Introduction
Dans les secteurs tels que la production d'énergie, le pétrole et le gaz, la pétrochimie et les raffineries, les tubes sans soudure sont des composants essentiels, en particulier dans les équipements qui doivent résister à des températures extrêmes, à des pressions élevées et à des environnements corrosifs et difficiles. Les chaudières, les échangeurs de chaleur, les condenseurs, les surchauffeurs, les préchauffeurs d'air et les économiseurs utilisent ces tubes. Chacune de ces applications exige des propriétés matérielles spécifiques pour garantir les performances, la sécurité et la longévité. Le choix des tubes sans soudure pour la chaudière et l'échangeur de chaleur dépend de la température, de la pression, de la résistance à la corrosion et de la résistance mécanique spécifiques.
Ce guide propose un aperçu détaillé des différents matériaux utilisés pour les tubes sans soudure, notamment l'acier au carbone, l'acier allié, l'acier inoxydable, les alliages de titane, les alliages à base de nickel, les alliages de cuivre et les alliages de zirconium. Nous explorerons également les normes et les grades pertinents, vous aidant ainsi à prendre des décisions plus éclairées pour vos projets de chaudières et d'échangeurs de chaleur.
Aperçu des alliages CS, AS, SS, nickel, titane et zirconium, cuivre et alliages de cuivre
1. Propriétés de résistance à la corrosion
Chaque matériau utilisé pour les tubes sans soudure possède des propriétés de résistance à la corrosion spécifiques qui déterminent son adéquation à différents environnements.
Acier Carbone: Résistance limitée à la corrosion, généralement utilisé avec des revêtements ou des doublures de protection. Sujet à la rouille en présence d'eau et d'oxygène à moins d'être traité.
Acier allié : Résistance modérée à l'oxydation et à la corrosion. Les ajouts d'alliages tels que le chrome et le molybdène améliorent la résistance à la corrosion à haute température.
Acier inoxydable: Excellente résistance à la corrosion générale, à la fissuration par corrosion sous contrainte et aux piqûres grâce à sa teneur en chrome. Les nuances supérieures, telles que le 316L, présentent une meilleure résistance à la corrosion induite par les chlorures.
Alliages à base de nickel : Résistance exceptionnelle aux environnements agressifs tels que les environnements acides, alcalins et riches en chlorures. Les applications hautement corrosives utilisent des alliages tels que l'Inconel 625, l'Hastelloy C276 et l'alliage 825.
Titane et Zirconium : Résistance supérieure aux saumures d'eau de mer et autres milieux hautement corrosifs. Le titane est particulièrement résistant aux environnements chlorés et acides, tandis que les alliages de zirconium excellent dans les conditions très acides.
Cuivre et alliages de cuivre : Excellente résistance à la corrosion en eau douce et en eau de mer, les alliages cuivre-nickel présentant une résistance exceptionnelle en milieu marin.
2. Propriétés physiques et thermiques
Acier Carbone:
Densité : 7,85 g/cm³
Point de fusion : 1 425-1 500 °C
Conductivité thermique : ~50 W/m·K
Acier allié :
Densité : varie légèrement selon les éléments d'alliage, généralement autour de 7,85 g/cm³
Point de fusion : 1 450-1 530 °C
Conductivité thermique : inférieure à celle de l'acier au carbone en raison des éléments d'alliage.
Acier inoxydable:
Densité : 7,75-8,0 g/cm³
Point de fusion : environ 1 400 à 1 530 °C
Conductivité thermique : ~16 W/m·K (inférieure à celle de l'acier au carbone).
Alliages à base de nickel :
Densité : 8,4-8,9 g/cm³ (selon l'alliage)
Point de fusion : 1 300-1 400 °C
Conductivité thermique : généralement faible, environ 10-16 W/m·K.
Titane:
Densité : 4,51 g/cm³
Point de fusion : 1 668 °C
Conductivité thermique : ~22 W/m·K (relativement faible).
Cuivre:
Densité : 8,94 g/cm³
Point de fusion : 1 084 °C
Conductivité thermique : ~390 W/m·K (excellente conductivité thermique).
3. Composition chimique
Acier Carbone: Principalement du fer avec 0,3%-1,2% de carbone et de petites quantités de manganèse, de silicium et de soufre.
Acier allié : Comprend des éléments comme le chrome, le molybdène, le vanadium et le tungstène pour améliorer la résistance et la résistance à la température.
Acier inoxydable: Contient généralement 10,5%-30% de chrome, ainsi que du nickel, du molybdène et d'autres éléments selon la qualité.
Alliages à base de nickel : Principalement du nickel (40%-70%) avec du chrome, du molybdène et d’autres éléments d’alliage pour améliorer la résistance à la corrosion.
