Guideline to Finned Tube: Enhancing Heat Transfer Efficiency
Introduction
A finned tube maximizes heat transfer efficiency between two fluids in heat exchangers. These tubes enhance thermal performance by increasing the surface area available for heat exchange. Whether utilized in power plants, HVAC systems, or chemical processing, finned tubes significantly improve heat transfer efficiency. This guide will delve into the details of finned tubes, covering their standards and grades, types of fins, materials, specifications, and suitable tube dimensions.
What Are Finned Tubes?
Finned tubes consist of a base tube with extended fins attached to its exterior. The fins increase the surface area, improving the heat transfer rate. These tubes are essential in applications requiring efficient thermal exchange and limited space.
Standards and Grades
Different standards and grades are used to categorize finned tubes based on their material, construction, and application:
EN 10216-2: Seamless tubes for pressure purposes:
P235GH TC1/TC2: Used in boilers and pressure vessels.
P265GH TC1/TC2: Offers higher strength for high-pressure environments.
ASTM Standards:
ASTM A179: Low-carbon steel tubes for heat exchangers and condensers.
ASTM A192: Similar to A179 but designed for higher pressures.
ASTM A213: Seamless ferritic and austenitic alloy steel tubes, including:
TP304/304L: Commonly used for its corrosion resistance and ease of welding.
TP316/316L: Preferred in environments with a higher risk of corrosion.
EN 10216-5: Stainless steel tubes:
EN 1.4301 (304): European equivalent of ASTM TP304, corrosion-resistant.
EN 1.4307 (304L): A low-carbon variant of 1.4301, ideal for welding.
EN 1.4401 (316): Offers improved resistance to chlorides.
EN 1.4404 (316L): Low-carbon version of 1.4401, suitable for welding.
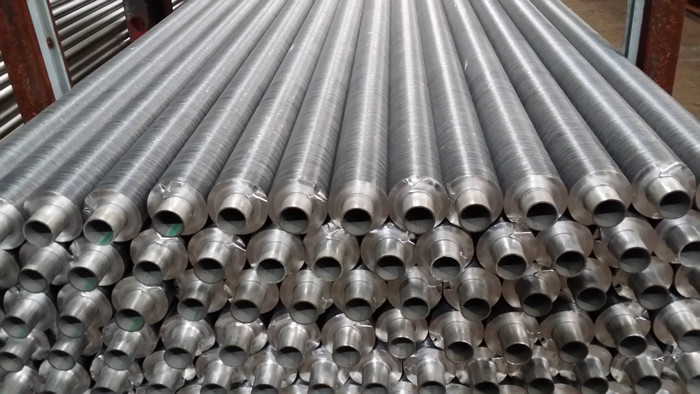
Finned Tubes
Types of Fins
The fins used in finned tubes can vary based on the method of attachment and the application:
Embedded Fins: Mechanically embedded into the tube’s surface, offering a robust bond and high thermal efficiency.
Welded Fins: The fins are welded onto the tube, providing durability and mechanical strength, which is ideal for harsh environments.
Extruded Fins: Fins are extruded from the tube material, ensuring uniform heat transfer properties.
Materials for Fins
The material of the fins is selected based on the desired thermal performance and environmental conditions:
Aluminum Alloys:
AA1100: Known for its excellent thermal conductivity and corrosion resistance.
AA1080, AA1060, AA1050: These grades provide similar properties with slight differences in strength and conductivity.
Specifications: Tube Dimensions, Fin Height, Thickness, and Density
The efficiency of finned tubes depends on various factors, including the outer diameter, wall thickness, fin height, thickness, and the number of fins per inch or meter.
Tube Outer Diameter (OD): Finned tubes are typically available in outer diameters ranging from 16 mm to 219 mm (approximately 5/8″ to 8.625″). This range covers most standard applications.
Tube Wall Thickness: The wall thickness of tubes suitable for finning generally ranges from 1 mm to 8 mm. Thinner walls are more common in applications where weight and thermal conductivity are critical. In comparison, thicker walls are used for high-pressure environments.
Fin Height: Typically ranges from 6 mm to 30 mm. Higher fins increase surface area but may result in more significant pressure drops.
Fin Thickness: Ranges from 0.2 mm to 0.6 mm. Thicker fins offer better durability but may slightly reduce thermal efficiency.
The number of Fins per Inch (FPI) or per Meter (FPM) is usually between 8 to 16 FPI or 250 to 500 FPM. Higher densities provide more surface area but can also increase pressure drop.
Length of Finned Sections: The finned portion of the tube can be customized, with standard lengths ranging from 1 meter to 12 meters.
Applications and Benefits
Finned tubes are utilized in a variety of industries for their superior heat transfer capabilities:
Power Generation: Used in economizers and boilers to improve heat recovery and efficiency.
HVAC Systems: Enhance the performance of heat exchangers, contributing to better temperature control and energy savings.
Chemical Processing: In reactors and condensers, they facilitate efficient thermal management, optimizing reaction conditions and product quality.
Frequently Asked Questions (FAQs)
1. What is the purpose of finned tubes?
Finned tubes increase the surface area of heat exchangers, improving the efficiency of heat transfer between fluids.
2. What are the most common materials used for fins?
Aluminum alloys, such as AA1100, AA1080, AA1060, and AA1050, are commonly used due to their excellent thermal conductivity and corrosion resistance.
3. What are the common standards for finned tubes?
Finned tubes are manufactured according to standards like EN 10216-2 for seamless tubes and ASTM A179, A192, and A213 for various applications.
4. How do fin heights and densities affect performance?
Higher fins increase the surface area for heat transfer, while the number of fins per inch or meter affects the overall efficiency. However, higher density may also increase pressure drop.
5. What are the typical applications of finned tubes?
Finned tubes are commonly used in power generation, HVAC systems, and chemical processing to enhance heat transfer efficiency.
6. What is the typical length of a finned tube?
The finned portion of a tube typically ranges from 1 meter to 12 meters, depending on the application.
Conclusion
Finned tubes are essential in systems where effective heat transfer is crucial. Understanding the different types of fins, materials, and specifications allows engineers to select the most suitable finned tube for their application, ensuring optimal performance, longevity, and cost-efficiency.
When selecting finned tubes, it’s important to consider your system’s specific requirements, such as operating temperature, pressure, and fluids involved. Doing so can achieve the best possible thermal efficiency and system performance.
Consulting with a specialized manufacturer or supplier is highly recommended for tailored solutions and more detailed information on finned tubes. They can provide expert guidance and help you select the perfect finned tube configuration.