehingga meningkatkan laju perpindahan panas. Tabung ini penting dalam aplikasi yang membutuhkan pertukaran termal yang efisien dan ruang yang terbatas.
Standar dan Nilai
Berbagai standar dan tingkatan digunakan untuk mengkategorikan tabung bersirip berdasarkan bahan, konstruksi, dan aplikasinya:
ID 10216-2: Tabung tanpa sambungan untuk tujuan tekanan:
P235GH TC1/TC2: Digunakan dalam boiler dan bejana tekan.
P265GH TC1/TC2: Menawarkan kekuatan yang lebih tinggi untuk lingkungan bertekanan tinggi.
Standar ASTM:
ASTM A179: Tabung baja karbon rendah untuk penukar panas dan kondensor.
ASTM A192: Mirip dengan A179 tetapi dirancang untuk tekanan yang lebih tinggi.
ASTM A213: Tabung baja paduan feritik dan austenitik tanpa sambungan, meliputi:
TP304/304L:Umumnya digunakan karena ketahanannya terhadap korosi dan kemudahan pengelasan.
TP316/316L: Lebih disukai di lingkungan dengan risiko korosi yang tinggi.
ID 10216-5: Tabung baja tahan karat:
ID 1.4301 (304): Setara Eropa dengan ASTM TP304, tahan korosi.
ID 1.4307 (304L): Varian rendah karbon dari 1,4301, ideal untuk pengelasan.
ID 1.4401 (316): Memberikan ketahanan yang lebih baik terhadap klorida.
ID 1.4404 (316L): Versi rendah karbon 1.4401, cocok untuk pengelasan.
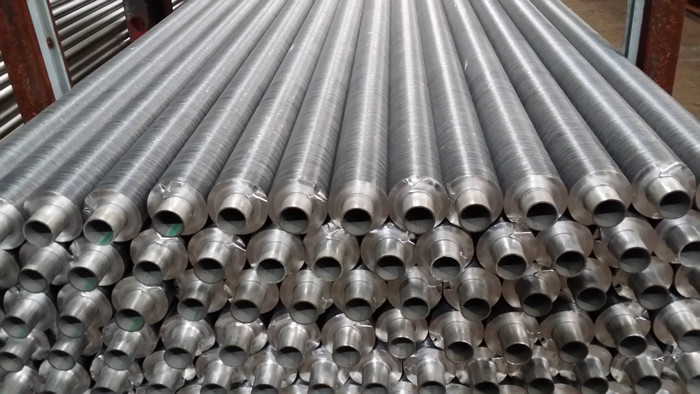
Tabung bersirip
Jenis-jenis Sirip
Sirip yang digunakan dalam tabung bersirip dapat bervariasi berdasarkan metode pemasangan dan aplikasinya:
Sirip Tertanam: Tertanam secara mekanis ke permukaan tabung, menawarkan ikatan yang kuat dan efisiensi termal yang tinggi.
Sirip Las: Sirip dilas ke tabung, memberikan daya tahan dan kekuatan mekanis, yang ideal untuk lingkungan yang keras.
Sirip yang diekstrusi: Sirip diekstrusi dari bahan tabung, memastikan sifat perpindahan panas yang seragam.
Bahan untuk Sirip
Bahan sirip dipilih berdasarkan kinerja termal dan kondisi lingkungan yang diinginkan:
Paduan Aluminium:
AA1100: Dikenal karena konduktivitas termal dan ketahanan korosi yang sangat baik.
AA1080, AA1060, AA1050:Kelas-kelas ini memberikan sifat yang serupa dengan sedikit perbedaan dalam kekuatan dan konduktivitas.
Spesifikasi: Dimensi Tabung, Tinggi Sirip, Ketebalan, dan Kepadatan
Efisiensi tabung bersirip bergantung pada berbagai faktor, termasuk diameter luar, ketebalan dinding, tinggi sirip, ketebalan, dan jumlah sirip per inci atau meter.
Diameter Luar Tabung (OD):Tabung bersirip biasanya tersedia dalam diameter luar mulai dari 16 mm hingga 219 mm (sekitar 5/8″ hingga 8.625″)Rentang ini mencakup sebagian besar aplikasi standar.