Titane: Les grades 1 et 2 sont du titane commercialement pur, tandis que le grade 5 (Ti-6Al-4V) comprend de l'aluminium 6% et du vanadium 4%.
Alliages de cuivre : Les alliages de cuivre contiennent divers éléments comme le nickel (10%-30%) pour la résistance à la corrosion (par exemple, Cu-Ni 90/10).
4. Propriétés mécaniques
Acier Carbone: Résistance à la traction : 400-500 MPa, limite d'élasticité : 250-350 MPa, allongement : 15%-25%
Acier allié : Résistance à la traction : 500-900 MPa, limite d'élasticité : 300-700 MPa, allongement : 10%-25%
Acier inoxydable: Résistance à la traction : 485-690 MPa (304/316), limite d'élasticité : 170-300 MPa, allongement : 35%-40%
Alliages à base de nickel : Résistance à la traction : 550-1 000 MPa (Inconel 625), limite d'élasticité : 300-600 MPa, allongement : 25%-50%
Titane: Résistance à la traction : 240-900 MPa (varie selon la nuance), limite d'élasticité : 170-880 MPa, allongement : 15%-30%
Alliages de cuivre : Résistance à la traction : 200-500 MPa (selon l'alliage), limite d'élasticité : 100-300 MPa, allongement : 20%-35%
5. Traitement thermique (état de livraison)
Acier au carbone et allié : Livré à l'état recuit ou normalisé. Les traitements thermiques comprennent la trempe et le revenu pour améliorer la résistance et la ténacité.
Acier inoxydable: Livré à l'état recuit pour éliminer les contraintes internes et améliorer la ductilité.
Alliages à base de nickel : Recuit en solution pour optimiser les propriétés mécaniques et la résistance à la corrosion.
Titane et Zirconium : Généralement livré dans un état recuit pour maximiser la ductilité et la ténacité.
Alliages de cuivre : Livré à l'état recuit doux, spécialement pour les applications de formage.
6. Formation
Acier au carbone et allié : Ils peuvent être formés à chaud ou à froid, mais les aciers alliés nécessitent plus d'efforts en raison de leur résistance supérieure.
Acier inoxydable: Le formage à froid est courant, bien que les taux d'écrouissage soient plus élevés que ceux de l'acier au carbone.
Alliages à base de nickel : Plus difficile à former en raison de la résistance élevée et des taux d'écrouissage ; nécessite souvent un travail à chaud.
Titane: Le formage est mieux réalisé à des températures élevées en raison de sa grande résistance à température ambiante.
Alliages de cuivre : Facile à former grâce à une bonne ductilité.
7. Soudure
Acier au carbone et allié : Généralement facile à souder en utilisant des techniques conventionnelles, mais un préchauffage et un traitement thermique après soudage (PWHT) peuvent être nécessaires.
Acier inoxydable: Les méthodes de soudage les plus courantes sont le soudage TIG, le soudage MIG et le soudage à l'arc. Un contrôle minutieux de l'apport de chaleur est nécessaire pour éviter toute sensibilisation.
Alliages à base de nickel : Soudure difficile en raison de la forte dilatation thermique et de la susceptibilité aux fissures.
Titane: Soudé dans un environnement protégé (gaz inerte) pour éviter toute contamination. Des précautions sont nécessaires en raison de la réactivité du titane à haute température.
Alliages de cuivre : Facile à souder, en particulier les alliages cuivre-nickel, mais un préchauffage peut être nécessaire pour éviter les fissures.
8. Corrosion des soudures
Acier inoxydable: Peut souffrir d'une corrosion localisée (par exemple, piqûres, corrosion caverneuse) au niveau de la zone affectée par la chaleur de la soudure si elle n'est pas correctement contrôlée.
Alliages à base de nickel : Sensible à la fissuration par corrosion sous contrainte s'il est exposé aux chlorures à haute température.
Titane: Les soudures doivent être correctement protégées de l’oxygène pour éviter toute fragilisation.
9. Détartrage, décapage et nettoyage
Acier au carbone et allié : Le décapage permet d'éliminer les oxydes de surface après le traitement thermique. Les acides les plus courants sont les acides chlorhydrique et sulfurique.
Acier inoxydable et alliages de nickel : Le décapage à l'acide nitrique/fluorhydrique est utilisé pour éliminer la teinte thermique et restaurer la résistance à la corrosion après le soudage.
Titane: Des solutions de décapage acides douces sont utilisées pour nettoyer la surface et éliminer les oxydes sans endommager le métal.
Alliages de cuivre : Le nettoyage acide est utilisé pour éliminer les ternissures et les oxydes de surface.
10. Procédé de surface (AP, BA, MP, EP, etc.)
AP (recuit et décapé) : Finition standard pour la plupart des alliages inoxydables et de nickel après recuit et décapage.
BA (recuit brillant) : Obtenu par recuit dans une atmosphère contrôlée pour produire une surface lisse et réfléchissante.
MP (poli mécaniquement) : Le polissage mécanique améliore la douceur de la surface, réduisant ainsi le risque de contamination et d’initiation de corrosion.
EP (électropoli) : Un processus électrochimique qui élimine le matériau de surface pour créer une finition ultra-lisse, réduisant la rugosité de la surface et améliorant la résistance à la corrosion.
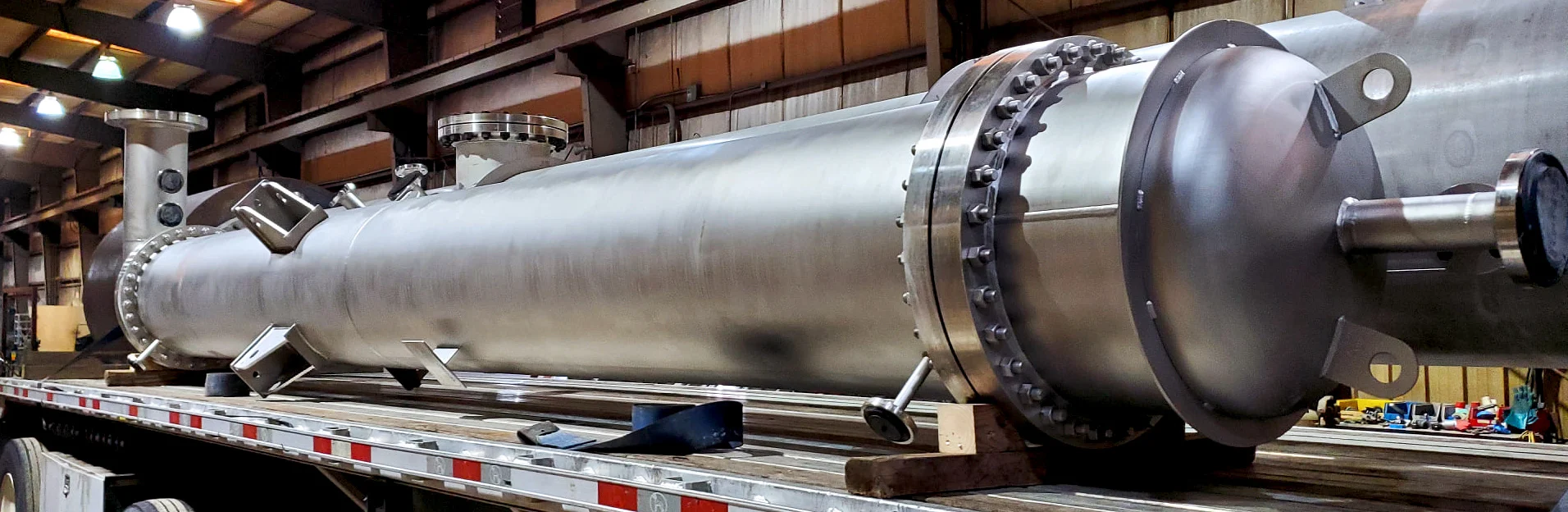
Échangeur de chaleur en acier inoxydable
I. Comprendre les tubes sans soudure
Les tubes sans soudure diffèrent des tubes soudés en ce qu'ils n'ont pas de joint soudé, ce qui peut constituer un point faible dans certaines applications à haute pression. Les tubes sans soudure sont initialement formés à partir d'une billette solide, qui est ensuite chauffée, puis extrudée ou étirée sur un mandrin pour créer la forme du tube. L'absence de joint leur confère une résistance et une fiabilité supérieures, ce qui les rend idéaux pour les environnements à haute pression et à haute température.
Applications courantes :
Chaudières : Les tubes sans soudure sont essentiels dans la construction de chaudières à tubes d'eau et à tubes de fumée, où des températures et des pressions élevées sont présentes.
Échangeurs de chaleur : Utilisés pour transférer la chaleur entre deux fluides, les tubes sans soudure des échangeurs de chaleur doivent résister à la corrosion et maintenir l'efficacité thermique.
Condensateurs : Les tubes sans soudure aident à condenser la vapeur en eau dans les systèmes de production d’énergie et de réfrigération.
Surchauffeurs : Les tubes sans soudure sont utilisés pour surchauffer la vapeur dans les chaudières, améliorant ainsi l'efficacité des turbines des centrales électriques.
Préchauffeurs d'air : Ces tubes transfèrent la chaleur des gaz de combustion à l'air, améliorant ainsi l'efficacité de la chaudière.
Économiseurs : Les tubes sans soudure dans les économiseurs préchauffent l'eau d'alimentation en utilisant la chaleur perdue des gaz d'échappement de la chaudière, augmentant ainsi l'efficacité thermique.