Ketebalan Dinding Tabung:Ketebalan dinding tabung yang cocok untuk sirip umumnya berkisar antara 1mm sampai 8mmDinding yang lebih tipis lebih umum digunakan dalam aplikasi yang sangat mementingkan berat dan konduktivitas termal. Sebagai perbandingan, dinding yang lebih tebal digunakan untuk lingkungan bertekanan tinggi.
Tinggi Sirip:Biasanya berkisar dari 6mm sampai 30mmSirip yang lebih tinggi meningkatkan luas permukaan tetapi dapat mengakibatkan penurunan tekanan yang lebih signifikan.
Ketebalan Sirip:Berkisar dari 0,2mm hingga 0,6mmSirip yang lebih tebal menawarkan daya tahan yang lebih baik tetapi mungkin sedikit mengurangi efisiensi termal.
Jumlah Sirip per Inci (FPI) atau per Meter (FPM) biasanya di antara 8 hingga 16 FPI atau 250 hingga 500 FPMKepadatan yang lebih tinggi memberikan lebih banyak luas permukaan tetapi juga dapat meningkatkan penurunan tekanan.
Panjang Bagian Bersirip:Bagian tabung bersirip dapat disesuaikan, dengan panjang standar berkisar dari 1 meter sampai 12 meter.
Aplikasi dan Manfaat
Tabung bersirip digunakan dalam berbagai industri karena kemampuan perpindahan panasnya yang unggul:
Pembangkit listrik: Digunakan dalam ekonomizer dan boiler untuk meningkatkan pemulihan panas dan efisiensi.
Sistem HVAC: Meningkatkan kinerja penukar panas, berkontribusi pada kontrol suhu yang lebih baik dan penghematan energi.
Pengolahan Kimia: Dalam reaktor dan kondensor, mereka memfasilitasi manajemen termal yang efisien, mengoptimalkan kondisi reaksi dan kualitas produk.
Pertanyaan yang Sering Diajukan (FAQ)
1. Apa tujuan dari tabung bersirip?
Tabung bersirip meningkatkan luas permukaan penukar panas, meningkatkan efisiensi perpindahan panas antara cairan.
2. Apa bahan yang paling umum digunakan untuk sirip?
Paduan aluminium, seperti AA1100, AA1080, AA1060, dan AA1050, umum digunakan karena konduktivitas termal dan ketahanan korosinya yang sangat baik.
3. Apa standar umum untuk tabung bersirip?
Tabung bersirip diproduksi menurut standar seperti EN 10216-2 untuk tabung tanpa sambungan dan ASTM A179, A192, dan A213 untuk berbagai aplikasi.
4. Bagaimana tinggi dan kepadatan sirip memengaruhi kinerja?
Sirip yang lebih tinggi meningkatkan luas permukaan untuk perpindahan panas, sementara jumlah sirip per inci atau meter memengaruhi efisiensi keseluruhan. Namun, kepadatan yang lebih tinggi juga dapat meningkatkan penurunan tekanan.
5. Apa saja aplikasi umum dari tabung bersirip?
Tabung bersirip umumnya digunakan dalam pembangkit listrik, sistem HVAC, dan pemrosesan kimia untuk meningkatkan efisiensi perpindahan panas.
6. Berapa panjang tipikal tabung bersirip?
Bagian tabung yang bersirip biasanya berkisar antara 1 meter hingga 12 meter, tergantung pada aplikasinya.
Kesimpulan
Tabung bersirip sangat penting dalam sistem yang membutuhkan perpindahan panas yang efektif. Memahami berbagai jenis sirip, bahan, dan spesifikasi memungkinkan teknisi untuk memilih tabung bersirip yang paling sesuai untuk aplikasi mereka, memastikan kinerja, keawetan, dan efisiensi biaya yang optimal.
Saat memilih pipa bersirip, penting untuk mempertimbangkan persyaratan khusus sistem Anda, seperti suhu pengoperasian, tekanan, dan cairan yang digunakan. Dengan demikian, efisiensi termal dan kinerja sistem dapat tercapai sebaik mungkin.
Konsultasi dengan produsen atau pemasok khusus sangat disarankan untuk mendapatkan solusi yang disesuaikan dan informasi yang lebih rinci tentang tabung bersirip. Mereka dapat memberikan panduan ahli dan membantu Anda memilih konfigurasi tabung bersirip yang sempurna.