Les chaudières, les échangeurs de chaleur, les condenseurs, les surchauffeurs, les préchauffeurs d'air et les économiseurs sont des composants essentiels dans de nombreuses industries, en particulier celles impliquées dans le transfert de chaleur, la production d'énergie et la gestion des fluides. Plus précisément, ces composants trouvent une utilisation principale dans les industries suivantes :
1. Industrie de production d'énergie
Chaudières : utilisées dans les centrales électriques pour convertir l’énergie chimique en énergie thermique, souvent pour la production de vapeur.
Surchauffeurs, économiseurs et préchauffeurs d'air : ces composants améliorent l'efficacité en préchauffant l'air de combustion, en récupérant la chaleur des gaz d'échappement et en chauffant davantage la vapeur.
Échangeurs de chaleur et condenseurs : utilisés pour le refroidissement et la récupération de chaleur dans les centrales thermiques, en particulier dans les turbines à vapeur et les cycles de refroidissement.
2. Industrie pétrolière et gazière
Échangeurs de chaleur : essentiels dans les processus de raffinage, où la chaleur est transférée entre les fluides, comme dans la distillation du pétrole brut ou dans les plates-formes offshore pour le traitement du gaz.
Chaudières et économiseurs : présents dans les raffineries et les usines pétrochimiques pour la production de vapeur et la récupération d'énergie.
Condenseurs : utilisés pour condenser les gaz en liquides pendant les processus de distillation.
3. Industrie chimique
Échangeurs de chaleur : largement utilisés pour chauffer ou refroidir des réactions chimiques et pour récupérer la chaleur des réactions exothermiques.
Chaudières et surchauffeurs : utilisés pour produire la vapeur nécessaire à divers processus chimiques et pour fournir de l'énergie aux étapes de distillation et de réaction.
Préchauffeurs d'air et économiseurs : améliorent l'efficacité des processus chimiques à forte consommation d'énergie en récupérant la chaleur des gaz d'échappement et en réduisant la consommation de carburant.
4. Industrie maritime
Chaudières et échangeurs de chaleur : essentiels dans les navires pour la production de vapeur, le chauffage et les systèmes de refroidissement. Les échangeurs de chaleur marins sont souvent utilisés pour refroidir les moteurs du navire et produire de l'électricité.
Condenseurs : utilisés pour reconvertir la vapeur d'échappement en eau pour la réutilisation dans les systèmes de chaudières du navire.
5. Industrie agroalimentaire
Échangeurs de chaleur : couramment utilisés pour les processus de pasteurisation, de stérilisation et d’évaporation.
Chaudières et économiseurs : utilisés pour produire de la vapeur pour les opérations de transformation des aliments et pour récupérer la chaleur des gaz d'échappement afin d'économiser sur la consommation de carburant.
6. CVC (chauffage, ventilation et climatisation)
Échangeurs de chaleur et préchauffeurs d'air : utilisés dans les systèmes CVC pour un transfert de chaleur efficace entre les fluides ou les gaz, fournissant du chauffage ou du refroidissement aux bâtiments et aux installations industrielles.
Condenseurs : utilisés dans les systèmes de climatisation pour rejeter la chaleur du réfrigérant.
7. Industrie des pâtes et papiers
Chaudières, échangeurs de chaleur et économiseurs : assurent la récupération de vapeur et de chaleur dans des processus tels que la réduction en pâte, le séchage du papier et la récupération chimique.
Surchauffeurs et préchauffeurs d’air : améliorent l’efficacité énergétique des chaudières de récupération et le bilan thermique global des usines à papier.
8. Industrie métallurgique et sidérurgique
Échangeurs de chaleur : utilisés pour refroidir les gaz et les liquides chauds dans la production d'acier et les processus métallurgiques.
Chaudières et économiseurs : fournissent de la chaleur pour divers processus tels que le fonctionnement des hauts fourneaux, le traitement thermique et le laminage.
9. Industrie pharmaceutique
Échangeurs de chaleur : utilisés pour contrôler la température pendant la production de médicaments, les processus de fermentation et les environnements stériles.
Chaudières : Génèrent la vapeur nécessaire à la stérilisation et au chauffage des équipements pharmaceutiques.
10. Installations de valorisation énergétique des déchets
Chaudières, condenseurs et économiseurs : utilisés pour convertir les déchets en énergie par combustion, tout en récupérant la chaleur pour améliorer l'efficacité.
Plongeons maintenant dans les matériaux qui rendent les tubes sans soudure adaptés à ces applications exigeantes.
II. Tubes en acier au carbone pour chaudières et échangeurs de chaleur
L'acier au carbone est l'un des matériaux les plus utilisés pour les tubes sans soudure dans les applications industrielles, principalement en raison de son excellente résistance, ainsi que de son prix abordable et de sa grande disponibilité. Les tubes en acier au carbone offrent une résistance modérée à la température et à la pression, ce qui les rend adaptés à une large gamme d'applications.
Propriétés de l'acier au carbone :
Haute résistance : les tubes en acier au carbone peuvent résister à une pression et à des contraintes importantes, ce qui les rend idéaux pour une utilisation dans les chaudières et les échangeurs de chaleur.
Rentable : Comparé à d’autres matériaux, l’acier au carbone est relativement peu coûteux, ce qui en fait un choix populaire dans les applications industrielles à grande échelle.
Résistance modérée à la corrosion : bien que l’acier au carbone ne soit pas aussi résistant à la corrosion que l’acier inoxydable, il peut être traité avec des revêtements ou des revêtements pour améliorer sa longévité dans les environnements corrosifs.
Principales normes et grades :
ASTMA179:Cette norme concerne les tubes en acier à faible teneur en carbone étirés à froid sans soudure utilisés pour les applications d'échangeurs de chaleur et de condenseurs. Ces tubes ont d'excellentes propriétés de transfert de chaleur et sont couramment utilisés dans les applications à basse et moyenne température et pression.
ASTMA192:Tubes de chaudière en acier au carbone sans soudure conçus pour un service à haute pression. Ces tubes sont utilisés dans la production de vapeur et dans d'autres environnements à haute pression.
ASTMA210:Cette norme concerne les tubes en acier à teneur moyenne en carbone sans soudure destinés aux chaudières et aux surchauffeurs. Les nuances A-1 et C offrent différents niveaux de résistance mécanique et thermique.
ASTM A334 (Niveaux 1, 3, 6) : Tubes en acier au carbone sans soudure et soudés conçus pour un service à basse température. Ces grades sont utilisés dans les échangeurs de chaleur, les condenseurs et d'autres applications à basse température.
EN 10216-2 (P235GH, P265GH TC1/TC2) : Norme européenne pour les tubes en acier sans soudure utilisés dans les applications sous pression, notamment dans les chaudières et les services à haute température.
Les tubes en acier au carbone sont un excellent choix pour les applications de chaudières et d'échangeurs de chaleur où une résistance élevée et une résistance modérée à la corrosion sont requises. Cependant, pour les applications impliquant non seulement des températures extrêmement élevées mais aussi des environnements corrosifs difficiles, les tubes en alliage ou en acier inoxydable sont souvent préférés en raison de leur résistance et de leur durabilité supérieures.
III. Tubes en acier allié pour chaudières et échangeurs de chaleur
Les tubes en acier allié sont conçus pour les applications de chaudières et d'échangeurs de chaleur à haute température et haute pression. Ces tubes sont alliés à des éléments tels que le chrome, le molybdène et le vanadium pour améliorer leur résistance, leur dureté et leur résistance à la corrosion et à la chaleur. Les tubes en acier allié sont largement utilisés dans les applications critiques, telles que les surchauffeurs, les économiseurs et les échangeurs de chaleur à haute température, en raison de leur résistance exceptionnelle à la chaleur et à la pression.
Propriétés de l'acier allié :
Haute résistance à la chaleur : les éléments d'alliage tels que le chrome et le molybdène améliorent les performances à haute température de ces tubes, les rendant adaptés aux applications avec des températures extrêmes.
Résistance à la corrosion améliorée : les tubes en acier allié offrent une meilleure résistance à l’oxydation et à la corrosion par rapport à l’acier au carbone, en particulier dans les environnements à haute température.
Résistance améliorée : les éléments d’alliage augmentent également la résistance de ces tubes, leur permettant de résister à une pression élevée dans les chaudières et autres équipements critiques.
Principales normes et grades :
ASTM A213 (Nuances T5, T9, T11, T22, T91, T92) : Cette norme couvre les tubes en acier allié ferritique et austénitique sans soudure destinés à être utilisés dans les chaudières, les surchauffeurs et les échangeurs de chaleur. Les nuances diffèrent dans leur composition d'alliage et sont sélectionnées en fonction des exigences spécifiques de température et de pression.
T5 et T9 : Convient pour un service à température modérée à élevée.
T11 et T22 : couramment utilisés dans les applications à haute température, offrant une meilleure résistance à la chaleur.
T91 et T92 : Alliages avancés à haute résistance conçus pour un service à très haute température dans les centrales électriques.
EN 10216-2 (16Mo3, 13CrMo4-5, 10CrMo9-10, 15NiCuMoNb5-6-4, X20CrMoV11-1) : normes européennes pour les tubes en acier allié sans soudure utilisés dans les applications à haute température. Ces tubes sont couramment utilisés dans les chaudières, les surchauffeurs et les économiseurs des centrales électriques.
16Mo3 : Un acier allié avec de bonnes propriétés à haute température, adapté à une utilisation dans les chaudières et les récipients sous pression.
13CrMo4-5 et 10CrMo9-10 : alliages chrome-molybdène offrant une excellente résistance à la chaleur et à la corrosion pour les applications à haute température.
Les tubes en acier allié sont l’option idéale pour les environnements à haute température et haute pression où l’acier au carbone peut ne pas fournir des performances suffisantes pour la chaudière et l’échangeur de chaleur.
IV. Tubes en acier inoxydable pour chaudières et échangeurs de chaleur
Les tubes en acier inoxydable offrent une résistance exceptionnelle à la corrosion, ce qui les rend idéaux pour les applications de chaudières et d'échangeurs de chaleur impliquant des fluides corrosifs, des températures élevées et des environnements difficiles. Ils sont largement utilisés dans les échangeurs de chaleur, les surchauffeurs et les chaudières, où, en plus de la résistance à la corrosion, une résistance à haute température est également requise pour des performances optimales.
Propriétés de l'acier inoxydable :
Résistance à la corrosion : La résistance de l'acier inoxydable à la corrosion provient de sa teneur en chrome, qui forme une couche d'oxyde protectrice sur la surface.
Haute résistance à des températures élevées : l'acier inoxydable conserve ses propriétés mécaniques même à des températures élevées, ce qui le rend adapté aux surchauffeurs et autres applications à forte intensité de chaleur.
Durabilité à long terme : la résistance de l'acier inoxydable à la corrosion et à l'oxydation garantit une longue durée de vie, même dans des environnements difficiles.
Principales normes et grades :
ASTM A213 / ASTM A249:Ces normes couvrent les tubes en acier inoxydable sans soudure et soudés destinés à être utilisés dans les chaudières, les surchauffeurs et les échangeurs de chaleur. Les nuances courantes comprennent :
TP304 / TP304L (EN 1.4301 / 1.4307) : Les nuances d'acier inoxydable austénitique sont largement utilisées pour leur résistance à la corrosion et leur solidité.
TP310S / TP310MoLN (EN 1.4845 / 1.4466) : Nuances d'acier inoxydable haute température avec une excellente résistance à l'oxydation.
TP316 / TP316L (EN 1.4401 / 1.4404) : Nuances contenant du molybdène avec une résistance à la corrosion améliorée, notamment dans les environnements chlorés.
TP321 (EN 1.4541) : Nuance d'acier inoxydable stabilisée utilisée dans les environnements à haute température pour prévenir la corrosion intergranulaire.
TP347H / TP347HFG (EN 1.4550 / 1.4961) : Nuances stabilisées à haute teneur en carbone pour applications à haute température telles que les surchauffeurs et les chaudières.
UNS N08904 (904L) (EN 1.4539) : Acier inoxydable super austénitique avec une excellente résistance à la corrosion, notamment en milieu acide.
ASTM A269:Couvre les tubes en acier inoxydable austénitique sans soudure et soudés pour un service général résistant à la corrosion.
ASTM A789: Norme pour les tubes en acier inoxydable duplex, offrant une combinaison d'excellente résistance à la corrosion et de haute résistance.
UNS S31803, S32205, S32750, S32760 : Nuances d'acier inoxydable duplex et super duplex, offrant une résistance supérieure à la corrosion, en particulier dans les environnements contenant des chlorures.
EN 10216-5:Norme européenne couvrant les tubes sans soudure en acier inoxydable, incluant les nuances suivantes :
1.4301 / 1.4307 (TP304 / TP304L)
1.4401 / 1.4404 (TP316 / TP316L)
1,4845 (TP310S)
1,4466 (TP310MoLN)
1.4539 (UNS N08904 / 904L)
Les tubes en acier inoxydable sont très polyvalents et sont utilisés dans une large gamme d'applications, notamment les échangeurs de chaleur, les chaudières et les surchauffeurs, où la résistance à la corrosion et la résistance aux hautes températures sont non seulement requises mais également essentielles pour des performances optimales.
V. Alliages à base de nickel pour chaudières et échangeurs de chaleur
Les alliages à base de nickel font partie des matériaux les plus résistants à la corrosion disponibles et sont couramment utilisés dans les applications de chaudières et d'échangeurs de chaleur impliquant des températures extrêmes, des environnements corrosifs et des conditions de haute pression. Les alliages de nickel offrent une résistance exceptionnelle à l'oxydation, à la sulfuration et à la carburation, ce qui les rend idéaux pour les échangeurs de chaleur, les chaudières et les surchauffeurs dans des environnements difficiles.
Propriétés des alliages à base de nickel :
Résistance exceptionnelle à la corrosion : les alliages de nickel résistent à la corrosion dans les environnements acides, alcalins et chlorés.
Stabilité à haute température : les alliages de nickel conservent leur résistance et leur résistance à la corrosion même à des températures élevées, ce qui les rend adaptés aux applications à haute température.
Résistance à l’oxydation et à la sulfuration : les alliages de nickel résistent à l’oxydation et à la sulfuration, qui peuvent se produire dans des environnements à haute température impliquant des composés contenant du soufre.
Principales normes et grades :
ASTM B163 / ASTM B407 / ASTM B444:Ces normes couvrent les alliages à base de nickel pour tubes sans soudure utilisés dans les chaudières, les échangeurs de chaleur et les surchauffeurs. Les nuances courantes comprennent :
Inconel 600 / 601 : Excellente résistance à l'oxydation et à la corrosion à haute température, ce qui rend ces alliages idéaux pour les surchauffeurs et les échangeurs de chaleur à haute température.
Inconel 625 : Offre une résistance supérieure à une large gamme d’environnements corrosifs, y compris les environnements acides et riches en chlorures.
Incoloy 800 / 800H / 800HT : Utilisés dans les applications à haute température en raison de leur excellente résistance à l'oxydation et à la carburation.
Hastelloy C276 / C22 : Ces alliages nickel-molybdène-chrome sont connus pour leur résistance exceptionnelle à la corrosion dans les environnements hautement corrosifs, y compris les milieux acides et contenant des chlorures.
ASTM B423:Couvre les tubes sans soudure fabriqués à partir d'alliages nickel-fer-chrome-molybdène tels que l'alliage 825, qui offre une excellente résistance à la fissuration par corrosion sous contrainte et à la corrosion générale dans divers environnements.
EN 10216-5 : Norme européenne relative aux alliages à base de nickel utilisés dans les tubes sans soudure pour applications à haute température et corrosives, y compris les nuances telles que :
2,4816 (Inconel 600)
2,4851 (Inconel 601)
2,4856 (Inconel 625)
2.4858 (alliage 825)
Les alliages à base de nickel sont souvent choisis pour les applications critiques où la résistance à la corrosion et les performances à haute température sont essentielles, comme dans les centrales électriques, le traitement chimique et les raffineries de pétrole et de gaz. Chaudière et échangeur de chaleur.
VI. Alliages de titane et de zirconium pour chaudières et échangeurs de chaleur
Les alliages de titane et de zirconium offrent une combinaison unique de résistance, de résistance à la corrosion et de propriétés légères, ce qui les rend idéaux pour des applications spécifiques dans les échangeurs de chaleur, les condenseurs et les chaudières.
Propriétés des alliages de titane :
Rapport résistance/poids élevé : le titane est aussi résistant que l'acier mais nettement plus léger, ce qui le rend adapté aux applications sensibles au poids.
Excellente résistance à la corrosion : les alliages de titane sont très résistants à la corrosion dans l’eau de mer, les environnements acides et les milieux contenant du chlorure.
Bonne résistance à la chaleur : les alliages de titane conservent leurs propriétés mécaniques à des températures élevées, ce qui les rend adaptés aux tubes d'échangeurs de chaleur dans les centrales électriques et le traitement chimique.
Propriétés des alliages de zirconium :
Résistance exceptionnelle à la corrosion : les alliages de zirconium sont très résistants à la corrosion dans les environnements acides, notamment l’acide sulfurique, l’acide nitrique et l’acide chlorhydrique.
Stabilité à haute température : les alliages de zirconium conservent leur résistance et leur résistance à la corrosion à des températures élevées, ce qui les rend idéaux pour les applications d'échangeurs de chaleur à haute température.
Principales normes et grades :
ASTM B338:Cette norme couvre les tubes en alliage de titane sans soudure et soudés destinés à être utilisés dans les échangeurs de chaleur et les condenseurs. Les nuances courantes comprennent :
Grade 1 / Grade 2 : Grades de titane commercialement purs avec une excellente résistance à la corrosion.
Grade 5 (Ti-6Al-4V) : un alliage de titane avec une résistance améliorée et des performances à haute température.
ASTM B523: Couvre les tubes en alliage de zirconium sans soudure et soudés destinés à être utilisés dans les échangeurs de chaleur et les condenseurs. Les nuances courantes comprennent :
Zirconium 702 : un alliage de zirconium commercialement pur avec une résistance à la corrosion exceptionnelle.
Zirconium 705 : Une nuance de zirconium alliée avec des propriétés mécaniques améliorées et une stabilité à haute température.
Les alliages de titane et de zirconium sont couramment utilisés dans des environnements hautement corrosifs tels que les usines de dessalement de l'eau de mer, les industries de traitement chimique et les centrales nucléaires en raison de leur résistance supérieure à la corrosion et de leurs propriétés de légèreté.
VII. Cuivre et alliages de cuivre pour chaudières et échangeurs de chaleur
Le cuivre et ses alliages, notamment le laiton, le bronze et le cuivre-nickel, sont largement utilisés dans les échangeurs de chaleur, les condenseurs et les chaudières en raison de leur excellente conductivité thermique et de leur résistance à la corrosion.
Propriétés des alliages de cuivre :
Excellente conductivité thermique : les alliages de cuivre sont connus pour leur conductivité thermique élevée, ce qui les rend idéaux pour les échangeurs de chaleur et les condenseurs.
Résistance à la corrosion : les alliages de cuivre résistent à la corrosion dans l’eau, y compris l’eau de mer, ce qui les rend adaptés aux applications marines et de dessalement.
Propriétés antimicrobiennes : Les alliages de cuivre ont des propriétés antimicrobiennes naturelles, ce qui les rend adaptés aux applications dans les domaines de la santé et du traitement de l’eau.
Principales normes et grades :
ASTM B111:Cette norme couvre les tubes en cuivre et en alliage de cuivre sans soudure destinés à être utilisés dans les échangeurs de chaleur, les condenseurs et les évaporateurs. Les nuances courantes comprennent :
C44300 (laiton amirauté) : un alliage cuivre-zinc avec une bonne résistance à la corrosion, en particulier dans les applications en eau de mer.
C70600 (Cuivre-Nickel 90/10) : Un alliage cuivre-nickel avec une excellente résistance à la corrosion dans l'eau de mer et les environnements marins.
C71500 (Cuivre-Nickel 70/30) : Un autre alliage cuivre-nickel avec une teneur en nickel plus élevée pour une meilleure résistance à la corrosion.
Le cuivre et les alliages de cuivre sont largement utilisés dans les applications de chaudières et d’échangeurs de chaleur marins, les centrales électriques et les systèmes CVC en raison de leur excellente conductivité thermique et de leur résistance à la corrosion de l’eau de mer.
Outre la chaudière et l'échangeur de chaleur, les condenseurs, les surchauffeurs, les préchauffeurs d'air et les économiseurs sont également des composants essentiels qui optimisent considérablement l'efficacité énergétique. Par exemple, le condenseur refroidit les gaz d'échappement de la chaudière et de l'échangeur de chaleur, tandis que le surchauffeur, d'autre part, augmente la température de la vapeur pour améliorer les performances. Pendant ce temps, le préchauffeur d'air utilise les gaz d'échappement pour chauffer l'air entrant, améliorant ainsi encore l'efficacité globale du système de chaudière et d'échangeur de chaleur. Enfin, les économiseurs jouent un rôle crucial en récupérant la chaleur perdue des gaz de combustion pour préchauffer l'eau, ce qui réduit finalement la consommation d'énergie et augmente l'efficacité de la chaudière et de l'échangeur de chaleur.
VIII. Conclusion : Choisir les bons matériaux pour la chaudière et l'échangeur de chaleur
Les tubes sans soudure sont essentiels aux performances des chaudières, des échangeurs de chaleur, des condenseurs, des surchauffeurs, des préchauffeurs d'air et des économiseurs dans des secteurs tels que la production d'énergie, le pétrole et le gaz et le traitement chimique. Le choix du matériau des tubes sans soudure dépend des exigences spécifiques de l'application, notamment la température, la pression, la résistance à la corrosion et la résistance mécanique.
Acier au carbone offre un prix abordable et une résistance pour les applications à température et pression modérées.
Acier allié offre des performances et une résistance supérieures à haute température dans les chaudières et les surchauffeurs.
Acier inoxydable offre une excellente résistance à la corrosion et une durabilité dans les échangeurs de chaleur et les surchauffeurs.
Alliages à base de nickel sont le meilleur choix pour les environnements extrêmement corrosifs et à haute température.
Alliages de titane et de zirconium sont idéales pour les applications légères et hautement corrosives.
Cuivre et alliages de cuivre sont préférés pour leur conductivité thermique et leur résistance à la corrosion dans les échangeurs de chaleur et les condenseurs.
Les systèmes de chaudières et d'échangeurs de chaleur jouent un rôle crucial dans diverses industries en transférant efficacement la chaleur d'un milieu à un autre. Une chaudière et un échangeur de chaleur fonctionnent ensemble pour générer et transférer la chaleur, fournissant la chaleur essentielle à la production de vapeur dans les centrales électriques et les processus de fabrication.
En comprenant les propriétés et les applications de ces matériaux, les ingénieurs et les concepteurs peuvent prendre des décisions éclairées, garantissant ainsi le fonctionnement sûr et efficace de leurs équipements. Lors de la sélection des matériaux pour la chaudière et l'échangeur de chaleur, il est essentiel de prendre en compte les exigences spécifiques de votre application. De plus, vous devez consulter les normes pertinentes pour garantir la compatibilité et des performances optimales.